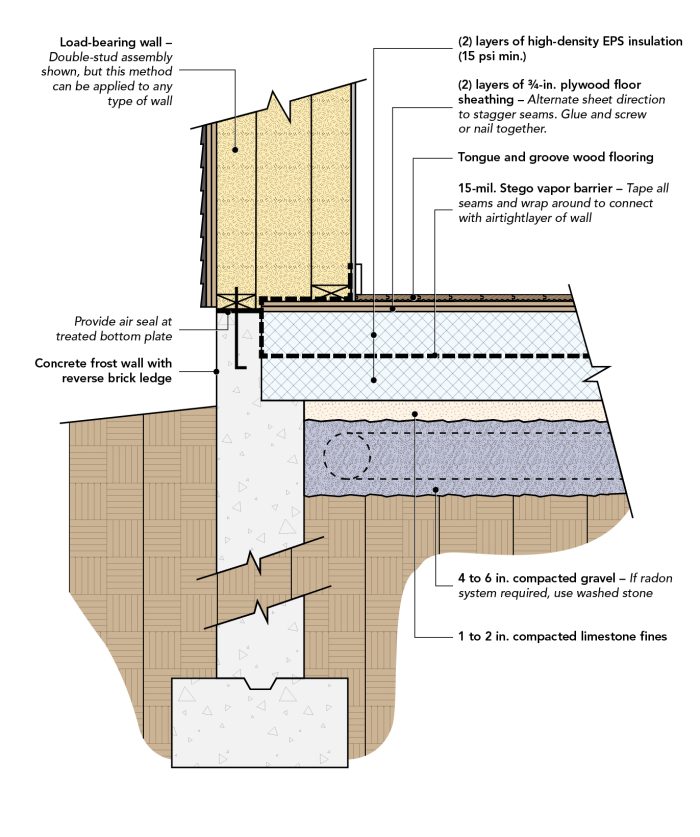
The first time I detailed a “slabless slab” was in 2013. I was working with homeowners who disliked the look and feel of concrete and wanted to install elm flooring they had salvaged. The design plans called for a robust insulation and air-sealing package, which meant an expensive building envelope. To reduce costs—and the overall square footage of heated space—we excluded a basement from the project. That meant we would be doing a slab on grade. But after learning about their flooring preference, the question came up: Why did we need a concrete slab at all? Why not skip the slab and the embodied carbon that comes with it?
This seems to be how many green building pros ended up experimenting with a concrete-free assembly. Today, there are several variations on the concrete-free slab being used in high-performance and Passive houses but 10 years ago, information on the method was limited so there was a learning curve.
A simple system
First, a few quick notes on this assembly: It works in any climate zone, though insulation levels will vary. Depending on the current cost of floor sheathing, wood flooring, and labor, it could offer some savings. I’ve never had a code issue with this system; if it can support a live load of 40 lb. per sq. ft., it’s fine.
The assembly itself is relatively straightforward, but below are some key considerations I learned about from first-hand experience.
Foam density is critical. Everything inside the house will be bearing down on this foam including interior walls. I typically spec high-density (15 psi min.) EPS for below-slab insulation; it works well in this application and is readily available in varying thicknesses and densities. For interior structural loads, I avoid load-bearing walls to avoid a strip footing, which creates a thermal…
Weekly Newsletter
Get building science and energy efficiency advice, plus special offers, in your inbox.
This article is only available to GBA Prime Members
Sign up for a free trial and get instant access to this article as well as GBA’s complete library of premium articles and construction details.
Start Free TrialAlready a member? Log in
37 Comments
Great article.
Any thoughts about whether this could be done for a garage? Can you build a concrete-free slab that stands up to vehicles being parked?
I once helped replace a section of floor in a large stamping plant. Two layers of perpendicular Ibeams made the base structure. Few more layers that I don't recall. But the end product was end grain wood blocks. I'd think you could use those wood blocks for a garage floor. They held up to 60k lb forklift traffic quite well.
Just have a gravel floor?
Gravel is what I have now. It's easy to drop things and lose them. It's uncomfortable to kneel on. It's impossible to sweep. I've been thinking about pouring concrete over the gravel but would rather do something concrete-free.
I wouldn't use it for a garage. It would not stand up to water/ice melt dripping off the cars and the plywood would absorb oil and other car leaks, spills, etc.
Another problem is that code requires non-flammable flooring in a garage.
I'm planning a garage that will be a workshop, and only called a garage for code purposes. I was thinking of doing an insulated ply floor like this and then tiling it, which addresses fire resistant surface requirements. But I don't really have the moisture concerns for my usage. In that case, would that work? Is it IRC compatible? Thanks!
This product lessens the amount of concrete necessary for a floor ...
https://rombus.com.au/concrete-slab/
It is great to see construction design that eliminates the concrete and this is beautiful detailing. I hope it catches on.....
If I had a concern with this approach it would be with perforations of the foam with plumbing, insects and animals that love to burrow through foam and the cost and complexity of this type of cosntuction for average builders. I would be curious to see now if any of the foam was attacked by termines or carpenter ants, or mice. Do you know how it has held up? Perhaps the gravel and fines are a good barrier?
For me the best type of construction is raised floor on treated wood pilings-no concrete and at least 36 inches off the ground. Probably over a million houses are built this way in coastal areas from Massachussets to Texas. Open web 18-24 inch trusses for the flooring system allow for easy movement of plumbing and HVAC, plus plenty of fiberglass or cellulous insulation. The typical foundation can be driven in a few hours and floors laid out the next day.
Hey Nick - I do worry a bit about what we are doing with foam when it comes to termites, ants and other bugs. (For example, when we do perimeter foam for a frost protected shallow foundation.) I'm in Wisconsin, so historically not much for termites, but it sounds like they are coming thanks to warming temps. For this system, being that all the foam is inboard of the concrete, I don't worry too much but I'm considering adding some basic protection like termite shields in the future.
I'm looking at doing a raised floor system with screw piles for an addition we are designing so I think that's also a worthy pursuit. I'm curious how you detail your crawlspace for proper ventilation. (We typically do unvented crawlspaces with concrete frost wall and insulation on wall interior and at grade, robust vapor barrier at grade and no insulation in floor, so heat from the house will reach that crawl space and keep it "conditioned".)
In coastal areas crawl spaces are a bad idea as most houses are in a flood zone and the idea is to raise the living area above the base flood elevation and allow flood waters to course around the pilings. Crawl spaces do not always perform well in floods. And also, the water table is often very high (sometimes 12 inchses under the surface) and gets even higher, especially on barrier islands during very high tides and north east winds. Better to leave it open or surround it with some form of louvers or lattice work so that air (and water in a flood) flow freely through. An insulated chase is built to protect the plumbing from frost and the underside of the floor should be sealed well with hardie board, fiberglass drywall or outdoor plywood-painted and sealed.
Now, to be honest, most folks in these areas don't care about low carbon footprint. And many houses are built at least 8 feet up so that the main floor is above the base flood elevation. These homes usually have the pilings enclosed into a garage using pressure treated 2x4 walls and hardieboard 4x8 sheets as siding. A concrete slab is usually poured and garage doors put in. Two layers of 5/8 drywall are used for the ceiling due to fire code and above that is batt or blown insulation separating the garage from the main living space.Sometimes the garage walls are spray foamed, other times they are left uninsulated (as this level is in the flood zone and thus cannot be living space or the flood insurance goes way up). The walls are often designed to break away in a flood.
Frankly I think making a garage out of the ground level space is a bad idea since (1) the house now has concrete in its construction, (2) the breakaway walls end up as debris in a storm surge flood, and (3) people tend to fill these garages with "stuff" that gets flooded and also ends up as debris in a flood. But Americans like a lot of "stuff" and want to baby their vehicles so.....
Christi,
Great to hear from someone with more than theoretic experience with these. A very minor suggestion:
Wouldn't it make sense to drop the ledge in the stem-wall several inches lower? That would mean the whole of the foam was supported on fill, reducing the chances of differential settlement. It would also allow you to lower the subfloor so it was flush with the top of the stem-wall - meaning all the wall studs could be the same height, simplifying framing.
Malcolm, it looks like a 4" wall above the step, which is pretty skinny--I would want it to be 6" if much taller than shown.
Micheal,
Depending on how thick the exterior framed walls above were (like the ones shown), I wonder if the stem-walls need much of a ledge at all?
Living out here in seismic-land, engineers can be reticent to approve reductions in the width of stem-walls. Instead I've been showing a 3 1/2'" cant on top of the outside. That has a couple of advantages. It gives you some wiggle room if the concrete and sill-plates aren't co-planar, and lets the siding run down slightly to protect the bottom
of the rain-screen cavity.
BTW, I didn't mean to imply we haven't had some excellent advice on these from you, who was one of the first adapters, just that there seem to have been some rather fanciful details being thrown around by people who haven't built one.
Malcolm, for me, in a cold climate, having the step is important more for thermal bridging than to resist differential settlement. My version, designed in 2017, is similar to Christi's but it had a 6" stem above a 12" wall but the 12" was mainly because my structural engineer was concerned about the wall's lateral stability. (https://www.greenbuildingadvisor.com/article/minimizing-concrete-in-a-slab-on-grade-home) We are fortunate to be in an area with low risk of seismic activity.
Michael and Malcolm - I agree that there could be several variations of this detail that could work. I've not had any trouble or push back with a 4" stem as long as it's not too tall. Could easily do a 6" though. Could drop the ledge a bit. Could drop the floor just enough to get the two stud walls to be equal. I think the intention here is to put a detail out that gives a starting point for designers/builders to customize for local conditions and specific preferences.
Maybe better to hold the plywood laters back a bit too so the foam and wall insulation are continuous to each other.
I do think it's critical to avoid disturbing existing soil that will remain, compact all those layers, use the right density of foam in order to avoid much settling at all.
Would I be correct to think this article should come with a warning about performing a soils test before anyone makes plans for a concrete-free slab system in sismic, difficult drainage, contaminates or expansive soils, etc.? I doubt this is a one-size fits all solution.
Armando - Good point. I don't think any detail is one size fits all. Always good to consider what you've got for soil, no matter what details are being used.
Christi, was the system you designed in 2013 similar to the one you show here?
Were you or your engineer concerned about the lack of a lateral connection at the top of the stem wall?
Micheal,
I was circling around that looking at Christi's detail - trying to think up a way to both connect the subfloor with the stem-walls, and still allow the floor assembly to go in after the roof was on.
Michael - I wasn't really concerned with the lack of lateral connection in this frost wall situation being that the top of the wall is above grade and really not much for lateral forces. Different in a basement though, where there is lots of lateral loading from soil pressure, so definitely something to consider. For a house we are building now that has a concrete basement slab with turned up perimeter foam, I called for treated wood blocking between slab and wall every 6' or so. Would love to hear more thoughts on this topic from others.
Christi,
Thanks for the reply. Thinking about it again, there really isn't any appreciable difference in the lateral stability afforded by the subfloor and what a slab would provide, as neither are tied to the stem-walls.
For those in the western part of Canada and the US , an excellent prefabricated and fully engineered concrete free floor system is manufactured by SI-Constructions using EPS foam and structural steel studs. https://sic-sys.com/non-concrete-basement-floors/
They also have a virtually concrete free foundation wall system, where you only need a small concrete strip footing. This system has been used in numerous high performance and passive house buildings in Western Canada
Thanks for sharing this detail Christi. I plan to use it on an upcoming project. Is there a concern about the limestone fines sifting down into the gravel radon bed? Would adding a layer of landscape fabric be a solution?
As for the height of the finish floor compared to the height of the concrete stem wall, I’ll try for a solution that works with an adjustable wood/aluminum door sill for a nearly flush accessible entry, one step up from grade (with plans for a future ramp). I’m interested in your thoughts of this. Amber Westerman
AmberWesterman,
You can also drop the height of the stem-wall under exterior doors to accommodate the threshold, while leaving the rest slightly higher.
Yes - that's what I do when needed.
For those that have done concrete free slabs, have you ever run into issues with banks, valuation, etc in the beginning of a project? For resale value, I'd think there is no issue as long as the final floor is performing just fine. I'm thinking of proposing this for my upcoming project, we weren't planning for a finished concrete floor anyway.
Yes, I consulted on one that Bensonwood was going to put a Unity Home on, their first concrete-free slab. The bank wouldn't approve the system as it's not common. It reminds me of how the insurance companies control our healthcare, rather than the doctors who actually treat us.
As an avid user of health care, I totally understand what you mean. Ok, sounds good. At least it's easy to make the switch in the planning stage.
Would a SIP work in place of the foam/plywood/Stego?
I would be concerned about the OSB under plumbing and near grade.
I like losing the concrete slab, but getting this approach approved in Missouri - well, the term "hell freezes over" comes to mind. As a variation, would it work to lower the insulation to where the insulation is level with the bottom of the ledge and then frame the floor with the appropriate treated 2x's that rest both on the ledge and the insulation? I think it would also be necessary to insulate the exterior of the foundation wall.
It doesn't violate any aspect of the building code. I have thought about your suggested method as well, and it's similar to the one architect Elizabeth DiSalvo has used on several projects going back many years. She shared her experiences here: https://youtu.be/iGXoAN4znTI?si=2izdlPsmaJQ2mZrJ.
I would want to add a filter fabric above the crushed stone to keep the layer of fines from dropping into the stone. (Assuming radon mitigation being used).
Thanks Christi!
I've now done 3 slabless in the last 4 years here in NE WI. Two were in unconditioned spaces (artist gallery/shops) with small heating sources. They love it as when it goes from -10F to above freezing, they are already using the spaces and comfortable. The neighbors can't use their slab spaces for another 2 months due to the cold temps held by all that concrete. Due to the possible spills with their work, I use the dimpled matt under the plywood sub flooring. Being on their feet most of the time, they also appreciate the soft feel for legs and feet. Love the Stego!
Great article!
Re the leak issue, would it be possible to use a water resistant material instead of plywood? For instance, cementitious backer board. The finish would have to be compatible, obviously.
Also, here’s a possibly dumb question: what’s the reason for two layers of plywood? Could it be reduced?
Thanks!
great article and detail. We are looking to do a concrete-free basement in a HPH we are building in Columbus Oh(CZ5). I have form-a-drain footing drain with 6"-8" of 57 gravel run to the top of the footing on the interior. I plan to add a small layer of sand to level out the store before applying a couple of layers of insulation(15 mil vapor barrier sandwiched between) and 2 layers of subfloor on top. Am I overthinking to wonder if laying the sand directly on top of the 57s is a risk for sand settling through the stone and into the form-a-drain?
Log in or become a member to post a comment.
Sign up Log in