Image Credit: Energy Vanguard
Image Credit: Energy Vanguard Standard 3 stud wall corner framing
Image Credit: Energy Vanguard Advanced framing 2-stud corner (Image credit: US Dept. of Energy)
Image Credit: US Dept. of Energy
Most new homes in North America are built with sticks. The early home builders used bigger pieces of wood—timbers—and when the smaller dimensional lumber that we use so much today hit the market, they scoffed at those newfangled little woody things, calling them sticks. Now our home construction industry is full of people who do stick building and the home you live is most likely stick-built. And sadly, many of the techniques used to build many of those homes are the same used before we started insulating them.
Before insulation became widespread, it didn’t matter if you put extra wood in your walls. In fact, many builders still think more wood is better. But when your insulation goes into the cavities between framing members, every extra bit of wood means less insulation. That means more heat loss in winter and more heat gain in summer because wood has an R-value less than a third that of most insulation. (Putting all the insulation on the outside is better, but that’s more expensive and not likely to happen on a wide scale in the residential market.)
The good news is there are some simple ways to improve the framing and get more insulation without compromising the structural stability of the home. Here are three I think ought to be used on every stick-built home.
Ladder T-walls
This one is a nobrainer. When an interior wall intersects an exterior wall, the standard practice is to use three studs to complete the T-wall. The photo above shows what that looks like.
One easy solution is the ladder T-wall. The diagram at right shows what it looks like.
Rather than vertical studs, you take some of your scrap wood and run it across horizontally. You put the wide side against the T-wall stud so you have space in the back to insulate that cavity. It’s beautiful! You save wood and get a better-insulated house, too.
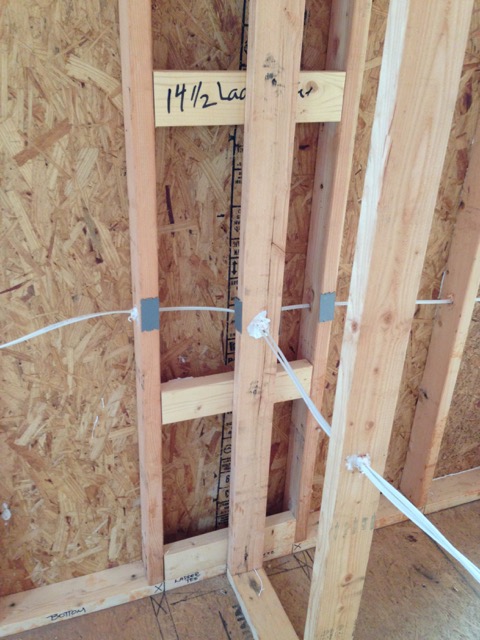
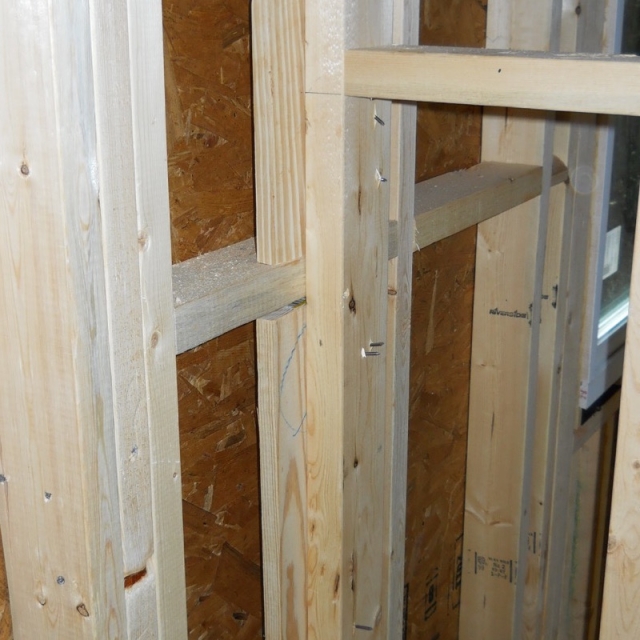
California corners and two-stud corners
This is similar to the T-wall problem. The standard practice uses three studs and blocks off the corner so you can’t insulate it.
The advanced framing alternative is to use three studs but leaves an opening to get insulation back into the corner.
It’s usually called a California corner here in the Southeast. I’m not sure what it’s called in California. Maybe just a corner?
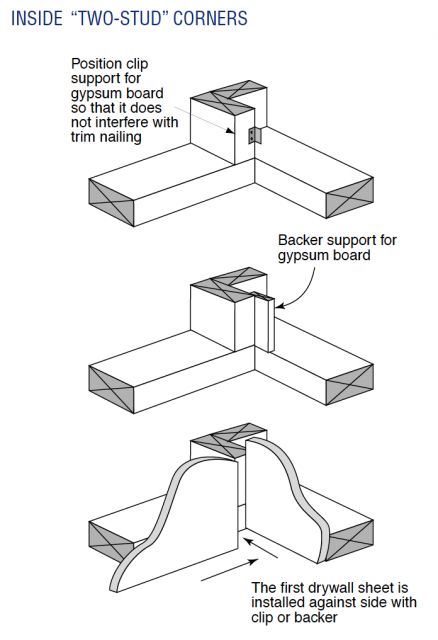
Insulated headers
Headers abound in stick-built homes. They carry the load when you can’t put in studs at the regular spacing, as is the case where you have doors and windows. They’re often made with two pieces of bigger wood, like 2x10s, but they have a gap. In a 2×4 wall, two 2x10s on edge are 3″ thick. The wall is 3.5″ thick. In a typical home, that extra half inch is wasted. In a 2×6 wall, you’re wasting 2.5”.
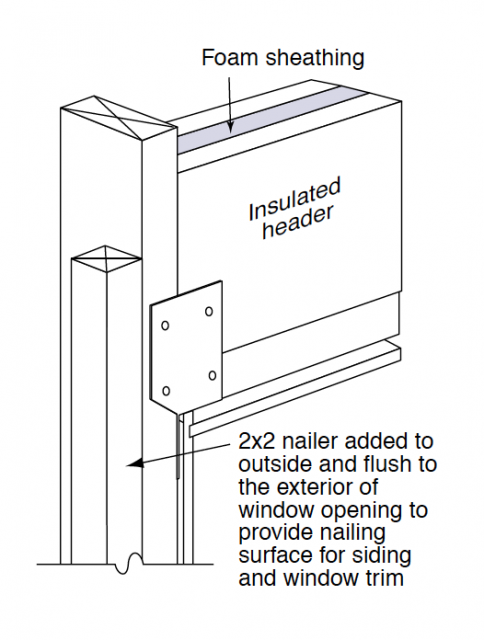
The image at right (from the same U.S. Dept. of Energy document on advanced framing as the ladder T-wall image) illustrates how it works.
Going a step further, you can get more reduction of thermal bridging at headers by sizing them properly or not using them at all. A lot of framers will use the same size header in every opening of the house. But different openings have different loads to transmit. And some have no load. In those cases, you can make the header smaller or eliminate it, leaving room for even more insulation.
Too easy not to use
These three advanced framing techniques for walls in stick-built homes are too easy not to use. In fact, some people will look at these and dispute their being called “advanced framing” at all. But in the Southeastern U.S. and some other regions, plenty of builders still haven’t adopted these three techniques.
The only reason they’re not already used on every stick-built house is inertia. “We’ve been doing it this way for 30 years and it’s never been a problem.” If you’re a builder and worried about trying something new, check out Matt Risinger’s video about standard framing versus advanced framing.
The exterior walls in a typical house are 25% framing. Wood has an R-value of about 1 per inch. Most insulation is close to 4 per inch. Using these advanced framing techniques will reduce the amount of wood in those walls and increase the insulation.
It’s time to get over the inertia. These things are easy, easy, easy. Your house won’t fall down. Instead, your house will be better.
Allison A. Bailes III, PhD is a speaker, writer, building science consultant, and the founder of Energy Vanguard in Decatur, Georgia. He has a doctorate in physics and writes the Energy Vanguard Blog. He also has a book on building science coming out in October 2022. You can follow him on Twitter at @EnergyVanguard. Images courtesy of author.
Weekly Newsletter
Get building science and energy efficiency advice, plus special offers, in your inbox.
7 Comments
Further detail please
Could you give more detail, or a diagram, to clarify the photo describing
"1-by deadwood for drywall and what is essentially fireblocking through the cavity"?
Thx.
Response to Robert Opaluch
Robert,
Like you, I'm not familiar with Allison's terms. Must be Georgia jargon.
The 2x4s that are "essentially fireblocking" are horizontal 2x4 nailers, installed stud to stud.
What Allison calls "1-by deadwood" is what I would call a vertical nailer, installed to catch the drywall in the corner.
Response to Robert Opaluch
Robert, sorry about the confusion there. Martin's answer is correct. The 4th photo in the article shows an example of what I was trying to describe. The deadwood is, I believe, a 1x4, nailed to the interior wall in the T and to which the drywall is nailed.
The fireblocking is like the ladder part that I described in the ladder T-wall except that the 2x4 is nailed with the long dimension running horizontally instead of vertically. That prevents the compression you get with fiberglass behind the ladder "steps" but increases thermal bridging.
Does that make more sense?
Partition Intersection Framing
The three stud intersection is a poor detail for other reasons too. Because the studs can't be nailed together it is hard to keep the corner straight.
Rather than the ladder, we use the variant I've shown below. One of the chief benefits is that the intersection of the two 2'x6"s acts as a guide to the location of the partition, so once the exterior walls are stood you don't need to measure or plumb the partition wall. It also provides continuous backing at the corner. Something that often turns out to be useful if you are adding interior finishes or built-ins.
PARTITION FRAMING
@ Malcolm - I like your solution IF the partition happens to fall on an exterior stud. But when it does not, it's at least one extra stud, and the ladder works better (less wood).
Kevin
It sure speeds up the framing process. The first thing you do when cutting your walls is count the number of corners and partitions, then make up the Ls. And as I said, once the walls are up you have a precise roadmap to locating all the partitions.
The continuous backing at the corner is also useful if you are installing an interior membrane or (god forbid) poly. Our code requires all joints to be made over solid blocking, not just taped.
I'm not as enamoured with trying to reduce framing as an insulation strategy as some builders seem to be. I'd rather keep a robust structural frame and deal with thermal bridging some other way. To me Advanced Framing yields the building equivalent of a high-end racing bicycle. Great in the velodrome, not so great on the street.
I was able to get the foam insulation installer to fill the corner cavities between the blocking with Great Stuff Window and Door foam, but the owner had to drill the 1 in. holes 2 ft. oc. I wanted to do a corner with a more accessible spacing, but the Florida Building Code requires the 2 full height stud corner with the intermittent blocking. It was a little tricky because I am a designer in Georgia and my son-in-law is building in Florida. He sends me pictures every day and I critique the construction. Insulation guy also did good job of continuing wall to roof insulation to maintain the air barrier. Haven't got blower door test results yet.
Log in or create an account to post a comment.
Sign up Log in