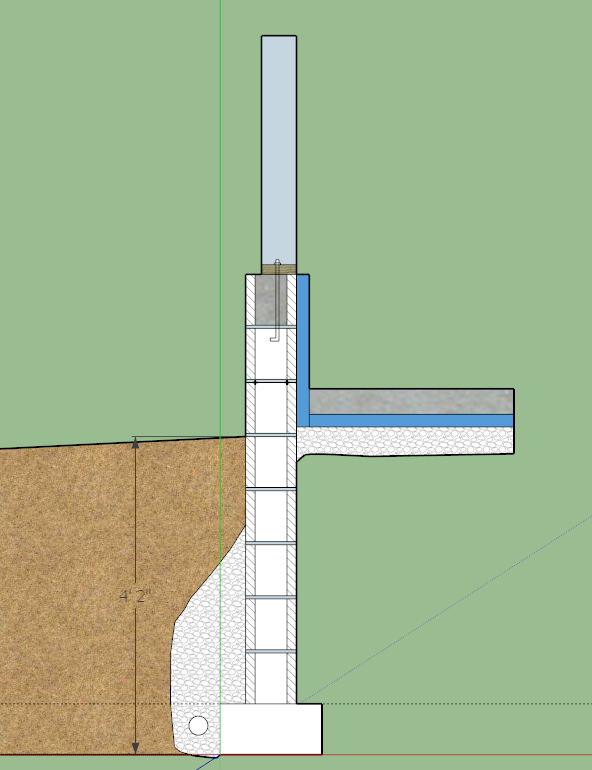
Image Credit: Nathan Scaglione
Nathan Scaglione’s central New York State building site gets plenty of snow and cold weather during the winter, and that’s proving to be a sticking point in his plans for a new house.
He’d prefer a slab-on-grade foundation rather than a basement, even though a full basement would be a more typical choice in this part of the country. The foundation would consist of concrete-block stem walls extending to a footing below frost line. Exterior walls would be framed on top of the block walls, roughly 24 inches above grade. Inside the block walls, Scaglione will pour a concrete slab floor.
As he explains in a Q&A post at Green Building Advisor, Scaglione has seen this detail in garage construction, not necessarily for a house.
“I would like to build on a slab with radiant floor heat,” he writes. “But I really can’t get behind the idea of melting snow sitting up against the stick frame and gradually rotting the walls. For everything except a [frost-protected shallow foundation], code says 16 inches above grade. Ideally I’d like to have the stem walls be 2 feet above grade. With a platform framed house, now we’re talking about the floor being close to 3 feet off the ground. From a design standpoint, I really don’t like being way up off the ground. I’d rather one step down and I’m walking on the grass.”
The drawing Scaglione has provided (above right) includes the basics. The slab would be about 6 inches above grade, and doors would be “about one step off the ground.”
Are there structural problems here that Scaglione is missing? Does this type of foundation have a track record? Those are the questions for the his Q&A Spotlight.
Is there really a rot…
Weekly Newsletter
Get building science and energy efficiency advice, plus special offers, in your inbox.
This article is only available to GBA Prime Members
Sign up for a free trial and get instant access to this article as well as GBA’s complete library of premium articles and construction details.
Start Free TrialAlready a member? Log in
3 Comments
Ants!
When taking into account the possibility that global warming will bring more pests up north, and the conversation about ants in foam (https://www.greenbuildingadvisor.com/blogs/dept/qa-spotlight/if-ants-rigid-foam-should-we-stop-using-it), I've become increasingly worried about relying on foam, particularly in hidden locations like foundations. I'm not sure what to do with this newfound concern, except to build with AAC, rockwool, and foamglass.
Pet anteaters
Adapting to climate change requires considering new approaches.
http://www.livingwithanteaters.com
They are feeding that anteater ants imported from China
... What could possibly go wrong?
https://farm3.static.flickr.com/2041/2216480360_b5a8efc3df_m.jpg
The anteater cost between 5,000 and 8,000 and just eats ants as a treat. They import ants for it "in bulk once a year from China."
In addition, the anteater eats raw ground beef, wheat bran, spinach or thyme and and some other things. They "REALLY love beef and ... blue cheese.
Source: http://www.livingwithanteaters.com/p/anteater-faq.html
Log in or become a member to post a comment.
Sign up Log in