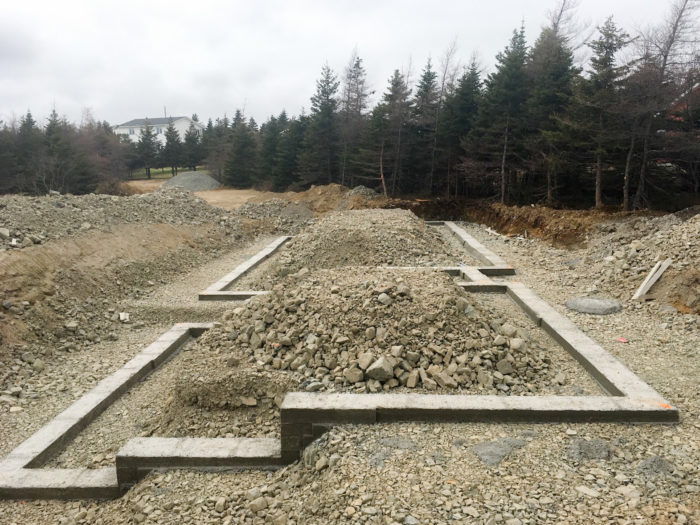
Footings are typically the first objects to take shape on the site of a new house, and in no time they have been surmounted by foundation walls, buried under yards of backfill, and with any luck are nothing but a distant memory as the house is built on top of them.
Their appearance may be brief, but footings play an important role in the long-term stability of the structure. Footings distribute the weight of the foundation, and in turn the weight of the house, and prevent uneven settling that leads to structural damage. The more problematic the soil, and the heavier the structure, the more important footings become.
For Pioneer Builders in Port Orchard, Washington, footings for a two-story house might be no more complicated than a 15-in.-wide swath of 3000-psi concrete 8 in. thick. A frost line just 12 in. below grade doesn’t hurt. “You scrape the ground and you’re there,” says Pioneer Vice President Bryan Uhler. But if you’re designing a house in parts of Texas, where expansive soils are the norm, footings can become a complicated engineering exercise that adds tens of thousands of dollars and months of planning to the project.
Footings support foundation walls, spreading the weight of the structure evenly on the soil below and preventing foundations and the structures they support from buckling, sinking, or cracking. In many locales, footings are made of steel-reinforced concrete, but the International Residential Code (IRC) also allows footings to be made from crushed stone, and builders lucky enough to be working in parts of the U.S. with predictably stable soils may be able to pour extra-thick foundation walls and skip separate footings altogether.
Soil type is an important consideration
No matter what type of foundation wall the designer chooses—concrete, concrete block, pre-cast concrete, or…
Weekly Newsletter
Get building science and energy efficiency advice, plus special offers, in your inbox.
This article is only available to GBA Prime Members
Sign up for a free trial and get instant access to this article as well as GBA’s complete library of premium articles and construction details.
Start Free TrialAlready a member? Log in
9 Comments
Scott,
Great overview as always.
A couple of random thoughts:
- What often determines how deep excavations go in areas where frost doesn't, is the depth necessary to provide cover for perimeter drains and rock.
- Here on Vancouver island we still often pour footings and foundation walls monolithically. The disadvantage is the inability to provide a capillary break. The advantages are not having to have a completely flat excavation (or top of footing), it is structurally stronger, and only takes one concrete pour.
Malcom,
I would imagine the load the footer is supporting and the bearing capacity of the soil would determine the depth of the footer. Also, if unsuitable material is encountered, can either over excavate and replace w/ structural fill or just pour it deeper.
Around here (PA), most older homes and even new are block or conc. stem walls ontop of poured footers. Although it seems like precast basement walls on stone are becoming more and more common with new construction.
Most lawsuits involving fnd settlement seem to be traced back to bad soil, improper compaction of soils, or improper installation of piles etc.
Concrete is concrete. And you can fix bad drainage around a structure. Wild card, IMO, is the underlying soil, groundwater, bedrock, etc, etc.
Yes very true. You make several good points. Although our frost depth here is basically existing grade, some excavations, especially on sites with a lot of organic material, end up being deep en0ugh for full basements. My comment was more around staying too high when there is good bearing close to grade. Space for perimeter drains and rock, separate pipe for downspouts, and enough clearance from grade to the framing, mean you need at least a 24" deep excavation.
"[Superior Walls] explains that as the depth of the footing increases, the wall’s effective bearing width, i.e. its weight-bearing footprint, also goes up."
Depth, in this case, meaning 'thickness' of the layer of crush rock—not depth below grade. This is one of those times when 'depth' can mean a bit too many things.
Also of interest is that they claim: "The load distribution path through the crushed stone is at an angle approximately 60 degrees from the horizontal." Which explains perfectly why increasing the thickness of the layer increases the effective bearing width.
It's the same with road beds and the like—it acts as a sort of beam.
Great overview, Scott. One detail I almost always see overdone is concrete footings. For some reason architects love to draw huge footings, even though in most cases their main purpose is simply to spread the load of the wall a bit wider, with the wall itself acting as a beam in the lengthwise direction. Footings are often drawn and built at 12" thick x 24" wide, when even on poor, 1500 psi soil, a 6" x 16" is enough for many homes when using the IRC as a guide. If you're showing a 16" wide footing there is no need for it to be 10" to 12" deep when it's supporting a reinforced wall above. Engineers generally don't down-size what an architect shows. The IRC also does not require rebar in footings. Like many people on this site, I usually exceed code-minimum standards, I just find undue focus put on the size of footings.
Per Code, sizing of footings and walls, includes among other things, soil condition and gradient. Long time ago, the UBC called for the thickness of the walls to be the thickness of the footings, and the width of the footings to be twice the thickness. Then, when I started designing in the Mountains, where the slope of the land called for different sizing of footings and walls, I had to readjust.
Once again, when I moved to TX and encounter soils with high PVR and expansivity index, then the rules changed again, and again in NOLA, and Houston, and Napa, etc.
The point is, that because some areas of the country allow Builders to design foundations with a certain local standard, it doesn't mean one should. I, for one, think that Codes have changed for the better on this subject.
My advise to all my clients, no matter where their home is going to be built, is to do a geotech analysis for their property, and consult an Structural Engineer. It's insurance. I've seen too many horror stories about foundation failures to know better.
Doing things by "this is the way I've done it for 30 years", its reckless and unprofessional, if not against Code.
"My advise to all my clients, no matter where their home is going to be built, is to do a geotech analysis for their property, and consult an Structural Engineer. It's insurance. I've seen too many horror stories about foundation failures to know better."
This is standard practice in the commercial world. We get a geotech to do borings at the corners of the building. There is already a structural engineer on board, for the building, that will do the footing/slab design. Footing/slab general design is usually driven by client/arch preference. And then usually a 3rd party QA/QC onsite during installation.
Getting pushback from contractors is rare. Unless there is something in the design that will cause a significant delay in schedule or it's vastly different from how "they're used to doing it." Occasionally we'll get request to beef up rebar, etc or add WW mesh to pads where it's not spec'd (e.g. fiber reinforcing to be added at the plant). Requests... that are hard to wrap your head around since.... there's a detail that client paid for to have designed... that an engineer is willing to stamp/seal and stand behind.... no reason to deviate from it.
General question... how common is it get borings done for residential homes? Becoming more common? Maybe not for a huge subdivision? But if you're building a passivhaus? Why not?
I think part of the answer as to whether you need geo-technical report depends on how consistent the soil conditions are in the region you build in.
Where I am we don't encounter surprises when we excavate. It's either rock, or good bearing soil. Right across the Straits on the river delta around Vancouver it's a completely different situation. We involve a geo-tech on steep slopes or some waterfront lots. The areas requiring them are identified on regional planning maps.
There are times where local municipalities, especially large cities and metro areas, require geotech reports for residential, as it’s the case in TX, but many rural areas do not. As far as I know, some areas, where I’ve designed homes, in California, Louisiana, Mississippi, TX Golf Coast, are the same. In some areas, as long as a geotech investigation was done within 200’, you don’t need another. It comes handy when you develop two lots next to each other. I would also suggest that areas near a river, where sediment of clay and expansive soils are present, it should give you a clue to do geotech investigations, and possibly consult an Engineer.
Developers and Production Builders usually have geotech investigations done in entire subdivisions, especially when they are doing the feasibility and infrastructure studies. In the Southwest, where sand is the prevalent soils, usually, Developers scrape the top 4’-6’ of the entire subdivision, and rebuild it back up, in 12” lifts, compacting the soils to specific standards for roads and house pads. Three soil samples are done on lots, usually in the center and two opposite corners, determining moisture and 95% min. compaction level.
A Proctor Compaction Test determines the maximum unit weight that a soil type can be compacted to use a controlled compactive force at an optimum water content. All this will protect the house from bearing, stability, erosion and heaving.
When you design footings and foundations in Flood Zones, per FEMA regulations, the House Pad must be elevated to 12” minimum above Base Flood Elevation (BFE). A house I’m designing now, in Creve Coeur, MO, the homeowner wants to raise the pad 2’-3’ above FEMA, which is a good idea.
A house I designed where a swimming pool used to be, also needed to have soils compaction test, in order to build the larger house on the lot. This is very common nowadays in metro areas, where Builders are buying teardowns to build larger homes. This is a big part of my work.
A think a lot of the GBA readers are building houses in rural or farm lots, and I imagine, without soil testing. I’m sure is a calculated risk for their areas, but why… to save $2k-3k on a $500k house or more?
Log in or become a member to post a comment.
Sign up Log in