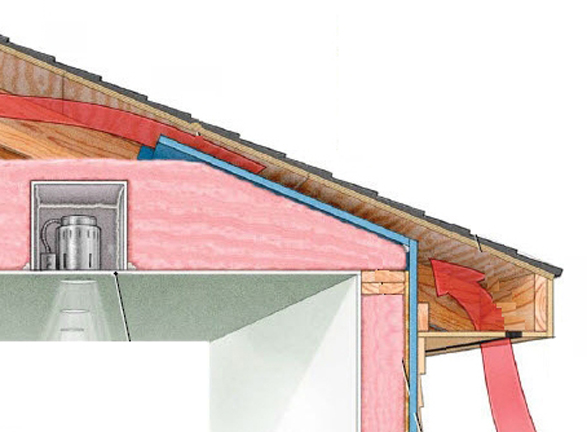
In most of the U.S. — everywhere but Climate Zone 1 — building codes require the installation of ceiling insulation rated at R-38 or R-49. Achieving these R-values with cellulose or fiberglass requires at least 11 inches of insulation for R-38, or 14 inches for R-49.
These R-value targets are fairly easy to meet for a new house, as long as the designer and builder plan ahead. (For more on new homes, see “Raised-Heel Trusses Make Better Enclosures.”) But owners of older homes — homes built before thick ceiling insulation was code-mandated — often discover that the attic lacks enough room near the eaves to accommodate minimum amounts of insulation. In many cases, the vertical distance between the top plates of the exterior walls and the underside of the roof sheathing is only 6 or 7 inches.
This problem can occur in homes with almost any roof configuration, including those with an attic above a horizontal ceiling as well as those with a cathedral ceiling framed with 2×6 or 2×8 rafters.
“It’s good enough”
It’s common for owners of older homes to post questions on GBA about installing attic insulation. A typical question might read, “When I visited my attic, I found that the attic floor has only 6 inches of insulation. I want to add enough insulation to achieve R-49, but there isn’t enough space between the top plates of the exterior walls and the roof sheathing. What should I do?”
For decades, the typical “solution” to this problem was to install ventilation baffles near the eaves — connecting the air space above the soffit vents with the attic — and then to install as much fluffy insulation (usually fiberglass or cellulose) as there was room for between the top plate of the exterior wall and the ventilation baffle. In other words, call it “good enough” and…
…
Weekly Newsletter
Get building science and energy efficiency advice, plus special offers, in your inbox.
This article is only available to GBA Prime Members
Sign up for a free trial and get instant access to this article as well as GBA’s complete library of premium articles and construction details.
Start Free TrialAlready a member? Log in
13 Comments
Martin, you were right on with the recommendation to me. Closed cell spray foam to the distance inboard where at least 16" of cellulose can be achieved. In our case it was 5' in because of the 4:1 hip roof. With bird cut rafters all I had was 3.5" at the outer edge of the exterior wall plate after the site built foam baffles (3/4" XPS) were installed. With the 9" of insulation on the outside wall up to that baffle, we've not seen any sweating near the shower in winter and the house is so much warmer. Thanks again, PK (One Man's Quest for Energy Independence; Parts 1-4).
Paul,
I'm glad my advice worked for you. It's certainly true that the owner of an old house often has to come up with an affordable solution that is the best option, even if that solution is imperfect.
It's good to hear that 9 inches of closed-cell spray foam solved your moisture problems and kept your house warmer. (Not too surprising, considering that 9 inches of closed-cell spray foam is about R-58 of foam.)
If you have 9 foot ceilings but don't want to redo the entire ceiling by dropping the whole thing, could you just drop the ceiling around the perimeter of the house in the form of a continuous soffit and fill that with insulation? Maybe there's a fire code violation there I don't know about.
Mateo,
Interior soffits, bulkheads or trays can be easily built to meet fire codes. In many instances the insulation alone suffices, in others they just need fire blocking between the studs.
In response to Comment #3:
Mateo,
Continuous insulation that (at least) meets minimum code requirements is always the best approach.
If you are interested in addressing this problem by trying to beef up the insulation at the perimeter of the room, you should read the discussion in one of the Q&A threads I referenced in my article ("Interior insulated cornice for use under low-heel roof trusses?").
The main problems with the "perimeter" approach are (a) builders often underestimate the width of the insulation needed to make a significant difference, and (b) most of these solutions have problems with air barrier continuity, since these solutions are usually installed under an existing ceiling. If there are hidden air leakage pathways above the existing ceiling -- a very common problem -- then any attempt to fix the problem by adding insulation in the interior side of the ceiling is doomed to failure.
So, when in doubt -- rip out the ceiling so you can (a) see what's going on, and (b) address hidden air leakage pathways before improving the R-value of your ceiling.
You mention "you also need to install a second layer of roof sheathing above the rigid foam" . But isn't it OK to apply a single ply membrane, for example TPO, directly to the top of polyiso foam? I am certain that happens in commercial applications. Or is polyiso not considered a rigid foam?
User 6925549,
While most roofs with a continuous layer of rigid foam above the roof sheathing require a second layer of roof sheathing above the rigid foam, you are correct that there are at least two exceptions to this rule:
1. As you note, it's possible to skip the second layer of roof sheathing if the roof is flat (or if the roof has a very low slope) and you intend to install certain types of membrane roofing. That said, most roofers prefer to install a coverboard between the rigid foam and the membrane roofing. This approach isn't used for roofs with a steep slope.
2. It's also possible to skip the second layer of roof sheathing if you are installing certain types of metal roofing -- the types that allow installation over 1x4 or 2x4 purlins spaced 24 inches on center. Installing purlins is usually less expensive than installing OSB or plywood. Before adopting this approach, however, it's necessary to check with the roofing manufacturer to determine whether the manufacturer requires solid sheathing.
The linked-to article implies that the problem is not so much lack of room for insulation at the eaves but the presence of thermal bridges at the eaves. So is the idea that the cold roof is conducting heat out of the bottom chord of the truss where it meets the rafter at the eave, and that the coldness is creeping down the truss away from the eave far enough to create a cold stripe effect? That would pull heat out of the top plate and wall framing in the same manner I suppose.
If that is the case, are we installing raised heel trusses primarily to get insulation in there or rather to lengthen the thermal bridge formed by the trusses themselves?
Also, would it help to insulate inside the eaves, between the top plate/wall and the vent holes of the soffit?
I've attached a (crooked) picture of my eaves. Fascia on left, top plate on right. There is a slightly raised heel. Won't the roof be coupled to the top plate and wall by radiation if I don't fill the space in between with insulation?
Granted it seems like a tedious task.
Response to Gordon Franke (Comments #7 and #8):
Gordon,
Both issues matter -- the R-value of the insulation and the presence of thermal bridges. Ideally, a high percentage (up to 100%) of the code-mandated R-value of the roof assembly would be above the roof sheathing. This approach (installing a continuous layer of rigid foam above the roof sheathing) reduces or eliminates thermal bridging through the framing.
It's important to have a wind-washing dam that separates the soffit area from the insulation. This wind-washing dam is usually located somewhere near the plane of the exterior wall sheathing, although you could locate it a little farther toward the fascia if you wanted to, as long as the wind-washing dam doesn't cover the ventilation holes in the soffit.
Martin,
Thanks for the article.
I’m redoing our bathroom and part of that included tearing out the old, failing plaster ceiling. I’m trying to improve the overall air tightness and insulation since we have easy access from below. Our house has 2x6 ceiling joists and 2x8 rafters, vented attic, and we live in zone 5 and neighbor a zone 6. The house was built in 1959 so not much original thought to insulation at the eaves, or in general. The house has soffit, gable, and ridge vent.
So far I’ve installed 1”x 2” furring strips (wish I had room for a 2” space but 1.5” it seemed like a good compromise) to the rafters up against the roof decking then foamed in sheets of 3/4” EPS foam. I then used the cut and cobble method to install a couple layers of XPS foam(had some leftover from another project). I got 3 plus inches of XPS at the exterior edge of the top plate and 5 inches of XPS 3 inches inward of the top plate. Should I add more foam inward or will stopping here and then blowing in cellulose give me the same performance? I was thinking about adding more XPS layers from the baffle downward to the joist, only far enough inward so I could install a deep enough blanket of cellulose. I would then blow in cellulose between the drywall and foam so there wasn’t cellulose trapped between foam layers. I’m hoping to shoot for cellulose with a R60 in the deepest parts of the attic. In the bathroom I plan on installing 5/8 moist resistant drywall on the walls as well as the ceiling.
Also is adding netting for cellulose to the joists before drywall worth it?
Appreciate any advice.
Thanks,
Ryan
Ryan,
You've got the right idea. You've got R-15 of insulation now at the edge of the top plate, and R-25 insulation further in. That's less than code requirements, but you're doing what you can.
If you can afford to buy a two-component spray foam kit -- they cost several hundred dollars -- you could install spray foam on the interior of your cut-and-cobble job, in whatever thickness you can afford.
Your cellulose insulation should be installed after your ceiling drywall goes up. The ceiling drywall should be installed in an airtight manner. You don't need netting for the cellulose -- netting is for walls.
Martin, thanks for the quick response.
I'll do some more research on the spray foam kits. I've always steered away from those kits because of the negative enviromental impacts regarding the disposal process. Do most of these kits use open cell or closed cell foam?
I think if I count the R value of the EPS baffle I'm at 18 value on outside edge and 28 to maybe 30 just inward of the wall. Let's hope the XPS holds it R value for a few decades. I know this work is less than ideal and doesn't meet new codes. I guess its a valid reason as to why old homes shouldn't last forever.
Thanks for your expertise,
Ryan
Log in or become a member to post a comment.
Sign up Log in