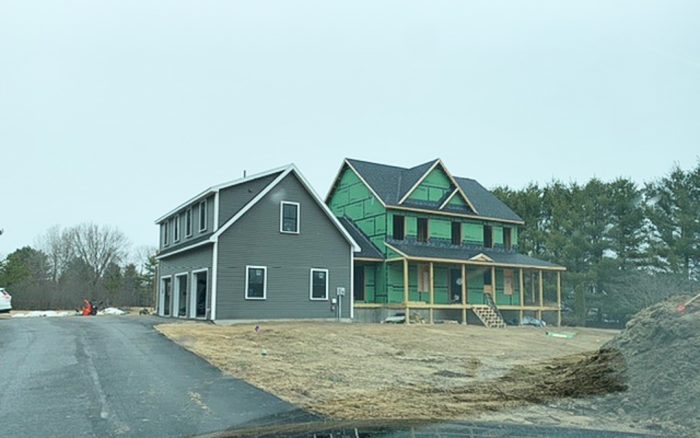
Brenton is building a new house in southern Maine (Climate Zone 6) that he currently plans to insulate with a combination of open- and closed-cell spray foam plus a continuous layer of exterior insulation in the form of R-6 Zip R-sheathing.
He’s willing to take suggestions on that approach, as he explains in this Q&A post, but a more pressing concern is how to heat and cool the house.
“I have been planning on installing a hydronic radiant system throughout the whole house with a wall hung Viessmann Vitodens 100 propane boiler,” Brenton writes. “My wife would like ac for the humid summer months here in Maine so I’ve been considering adding a 5 zone Fujitsu air sourced heat pump.”
“My question is this,” he continues, “would I be better off going solely with heat pumps for my heat and ac and scratch the radiant and put that money into solar? Or should I install the radiant and have the heat pumps for ac and auxiliary heat?”
That’s where we begin this Q&A Spotlight.
First, review your insulation plan
Before discussing heating and cooling, GBA Editor Brian Pontolilo suggests Brenton take a second look at his plans for spray-foam insulation, particularly in the roof where Brenton is planning to use 11 inches of open-cell foam.
“Because you weren’t specific about the roof and venting, I want to point out that when using open cell spray foam in the roof, the assembly should be vented,” Pontolilo says. “Closed-cell spray foam is the only reliable option for beneath the roof deck in an unvented assembly.”
A second option for an unvented roof would be to install rigid foam over the roof deck, which would allow Brenton to use a number of insulation types below the sheathing.
As to…
Weekly Newsletter
Get building science and energy efficiency advice, plus special offers, in your inbox.
This article is only available to GBA Prime Members
Sign up for a free trial and get instant access to this article as well as GBA’s complete library of premium articles and construction details.
Start Free TrialAlready a member? Log in
4 Comments
You might want to think further about the multi-zone heat pump. There are a few studies out there pointing to significant efficiency hit with that equipment vs. 1/1s.
+1!
A 5 zone single compressor heat pump is usually going to be sub-optimally (even CRAZY) oversized for a 1300' code-min or better house, leading to poor latent cooling control and low efficiency short-cycling. A zone per floor using ducted (or ductless- in open floor plan) mini-splits would allow proper sizing, for higher efficiency.
Spending the $20K allotted to the hydronic system on rooftop PV would more than cover the space heating/cooling expenses.
Does anyone find it concerning that an already framed house doesn't have a mechanical system figured out in advance?
My thought as well. We are still trying to figure our systems out and our house is only on paper.
Log in or become a member to post a comment.
Sign up Log in