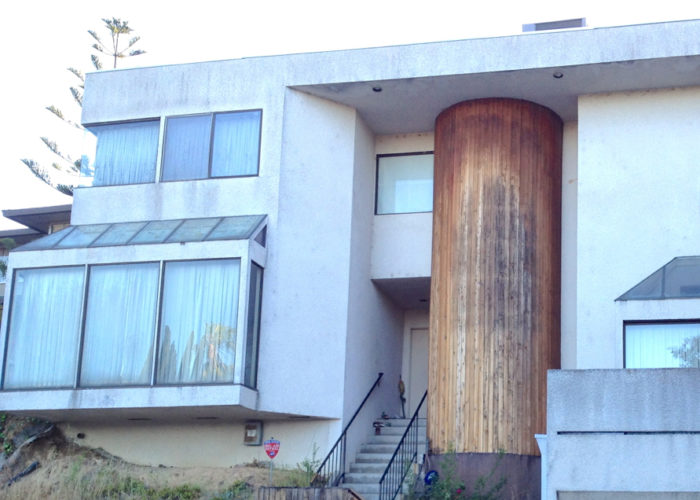
Image Credit: James Morgan
Most of the houses that Atlanta architect Scott West designs are contemporary, and they typically come with flat roofs. Construction often consists of 12-in. deep I-joists or open-web 2×4 trusses capped with oriented strand board (OSB) sheathing. Roofs are unvented, and the use of recessed can lights is probably unavoidable.
The most common options for insulating these roofs, West writes in a post at GreenBuildingAdvisor’s Q&A forum, would include:
- Over the roof sheathing, add an additional layer of OSB installed on tapered 2x furring strips to slope the surface of the roof to drains, and then insulate with R-30 fiberglass batts between the rafters. “Not particularly smart or green in any way,” he says, “and requires extensive air-sealing, but as with most things, the most-common way is most affordable.”
- Place 4 in. of XPS rigid insulation on top of the deck and 4 in. of closed-cell foam on the underside of the deck for a total R-value of about 44.
- Place 4 in. of XPS rigid insulation on top of the decking, 2 in. of closed cell foam under the deck as an air barrier and then add R-30 batts for a total R-value of about 62.
- Skip the XPS above the deck and use sloped decking as in the first option, then use 2 in. of closed-cell foam and fill out the remaining 10 in. of the roof cavity with dense-packed cellulose for a total R-value of about 47.
Among West’s questions are:
“Any help in assessing these options and especially in comparing real-world costs wold be greatly appreciated,” West writes. That’s the topic for this Q&A Spotlight.
First, lose the can lights
…
Weekly Newsletter
Get building science and energy efficiency advice, plus special offers, in your inbox.
This article is only available to GBA Prime Members
Sign up for a free trial and get instant access to this article as well as GBA’s complete library of premium articles and construction details.
Start Free TrialAlready a member? Log in
4 Comments
flat roof
Hello,
There's a lot of good material in this post for comment. Let me just mention that the flat roof as a motif certainly predates 1933. Gropius and Le Corbusier in the 20s sought to capture the machine age by using "industrial" style roofs. It became a unifying motif of the International Style at Mies van der Rohe's Weissenhof Exhibit in Stuttgart in 1927. Richard Pommer from Vassar College wrote several good papers on the cultural context of flat roofs. In Weimar Germany the roof style issue became politically charged, as the conservatives, who favored the heimatschutz (fatherland-style with steep pitches) found the Weissenhof examples to belong more in "a suburb of Jerusalem".
“[Deleted]”
In what world is polyiso 'greener' than EPS? (Purely R-value per inch? That's pretty simplistic. Journalists, please verify the claims of your sources!) If EPS bothers you, look at graphite-EPS. From a sustainability perspective, first avoid spray-applied urethane if at all possible (kills any chance at adaptation/reuse), then Control Your Dew-point! (This has to be region-and-climate-specific.) Nothing is less sustainable than a building that has to be torn down because of mold problems. Most hybrid systems (foam board plus blown-in) serve adequately; it's the holes and gaps (e.g. recessed cans, mechanical systems, or just plain poorly-punchlisted construction) that kill you. And it's worth saying that a well detailed flat roof, particularly protected with ballast and/or a green roof assembly, can last longer than a pitched roof, and thus justify its extra cost.
P.S. Listen to Yost. He's the best at this stuff.
Dr,
I'm curious if you have more to share on EPS vs Polyiso. You seem eager to denounce something but offer no meat to your criticism. What's the story. Share the 'world' we should become familiar with.
Log in or become a member to post a comment.
Sign up Log in