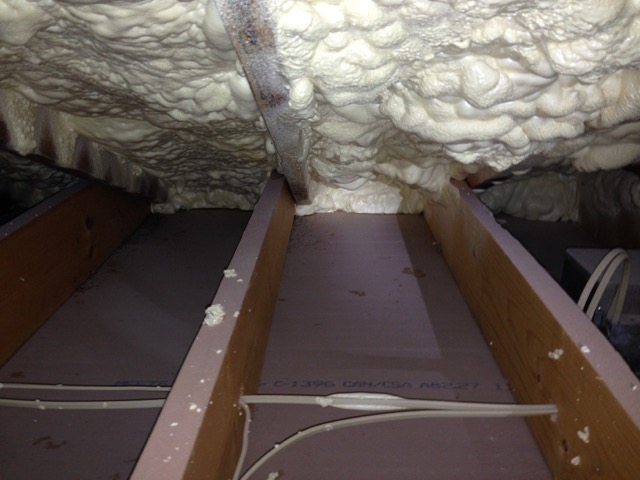
Image Credit: Energy Vanguard
I recently investigated an attic with spray foam insulation where we observed an interesting humidity pattern. We placed data loggers near the ridge and floor of the attic as well as in the living space and outdoors.
The graph at below shows dew point data for the four locations. The really interesting part is the big difference in dew point between the highest and lowest points in the attic, shown by the red and green curves in the graph.
Let’s take a look at the data for the ridge and floor in separate graphs now. The next graph shows the attic floor, and this time I’ve included the relative humidity. As you can see, the humidity, as measured both by dew point and relative humidity (RH), goes up during the day as it gets hotter outdoors and down at night when it cools off. But the humidity near the attic floor never gets out of control. The dew point and RH stay below 70° F and 70% at their peak (the peak of humidity, not the peak height in the attic).
In contrast, the humidity near the ridge in the attic gets very high. The dew point and RH get up close to 90°F and 90%. That’s way too high. On the bad days, when it’s sunny outdoors, the RH stays above 70% for about eight hours per day and above 80% for more than four hours. Not good!
Why is this happening?
This has been a topic of conversation in Joe Lstiburek’s backyard at Building Science Summer Camp for the past three years. In 2014, Foster Lyons, Joe, and I talked a lot about this. Foster, in fact, kept pressing for better explanations and is the one responsible for Joe’s latest article, Ping Pong Water and The Chemical Engineer.
Foster is the chemical engineer alluded to in the title. He loves to talk about chemical potential, which is part of his explanation for what’s going on. If you want a more detailed explanation, including discussion of sorption isotherms and pressure swing adsorption, go read Joe’s article. I’ll give a more simplified version here.
What happens is that moisture makes its way into the attic. This could be from cooking, bathing, and breathing below. It could be from the very humid crawl space. It could be from some mystery source. In the living space of this house, the air conditioner and dehumidifier handle the moisture load and keep the humidity under control. In the attic, there’s nothing to remove the water vapor that finds its way up there.
At night, the roof cools off. The cool OSB roof deck then offers refuge to the water vapor. Wood is hygroscopic, meaning it’s a porous material that can pull water vapor out of the air and store it on the surfaces and in the pores. The lower its temperature, the more it can store.
So all night long, the roof deck is cooling off and storing moisture. When the sun comes out the next day and starts warming the outdoor air and radiating down onto the roof, the roof deck warms up and drives the moisture out.
When the water vapor exits the spray foam, it increases the relative humidity of the layer of air near the foam. Because water vapor is lighter than dry air (mostly nitrogen and oxygen), that layer of air can move upward in the attic. The result is higher humidity at the ridge than at the floor. Lstiburek calls this the ping-pong effect. The water vapor pings and pongs its way to the ridge through the daily cycling.
Another thing might be driving the upward migration as well. A couple of years ago, Bill Rose spoke about this at the Passive House conference, and I think it makes sense. The ridge of the roof has more exposure to the night sky than lower parts of the roof. That can cause it to cool down more than lower parts of the roof. The lower temperatures can help it pull more water vapor in.
The role of open-cell spray foam
Open-cell spray foam insulation doesn’t store the moisture. It’s just a pathway. It has a relatively high vapor permeance (~3 perms), allowing water vapor to migrate to the roof decking at night and back into the attic air in the daytime. It’s the wood decking that stores the moisture.
The photo at right shows a rusty OSB clip in the same house. They had the foam removed and replaced here (because of an off-ratio installation when it was first done) and I got a chance to get up there and inspect the roof deck. I saw a lot of rusty nails and OSB clips. I also saw places where the nails and clips weren’t rusty.
But the corrosion here indicates that moisture was indeed migrating through the foam and finding the roof deck. Well, at least most evidence points in that direction. In an article from a couple of years ago, I wrote about Joe Lstiburek’s research on different underlayments on top of the roof and how he showed that the moisture in the roof deck was not coming from above. The humidity data above show that there was plenty of moisture below. The conclusion is pretty simple. The moisture comes from below.
What’s the solution?
So, how do you fix this, or better yet, prevent it? Well, let’s look at prevention first. If the problem is moisture migrating through relatively permeable foam, you can make it less permeable. Put a vapor retarder on open-cell spray foam. That’s actually required in Climate Zones 5 and higher. Or you can use closed-cell spray foam. Those options would slow down the moisture migration and prevent the problem.
If you don’t do that, you’ve got to reduce the amount of water vapor in the attic. You can do that by directly conditioning the attic with supply air, by blowing conditioned air from the house into the attic, by exhausting air from the attic to outdoors, or by using a dehumidifier.
In his article, Lstiburek mentioned that he had this as a code proposal. I just spoke with him and his proposal passed, so this will be acceptable in the 2018 International Residential Code. Note that it applies only to Climate Zones 1, 2, and 3, though.
The upshot of all this is that open-cell spray foam installations have to change. The days are over when you can spray open-cell foam in an attic, close it up, and walk away. We know now that this can cause problems.
Allison Bailes of Decatur, Georgia, is a speaker, writer, building science consultant, and the author of the Energy Vanguard Blog. Check out his in-depth course, Mastering Building Science at Heatspring Learning Institute, and follow him on Twitter at @EnergyVanguard.
Weekly Newsletter
Get building science and energy efficiency advice, plus special offers, in your inbox.
16 Comments
Allison,Thanks for the
Allison,
Thanks for the article. Looks like Joe L's "Law of Buoyancy" is up to its old tricks again.
I have a few questions for you:
1) I assume the same issue would arise in cathedral/vaulted ceilings?
2) What would happen if the homeowner were to add a couple of inches of ccSP on top of the open cell. Will that forever lock in the moisture and it will play ping pong until the roof rots? Does this mean the homeowner should have the fix done later in the day on a hot, dry sunny afternoon so the vapor is driven out of the foam first?
3) Do you plan on keeping your sensors in so we can see what happens after the homeowner adds ccSP?
4) What would be the best stack-up to avoid this issue with the least amount of environmental impact? Maybe a couple of inches of ccSP on the sheathing followed by either open cell or DP cellulose?
5) In new construction, and assuming the answer to 1 above is yes, do you think it would be safe to just insulate with DP cellulose and a smart vapor retarder or would you recommend a combo of ccSP and DP cellulose?
Thanks,
Jonathan
In looking at the GBA articles, looks like 3 inches of Closed Cell, followed by open cell for remainder of cavity would do ok in Zone5 to prevent vapor from depositing on the roof deck in cathedral ceiling scenario where no access for continuous rigid on top. Is that summarization correct? HERS rater wants r56 in 12 inch rafters. Dont see another way but open to suggestions.
keep the OSB deck warm?
Thanks, Allison. Joe's ping-pong article led to a lively discussion at our company yesterday.
Would a layer of rigid foam on top of the roof deck mitigate this? And if potentially so, will Joe tell us how thick that should be?
If there is no return in the attic, how is the moisture actually removed - or are we just moving it around until the sun comes up?
Response to Todd Eidson
Todd,
Q. "Would a layer of rigid foam on top of the roof deck mitigate this? And if potentially so, will Joe tell us how thick that should be?"
A. Rigid foam above the roof sheathing is preferable in all respects to any type of spray foam between the rafters, and GBA has been advocating the practice of installing rigid foam above the sheathing for many years. For full details concerning minimum thickness requirements for rigid foam above roof sheathing, see these two articles:
How to Install Rigid Foam On Top of Roof Sheathing
Combining Exterior Rigid Foam With Fluffy Insulation
Q. "If there is no return in the attic, how is the moisture actually removed - or are we just moving it around until the sun comes up?"
A. If you pressurize the attic by installing a supply register, the hope is that the attic air will be forced through ceiling cracks into the rooms below. As long as the furnace or air handler keeps blowing, the conditioned air is, in theory, circulating.
A return grille in the attic would be a good idea, except for the fact that building codes have decreed that return grilles in conditioned attics are illegal (due to fire safety concerns). For more information on this issue, see my article, High Humidity in Unvented Conditioned Attics.
attic duct
Thank you Martin.
1. If we see a 15-20 degree temperature drop overnight, then the unit has less of a chance of running. Isn't that the crucial time?
2. Are we going to have to include the additional duct(s) in our Manuals J,S&D?
3. How will the additional duct(s) affect our duct blast test results?
Response to Todd Eidson
Todd,
Q. "If we see a 15-20 degree temperature drop overnight, then the unit has less of a chance of running. Isn't that the crucial time?"
A. Are you talking about a drop in the indoor temperature or the outdoor temperature? I'm guessing that you are talking about the outdoor temperature.
If a house has a sealed conditioned attic, the temperature of the attic should be within 5 F degrees of the rooms downstairs.
I'm not sure what you mean by "the crucial time." The phenomenon we're talking about -- damp roof sheathing and high indoor RH in a conditioned attic -- is a chronic problem, not a "just for a few hours" problem. The need is to lower the average indoor RH in the attic so that everything stays dry. If there is a forced-air register in the attic, the average RH in the attic stays lower than when there is no forced-air register in the attic.
Q. "Are we going to have to include the additional duct(s) in our Manuals J, S & D?"
A. If you are designing a house with a conditioned attic, and if you plan to install a forced-air register in the attic, then it makes sense to include the attic in your Manual J, S, and D calculations. That said, I don't think that including the attic is going to affect these calculations very much.
Q. "How will the additional duct(s) affect our duct blast test results?"
A. The answer depends on the skill of your HVAC contractor. If your duct installer understands duct sealing basics, and uses mastic on all duct seams, then you will always pass your Duct Blaster test with flying colors, first time around. If your contractor doesn't know how to seal duct seams... then you have a problem.
attic duct
OK so the direction we're given is to design a mechanical system with a very specific additional duct(s) that will service a non-occupied, uninhabitable space. This duct(s) needs to be included in our load calculations, despite no return-air for it and without any true latent load associated with it. This duct(s) has to be sealed tight, despite the fact that the whole purpose of it is to actually leak air into the attic.
We've all worked hard for years to get the AHU cabinets tighter and sealed with mastic, the duct boots sealed, the grill registers and can-lights gasketed to the drywall ceiling, all in an effort to minimize leakage into the attic. Now, we actually need that leakage?
If it's 95 outside during the day and the set-point is 72, logic says that the unit is going to run. At night, when the outdoor temperature drops to 70, there is less chance that the unit will run. If it's a constant phenomenon, what will keep the unit running when there is no t-stat in the attic? I read in Allison's piece that "So all night long, the roof deck is cooling off and storing moisture." If the unit runs during the night, the moisture should remain suspended and not absorbed.
Code be-damned, why wouldn't we just cut fake grill registers in the ceilings throughout the house and let the conditioned air move from the occupied space into the attic?
Response to Todd Eidson
Todd,
If you have a "code be damned" attitude, you're right -- you can do anything you want. Any method that encourages air circulation between the lower floors and a conditioned attic will help lower the relative humidity in the attic.
If the attic is conditioned with a supply air register connected to a forced air duct, the attic air will be dehumidified during the day, and there will be less moisture in the attic available for storage in the sheathing at night.
If the air doesn't cross any
If the air doesn't cross any coils how is it dehumidified?
Response to Todd Eidson
Todd,
In the summer, when indoor and outdoor air are often hot and humid, you're right -- you need either an air conditioner or a dehumidifier to lower the humidity of indoor air.
In the winter, when outdoor temperatures are usually cold, indoor relative humidity can be lowered (improved) by ventilating a house with outdoor air.
What's you point?
shoulder seasons?
At the most recent EEBA conference, two sessions showed data that humidity is higher inside homes during the shoulder seasons. This echoes my concern of the nighttime lack of unit operation. I don't understand how only 50cfm/1000sqft of conditioned forced air can dehumidify an attic when there is substantial time when the units simply don't run, on top of the fact there's no return. I get the theory, I just don't get the logic. If the set point is satisfied, there's no moving air.
Seasonal & daily time windows @ Todd
During the fall shoulder season the amount of residual humidity left in the roof deck should be quite small, having come off the cooling season, so it won't much matter if the average indoor humidity rises a bit.
During the winter season the roof deck will accumulate some moisture, despite lower indoor humidity, due to the much lower roof deck temperature.
The attic humidity levels will spike during the early spring shoulder season as the roof deck runs warmer, but there will be at least some heating load to provide dilution from heating air (assuming the same ducts are used for heating as air conditioning). The time of day when attic humidity peaks isn't well correlated with the time of day when the heating load peaks, but there will be at least some drying/dilution going on, since there is at least some air exchange, dampening the ping-pong moisture.
It's really the dead zone of the spring shoulder season when there is little to no heating or cooling load that the daily moisture cycling will peak, but as soon as there is a significant cooling load the drying should happen pretty quickly. The maximum drive of moisture out of the roof deck is at the peak roof deck temperature, which is reasonably well correlated to the time of day when the cooling load is peaking. The peak attic moisture occurs when the peak duty cycle of the AC is happening, displacing the maximally moist air with dry air conditioned air.
Response to Todd Eidson
Todd,
From all reports, Joe Lstiburek's suggestion (installing a supply air register connected to a forced-air heating and cooling system in the sealed attic) works.
That said, there's a lot we still don't know about this phenomenon. If this type of attic makes you nervous, you're not alone. You may want to choose a different approach than using open-cell spray foam in this location, in light of your unease.
Thanks Martin & Dana
Hopefully we won't soon learn that we actually need another whole piece of equipment to deal with this. We build in both Climate Zones 2 & 3. This issue could be a game changer. Thanks very much for your responses.
Molly here. Zone 5 Michigan. 2003 home, balloon framed.
We did the Icynene open cell about 5 years ago. I think air traveling up the baffles by our room was picking up heat and transferring it to the attic. The wall is more like a Cathedral style setup. We had r38 of fiberglass supplemented with 12” of cellulose in the attic itself. . After another year or two of condensation dripping pm swing days, we decided to use open cell icynene to fully enclose the attic space as an unvented unit.we removed the insulation on the floor.
Like most homeowners new to this, we got talked into the “R21” is virtually the same as r49 when you look at the return in value. About 6-8”of icynene. Under roof deck and 3-4” gable ends
Now we have very high humidity on warm day in the attic. Sometimes 65-70% . Temps range within 5-10 degrees of house temp. We have installed an automatic good sized dehumidifier to get some air movement and decrease humidity. Up there.
Ideal solution is to add 6” polyiso to roof deck when we reroof in a couple years. And add 2” exterior rigid insulation to 2x4 walls.
As a temporary solution for the humidity issue, what options to I have? Sprague over with froth pack closed cell to add a vapor barrier? Add rigid panels with seams foamed together? Any suggestion welcome until we can get this fixed.
Molly,
I'm sorry to hear that you got bamboozled by an ignorant or crooked spray foam installer. At this point, operating a dehumidifier as a temporary solution is a good way to go. Your plan to add a continuous layer of exterior rigid foam is a good one.
Log in or create an account to post a comment.
Sign up Log in