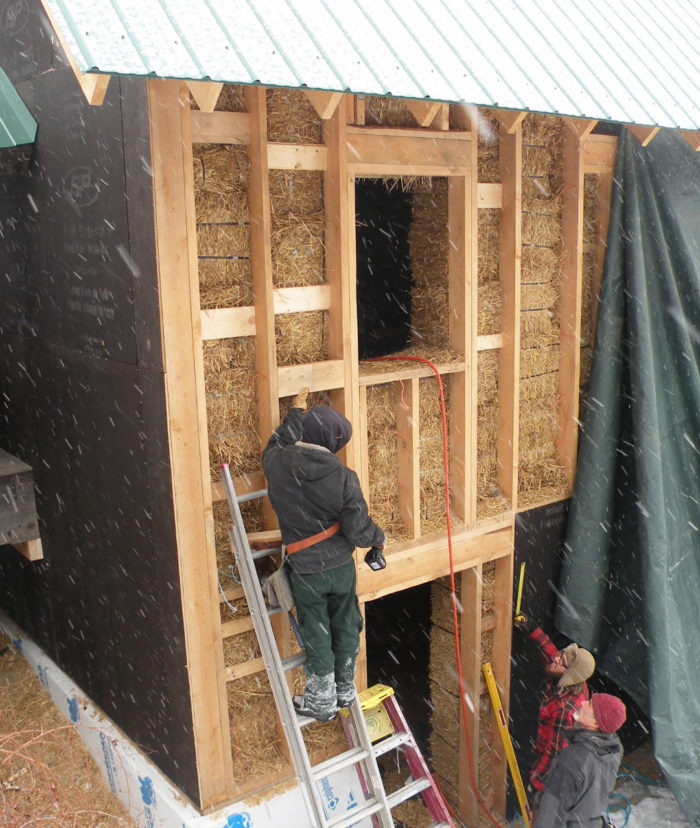
Image Credit: All photos: Ben Graham
Image Credit: All photos: Ben Graham The posts and beams of this second-generation straw-bale home have been fitted with drywall "air fins." These fins connect the plaster on one side of the framing to the plaster on the other side of the framing, ensuring that the interior plaster air barrier is uninterrupted. While the post-and-beam frame of this second-generation building bears the roof load, third-generation straw-bale buildings use a load-bearing 2x4 wall on the exterior of the bales to support the roof load. Another example of the use of air fins to ensure air barrier continuity. Like the house depicted in Image #2, this second-generation straw-bale house has a post-and-beam frame. This straw bale home uses Intello Plus as an air barrier membrane. When straw-bales homes include an exterior stud wall, window installation is simplified.
The mechanical baler was invented in the 1850s (Reynolds, History of Hay Balers), and it’s been a while now since those folks in the Midwest put up a couple of bale houses. You would think that by now we would have very refined construction techniques for straw-bale construction, given that some of those original buildings are still standing. Well, we are getting there.
Let’s call those first bale houses the first generation. The bale houses that came out of the natural building boom in the Southwest during the 1990s I’m going to call the second generation. This was more of a reinvention (along with cob construction), as there was a big gap between the first and second generation, with little continuity or carryover of development.
From that point on, as straw-bale building has spread across the country and the world, there has been a steady development of technique and skill.
The Northeast gets a lot of rain
When straw-bale construction reached the Northeast, builders quickly realized the climate-specific designs from the Southwest and Midwest were not quite appropriate for northern climates. We soon began to adapt by adding bigger roof overhangs and “air fins” to make the walls tighter and more protected. (“Air fins” were developed as part of the second-generation airtight system; they consist of pieces of an airtight material such as drywall that are installed wherever there is a break in the interior plaster. Typical spots requiring air fins are at posts and around windows or doors. The air fin material should allow plaster to bond to it, and should be installed so that it runs continuously — for example, behind a post — to allow the plaster can act as an uninterrupted air barrier. Air fins can be seen in Images #2 and #3, below.)
The classic timber-framed straw-bale wrap kept us busy here in the Northeast for the first ten years of the millennium.
Then something happened to push straw-bale construction into what I am calling its third generation of design: Builders and designers got caught up in the Passivhaus movement. This spurred greater attention to building performance data, and in northern climates builders wanted more than just a bale’s worth of insulation.
New ideas emerge
One result of these developments was a technique pioneered by Mark Hoberecht of Harvestbuild in Columbia Station, Ohio. After getting his Passivhaus certification, Hoberecht began to combine straw-bale with cellulose-insulated wood-framed walls. This was not the first time that happened, but it was the first time I know of where the technique was marketed as a unique design.
Another development was the preassembled straw-bale panel. These panels are being constructed in controlled environments for better outcomes, with specific design features for connections and airtightness.
Adding a stud wall filled with cellulose
I am going to focus on the straw-bale and cellulose combination that we at New Frameworks have developed after engaging in early conversations with Hoberecht in 2012. We had just completed an energy audit of seven houses that we built between 2008 and 2011.
We used Kickstarter to fund a project aimed at understanding the results of our work in order to develop better straw wall details. The conclusion we came to was that we were making progress on developing second-generation straw walls to perform to our rising standards of energy performance, but that (given the constraints of the design) the curve of returns on investment were too steep. Even with our modifications to window details and air fins, we felt that the whole system needed to be rethought, in order to achieve the higher performance we wanted in an easier manner, as well as to make it more affordable.
As we began to think through the idea of adding a load-bearing wood frame to the exterior of the straw wall, we realized there were a host of beneficial opportunities that we wanted to make sure we capitalized on, based on our insights about what made the second-generation straw bale wall design difficult to build.
- A coat of plaster could be eliminated. This was a bit of a paradigm shift for some of us here who had always instructed that bales needed to be fully encased in plaster to preserve and ensure optimal hygrothermal performance. One of the big questions was could the bale system maintain integrity with cellulose blown in against the exterior of the bale? And with the elimination of the exterior plaster coat which was definitely the more costly than the interior, we were looking the end of racing to complete exterior plasters for cold weather.
- Bales could come down to the interior finish floor and we could eliminate the 18” pony wall needed to keep bales off the ground and protected from rain. By placing the stud frame wall to the exterior, the bales were now completely inside the structural shell and do not need to be protected from weather, though they still need to be kept dry.
- There were many more places to secure the bale wall to the structural frame than the typical timber-frame structure.
- Windows and doors are installed just like any other stud frame structure.
- By incorporating interior strapping to sandwich the bales to the stud frame, we could cut the bale strings and eliminate the process of squaring bales and stuffing cracks.
- We could easily add more insulation to achieve our increasing standards for superinsulated structures and make this wall system a candidate for Passivhaus designs.
- Homeowners could choose more conventional wood siding with a rainscreen and a water-resistive barrier (WRB). You could even place your air barrier to the exterior if you wanted.
At this point we knew we were working with a whole new generation of the classic straw-bale wall. With a few projects under our belt and a blower door test result of 0.84 ach50 on a 1,200-square-foot addition — a project where we were aiming for 1.5 ach50 — we are finding it hard to imagine going back.
Ben Graham is a partner in New Frameworks in Plainfield, Vermont. He is a third-generation house builder and woodworker with a bachelor’s of architecture degree from Rhode Island School of Design, a permaculture design certificate, and training in passive house design from PHIUS. Ben’s current work is focused on developing natural building methods that meet the twin goals of high performance standards and low income affordability.
Weekly Newsletter
Get building science and energy efficiency advice, plus special offers, in your inbox.
31 Comments
Why the straw?
I can't help thinking that by the time you have modified straw bale building to this third generation technique, you begin to wonder why have the bales at all? Where the first generation used straw as structure and insulation, you now have three redundant potentially load-bearing structures: The timber frame, the bales and the stud walls. The bales have been relegated to infill. Perhaps this makes sense to use them this way but it seem on the face of it to be a pretty convoluted building system.
Frame Wrap
Ben, great article, seeing natural building methods on this site is about the only reason I keep coming back. I too am a big fan although the nahers are resistance even when you prove some natural building methods out perform factory products by far and are very affordable. Seems to be case everywhere, most have a lack of understanding which is a shame.
I recently read "Natural Building Companion" by some Vermont balers great book.
I'm sure you are aware of new 2015 IRC code. I've asked our B&S office to adopt. One issue we found is obtaining bales that meet code and are construction quality. We need a season lead time and contract with farmers. We got quotes in the $5.00 per small bale price we think we can down to $3. Those are some considerations when considering bales.
I gather your outer frame wrap decision beat out load bearing walls, all cost considered, and the decision was driven by passivhaus goals? Otherwise, in warmer climates like here in midwest 4 with low utility bills the redundant frame is not needed. Load bearing would show a better ROI. I guess what you are also saying is the frame and cellulose cost beats out exterior plaster, stuffing, pinning, and time air sealing as opposed to the conventional interior post and beam. I personally think the aesthetics of an interior post and beam would increase the value of home, showing an ROI for the added labor compared to a dimensional frame wrap there in the NW where green wood is cheap and available. Here in the midwest it has to be shipped in at a high cost, closest being NM.
"By incorporating interior strapping to sandwich the bales to the stud frame, we could cut the bale strings and eliminate the process of squaring bales and stuffing cracks."
This statement confused me. Would you not still want to stuff, and how does interior strapping eliminate the need to square bales....are you saying no need due to the cellulose wrap?
Another question is what are you estimating as an r-value for this bale-cellulose wall?
How do you construct the roof?
How do you stack up straw, hemp, wood, cretes to strawbales. From what I gather, strawbales require alot more detailing starting with the farmer (airfins, etc) to protect the bales against moisture than casted cretes with a render.
Here is a strawcrete mix I created that did an excellent job air sealing a garage door room conversion, much better, less toxic, than popular spray foams. We have much more round bales here, wet ones can be used in a crete. When you cast a crete around a wood frame it also provides resistance to compression, racking, better more protected structure.
We too are testing natural methods on rehabs and additions first then will offer new construction of bales, cretes, earth, along with light construction and hybrids.
Reply to Malcolm.
Malcolm,
I'm guessing these third generation houses use the exterior frame to carry all the roof and floor loads and that the timber frame pictured belongs to some second generation project...
Having the exterior frame certainly seems to make easier many of the "weathering-in" issues that straw bale construction is famous for.
I think the straw infill is just added R value.
I can see the appeal over other alternative means of achieving a similar R value if one is willing to sacrifice some interior square footage for the same size exterior footprint.
Straw bales are cheap, easy to stack, "natural" and in some areas available in abundance locally.
Clarification on pictures and replies to Terry/Malcom
The pictures shown should be clarified as the two images that describe air fins are an example of the second generation bale wrap system with a timber frame. The third generation that is shown here is with the load bearing stud wall to the exterior and no timber frame.
Terry-
Thanks for the feedback, "The Natural Building Companion" was written by my two partners at Newframeworks Ace McArleton and Jacob Racusin.
We have a long term relationship with our bale supplier and have consistent quality that we expect and our supplier knows about. This is important!
Load bearing walls share our system of no timber frame and they don't have to deal with stud frame either so it's easier to get air tight. We simply have not pursued the load bearing system because of higher complexity of structural system. Higher insulation is also a factor.
When we end up cutting the strings on bales they tend to puff up and fill gaps between the bales. Then we just feather them together to eliminate needing to stuff. There may be minor stuffing needed in places, but nothing like the typical process of straw-clay stuffing in 2nd generation systems.
We call this system an R-50 wall. You could certainly use a 2x4 wall and have less insulation.
The roof is framed as a typical roof on balloon framed outer walls. We used trusses in this project.
I like the idea of blowing straw, but we tend to stay away from heavier wall system that incorporate concrete because of the insulation value we are aiming for.
Malcom -
The third generation wall indeed is only supported by stud frame and bales are infill, but no timber frame.
The whole reason we are using straw is to try to incorporate using local materials into construction that have low embodied energy and are non-toxic. This includes the clay plaster air barrier on the inside of the straw wall.
Yes, the first generation and some second generation bale houses used straw as structure also, which is great, but this system has a limited application because of structural considerations. What our goal has been is to make strawbales easily adaptable to modern construction techniques which has seemed convoluted at times but we believe we are getting somewhere.
Granted, there's a lot to tease out here in a short space on a little known topic. I plan to continue this subject in another blog post to expound. Stay tuned.
Ben
Thanks for the clarification - the confusion was mine. Make much more sense now. The third generation seems like a good innovation to have made.
About the photo captions
Ben,
Thanks for clarifying the question about post-and-beam frames for straw-bale homes. I have edited the captions to Images #2 and #3 to make it clear that the homes in those two photos are so-called "second-generation" homes, not third-generation homes.
Nebraska Load Bearing Wall
Ben, there is plenty of data showing more "complexities" and of light construction vs mass or the 1 st generation SB, and I am sure 3rd will create more complexities. The ductile core combined symmetrical stiff skins with high aspects ratio(footprint on the ground with respect to depth) have been proven since it's creation in the late 19th century in Nebraska and abroad, many of which still stand after seeing the same winds and blizzard conditions, flying debri, as stick that ends up distroyed. Last June I visited Piger, OK where twin EF4s destroyed stick but mass homes survived, and there is many more examples. Latest aircraft structure has the same sandwich construction geometry but stronger materials such as graphite skins and phenolic honeycomb core that is replacing stick(web and stiffeners with upper and lower chords or sills) construction for about the past two decades.
They also out perform in high seismic zones like CA: http://nees.unr.edu/projects/straw-house
2015 IRC appendix S provids an easy to follow prescriptive path. The path has the best COP. Please provide data showing 2nd and 3rd generation is stronger.
IMHO, 2nd is structurally redundant, 3rd to use strawbale in cased in stick with redundant cellulose so you have a smaller "embodied energy" makes no sense. You can attach siding to bales. There are other ways to get to a r-50 wall.
Frame the house in stick, use cellulose, rigid, boards, call that stick or mainstream, don't make up another bale "3rd generation" just for sake of claiming lower embodied energy. If you have an abundance of wood and a local cellulose manufacture you are already lower than most.
Load will be transfer to the bales from your stick straps, but not as symetrically efficent as 1st since there is stick, bale, plaster, vs stucco-bale core-plaster.....Same concept as ICI or CIC concrete....I guess the next "gen" ICF is stick/cellulose-concrete-foam SCI?
Terry, so much for a piece of
Terry, so much for a piece of foam whacking a carbon based wing....
By the way my buddy Terry, I have built several flying devices... airplanes... spent time at Rutan's back when he was designing the Eze among other fun designs.
I build surfboards and strip canoes.... we build planes from twigs... geodesic structures... I hate them... lean on the wing and yaa can put your hand through a section. Same with glass over foam.. the foam gives... soft spot.... no good... no more.... we build pontoons for planes... foam sandwich... same problem real strong for the weight but can't take point loads.
yaa... Terry... went to engineering ... RIT.... we can yap about shear and whatever... anytime my friend.
Speaking of non point loads.... foam under a floating slab is not a point load... and any foam is way more able to handle 4" of concrete. Any foam. The concrete is pressing down with .25 pounds per square inch... .25psi is the dead load. Add a human 40psf/144= That's another .2777777777777777777777777777778psi... so the foam has to hold less than 1psi. That's nuttin my man. Forget creep... crap and let's celebrate with some crepes.
How do you add a bar over a number anyone? Terry?
_
7
?
|overline 7
7 text-decoration: overline 7
7
7
Reply to Terry
Firstly, I am not making a case for structural superiority. I am not saying any system here is better than the other, they all have their place. We have chosen the stick frame for its ease of acceptability and flexibility of application.
Taking a step back, what I am trying to describe is a process where a relatively little used construction system is developing over time to accommodate certain priorities.
For us, that is higher performance(insulation, air tightness), more adaptability to conventional construction techniques(stick frame, wood siding) and more economy compared to other bale wall systems and eventually other similar performing wall systems.
In general, natural building aims to use lower embodied energy building systems. Sure, you can just build a double wall with R50 of cellulose and maybe be a little cheaper, and we have done that, but we are not trying to just build the cheapest wall. We are trying to use very low embodied energy materials that are local. We use cell in the outer wall because we are already blowing cell in the ceilings and its practical. We don't see it as redundant but instead taking advantage of the framed space to get more insulation.
We don't see this as a perfect system that is complete but rather a step in a process of changing the way we build to use more insulation and local materials, and less energy and carbon. We think some of the current bale wall systems including the one I have described here on this blog and the prefab bale systems have developed significantly enough to make note.
More on embodied energy
We believe that as buildings become higher performing they use more embodied energy and this becomes a higher percentage of overall embodied energy in the life cycle of a building as they use less energy daily. This means it will be important for buildings to use less embodied energy materials such as foam/metal/plastics/concrete.
Ben
What is the difference in embodied energy? 50%... What are the calculations?
I am a fan of cellulose and reduced embodied energy.
Thanks
Aj
embodied energy
AJ, I am a fan of cellulose too!
Quickly, embodied energy of strawbales - .24- .91 MJ/kg Cellulose - .94-3.3MJ/kg (Gieger;ICE, Bath Univ.) So I would say roughly 1/4 to equal that of cellulose depending on the source.
M. Holladay explains complexity of embodied energy science well in his post
https://www.greenbuildingadvisor.com/blogs/dept/musings/all-about-embodied-energy
We can source bales from within our county and at worst within 100 miles. Typically they are put on a trailer and brought directly to the site.
Bales allow us also to use clay plaster for interior finish.
Clay plaster – 113 MJ, Gypsum board – 6,800-9,942 MJ
(taken from Making Better Buildings, New Society Publishers, 2014)
Another point I haven't made yet is the carbon sequestering ability of strawbales which is not particularly impressive but at least a step in the right direction!
Per unit what
OK, so straw bales have ~1/4 to ~1/3 the embodied energy per kg. But the density of straw bales is about 3 times higher than the density of dense-pack cellulose insulation. So the embodied energy per unit volume is about the same, certainly within the precision of our numbers. And per R-value the embodied energy of cellulose insulation probably comes out lower.
Bottom line: both are great materials in that regard.
Embodied Energy
Charlie wrote: "But the density of straw bales is about 3 times higher than the density of dense-pack cellulose insulation"
Bale code density requirement: 6.5 lbs-ft3, blown cellulose 3.5. ..it gets inspected by weight, along with moisture content with a bale meter.
More density = more compression and bending strength, less r-value. Bales depending on density R 1.3 per inch per code. On-edge (18 thick) R-2. In structural bale design where the bales are taking the load it does get complex balancing r-value and structural strength. I'm sure that is what Ben meant. Good news in you can use code min (100psi + weight of bales) and a PE can get to the desired compression with plasters. Clay allowable = 100 psi(low) cement 1400 psi (high).
Straw has a higher ability to wick and evaporate moisture by capillary action than DPC.
Bale Gen 1 foot print on ground 4" renders, 16" bale = 20" typically set on a rubble trench per code due to the expense and embodied energy of concrete(portland cement). Note cost and EE already high if using concrete. This is structurally the best performer, and lowest in cost. Some use a double stud pony wall(feet) to protect the bales from capillary moisture.
Add 6-8" of footing/slab of concrete or up to 30" for your generation 3? Double stud stick design such as larson much lower...6" total?
Gen 3 Footers
Terry, I will be showing details of this in another blog post, but in our last project we designed the footer to just support the weight of the stud wall. So it was your standard dimension. We didn't widen it for the bales because they are infill. Bales came down on insulation gap between footers and slab.
Gen 3
Sounds good! Looking fwd to it. I be interested to see how this new gen of whomever created it ties into basement walls....Gen 1 taking 20" of distributed load down under can get expensive. I'd also be interested in your air seal effort, since you are using siding on stick and loosing the stucco outer plane, where is your main air and moisture plane? I like gen 1 for it's redundancy.
We're pushing the resurrection here in the midwest, we asked our local B&S office to adopt 2015 that does require bales be strapped to adjacent framing BTW, however I don't see any provision for eliminating bale ties. I have some dense bales now, I don't see them filling gaps without the ties unless I spend effort loosing them where they would abutt. We see high winds and have a profitable business replacing siding motar does not have, gutters, shingle roofs every year that are not designed to take the wind and/or hail. We are also after tornado resistance. I'm all for a "3rd generation" that is internationally or at least national adoptable to all climate zones, and eliminates the limitations of Gen 1-2 improving COP and ROI to the builder and homeowner, otherwise, I see it as a hard sell.
If you set the bales on end your wall is r-36, plaster and stucco provides mass effect DPC and siding does not, so your effective r-value could be r-40 to r-45, and as I said straw has a higher ability to manage moisture. The question then becomes the cost of the additional framing and labor to gain r-5 to r-10 with less mass effect and moisture management (depending on the density of the plaster, clay being the highest in moisture management or breath-ability.
AR105.6.5
Code requires separation of bales and concrete w/cl 2 vapor retarder, 3/4 insulation/ wood or rigid foam, gravel, etc....sill plates are also required, so you have not got rid of the total cost of a pony wall in Gen 3.
Other Considerations
As a co-conspirator with Ben, I want to chime in with a few other considerations for why we are excited about the 3rd Generation straw bale wall system (Straw Bale 3.0?). Ben mentioned or paid reference to these, but I wanted to make sure they didn't get lost in the EE calculations (which are great, BTW).
- In addition to the comparative EE of insulation (say, between straw and cellulose) we also need to consider the interior finishes. The ability to remove all of the interior gypsum wallboard and replace with clay plasters is a major improvement in embodied energy (assuming local sand) and sourcing materials closer to home. Plaster (and here I mean 1" - 1-1/2" clay and/or lime plaster) holds other advantages, including great efficacy as an air barrier, humidity management, durability, aesthetic and creative opportunities (this is a huge one!), and the joy of application. It's important to think comparatively between wall assemblies, not just the insulation in a "BTUs saved per installed $" metric.
- We wanted to find a way to adapt bales more efficiently and logically with stud framing, because timber frames are not practical for many of our projects. This allows many benefits: more trades can engage with a more familiar system, framing costs are lower, and design detailing is greatly simplified
- We wanted the option for a more resilient finish than plaster for high-exposure and/or low-maintenance projects. With this system standard best practice detailing and a wider range of cladding/aesthetic options are available. Perhaps more importantly, maintenance protocols are more conventional and can be executed by a wider range of tradespeople.
- We can do without the exterior coat of plaster as a result of all this, which significantly reduces assembly costs, custom trades, and removes the limitation of needing to build only within the warm season - very short here in Vermont!
- We can get a higher net R-value and achieve very tight assemblies for lesser cost and effort with this system than with a bale-only, timber frame wrap system.
This is a system we've developed responsive to our cold, wet climate. Some of these benefits are less relevant in warmer or dryer climates, and this is perhaps the most important thing to remember when talking about a "straw bale" house - there are many systems, which are all very flexible and adaptable, and depend heavily on climate, aesthetics, scale. So the same way that we wouldn't call out a building as a "cellulose" house and have one system pop into mind, so too are we diversifying our working understanding of this material to respond to the wide range of building forms and needs.
Glad to see this discussion here on GBA, thanks all for contributing!
Strawbale vs Strawcrete
Jacob, what a pleasure seeing you here on GBA, I’m a big fan. Yourself and Ace did an excellent job on “Natural Building Companion”. I highly recommend this book to anyone in construction. Even if you never build a bale home you will learn a lot about building construction. The book is easy to read, lots of pics, and a DVD that takes you to the construction sites for a look see on what is being discussed. As an Engineer that dabbles in several industries, I could tell you covered the basic principles and simplified them, pointing the readers to other material as required. The book is written for the NE climate, but most, if not all of the principles, apply to any climate zone.
Jacob, I gathered from your book your preference was the bale wrap, timber frame infill especially green natural lumber joinery. I have to agree, some beautiful homes you built. Now your preference is a dimensional frame wrap for the reasons stated?
With all due respect, I been testing out strawcrete (and hemp) which has very low EE, trades (IMO less is more to manage), cost. Here, I did a cost out lay of material and labor that shows at or below mainstream, not that I verified with a build yet. As a prime, managing 2-3 subs (frame, cast, renders) vs 8-10 stick pays off, and the casted strawcrete is manufactured on site, outside of the frame. Europe is showing an r-value of 2.5-3 per inch for hemp, can’t imagine it being lower for straw, that depends on mix. From what I understand, hemps higher silica content provides a better bond to lime silica, and the fiber is a little stronger. Hemp is becoming available, CO next to me in it’s first growing season, as are other states. I found the wheat straw is not that much lower. It gets rock hard, prevents racking, adds compression, cellulose does not, and it is not manufactured in a factory, other than the lime which has low EE.
The flexability is huge, by changing out the binder. The potential to eliminate the frame with magnesium cements that are much stronger than Portland cement and do not conduct heat, basalt rebars, geopolymer cements, provides a lot of design flexibility. We also do not have to worry about farmer quality construction grade bales, or protecting them from harvesting to the build. Round bales can be used which are abundant in most parts of the country. Here in the Midwest round bales are everywhere, they can be obtained at a competitive cost. Small square takes a season lead time and advanced purchase contract with the farmer that has to spend a lot of time getting the density and moisture content to code.
True there is no code for hemp or strawcrete but, there is an alternative materials path in IRC. Many areas of the country do not have an energy code from what I understand, the strawcrete is being used as insulation only. You can fasten siding to the exterior, or stucco….you are correct the sculpting and art one can perform with clay plaster and stucco on the outside one cannot do with siding and OSB, I’m talking curb appeal here. Siding-OSB is not as durable and will not get stronger over time. Realtors are loving the idea of homes that do not have the same ol same ol look, I’m talking a new curb appeal which can add or subtract the value of the home.
Attached is a pic of a test wall I have not rendered yet. Here I went with 2 x 6’s @ 24 to save cost, again the aerated cast in place makes the studs stronger and protects them from moisture, rot, fungi, fire, insects, better than the toxic fire retardants and resigns found in siding-osb-plywood, and the air seal is unsurpassed. I understand the benefit of erecting a frame wrap in cold moist weather vs tarps but, once the frame is build a cast would not take more than a day or two, the only issue with rain is too wet of a mix easy to control by cutting back on water. I pulled my forms in an hour, my core was dry in 24 ready for render. It all depends on the mix or the engineering, weather, the labor is simple.
Gen 3? I’m liking aerated cellulose cretes or the “Strawcrete Home” vs “Stawbale Home” and the future of magnesium and geopolymer cements. MGO, etc. I could not find readily available pure MGO except in some lime mortars at low percentages (30-40%). MGO has a huge history that got lost too. I called a local manufacture and it’s not cheap from what I know. I see mag board is replacing gypsum slowly.
Anyway, food for thought :)
The pic is hemp, strawcrete is going on top so I can run some test as soon as the cold weather lets up a bit. It did not freeze in 5F wind chill temps we recently had, it drains well regulates moisture, air, at the surface. I can not get 12" to thermally bride with a 50F delta t.
Rammed Straw
Here is some straw section I added to RE to test on a ext retaining wall before I go to a interior pony wall over a footing that is thermally bridging, cold interior footing I will cast soon. It has held up well to freeze-thaw, no thermal bridging, super strong, as casted. No render required, but I'll do a lime wash since my soil colors were limited and to increase the friable wall. I found stabilizing cements can make all the difference, it's all in the engineered mix. I'm proud of my drain holes although I got a better way to do those next time, hopefully a large arch in a wall.
I think it looks neato too :) The neighbors have been wondering what the heck is going on over there, ;) Lets see realtors, mailman, police even came by for a look see (well they didn't like the piles of mix in the street) ;) ...the sculpting and art is like no other construction method, very full filling, and you can patch mistakes easy. Its been raining, snowing, cold (0-5F) no issues.....
Funny the 6 year old neighbor asked me "isn't that earth wall your building going to wash away?"...I think is parents put him up to ask, I said nope! :)
The upper 3 " course has straw in the mix....
Cretes
Terry, thanks for your kind words and support of the Natural Building Companion, I'm so glad you've found it helpful.
Nice work R&Ding with straw/hemp crete, there seems to be a lot of potential here. We've been looking into hemp-crete as it is showing up more around here - at least more people are trying to sell it and teach about it, which is a start. We've spoken a lot with one distributor and looked at a few off-the-shelf products, and seems like there is a lot going for it for all the reasons you mention. Cost and access of materials is still a huge hurdle, but I trust in time that will shift.
I'm very skeptical of R-values moving much beyond 2/in, based on all relevant/reputable testing I've ever see of straw bale, straw-clay, or wood chip-clay (at true installed densities, not fluffy samples). I don't know a lot about hemp hurds' thermal properties, nor seen any formal tested results (in the US, who may use different standards than European testing depending on the lab) for hemp-crete, but straw bales, which are pure straw and no non-insulating binder, are about 2/in (depending on the orientation). Other fiber clays matrices come in at or below this. Adding lime into the mix won't do the R-value any favors, but I'd be happy to be proved wrong with a test that gives us apples-to-apples comparisons! I've seen so many claims of over-inflated R-values for natural building materials that I take all of those values with a pound of salt until I see the lab report...
The other issue I'm concerned about this the amount of entrained moisture in any wet-wall assembly. I understand that lime cures to hard much faster than a clay-based system, but that doesn't mean the water is all gone - just that a crystalline matrix has been established that stabilizes the wall. The moisture still needs to go somewhere. We've been limited to about 12" thickness for our fiber-clay wall assemblies, and that's when installed during the first part of the summer with good drying conditions. Now perhaps the lime will arrest any significant decomposition during curing/drying, and it may ultimately be a situation that is relatively easy to manage, but I've been burned by built-in moisture in the past, and am wary of how much time it takes to remove moisture from deep within a wall cavity when we are in such a poor drying climate (it's either wet, or cold, or both).
I'd love to see some sensors in a hemp-crete wall putting out real-time data on the drying rate (coupled with interior/exterior RH/temp data), and a solid hot box test to get a comparative R-value. Heck, I'd be love to do that when the right project presents itself! (at least the sensors - I don't have a hot box test in my tool kit) Until then, I have to assume 1) lots of built-in moisture, 2) 12" max wall thickness, 3) ~ R-25 walls (not enough for my taste for new con permanent full-scale residence in this climate) based on all the other fiber-binder matrix walls I've worked with.
I look forward to seeing more testing and development on this front, best of luck in developing out the system and helping lead the way. Get some sensors in there. Share the data!
Cheers,
Jacob
Heat Test
Here is an isolated simple heat test I did on 12" RE, it stayed at the surface, with a 50F delta T after 24 hrs of loading. It may have got to 6" after a week. This is inline with ORNL with dense high OPC that does not have the ability to manage water.....It's hard to say how this would behave in a home, other than looking at what homeowners are saying that is favorable. Assigning an r-value to this is misleading. I'll run hemp today although this is not a pro test, but it gives some idea. I used no OPC at this location, just lime and a pozzolan to stabilize the weak soil.
Response to Terry Lee
Terry,
RE = renewable energy. Or maybe rammed earth?
OPC = Other Project Costs, or maybe Oklahoma Pork Council, or Ontario Police College.
ORNL = is a lab in Tennessee. I've heard of them.
Acronyms
RE= Rammed Earth
OPC= Organic Portland Cement (organic used loosely)
ORNL Hot Box test and calculators = http://web.ornl.gov/sci/roofs+walls/AWT/InteractiveCalculators/index.htm
Building Science Corp (BSC) Hot Box Test= http://www.buildingscience.com/documents/special/content/thermal-metric/BSCThermalMetricSummaryReport_20131021.pdf
Natural Building Methods and Testing
Jacob, I’m not as polished of a writer so excuse my skills. Judging off or your well written book I would venture to say you would LOVE working as a Project or Test Engineer in a lab. The last assignment I had last winter was in MI. I had been involved in some small scale structural testing for large manufactures in the past, but nothing like this for a multi-million dollar test facility. I quit to come home and build natural homes for a living. Mainly metals for the aircraft-industry we ran hot box, wind and hail, shaker table (seismic), thermal cycles, fire, you name it.
It can get very complicated especially troubleshooting or why new design development is failing for which a fault tree is used. Trying to simulate the environment of existing assemblies failing in the field, another challenge. We had customers from all over the world, including Europe (airbus, MBD ( Messier-Bugatti-Dowty's was my last client), hard headed Frenchmen ;) The standards in a world class lab such as this are international. This testing is part of a design process I try to explain out here, but due to cost it is not conducted much in the home construction industry, so we look at what we can understand or a reference “r-value”. For loose or porous material, the r-value accounts for convective and radiative heat transfer THROUGH the material. However it does not account for the radiative or convective properties of the material's surface, which may be an important factor for some applications. We can see there is much more to it than that some try to make sense of with a misleading or good enough r-value. I can identify and appreciate ORNL Dynamic Mass Benefit testing and comparison of mass to insulation. They have a calculator that shows the benefit for concrete compared to FG batt r-value homes, it is quite substantial if designed properly with dense concrete. With a cellulose or clay aerated concrete mix that manages water it would be even higher, if mechanical properties are maintained which is first and foremost. To quantify this would be very expensive but, it could be accomplished better than ORNL wall assembly testing with a scaled down home in a hot box tested to an international standard such as ISO that subjected the test model to most climate zones in the world, such as aircraft sees. To do that for several material compositions alone, would be in the millions, anything less misleading. A team of Engineers would need to be involved in the test plan. The final test results would need to be closely monitored by field builds with instrumented testing designed and monitored by qualified test Engineers. The output would produce design guides and software better than today's, but who has the funding?
Just as heat management dynamics differ from cretes or mass to for example batts or blown insulated wall assemblies, so does water management. BSC did a good job at showing a reduced “-r-value” for moisture-air convective loops in 8 different wall assemblies. If Rammed Earth or cretes manufactured with water had been in the test the results would be different. We know water or moisture has a high influence on heat flux, in some cases it adds a benefit, such as clays-cretes ability to manage it at the surface, now add heat, cold cycles, complex testing that would need more than thermo-couples and stead state r-values.
The best data we have to date is field observations of many crete homes built across the world for centuries. It would be nice to have a database. There is now a handful of hemcrete homes here in the states you can find on the internet starting with NC. There is also an effort I heard of to quantify materials and manufactures to put an end to false claims. This will all help, but as I stated above just as the concrete industry struggles to quantify the benefits of mass, so will the cellulose concrete. It is not as easy as determining steady state heat flux or assigning a value not to exceed 2, it could very likely be higher.
In this respect, it is probably a mistake, or misleading, to use r-value as I have included. It would scare people away from thinking hempcrete or strawcrete can only achieve r-25 @ 12” which is a bad assumption. We have evidence in NC, Georgia, CO, CA, AK, and more are being built that show net zero utility bills, and comfortable homes. Don’t get me wrong, like all building methods cretes have their issues.
For now, unless you understand hemp I’d stay clear of it until there are more test and local availability. There are European distributors, and consultants coming over to the states claiming to teach all about it, seminars, etc, as a last ditch effort imo to losing sales to local farmers. A few, making false claims such as the “hydraulic” lime (NHL 2,3,5) is better than the states and you have to ship in 50 lb bags with a ratio of 2:1 lime-to- hemp which is VERY expensive and ridiculous! If you do the math your wall cost will be 3-5 times higher than stick-batt-blown, and low COP. It’s is the other way around according to the American Lime Association testing. We have the lime, some of the USA lime manufactures, and Engineers I have talked to are producing a binder or looking at it. Europe is trying to beat them to the Home Depo/Lowes shelf. They are also getting down the 3 month drying time (depending on climate) to days in any climate zone. I have my own proprietary blend that dries fast. I fail to see the issue with drying anyway, since lime manages water much better than dense pack cellulose. Its ability to absorb, drain, dry fast, even at the core (depending on binder), re-cure, harden, get wet repeat the cycle, absorb CO2, is totally difference than batts or blown in.
In the meaning time, there is nothing wrong with substituting straw lowering EE and supporting your local farmer, until proper testing proves otherwise.
Baffles me the lack of interest here, if it were a "foam built house" we have all kinds of participation. We have a long way to go in the USA, thanks to books NBC and blogs like these on GBA we will get there :)
Here's one, Northwest "Mushroom Foam Home", $1.2 mil, what a toxic nightmare! I like the sculpting, however COB would have been a better choice. http://www.zillow.com/blog/bethesda-mushroom-house-163230/
Settling?
I am curious how one prevents "settling" of tied or cut string straw? I would think that over time the straw would slowly pull away from the top of the wall cavity and create an uninsulated void. How is this prevented?
BTW, I harvest and sell small square bales of switchgrass straw for biofuel research, to organic growers for mulch, and yes one of my customers even built a straw bale shed using it. He told me the other day he was contemplating a straw bale addition to his house. Made me wonder if a straw bale garage might be in my future.
Settling response
Hey Andrew,
This is a good question in general for bale walls. Without cutting strings, you would typically not experience settling because of the compression of the strings....UNLESS....you applied a single coat of very thick(1+") plaster on a high wall. Then the bales will squish together and we have seen this happen when applied with a spray machine. Typically with thinner coates that are allowed to stiffen a bit, you will not experience settling.
That said, when you cut the strings, you want to make sure you don't see much if any expansion in your wall. With the strings cut you will not see as much settling between bales, but generally the plaster will prevent settling in bale walls because of the bond.
This system I am describing relies on clay plaster being directly bonded to the bales.
To prevent the expansion of the bales, we used a system of strapping that I will describe in subsequent blogs.
Time to think -Inside the box!
I have seen hemp-crete walls in Spain that were performed in a warehouse to facilitate drying time. The system of prefabbing these walls would be similar to pre cast concrete construction set up as far as installation in concerned. Apparently the use of MGO (magnesium oxide)opposed to lyme greatly increase the structural component of the walls to take the load bearing of the building.
I wonder if the addition of paper honeycomb cores to this type of fiber-crete wall would facilitate a workable solution to the strength situation. The research done on paper honeycomb wall dates back to the 1940's and was all the rage at the time. Perhaps its time to revisit this concept. There are numerous products worldwide using honeycomb set-ups already and Chinese manufactures are even using the kraft paper honeycomb cores for wall assemblies exactly the way it was tested in the US over 70 years ago! The in filled honeycomb sandwiches were able to match 2x4 standard construction U-values back then and they were only using 3" cores! These cores have been massed produced worldwide for the longest time and the research is already done. The combination of pre-set fiber-crete with strong honeycomb cores seems like a no-brainer to me.
Apparently this the approach is being pushed by a co. out west called hemp adobe homes. Im not sure what their wall profiles actually are but the gist is; back filled honey comb cores(not paper) sandwiched between MGO inner and outer layers.
Any updates on this technique? The author talks about writing future blog posts about it but i was unable to locate. Has it been deemed a poor choice? If not would love to find some best practices based on experience.
I would love a follow up post as well. When I look on website I don't see this style mentioned but do see they're working on prefab straw panels.
A recent BS + Beer Show included Ben's business partner, Ace, discussing their panelized straw-bale system: https://youtu.be/dUklvUuQyww. They are still using it successfully.
“[Deleted]”
Log in or create an account to post a comment.
Sign up Log in