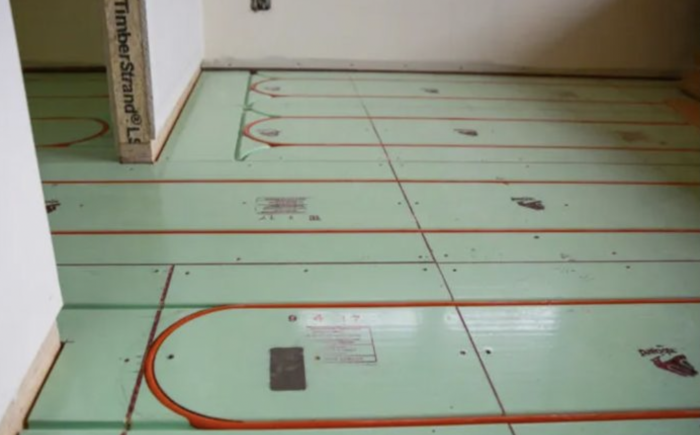
Hydronic heating systems—where water is the medium for transferring heat—use one of several types of radiators, including wall-mounted, baseboard, and those old cast iron classics that stand on the floor. But when someone says “radiant heating” they are usually referring to radiant-floor heating, a heat distribution system that relies on tubing that’s completely hidden from view.
The absence of visible radiators is one of the attractive characteristics of these heating systems. They also run soundlessly. Heat is distributed evenly, quietly, and without the annoying off-and-on modulation of a forced-air system. Homeowners won’t have to arrange furniture to accommodate hot-air registers or bulky radiators. It’s basically a set-it-and-forget-it system.
There are some downsides, too. Among them are high cost, the difficulty of repair in some types of systems, and the inevitable disappointment among homeowners when they discover that their feet will not, in fact, feel warm all winter long.
In short, opinions on these systems are divided. Some homeowners love them. Some designers don’t see a place for radiant-floor heating systems in well-insulated, tightly built homes. Martin Holladay, the former editor at Green Building Advisor, even objects to the term “radiant-floor,” preferring instead the longer but more accurate phrase “in-floor hydronic tubing.”
But let’s start with a look at how these systems are put together, consider the electric radiant alternative, and then turn to the question of whether the same network of tubing that delivers heat in the winter also can cool the living space in summer. (Much of the technical information cited in this article comes from previously published work by Holladay, Alex Wilson and others, which is referenced in the text or in the “Related Articles” list at the bottom of the page.)
Tubing is typically in the floor
Tubing can be placed in the walls or ceiling (Messana is a company that offers this type of system), but radiant floor heating systems are usually built around tubing that’s either stapled to the under side of the floor sheathing (staple-up systems) or embedded in a layer of concrete or gypcrete. Alternately, tubing can be placed in special kind of grooved underlayment before it is capped with the finish flooring.
Tubing is made from a very tough plastic called PEX, short for cross-linked polyethylene. Loops of the tubing are connected to manifolds which are, in turn, fed by a supply line from a boiler or a water heater. The water circulating in the tubing is usually at a lower temperature than water that would supply baseboard or wall-mounted radiators. Even in the dead of a New England winter, circulating water might be only about 80°F.
Concrete floors have a lot of mass, so they are slower to warm up and slower to cool down than a wood floor. Radiantec, a company that specializes in radiant heating systems, says a concrete slab installation is the simplest and most efficient option, as long as it is done correctly. Tubing also can be placed in thin slabs that are installed over wood framing (Radiantec calls these “suspended slab” systems). One thing to keep in mind is that when tubing embedded in concrete springs a leak, repairs will be difficult, messy, and expensive.
Staple-up systems sometimes include aluminum transfer plates that help warm the floor more efficiently. Joist bays may also get a reflective barrier and a layer of insulation to direct heat upward. Warmboard makes a structural subfloor panel that incorporates a reflective layer. It’s grooved to accept PEX tubing.
Hey, my feet are chilly
Homeowners who think a radiant-floor system will guarantee warm feet all winter long may be in for a surprise. In a well insulated house, this is probably not going to happen.
Even on a very cold day the floor will be only a few degrees warmer than the room. If the thermostat is set for 70°, let’s say, the floor temperature will be 75° or so—a lot cooler than the bottom of an unshod foot. If the slab were warmed to the point where it felt like your favorite pair of fleece slippers the room would be overheated.
Well-insulated houses that have been carefully air-sealed have low heating loads. A radiant floor system powered by a boiler that produces 75,000 or 80,000 Btu per hour is overkill, what Theodore Bernstein would call an “atomic flyswatter.” The case for an expensive heating system built around a powerful boiler begins to collapse as the building enclosure becomes better insulated and air-sealed.
Here are a few other issues that frequently come up:
- Are radiant floor systems cheaper to operate? Water temperatures from the boiler can be lower, but savings are unlikely to be significant, according to Wilson’s research. For one thing, circulating pumps that move the water through the tubing have to run a lot.
- Although some proponents of radiant-floor systems argue that homeowners feel comfortable with lower thermostat settings, there’s no data we know of supporting this claim.
- Radiant-floor systems installed in slab-on-grade houses need sufficient insulation beneath the slab to avoid losing a good deal of heat to the earth. If this need isn’t addressed, it could potentially mean higher, not lower, energy consumption.
- Does the tubing have to go in the floor? No. Radiant panels installed in the ceiling are not as common, but as Lloyd Alter notes in this discussion, panels made by Messana have some advantages. They are easier to install, can handle higher water temperatures, and have less of a lag when temperatures are adjusted. Plus, they can be used for cooling as well as heating, providing indoor humidity levels can be controlled.
The electric option
Floors also can be heated with electric mats. Because electricity is a relatively expensive fuel in many parts of the country, electric radiant heat typically is relegated to small areas—a bathroom, for example, where you just want spot heating for short amounts of time.
Electric mats can be installed under tile in a bathroom or mudroom. There also are versions designed for installation under wood, vinyl, and laminate flooring. Nuheat is one manufacturer.
The economics of electric heat depend a lot on whether the house has solar panels that can offset the cost of electricity through net metering, as well as how tight and well insulated the building enclosure is. That’s probably not a big deal when a couple of warming mats are installed around the house.
What about radiant cooling?
Radiant-floor heating systems usually do not include a provision for cooling. The same tubing that circulates hot water in winter could potentially be used to keep people cool in the summer. But while these dual systems are entirely possible, they are, at least so far, rare in U.S. homes.
One reason is the potential for water damage as moisture in the air accumulates on surfaces that have been chilled below the dew point. To avoid this, indoor relative humidity has to be controlled, a more difficult job in parts of the country where latent cooling loads are high. Installing a dedicated dehumidifier is one solution.
Finding a mechanical contractor to design and install a radiant cooling system probably won’t be easy, either. But radiant cooling has been widely used in Europe, according to this article posted at Heating Plumbing Air Conditioning, and has been successfully installed in a variety of commercial buildings in Canada.
_________________________________________________________________________
Scott Gibson is a contributing writer at Fine Homebuilding magazine and Green Building Advisor.
Weekly Newsletter
Get building science and energy efficiency advice, plus special offers, in your inbox.
30 Comments
As appealing as radiant floor heating sounds, it's hard for me to consider it "green building" with the current state of air-to-water heat pumps. Until they're widely available in North America from big name brands and installers feel comfortable installing them, new radiant floor heating is just locking in a combustion boiler.
Paul,
Many of the installations here use an electric resistance heater. In a region with a grid supplied mainly from hydro electricity, it may not be that efficient, but I think it's pretty green.
Thanks Malcolm. Wrong assumption on my part, thanks for your perspective. Are they commonly electric mats or tubing with electric boilers?
Paul,
Mainly pex with electric boilers - often just domestic hot water tanks.
Your point still stands except in the very few areas fortunate enough to have grids as clean as ours.
Agree, but with a slightly different perspective: air-to-water heat pumps are a great technology and we need more of them. They work particularly well with hydronic floors, because the low temperature water needed for the floor makes the COP go up--that benefit is much bigger than the efficiency gain with any combustion boiler. If the popularity of hydronic floors helps drive the market for air-to-water heat pumps, that's a good thing.
Good point! We'll need them for retrofits especially. If there was a more defined delivery date for air-to-water heat pumps from the large manufacturers, my answer would probably be different.
Low distribution water temperature should always be encouraged. Whether operating a heat pump, a condensing gas boiler, or a pellet boiler, low distribution temperature enhances efficiency of the heat producing device. There are proven cost savings with higher COP, condensing vs. non-condensing, and fewer start/stop cycles with for a pellet boiler. It is almost never an advantage for hot water distribution in new or remodeled, efficient buildings to be able to take higher water temperature, as was noted for radiant ceiling panels. The future for distribution is with lower and lower temperatures, whether in water or air. The biggest problem with radiant floor heat of any kind, when placed in an efficient building, especially a building with high insolation, is the inability to accommodate large temperature swings due to insolation or where temperature variation might be desired in a bedroom, for instance. Floor heating systems cannot heat up or cool down quickly. Lastly, floor coverings and furniture weren't mentioned, but when floors are covered over in an unplanned way, which is highly possible as spaces are decorated differently over time, floor heat output can be diminished substantially. Being out of sight and mind can have drawbacks. Kitchens, entries/mudrooms, laundry rooms, and bathrooms are great places for radiant floor heat.
I started out with radiant floor plans, but changed as it became clear how expensive they are for the small amount of heat I need in my almost PassiveHouse. Plus this hot summer is the first time I've felt AC was needed in my climate. So I'm now doing Ditra heat in the baths, Daikin VRV Life heat pump in the rest of the house, some electric resistance heaters in rooms with very small loads.
Now just figuring out whether to do gas or electric water heater and how to heat the garage.
From what I've read, the main advantage of radiant heating/cooling is because radiant surface temperature is one of the key factors in determining (human) occupant comfort levels. That is, we tend to feel the radiant temperature of a surface first over the ambient air temperature.
The main difficulty appears to be in constructing a medium for radiant heating/cooling that could achieve constant temperatures within human comfort levels.
Well particularly with very low heat loads. Much reading convinced me it didn't make sense for very low loads. (Our max load is about 6 BTU/sf and radiant systems are typically set up for 25+)
DC Chan,
The problem though is that in a well-built house the temperature necessary to heat the radiant surfaces to is quite close to that of the air, meaning you don't get that comforting surface heat or cooling.
Thanks for the replies. I didn't get any notifications via email, so I apologize for the late reply.
qofmiwok,
I saw a product at the North America Passive House conference a couple of years ago. Electric radiant heat mats that are installed at the subflooring. Not sure how strong their typical loads are, but I'd imagine they would be low enough to provide heating to PH buildings without overheating. If not, the would pay for a set up a booth at a PH conference?
Malcolm,
You make a good point in highlighting the challenge of using radiant heat in very well-built buildings. Even though air heating (via a minisplit unit, for example) is technically less efficient in transmitting heat to occupants, it is also far easier to control without overheating your space and making the occupants uncomfortable.
Radiant may not be practical for a super insulated house in a mild climate ....
I have used Warmboard on a few projects and it's a nice product -- my current project has it for most of the main living areas of the house. Other parts are slab and one very large room is plates as we did not remove the floor.
New modulating boilers and controls make setups easier -- pumps are smarter and more efficient. It's still the most expensive way to go.
In zone 6 (Minnesota) and have Warmboard on the first and second floor. We keep the bedrooms at 67F and the bathroom floors at 70F. So most of heat comes from the bathroom those are floors that are warm to the toes. The rest of house has an even distribution of heat which is typical of hydronic heat.
Make sure you micro zone and budget for the controls. No need for a boiler, just use a DHW tank and a heat exchanger.
What did you figure per square foot for the total cost including Warmboard, pex, heat exchanger, controls, etc ? Also installation if you didn't do it yourself.
I did the controls and wiring myself using Taco equipment. The carpenters installed the Warmboard and the PEX tubing. The HVAC guys connected the PEX and installed the manifolds, the commissioned the hydronics. We just “did it” — I still have receipts to enter into a spreadsheet.
Hi William,
I live in the Minneapolis area and am tentatively planning to use Warmboard in an house addition but am concerned about summer months and how to cool/dehumidify the house. How did you deal with this in your house?
I would also love to know you thoughts and opinions on using Warmboard in your house.
Love the Warmboard got rid of the slant-fin, the house is very comfortable. We also replaced our A/C with a Trane system. In hind sight, we should have gone with a air to water heat pump and a whole house dehumidifier.
Based on my research, Santa Fe makes one of the better products. I also like the Messana ATU.
For pictures on Warmboard…
https://www.applewoodremodelers.com/birchwood-renovation
The reason I landed on this article is a search for "radiant cooling," but there is not a lot of info or commentary on it. I am building a 1-story 24'x36' cottage and we're doing radiant heating, but want to try radiant cooling too (US residential has to start somewhere).
If we ran a whole-house dehumidifier and cool-enough water through the tubing, is there any reason why this wouldn't work? I am just an ignorant homeowner, but if we can get the humidity out of the house it seems like it should. Thanks for any feedback.
[email protected],
You may find these other articles by Scott useful:
https://www.greenbuildingadvisor.com/article/research-bolsters-hopes-for-radiant-cooling
https://www.greenbuildingadvisor.com/article/in-floor-radiant-cooling
I theory, that's possible. In most climates, you'd want a really good control system that would ensure you never cooled the floor below the dew point.
If you are in the right climate, this might be an efficient option. If you are in a high-summer-humidity climate, it could be worse than a conventional system.
It's doable with a well insulated house and a dedicated dehumidifier. Tekmar has a controller (406) that support radiant cooling. It constantly checks that the water temperature is higher than the dew point. I know some people on this website have been happy with this setup. Just search "tekmar 406".
By the way, check out Robert Bean website too. It's a great ressource if you are interested in radiant cooling.
Thanks to @alexqc and everyone else for the replies. Super helpful! This is why I just re-upped my membership.
A couple of months ago I listened to John Siegenthaler on BS+Beer (https://www.youtube.com/watch?v=7ABZne0KIfo) and unsuccessfully tried contacting him. I'd like an expert to design the system. Any suggestions along these lines would be welcome, too.
Dack
John Siegenthaler is not taking on new projects, as far as I know. You might try Allison Bailes + Co at Energy Vanguard.
Thanks Michael. Allison was a bust, too. Energy Vanguard only does air, no hydronic.
This is so frustrating. I might just buy Siegenthaler's book and design my own system :)
https://www.amazon.com/Modern-Hydronic-Heating-Cooling-Residential/dp/1337904910/
A little surprised by the irreverent attitude here towards 70°f floors. We have a wood stove in the basement and the difference between a 60° floor and an 68° floor is immense, no matter what you're wearing on your feet.
lukepigheti,
I think we come back to whether its a new well insulated house, or an older less efficient one. In the former the floor surfaces should track the air temperature within a degree or two, so you never get those 60F foot chillers, and if you install in-floor heating, that will only increase it by perhaps a few more degrees - say from 70F to 75 - which may not be particularly noticeable.
I like the approach that Akos has suggested in other discussions of using the in-floor heat selectively in areas like kitchens and bathrooms, allowing the floors there to be much hotter - just where you would appreciate it most.
Malcom, you write a huge amount of great stuff on GBA. You are a great resource. 70 to 75 deg F floor temp is extremely noticeable. I've got radiant floor heat and 70 to 75 is just the range of temps from in between radiant runs to on top of the runs in my house on the coldest days. It's clearly obvious walking over it with feet with socks on. While "warm" floors sound romantic, everything at the correct temp is much better. I bought my house with nearly no insulation and the floors were "warm" in the winter. They are much less so now with more insulation wherever I could put it. It's miles more comfortable this way. Radiant systems have problems - they are expensive, intrusive to repair, relatively hard to use a heat pump on, etc. But living with 70-75 deg F floors is a lovely thing.
Erik, are you saying that you notice a big difference in going from 70° floors to 75° floors? Or from 60° to 70-75° floors?
erik_brewster,
As is often the case, I've explained the point I was trying to make poorly.
In a well air-sealed and insulated house, if the floors track the indoor air to within a couple of degrees, without any in-floor heating you are already looking at a floor temperature of 70F. Adding heat to those floors will probably only raise them to somewhere around 75F. I'll defer to your experience as to whether that 5F makes a difference in comfort.
Log in or create an account to post a comment.
Sign up Log in