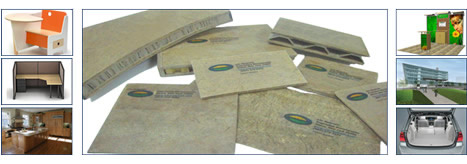
Image Credit: e2e Materials
A startup specializing in high-strength, lightweight biodegradable composites is using the technology to produce a wide range of products, including durable building materials
When it celebrates its grand opening in September, the headquarters of the Syracuse Center of Excellence in Environmental and Energy Systems, in Syracuse, New York, will showcase its role, in a very tangible way, as “a test bed for environmental and energy technologies and building innovations.”
What’s more, the center also will play host, along with Syracuse University, to the Ninth International Healthy Buildings Conference and Exhibition, scheduled for September 13-17.
Needless to say, September will be a huge month for Syracuse CoE. But it also will be big for companies such as “biocomposite” specialist e2e Materials, whose building products are among those used in the headquarters building (which is, appropriately, a LEED Platinum structure).
Based in Ithaca, New York, e2e is gradually putting into production high-strength lightweight composites that are made from biodegradable, annually renewable sources including soy proteins and natural fibers such as jute, flax, and kenaf.
Patrick Govang, e2e’s CEO, points out that the composites, which were developed over a 15-year period by Cornell Professor Anil Netravali, have a wide range of applications. As mentioned in a recent Greentech Media blog, Comet Skateboards uses e2e’s natural composites, rather than fiberglass or carbon fiber, in its skateboard decks.
The challenge to particleboard
In the homebuilding realm, the composites are being used to make components for furniture and cabinets, and for shelving, doors, and building materials, such as sheathing and subflooring, that have been traditionally made with particleboard or MDF.
In addition to their biodegradability and their relative strength, light weight, and durability, Govang cited several other advantages to the use of e2e materials, the most prominent being that they contain no formaldehyde or petrochemicals.
Then there’s e2e’s smaller carbon footprint in manufacturing. Govang says the production of e2e building components requires two-thirds less energy and less raw material than is required for particleboard. “We operate at about half the temperature required to produce typical resin-based panels,” he says. “We also require none of the OSHA equipment to mitigate fumes. So we use less energy, less material.”
The end product, because it is a protein-based material, also serves as a flame retardant. “It’s like trying to burn a piece of dog food,” Govang says.
Although the e2e manufacturing process requires the same size workforce used for particleboard (no jobs are lost, for example, if a particleboard facility is converted to e2e manufacturing), the cost of the product still is competitive, Govang says, noting that even though e2e’s raw-material costs are higher than those for particleboard, the end cost is reduced because less material is used and the manufacturing process is more efficient than turning wood into chips.
The company, which is run by a core team of seven people and assisted by four other organizations contracted to help it get going, recently completed a production run of 2.5×4 panels for use by furniture makers and cabinetmakers, says Govang.
He adds that about 40% of the company’s products, including 4×8 panels that will go into production, will go into residential and commercial construction projects.
At this point, the company’s basic product is called e2e Biocomposite. “We have not yet come up with a formal marketing name,” Govang says.
Weekly Newsletter
Get building science and energy efficiency advice, plus special offers, in your inbox.
One Comment
sustainability and soy base building products
The story of stuff http://www.storyofstuff.com (see e2e website) is well done simplistic and therefore enlighting to the masses. If e2e bases it's sucess in pioneering new sustainable building material partially on soy based products might they also be affecting the food industry (driving up costs by increased demand) much the same as with bio fuels made with corn? Perhaps further thought is required in using food sources as raw materials to develop products for this reason; It drives an increased demand, potentially this is good, more jobs economy boost etc. Increased demand causes development (opportunity to make more money)by seed companies to incure stronger, less disease prone and excellerated growth in plants. To accomplish this seed companies have genetically modified (GM) seeds to meet the demand. Potentially bad since it hasn't been proven this process is healthy in the food chain plus the increase of weed controling chemicals. Chemicals hazardous to any plant not GM prepared. Check out http://www.futureoffood.com or watch the video "The future of food" on u tube. "It''s not easy being green" as kurmit the frog says but a responsible understanding of cause and effect should be practiced in the pusuit of sustainability.
Log in or create an account to post a comment.
Sign up Log in