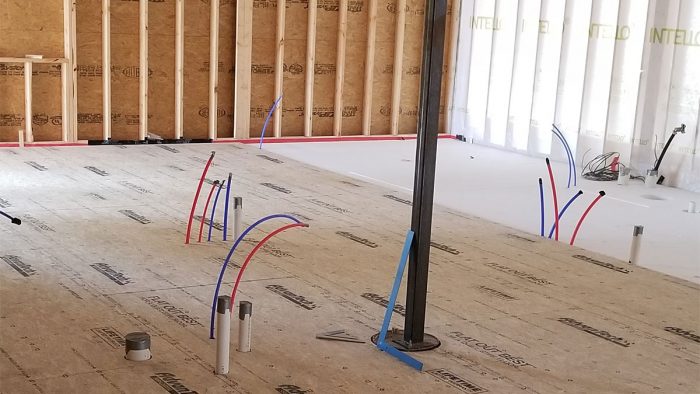
Randy Williams of Willcon Inc. recently contacted me regarding a project he is wrapping up in northern Minnesota. I was intrigued because he has eliminated the concrete slab foundation altogether, which, given the material’s carbon load, is a design decision I fully support. There were additional aspects of his approach that were equally interesting, including his use of cutting-edge products in a residential building market generally unfamiliar with them; his success building directly off insulated concrete forms (ICFs); and his choice of a plenum truss for running duct work. To inform his decisions, Williams had several conversations with Steve Baczek and Jake Bruton, both of whom are experienced in the science of the “slabless slab.” Ultimately, in lieu of a slab-on-grade foundation, Williams used two layers of 2-in. Type IX EPS, a 6-mil. reinforced poly vapor retarder, and two layers of 3/4-in. AdvanTech subfloor.
In large part, Williams’s approach was a response to the clients’ desire for a heated floor. “I wanted a system that didn’t need heat in the floor,” he explains. “In our climate, the heat moves downward and warms the ground, not just the upper living spaces. The system I used creates a warm floor without having to incorporate a heat source.”
Though similar to Michael Maines’s frost-protected shallow foundation, Williams’s approach starts with excavating down 5 ft. Additionally, Maines puts sleepers on top of the EPS foam, and his flooring extends to the exterior walls. Here the floor system butts up to the double bottom plate of the wall framing. “My concern with Maines’s method was moisture,” says Williams. “We couldn’t build it fast enough to get it shelled in before the floor assembly would get wet. With two layers of AdvanTech, two layers of foam, and poly, we would have trapped in…
Weekly Newsletter
Get building science and energy efficiency advice, plus special offers, in your inbox.
This article is only available to GBA Prime Members
Sign up for a free trial and get instant access to this article as well as GBA’s complete library of premium articles and construction details.
Start Free TrialAlready a member? Log in
35 Comments
Cost Savings?
First- thank you for this article. I am so glad to see that more attention is being paid to reducing the carbon footprint of our buildings up-front and not just energy savings over time.
I really like Randy's design. By having two layers of EPS, Randy can protect the vapor retarder from damage. Obviously with a normal concrete slab, this isn't issue as concrete is an air barrier. But in this case, his vapor retarder is his air barrier. The upper layer of EPS combined with sleepers and subfloor should prevent any fasteners from penetrating.
My Question:
I wonder if one could opt for Type II EPS rather than Type IX? (Not talking about footings here, but the "slab" area.) There is probably a 25-30% cost difference between the two. With a conventional slab, Type II will suffice just fine. If you could also use Type II EPS for this arrangement, then I imagine that you could start to see real cost savings here. Perhaps wider sleepers- like 2x6 or perhaps strips of Advantech would make this possible?
Great article! Thank you Kiley, GBA Team.
We compared the cost of the system we built with a concrete slab and the tubing for the in-floor heating. We were a couple hundred dollars cheaper using the Advantech and EPS. Type II would save additional costs. I feel better using the type IX, never know what a future homeowner might load onto the floor system.
Matt Risinger briefly shows a similar detail in a recent video:
https://youtu.be/i_5Up65qOPw?t=88
A really nice, well thought-out project.
One comment on compaction: Doing it for a set period of time is a bit like acclimatizing wood flooring on site for a week rather than using a moisture meter. Instead of guessing whether three days is enough (or maybe one or four?), you can take the uncertainty out of it by getting a Proctor test. Then you know exactly where you stand.
I am confident with how we compacted this foundation, but I agree, If we do another system like this one, we will be testing.
Randy,
You know what you are doing. My comment was more a general one for people attempting the task for the first time.
I know this article is about construction techniques, but I'd love to see photos of the finished project.
“[Deleted]”
I'm interested in the validity of a Proctor test for measuring compaction when it is apparently a "optimal moisture content" test.
"The Proctor compaction test is a laboratory method of experimentally determining the optimal moisture content at which a given soil type will become most dense and achieve its maximum dry density."
Jon,
You are saying you don't think the standard engineering tests to measure compaction under foundations work?
https://www.youtube.com/watch?v=tqHNK67IgG4
At the end of the video, you see that the result of the Proctor test is a curve of moisture content vs compaction - ie, properties of a soil. But that says nothing about how well some specific site is compacted. So I'm curious how one proves that some specific site is adequately compacted to the right depth. Some kind of soil boring test?
Jon,
If you start with Proctor test you get the amount the fill can be compacted and how best to achieve that. It takes the guess work out.
Our warranty provider required confirmatory compaction tests on the fill before the slab could be poured. They used several probes. Some seemed to core the fill, others measure resistance.
A nuclear densometer checks the density in the field. Very likely the same company that did the proctor can provide the field test.
I'm concerned in this quest for the greenest approach to building.
I'm concerned about insects invading foam board in general outside of the building envelope and eliminating a concrete slab(insect barrier) comes with some risk.
I couldn't feel secure about a foam/plywood slab. It's seems not robust enough against insects. Also, a floor drain under a refrigerator is likely to be forgotten and a source of IAQ problems from septic gases. Did I read that wrong?
It's 70F in Southwest Virginia today. Wasps and bees are landing on my houses' south wall. Makes me wan't to live in a concrete bunker.
James,
living in a region with destructive carpenter ants I share your concerns, but not so much in this situation. If the insects get through 5 ft high concrete foundation walls they are already inside, and I'm not sure it matters much whether the foam they destroy is sub-slab, or under the subfloor. I'd be more concerned with an ICF foundation in areas where insect are a problem.
I have yet to see any signs of insect problems in below grade foams in my climate. No termites, some carpenter ants but I have only seen them inside homes that have moisture issues. Our winters tend not to be conducive for most insects. One advantage to living in a climate with 10,000 heating degree days and at least a few days every winter with 100 degree differences between inside and outside temperatures.
Great article! Does anyone have a link to the Mike Guertin metal icf foundation cover? Thank you in advance for your help. - Chris
It's a tip he posted on his Instagram account, @mike_guertin. The post appeared October 30, 2018.
I think the pressure-treated foundation is an interesting idea in combination with the slab-less slab. Would this be pier and beam? Or something like this: https://www.nachi.org/permanent-wood-foundations.htm
WillTe,
I think it would have to be the second, as pier and beam foundations don't have slabs to replace.
The impetus to switch from concrete foundations to pt wood ones seems to have stalled about a decade ago, and I'm not sure carbon concerns are going to be enough to revive them.
Never seen Advantech OSB. What is the advantage over exterior grade T&G plywood ? Is it more resistant to water damage, or is it flatter and less likely to warp?
David,
It is impregnated with wax making it more resistant to water damage, and stiffer than plywood of equal thickness. It doesn't act as a variable perm vapour-retarder the way plywood does though.
Ok, thanks Malcolm. I found a local seller, and the price is essentially the same as Exterior T&G plywood. Leaning towards using this floor system instead of a concrete slab. Just need to find out how the building dept would react.
David,
I've been wondering the same thing. I pester my building inspector with annoying questions all the time. Maybe I'll try this one on him.
Amazing how people prefer to overthink a good idea and waste money in the process.
George, Can you elaborate?
You can get good idea by looking at his posting history.
There, Malcolm knows all and confirms my statement.
If I understand the floor correctly, it consists of moist soil, a .06 perm poly vapor barrier, wood, then 0.006 perm Ditra. Nobody is concerned about the wood eventually rotting in this moisture trap?
I was wondering if this system would work with 1.5'' screed and pex tubes on top of the Advantex. Any thoughts? Would the screed + flooring make it too heavy for the advantex/EPS?
I' m looking for ways to reduce the concrete / portland cement in my build and this seems like an interesting option. Here in Europe they seem to use the thin screed layer for UFH more often than putting the pex directly in the slab, which would seem an easy way to reduce concrete.
I've done the math for a similar floor system as Randy's but with a single layer of Advantech on 2x4 sleepers. The extra weight of 1.5" concrete adds less than 20 lbs per square foot, or about 0.13 lbs per square inch. Foam rated for 15 psi can safely handle 5 psi, so 0.13 psi does not move the needle much. I'd have no qualms at all putting it over a double layer of Advantech.
Here in the US, that kind of screed layer is usually gypsum-based concrete, which is about 25% lighter than conventional concrete. I don't think embodied carbon emissions of gypcrete are any better than regular concrete, though.
Thanks Michael for the quick and very helpful answer.
Re concrete vs. Gypcrete, I agree. My thinking was along the lines of 1.5'' of screed (whether concrete or gypcrete) contains a lot less portland cement than 6'' or 8'' of concrete slab (which I had assumed I would need to do pex UFH). It' s possible gypcrete might even have more portland cement since it has fewer big aggregates, I am going to look into the potential CO2 savings and options to reduce concrete for the whole assembly in more detail.
I looked into changing out one of the layers of Advantech to Warmboard, https://www.warmboard.com/ Warmboard is a plywood flooring with grooves cut for the placement of pex tubing and metal skin to help in heat transfer. Not sure if a similar product is available in Europe. I think I would go to that type of assembly over gypcrete.
Hi @Randy first to say how much I appreciate you sharing the details of your project in the original blog.
I think the European equivalent is something like Uponor's FastTrack, or their knobbly board. Actually I live in Europe but am building in Quebec, so warmboard would be an option. However my initial research suggests it would be cost-prohibitive on my budget, compared to DIY stapling the pex and screeding.
Out of curiosity, why did you decide against the warmboard?
I hadn't thought of the Warmboard assembly until after this build was complete. The homeowner might have gone with that option too. They wanted in-floor heat.
Good luck on your project!
I am a south of Randy in White Bear Lake. Warmboard is very comfortable product. We removed all of our subfloor and replaced with Warmboard and 2 inches of closed cell foam on the exposed exterior walls. For our current 80s house this is great very comfortable solution.
Having done the heat balance on a new PGH design, I will only use warmboard in the bathroom and tile areas. Would use radiant panel in the ceiling for the rest of the house.. A PGH house should be able to use 90F water for heating and 68F water for cooling. If I look at the heat pump graphs the COP should be above 2,0 most of the time.
Radiant panels are similar to Warmboard, they have aluminum diffusers and AL-PEX for the tubing, covered with gypsum. Robert Beans Healthy Heating discusses this in depth.
Log in or become a member to post a comment.
Sign up Log in