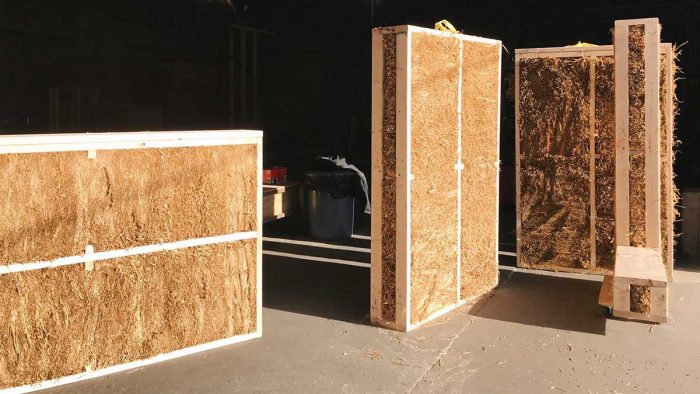
A few months ago, I tasked long-time contributor Scott Gibson with giving GBA readers an update on available tools for calculating a building project’s embodied carbon—or, as I prefer to call it, upfront carbon emissions (a term coined by Lloyd Alter). The published article, “Measuring Embodied Carbon,” elicited this comment from reader Andrew Frederick: “This past year, I started an on-shore U.S. company making off-site compressed straw panels, and the market demand is through the roof. Straw requires some interesting problem-solving to make a homogenous panel, so please, guys and gals, apply your ingenuity and make some too—the market is there. There really isn’t a better bang for your embodied carbon buck than straw.”
I was curious to learn more about Andrew’s venture, so I tracked him down and called him. Croft manufactures high-density compressed-straw panels in Rockland, Maine. Prior to its launch, Andrew was an independent carpenter with architecture training, who specialized in Passive House design and construction. It was a Power Point presentation on embodied carbon by Chris Magwood that completely changed his professional focus.
“It was the first time I’d seen the jaw-dropping fact that high-performance homes—if not built with the right materials—are worse for the climate than a regular code-compliant building,” he says. “Unless something is insulated with cellulose, it’s always worse . . . no matter how long you wait for the energy-efficiency to pay back, you never [recoup] the upfront emissions from manufacturing foam products. As a builder, I felt it was incumbent upon me to use the right materials.”
For him, straw is the right material. But he found its market availability sorely lacking. So, he decided to produce the product he wanted to work with: supercompressed-straw wall and roof panels. He launched Croft in January…
Weekly Newsletter
Get building science and energy efficiency advice, plus special offers, in your inbox.
This article is only available to GBA Prime Members
Sign up for a free trial and get instant access to this article as well as GBA’s complete library of premium articles and construction details.
Start Free TrialAlready a member? Log in
18 Comments
Outstanding to see more buildings being built with straw. Perhaps 12 years ago, I had an opportunity to work on the construction of a traditional straw bale home, and it was one of the highlights of my career so far. That being said, since then I have been thinking of how straw could be integrated with modern air tight construction. As such, I have been very interested in the development of straw cell panels.
Though ever since I first saw pictures from New Frameworks about their straw panel operation, I have been wondering how the panels are fastened to the mudsill. I am having trouble picturing how the straw does not get in the way, when one is threading the nuts onto the foundation bolts every 36” or so.
Also, I have also been wondering weather or not blown in straw is a viable option (chopped up into fine pieces of course).
Any info would be much appreciated,
Ben
Regarding blown in straw...check out rice hull insulation. Rice hulls aren't available everywhere, but in rice growing regions (parts of the SE, Northern California, etc...) they are near free and can be blown in. They've also been tested for fire and rot resistance and meet applicable standards. Presumably they are also a winner carbon wise. A little off topic...these straw panels are very cool.
Hi Ben,
One option is to bolt down a heftier mudsill assembly and utilize structural screws as a connection between that and the panels, we actually utilized a "keying" plate assembly on an early project where a mudsill, sized to fit in the 9" gap between the 2X4 plates of the panel, was bolted to a S.O.G. foundation, and we through-screwed horizontally into that. Fussy and maybe not ideal, but it worked well, and it is great for indexing the panels into a nice straight line. I'm not sure how New Frameworks executes theirs, but I've talked with plastering folks who say it's fine to toe-screw right through the "scratch coat" of plaster, which NF applies in shop.
We've done lots of tests with blown-in straw. So far, not faster, and it requires a very narrow window of fiber length to play nicely with existing blowing equipment. It's possible to source this stuff from animal bedding companies (!), but it moves away from the all-encompassing goal of utilizing materials sourced as locally as possible, with the lowest embodied energy represented in the material.
Very interesting. Thank you for giving me some things to think about. I had never heard of rice hull insulation, always nice to learn something new.
Ben
If the same agricultural land is impoverished of crop residue year after year the soil will become more erodible and less productive. Some balance will need to be struck on the use of these crop residues. Back in the day when we took straw off small grain fields we would take 1/2 and leave 1/2 to retain some of the very important biomass.
You are right! There have been studies done in China regarding carbon content in the soil, and the importance of "soil return". After about 12 years, the C content in the soil is maxed out, and you can significantly drop the amount of C returned to the soil each year without undue harm, and we even offer to pay farmers for that 1/12th of the crop that they return to the soil for this very reason. (This formula changes if farmers need to retain cations or other nutrients that get taken up in the straw, as is the case with one of the largest grain producers here in Maine. In that case, we don't buy their straw, and they put it back into the ground!)
I've got mixed feelings about the use cases. On a technological front, it's worth having. It demonstrates that compressed straw panels can be made, and manufactured. That's important for many reasons, not the least of which is that it can be assembled by carpenters with small changes to work flow. No home builder is going to start stacking wire tied bales of straw into the shape of a house, save a few one off cases. It utilizes a material that can be had 'cheaply', locally, and those are good technologies to know about.
On the other hand, the assembly takes up a lot of room. Those walls are thick! They have to be to get any real R value. I've read the oak ridge studies (1 and 2) that show the R value to be roughly 1.5/in. That's only half as good as fiberglass, and surely costs more than a product that has been optimized to fit in our standard method of residential construction (US at least). There's no mention of borates or other treatment for pest / fire resistance, and having grown up on a farm, densely compacted straw turns bad fast if it is exposed to moisture (not that other materials don't, but I wouldn't trust dense packed straw over dense packed cellulose).
Comparing this wall panel to a 2x6 24" OC wall packed with cellulose, I'm not sure what advantage it offers besides the straw novelty. I think it's cool, but the retail price can't be cheaper than what's currently available.
Hi Kyle,
No shade to the 2X6 wall with cellulose (it's a good wall), but I've never yet had someone complain about having thick walls! We are undertaking ASTM testing soon, but similar panels test out at around R38, which is would require an 11" thick wall with cellulose to achieve.
Straw naturally bioaccumulates silica, and at our densities, both fire and pests don't really get much of a toehold.
We, like any good builder, detail the assemblies to deter both, and as anyone who has ever done an ounce of renovation will tell you, mice, squirrels, and other pests are plenty happy with the current options we give them, such as fiberglass, rockwool, etc.
As for moisture, you are right; we install Omnisense sensors in every project and keep an eye on moisture levels, and are super-diligent during site installs to keep out any bulk water. Additionally, the cut/shaved surface of the straw panels seems to do a remarkable job of wicking moisture away; some destructive wingnut testing in our shop had panels losing remarkable amounts of moisture content in a 24 hr period after being shaved flat.
All in all, so far, so good!
Thanks for the reply Andrew! I think you have a good product, it's the market that needs adjustment. I'm very curious about the results. Do you know the approx. time frame? IE late this year, or early next year? There seems to be a very large range of accepted R values, though I'm not sure I've seen anyone test at your density.
I am a bit confused. Are they using the residue from straw harvesting or are they growing the straw specifically for use in buildings? if the latter, doesn't that take away land from the traditional use of straw in feeding animals in food production? I hope it is the former; we don't need another ethanol like problem sucking farmland away from a hungry world.
If this can be done with left over materials after a harvest, it might be an interesting product in third world countries, where modern insulation materials are way too expensive for most.
Nick-
We get straw from two different sources; one is the leftover "stem" of food crops like wheat, oats, barley, etc. The other, and frankly, my preferred source, is from cover crops. In our region, winter rye is commonly grown between cash crops to stabilize soils and plays well with no-till practices; harvested before maturity, it contains no mature seeds that can cause fermentation issues, and it remains nice and clean because it hasn't been run through the gauntlet of a combine harvester. And it smells nice, which I've never heard a carpenter mention about any other insulation.
My end goal here is NOT to convert more land to agricultural use, and there's no need to: the US already grows plenty, arguably with dubious practices. The numbers are a bit staggering: we could superinsulate every new build in the US using approx. 10% of the straw we will grow this year!
Thanks. Forgive me for being ignorant of farming methods you mention.....As someone who works with African villages, we are seeing huge increases in imported food prices (in part due to inflation in general and in part due to the Russian war on Ukraine), so these days I am particularly nervous about the use of farm land (or farm crops) that might compete with food markets in any way or drive up food prices.... Of course, I like the idea of using materials that would otherwise rot in the field or go to waste.
I think David Arkin missed the biggest obstacle to adoption, which is there being no widespread availability of a ready to install product. For better or worse, that's how building works. There's no way builders I know are going to source straw bales and monkey around weed whacking them into shape, and then figure out how to attach finishes to both sides. That process is what condemns it to a niche technique. It's the equivalent in wood framing of getting a pile of logs delivered to your site. Hopefully Andrew's company can help change that. Good luck to him!
"Andrew is booked through mid 2024." Andrew, do VIPs (i.e. GBA subscribers) get to move ahead in line? :)
These sound amazing and am very interested in pricing info. Last fall I looked into straw panels from New Frameworks, and sorry I don't recall the exact numbers, but they were several x more per SF than standard foam SIPs from someplace like Extreme Panel. Like, not even in the same ballpark. I recognize it's apples and oranges, but they were quickly ruled out as an option, even for someone who's usually OK paying a premium in order to help save the planet.
Best of luck and can't wait to hear more.
Outstanding! Keep the enthusiasm high and keep going forward! Looks like an amazing product.
Ditto... on best of luck and can't wait to hear more.
These guys are right down the road from me, I might need to arrange a visit! There's some cool stuff going on in this region, Go Lab will be manufacturing wood insulation up in Belfast.
Very neat! Andrew, we wish you much success (enough to attract copy-cats and big money).
I wonder if mycelium would add anything to this. The folks at Ecovative Designs (www.ecovative.com) made a splash with their prototype "mushroom" insulation, but have since shifted their focus elsewhere. I played around with their DIY grow kit (https://grow.bio/) a couple years back - it's impressive stuff.
Of course, if the straw panels are good enough as-is, don't fix what isn't broken! :)
I would love to read a long blog detailing the construction of a house with these.
Log in or become a member to post a comment.
Sign up Log in