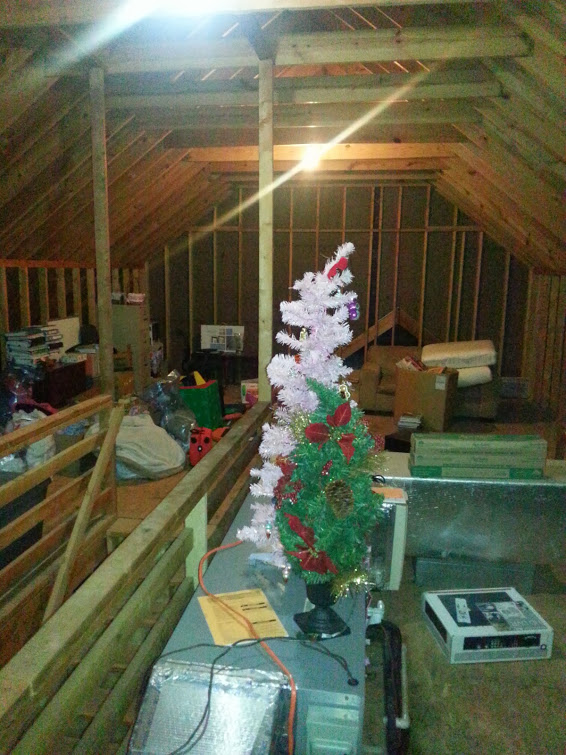
Image Credit: Joe Watson
Joe Watson lives in a three-story 1993 house in Richmond, Virgina, with a walkup attic, part of which he’d like to turn into living space. The question is how.
“I am looking to insulate all the rafters and bring the HVAC into semi-conditioned space,” he writes in a Q&A post at GreenBuildingAdvisor. “I would get a minisplit system for the 20×20 room that would be drywalled in on the third floor. (The rest of the attic space would be left unfinished with a fire barrier of the insulation).”
He’s been told that R-30 will be adequate for his Climate Zone 4 home, and Watson so far is looking at two insulation options: fiberglass batts and spray foam.
“If I go fiberglass, I would attach 2x4s to the 2×8 rafters to give me a space of 10.75 inches to add insulation and leave a gap for a vent from soffit to ridge,” Watson says. “If I go spray foam (professionally done only) I am unsure on open-cell vs. closed-cell in my climate zone. Two of the three quotes I got said open-cell, but could do closed-cell for more $$$ (shocker). I get my third quote tomorrow.
“After reading so many posts/blogs/articles, I am lost on the open-cell vs. closed-cell question for my area,” he continues. “We get really hot in the summer, and, last winter hit the low teens at night (unusual, though). Any thoughts?”
That’s the topic for this Q&A Spotlight.
R-30 worth of insulation just isn’t enough
No matter what his local building office says, Watson’s climate zone calls for more insulation than R-30, says GBA senior editor Martin Holladay. “In your climate zone,” he writes, “the 2012 International Residential Code calls for a minimum of R-49 roof insulation — so even if your…
Weekly Newsletter
Get building science and energy efficiency advice, plus special offers, in your inbox.
This article is only available to GBA Prime Members
Sign up for a free trial and get instant access to this article as well as GBA’s complete library of premium articles and construction details.
Start Free TrialAlready a member? Log in
4 Comments
Unvented Roof with clay shingles
I am in the process of planning a finished attic with the following:
* SE Michigan
* 8 inches of open cell foam applied directly to roof sheathing (8" tongue and groove pine planking).
* The roof is interlocking clay tile on top of tar paper, so there is an air gap between the paper and shingle.
Will I have a moisture problem with the sheathing? Should I apply a vapor barrier to the inside of the rafters? if so, we were planning 5/8 drywall with paint, is this sufficient or should we use taped rigid foam panels?
Response to Adam Warmack
Adam,
A layer of vapor-retarder primer (paint) on the drywall ceiling will be an adequate vapor retarder.
The biggest problem with your plan is that the roof has a low R-value (R-29). Most building codes require at least R-49 insulation in your climate zone (Zone 5).
finished attic air barrier
Membrain is no longer available from any suppliers that I know. We just completed a project where we had orphaned stock shipped in from around the US.
Response to Daniel Hagan
Daniel,
I'm surprised at your statement.
MemBrain is still being promoted at the manufacturer's web site.
Moreover, it is also being listed as available from Home Depot and Menards.
Log in or become a member to post a comment.
Sign up Log in