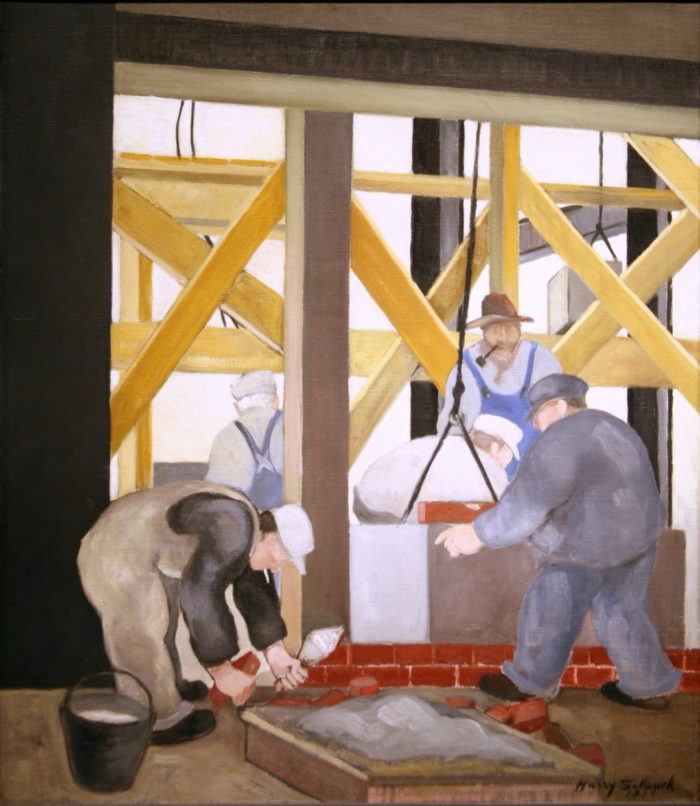
Image Credit: Workers on the Cathedral of Learning, 1934, oil on canvas by Harry W. Scheuch
Construction projects are becoming more complex, with increasing levels of regulations, more product choices, and higher performance expectations. And there are so many more ways of getting bombarded with information — e-mail, text, voice-mail — that we get swept up into survival mode of responding to the bits of info as it comes along.
But the danger of this multi-tasking is that it doesn’t really work: you lose sight of the big picture (only seeing one piece of the elephant), and there is really no one who has a handle on the whole situation.
On commercial projects, the solution to this problem has been early morning trailer huddles or at least message boards at the jobsite trailer. The trend is to increase the membership to these meetings — inviting in subs who previously just got their marching order as they went along.
The problem with these meetings is that the communication is mostly a one-way deal. The schedule and work packets have already been figured out, and are just being passed along. Yet the meeting can help in creating awareness of what other workers will be doing on the job site, and ideally does allow for some shifting work around a conflict area, mostly regarding safety.
Howell and Ballard
The problem with this traditional method of communication is that expectations don’t always match reality. Years ago, Greg Howell and Glenn Ballard measured the percentage of planned work that was actually completed, and discovered that it was often very disappointing. The work would just get rescheduled, and would have already created havoc through lost productive work time and increased stress from the unpredictability. They went on to develop a practice known as “The Last Planner,” in which activities are first “made ready” by completing all precedent work. This ensures that all resources and supplies are in place, and that any affiliated work is ready to be deployed at the same time.
Once the day or week is over, any work that doesn’t go as planned is analyzed for the underlying reason, in order to correct the condition on future work. The goal is to increase the predictability of the work.
The Lean Construction Institute
This is just a quick cameo of the type of communication and streamlining of work that Howell and Ballard developed. Along with their colleague Iris Tommelein, they founded the Lean Construction Institute and catalyzed a shift in efficiency, value delivery, and improved design and project management.
If you haven’t yet tapped into this very logical and powerful concept of lean thinking, then I would recommend seeking out a local community of practice.
Better communications systems for residential job sites
My current challenge is to adapt this same underlying concept to the smaller scale of residential construction. What happens when you don’t have a jobsite trailer? Or if your subs typically don’t ever meet each other until the job site? And, in fact, the scheduling is often set up so that there is no overlap, thus avoiding the conflicts that have often ensued when subs tangle on site.
Is there a way of tapping into this same communication technology that drives us into frenzy, and tame it into submission? Would it be possible to have one initial face-to-face meeting at the outset of the job, for everyone to meet, identify their precedent work needs, and jointly determine a schedule? Is there a way to convert this information to a jobsite board that is interactive, with the ability to assess real-time what is work-ready, or what needs to be rescheduled?
This is the challenge that I am about to undertake for a local affordable housing project. I would very much welcome any input. (My e-mail address is ecobuildtrends [at] gmail [dot] com.).
There is much to be gained – if we can figure this out.
Dr. Vera Novak was recently awarded a PhD in Construction by Virginia Tech. Her work is dedicated to increased depth and breadth of sustainability in construction, by leveraging the points of greatest potential impact. She is currently working on optimizing corporate sustainability practices to support regenerative design, as well as adapting a lean thinking process for smaller scale projects. She also writes the Eco Build Trends blog.
Weekly Newsletter
Get building science and energy efficiency advice, plus special offers, in your inbox.
7 Comments
Great piece
Wish I had something intelligent to say. Much food for thought here - thanks.
Jobsite Board
Thanks Dan - As an update, and maybe to help focus the food for thought - I am developing a jobsite communication board, with cards set up to represent job packets and arranged by date/ trade. The information from the cards is derived from a pre-con meeting, and lists the work and the dependencies both prior to and following this work packet. When the work is done, the contractor signs it and turns it over to the "green" side. This lets everyone else know it is done and that it is on schedule. That is the general idea, now lots of details to work out....
Back to a blackboard...
Interesting concept. The integrated design and initial project meeting processes are in place for projects I work on, but the daily meetings with Custom Builders and Subs is not. It’s all up to the builders. As with Commercial Builders, for most production and multifamily builders maybe easier to get those early morning meetings with subs, however, for custom builders, until technology/education is available for all to carry an IPad to the jobsite, maybe a blackboard on location would help communicate between GCs and subs, and supplement the subs checklist board for every project.
Some thoughts:
I would not necessarily conclude that a lack of communication alone is the problem. The individual sub-contractors all have their own self-interest, and communicating with other subs is not necessarily in the direct interest of any of them.
Thorough communication will solve a lot of problems, but one overriding problem is that the information needed to be communicated is highly variable and unpredictable. Each phase of work is subject to delay just by the work process not going as smoothly as anticipated. Not only does this affect the subcontractor doing the work, but it also affects the commitments made to other subcontractors who coordinate work with them to schedule following work phases. So, all subcontractors face the prospect of delay, not only by the progress of their own work phase at all jobs they are engaged in, but also by the progress of coordinating subcontractors at all jobs they are engaged in.
Perhaps this uncertainty could be largely overcome if the communication were nearly constant among all participants. That way, the commitments could be continuously revised to be almost perfectly current all the time. However, participating in this communication costs money in terms of subcontractor time. The communication itself takes time, but the management of the information flow going into the communication probably is the biggest time consumer. It is unreasonable to expect subcontractors to pay for this time when it not directly in their interest or part of their bid. So, I conclude that this intense communication is just another phase of the work, and it must be paid for just like all the other phases.
However there is another point to consider. Even with constant, perfect communication, the awareness of an impending delay of significant disruption and duration can instantly arise without any warning. In other words, while many delays might arise and be instantly compensated for by constant communication, there is still the possibility of delays that will require a prolonged response once they arise even if they are discovered by constant communication the instant they arise. They may be instantly discovered, but not instantly resolvable.
Predictability of Work Schedule
Ron - you bring up a good point. Construction is a network of commitments, all of which blends into a complex schedule. Any one change becomes the weakest link and triggers a wave of schedule disruption. One of the practices of Lean Construction, called The Last Planner, focuses on improving the reliability and predictability, which can help keep the project work flow on schedule. There is an emphasis on getting everything in place before the work packet is released for schedule. It can help adjust for smaller unexpected weather events, and subcontractor variance. That being said, we will be experimenting with this on smaller scale projects, to see just how well it can be adapted, and whether it can help smooth the workflow. And of course, with remodeling work, there is the added factor of surprise and unpredictable. Yet one more challenge.
Lean Residential
A very timely article...at least for me. I have spent the last two weeks researching this very subject....and how it can be used on the residential side where things are a bit more relaxed, meaning scheduling by the seat of your pants so to speak. At the AGC of America website they offer a free Lean Construction 101 course...but again it applies more to the Commercial side where it is being used on larger scale. The one thing that stood out for me was the concept of push vs pull. In our standard way of doing things, we are constantly pushing our projects forward to some end in the future....from one task to the next and so on. As with most things, when your are constantly pushing, things can quickly get away from you. In Lean Construction, the concept is to Pull the job to the point of completion...so in theory, as Vera pointed out above, if you start from the end of the job and work your way back to the beginning, everything can be preplanned and put in place before the project starts. Of course, easier said then done but it is an idea worth thinking about. How much fun would it be to get all your subs in a room to talk out the schedule before the jobs starts....
Vera - I hope we can hear about how this works for you in your current project....
Communication
One more thing - In my quest to streamline jobsite communication for all parties involved, I am trying out a cloudbased software package called Co-Construct. It is geared to small builders and remodelers. It seems fairly comprehensive. Any one else use this or have other methods of enhancing real time communication in the residential construction arena?
Log in or create an account to post a comment.
Sign up Log in