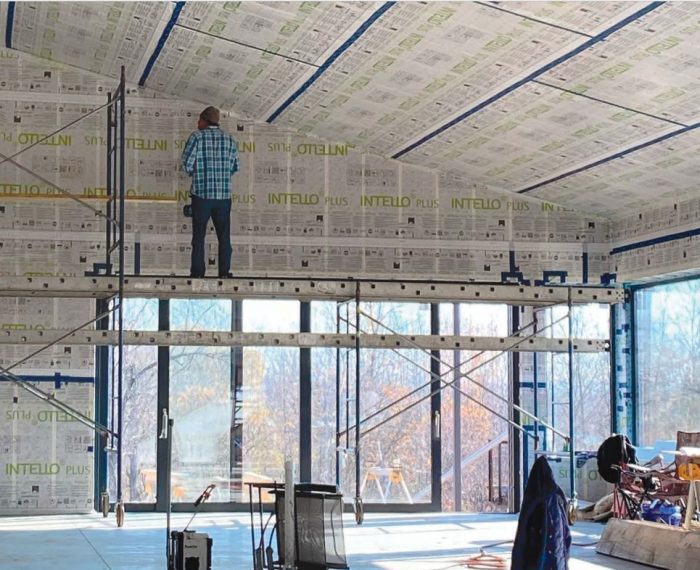
Building code requirements for interior vapor barriers (or vapor retarders) have a sad and shameful history. First introduced in the U.S. in 1948, these code requirements were never based on science—they were based on erroneous theories promoted by manufacturers who were worried about liability issues associated with moisture accumulation in walls. (For more information on the history of these requirements, see “Do I Need a Vapor Retarder?”)
Once these code requirements were established, training manuals for builders regularly reinforced erroneous lessons on vapor diffusion. Scientists now know that most moisture problems in walls originate from rain or air leakage. (During the winter, exfiltrating indoor air carries moisture that can accumulate in or on cold materials, especially in cold climates.) Very few moisture problems in buildings have anything to do with vapor diffusion.
Since 1948, building practices have changed
Although building code requirements for vapor barriers were totally unjustified when they were first established in 1948, there have been three technical developments since then that have changed the way interior vapor retarders affect wall performance.
The first two of these technical developments were the widespread adoption of residential air conditioning and the use of polyethylene as a vapor barrier material. These two technical developments increased the likelihood that interior vapor barriers in warm, humid climates could contribute to moisture problems in walls.
The third technical development was the invention and widespread use of OSB sheathing. Since OSB sheathing replaced sheathing materials that were more vapor-permeable than OSB—materials like boards and plywood—the widespread use of OSB sheathing created, for the first time, a possible justification for the use of interior vapor retarders.
These days, diffusion-related moisture problems in walls are possible—especially in buildings sheathed with OSB. OSB-sheathed walls can’t dry to the exterior as fast as walls sheathed with boards or…
Weekly Newsletter
Get building science and energy efficiency advice, plus special offers, in your inbox.
This article is only available to GBA Prime Members
Sign up for a free trial and get instant access to this article as well as GBA’s complete library of premium articles and construction details.
Start Free TrialAlready a member? Log in
39 Comments
Very timely article. I'm retrofitting an old balloon framed house (Zone 5 Massachusetts) from the inside: removed lathe and plaster on exterior walls, cut and cobble stud bays with recycled rigid foam, running continuous layer of taped and caulked foiled faced rigid foam across studs, then building new 2x3 stud walls inside that filled with batt insulation. The foil-faced continuous rigid foam in middle of wall assembly is air and vapor barrier, but building inspector has inquired about vapor barrier on inside of the new stud wall, which I had assumed should be minimal to allow for drying to the interior. I think kraft faced batt insulation will satisfy him, but is that necessary and would unfaced batt insulation make more sense in this situation.
Stolzberg,
Q. "I think kraft-faced batt insulation will satisfy him, but is that necessary?"
A. The kraft facing is not necessary from a building science perspective. Whether or not it is necessary from a code compliance perspective depends on the ruling of your local code enforcement official, who wields a lot of power when it comes to such rulings.
Q. "Would unfaced batt insulation make more sense in this situation?"
A. Yes, but the kraft facing (though unnecessary) will be harmless.
If it is useful for folks to see the table that's at the heart of this new code section (TABLE R702.7(2)), a screenshot is attached here. Seeing stuff in a tabular/visual format is sometimes easier to digest than text.
I'd characterize the three footnotes as:
(a) You can use a variable-perm vapor retarder anywhere
(b) Don't build a double vapor barrier (Class I on both sides)
(c) If you're using impermeable foam on the outside, here's what you need to do.
Kohta,
Thanks for your helpful comments. I love your characterization of the three footnotes; I wish you were writing the code, instead of the English-challenged specialists who write the code these days.
Thanks also for the comments you sent today in your private email to me; they were perceptive and helpful, and allowed me to correct a few technical errors in my piece.
I work in code development, and I am always appalled by the poor writing -- just bad English prose. They (the many who write codes, usually by consensus in a workgroup with no editors) believe it makes the code more important or technical to use an undecipherable sentence structure. It results in a code normal people cannot easily understand or use.
Kohta -- is that table posted/available elsewhere-when I open it up within the GBA blog, still too small to read.
Doug,
See my comment #5, below, and the attachment to that comment. (Click on the image to enlarge it.) That comment, with its more readable table, was posted 6 days ago.
To see the original table -- designated Table R702.2(1) -- as published in the IRC, use this link.
Kohta,
Here is an easier-to-read version of the code table. The small letters in parentheses refer to the dreaded footnotes.
Anyone interested in reading the original code language should use this link: Vapor retarder requirements in 2021 IRC.
Later edit: I'm also attaching a screen shot of the original image from the International Residential Code.
That link says "Vented classings shall include vinyl, polypropylene, or horizontal aluminum siding, brick veneer with a clear airspace... and other approved ventilated claddings."
I assume anything applied over a furring strip rainsceen qualifies as a ventilated cladding?
Qofmiwok,
The code has always done a poor job of describing what it means by "other approved ventilated claddings." It sounds to me as if they are talking about siding installed over a rainsceen gap, but they don't bother to answer basic questions like, "What is the minimum depth of the gap?" or "Does there need to be a ventilation opening at the bottom of the wall?" or "Does there need to be a ventilation opening at the top of the wall?"
In other words, the phrase "approved ventilated claddings" means whatever your local building official wants it to mean.
While it's clear that plywood performs better than OSB, the two get used here interchangeably depending on the cost of sheet goods. OSB had almost completely disappeared for both single family and multi-unit buildings until the price spike of last spring. Now it's everywhere.
Writing codes is a balancing act. They typically have favoured general rules, which may not be useful in individual circumstances. Now they seem to offer so many options both designers and building inspectors end up confused as to whether projects are compliant or not. Add in government-speak and it's no wonder we end up engaging so many consultants to navigate what should be a much simpler process.
Great article thanks. I read this and the link to the 2010 "Calculating the Minimum Thickness ..." article. I thought I was executing a great plan on my new house but now I'm not so sure. I'm using 2" XPS continuous on the exterior as well as R-21 non-faced fiberglass in 2x6 walls with Class 3 latex paint. However I'm covering the inside of the rimjoist between the I-joists with 1" foil faced polyiso and closed cell foam in the cracks. I thought this was an approved air sealing solution. I specifically chose the foil faced polyiso product because it is rated to be left exposed and not be a fire hazard. But will the interior polyiso and foam prevent evaporation to the interior?
Jim,
It's impossible to provide feedback on your wall insulation plan unless you are willing to tell us your climate zone or geographical location. Your R-10 exterior rigid foam will work if you live in Climate Zone 5, but it will be insufficient if you live in Climate Zone 6, 7, or 8.
It's possible to note, however, that XPS is a poor choice for green builders (unless you are using one of the new climate-friendly types of XPS), since most types of XPS sold in the U.S. are manufactured with a blowing agent that has a high global warming potential. (For more information on this issue, see "Extruded Polystyrene Insulation with Low Global Warming Potential.")
Your plan to use foil-faced polyiso to insulate your rim joist is fine, although 1 inch is rather thin. You could improve your plan (and raise the R-value of the assembly) by installing fitted pieces of rock wool insulation on the interior side of the polyiso.
Of course, more info would have been helpful. I live in Zone 5 in Colorado. I should also say that I have 2.5" XPS insulation exterior to the concrete poured foundation. The idea is that the outer layer of lower, foundation XPS will be in the same plane as the upper 2" of rigid foam exterior of the sheathing making for a nice taped joint. The boundary of the two is about 6" below the mudsill. However the primary air barrier surface will be the OSB sheathing with taped joints. Thus the interior polyiso and spray foam along the rimjoist is really a secondary or even third layer of air penetration defense. But since that area seems to be a typical trouble spot, I'm willing to make that effort. Good point that the 1" doesn't provide much insulation. I've got the R-10 on the outside and I will stuff some amount of fiberglass batting in there as well.
I'm glad to hear that you think that installing the interior polyiso is fine from a water vapor standpoint. But I'm interested in why. If exterior rigid foam blocks vapor release to the outside, wouldn't a foam sandwich block it in both directions? Is it because vapor can't get inside in the first place? Just a small area so it's OK?
BTW, yes rockwool was my first choice but not readily available in my area. XPS was an unfortunate budget choice.
Again, thanks for the great info and advice.
Jim,
You hadn't mentioned in your first comment that the rim joist was insulated on the exterior with 2 inches of XPS. If that's the case, you don't need interior rigid foam for your rim joist. Just install either rock wool insulation (my preference) or unfaced fiberglass batts on the interior.
If you want to air seal any visible cracks on the interior of your mudsill, you can -- just use caulk.
I know it's somewhat controversial, but you can google this site and find articles about OSB not being an effective air barrier.
Excellent summary! I'd like to clarify something.
"Class III vapor retarder if you have vented cladding (brick veneer or siding over a rainscreen gap), or if you have a sufficiently thick layer of continuous exterior rigid foam or semi-rigid mineral wool."
Then you go on to talk more about foam insulation than mineral wool, and even title the section on the ratio table as "Ratio rules for exterior rigid foam".
1. Are you saying that with Class III retarder and vented cladding, you can use any amount of continuous insulation, whether foam or mineral wool?
2. Does that entire section on exterior foam ratio rules for exterior rigid foam also apply to exterior mineral wool? So if you don't have vented cladding, and Class III retarder, you must follow the ratio table?
Thanks
Qofmiwok,
The phrasing in the code -- specifically, in Table R702.2(3) -- doesn't mention rigid foam or semi-rigid mineral wool; instead, it refers to "continuous insulation." Presumably, the code writers were referring to continuous insulation installed on the exterior side of wall sheathing -- but as with many code provisions, the wording isn't as clear as I'd like to see it. That table is the section of the code that allows the use of a Class III vapor retarder where ordinarily a Class I or Class II vapor retarder would be expected. Installing a sufficiently thick layer of continuous insulation allows the builder to change the class of the interior vapor retarder -- from Class I or II to Class III.
Q. "Does that entire section on exterior foam ratio rules for exterior rigid foam also apply to exterior mineral wool?"
A. That's an excellent question. The building science answer is: "With a continuous layer of exterior mineral wool, the ratio rules don't apply, because mineral wool is vapor-permeable enough to allow rapid drying the the exterior."
Evidently the code agrees. According to footnote c of Table 702.7(2), the ratio rules only apply when "foam plastic insulating sheathing" is "installed as continuous insulation on the exterior side of frame walls." In the case of such foam plastic insulating sheathing (that is, continuous exterior rigid foam), the rigid foam must comply with the ratio rules of Table R702.7(4) and the interior vapor retarder must be a smart vapor retarder. Since this language refers to "foam plastic," it does not apply to continuous exterior mineral wool.
Very interesting article. What is unclear to me with the new building code requirements is if those impact ICF buildings in Zone 5-8. I'm using an ICF company that uses BASF Neopor GPS and has a vapour permeance of 2.5-4.0 both sides of the wall (2.5" each side) feels like this could be an issue.
Stephane,
The vapor retarder provisions in R702.7 only apply to "frame walls." These requirements don't apply to walls built with insulated concrete forms (ICFs).
Very timely article for me as well. To make matters even more confusing; builders and architects provide conflicting and outdated advice when asked. I'm in zone 6, but have just decided to use plywood sheathing with a vapor permeable WRB on the outside and Siga Majrex vapor barrier on the inside. The Siga is smart but is only vapor permeable in one direction, inside out.
It's more costly, but I'd rather not keep going in circles on this and having any mold or rot issues in the future.
Try pro clima intello or Partel vara - Vapor permeable both ways
Not sure two way permeable is good in cold climates. The poly was meant to keep moisture from inside the house migrating through the walls during winter. You don't want moisture to move from the house into the walls in the winter time through a diffusion permeable membrane. Problem with poly is in the summer where moisture can condense on cold air conditioned walls and cause mold. The one way Siga allows the wall to dry to the inside during the summer but keeps the moisture from moving into the wall in winter.
That's my understanding from my readings, but maybe the experts can chime in
Allan,
Any Class II vapor retarder will work for your Zone 6 walls. That includes Pro Clima Intello or Siga Majrex, as well as ordinary kraft paper facing. I think the hype about Siga Majrex being a "one-way" vapor retarder is irrelevant in your case.
As with all frame walls, the main issues are ensuring that your penetrations are well flashed (to avoid water entry problems) and that you have paid attention to airtightness. Vapor diffusion isn't much of a worry.
Thank you Martin for the clarification. The confusion in my area is that Class I poly is used as the standard and is assumed to be the code compliant method of vapor retarder by builders and even inspectors. It's been like this for decades. The code actually states 60 ng/(Pa∙s∙m2), which is less than 1 perm, but most builders default to poly.
My takeaway from this is to avoid poly as a vapor retarder and use a Class II retarder based on cost and ease of installation and focus on sealing up air leaks from penetrations.
Allan,
I guess the question is whether interior vapour barriers in cold climates such as Ontario's pose more than a theoretical threat to walls, even when the houses use air conditioning in the summer? Are we seeing the predicted problems in houses there when walls are opened?
Malcolm,
That's a great and relevant question. I've never opened up a wall to see if there is mold or rot. Very few houses are built to the methods and specifications that many discuss here, but they survive. Almost all of them are built to minimum code for maximum profit.
With my current build, I have the opportunity to specify materials and building techniques within the expense and budget that I am comfortable with. It's been a huge challenge to weigh the risk/return of materials and techniques with all the marketing hype from building product manufacturers and anyone with a blog and you tube channel.
This site is a good sounding board. Thanks to all who help!
Can't fathom why we are still obsessed with vapor barriers. It is so problematic and expensive to do well. Money is much better spent on meticulous air sealing, or Aero barrier, and bulk water flashing in just about all climates ? Agreed?
Doug,
Yes and no. The differing permanence of the various materials in any assembly are what keep it safe and functioning. It may not be as important as air-movement or bulk water intrusion, but it isn't something that can be ignored.
Let us not forget the micro-climate in which we build. I'm in zone 5 in Colorado, in a valley. On our side of the valley, we are facing south, so things dry out much more quickly in the winter than our neighbors across facing north. One could say we are semi-arid in our specific location. I am building second story walls with R19 fiberglass in 2x6 walls, then osb, then 1.5 inch xps, then cement board. The roof assembly is 5/8 sheathing on top of 2x10, underneath of which is unfaced fiberglass batting, on top of which is an underlayment of high tech material to last till I can then put on two layers of 2 inch xps per code, then osb with long screws 24 in OC, then another layer of underlayment, then metal or asphalt roofing. It is an unvented roof. I have no qualms about that assembly but hope the building inspector does not either. The point is to follow code but allow for your micro location. It's going to be fine I'm sure.
I am planning a new build in Victoria, BC (zone 4 and marine). Thinking about double stud wall, dense-pack cellulose and plywood sheathing, with an extra layer of plywood on the exterior side of the interior stud frame wall. Of course everything will be properly air sealed. Should I add a layer of rockwood on the exterior prior to the furring strips and siding, or is that unnecessary?
Stephen,
A couple of suggestions:
- Do energy modelling of your building assemblies. Unfortunately on Southern Vancouver Island double walls simply don't make sense. I say unfortunately because I've been looking for an excuse to use them on a project here for a decade, but the walls don't make sense from either an energy saving or comfort perspective. The effort is better used elsewhere in the build.
- Before adopting a vapour-retarding strategy you've seen here on GBA, run it by your building inspector. Many of the ones that practically may work and comply with US codes, don't meet ours. The solution may be simple, like coating the plywood with a vapour-barrier paint, but may also not yield appreciably better results than the ones like poly or variable perm membranes that are usually used.
Stephen,
From a building science perspective, there is no technical reason why you would want to add a layer of mineral wool insulation on the exterior side of a double-stud wall.
If all you are looking for is more R-value, remember that you can achieve any R-value you want, simply by adjusting the spacing between your two 2x4 walls. If you want more R-value, make your wall thicker.
Is there a concern with condensation on cold sheathing which might suggest some roxul on the exterior to keep it warmer? Or is the plywood, furring strips for ventilated rainscreen gap and cellulose enough protection, even in a marine zone? Thanks
Stephen,
With the amount of insulation you will have in the double stud walls, exterior mineral wool won't make an appreciable difference to the temperature of the sheathing.
In any case, with a well air-sealed wall, and a rain-screen to aid drying, sheathing in this climate doesn't experience damage.
Stephen,
I agree with Malcolm. The "warm sheathing" approach is hard to achieve with a double-stud wall, since you have so much insulation between your studs. If you want warm sheathing, stick with a 2x4 wall or a 2x6 wall.
Thanks Everyone. I think I will skip the double stud wall, and just use the regular 2 x 6 stud wall but add Rockwool to the exterior. Victoria is not that cold (although this year they got to - 15 Celcius) but there is a lot of humidity, so that is my larger concern.
Stephen,
Exterior mineral wool will give you a great wall for this climate.
Good luck with your build!
Hi - older article, but newer comment. Hopefully someone chimes in?
Very curious to know what conditions, under IECC 2021, Intello Plus (since that's the photo in the article) can be used. I'd like to include it in an unfinished knee-wall space, but I'm not sure if it meets fire requirements (like, say, FSK paper). Thank you!
Log in or become a member to post a comment.
Sign up Log in