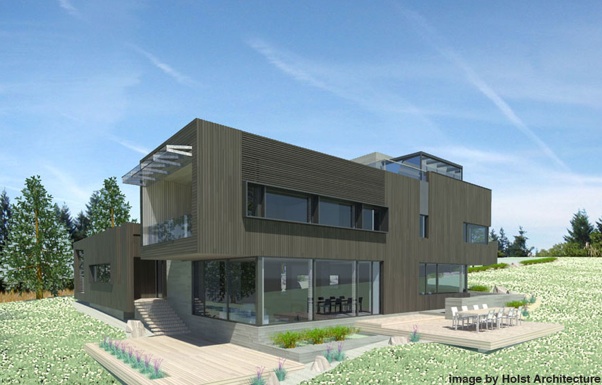
Image Credit: Holst Architecture (images 1 and 2); Aaron Bergeson, Shelley Martin, and Scott Gunter (images 3, 4, and 5)
Image Credit: Holst Architecture (images 1 and 2); Aaron Bergeson, Shelley Martin, and Scott Gunter (images 3, 4, and 5) Karuna House builder Hammer & Hand notes that the project client, a climate policy advocate, hopes the house will serve as a case study on ways that Passivhaus, LEED for Homes Platinum, and Minergie-P-ECO certification standards can mesh well or, perhaps, conflict. The Karuna House project incorporates three foundation strategies: slab on grade, platform framing (decking above a slab), and a full basement. Grade beams are leveled, graded, and compacted, then pieces of expanded polystyrene foam are aligned and anchored in place with 2-ft.-long ¼-in. pins driven through pilot holes in the corners of each foam slab and then hammered into the sub-grade. Screeding out the gravel bed. The bed is then compacted before expanded polystyrene foam is set in place and aligned with string lines marking the end of the foundation wall.
Are the developers of a project called Karuna House — Oregon-based builder Hammer & Hand, Holst Architecture, and their collaborators — inviting skirmishes between certification programs? Maybe a little bit.
According to information on the Hammer & Hand website, “The Karuna House’s client, a leading proponent of smart climate policy and sound land use, is pursuing the project as a case study to shed light on the ways that the leading green building certifications and standards complement one another, and the ways that they may conflict.”
Under construction on a perch in Yamhill County that overlooks the Willamette Valley, northwestern Oregon’s wine-growing region, Karuna House is designed to qualify for Passivhaus, LEED for Homes Platinum, and Minergie-P-ECO certifications. That’s a pretty full green menu. As Hammer & Hand principal Sam Hagerman, who also serves as president of the national Passive House Alliance, observes, the design/build team is left with “a fairly narrow path to navigate through.”
A siting workaround
By the first week in November, the site had been prepped with straw wattles to divert water and limit sediment runoff, and the team had foundation work well underway, with foundation beds leveled and compacted, and expanded polystyrene structural-foam slabs aligned and anchored in place. (The project’s structural fill was built up using native fill excavated from various locations on the site, eliminating the need to import fill from elsewhere.)
Even though construction is still in the early stages, the Karuna team has already had to develop a few workarounds to keep the project in compliance with the three sets of certification requirements. An October 27 Hammer & Hand blog post notes, for example, that even though LEED for Homes favors constructing homes in existing neighborhoods rather than on greenfield sites, LEED credits for Karuna’s exceptional energy efficiency are expected to offset those lost because of the project’s location.
An alternative to site-applied spray foam
In addition, Mingergie-ECO prohibits site-applied spray foam, a material that had been specified in the original design plans. The project team decided to switch to high-density cellulose insulation and, to fill gaps, acrylic-impregnated expanding foam tape. Mingergie-ECO also prohibits treated lumber inside the building’s air barrier – which had been specified, in compliance with code, for the sill plate. The chosen alternative: a borate-treated sill plate installed over a structural EPDM gasket.
And, finally, code requires hood exhaust units in kitchens – a nonstarter for Passivhaus and Minergie-P certifications, whose requirements also nixed the notion of using conventional dryer vents in the house. Holst and Hammer & Hand addressed the hood exhaust requirement by locating the heat recovery ventilator near the kitchen and installing a recirculating fan with a grease filter between the kitchen intake and the HRV. For the dryer, the solution is to install a closed-cycle heat pump dryer.
So, there are no real conflicts yet among the three certification systems, but the team acknowledges there’s still plenty of time and opportunity for that, as well as more workaround challenges.
The three-bedroom home will have 3,261 square feet of interior space and is expected to cost about $2 million. It will incorporate three foundation strategies: slab on grade, platform framing (decking above a slab), and a full basement. Expanded polystyrene under each foundation element will bring the foundation R-value to 56. The R-48 exterior walls will have 2×6 studs filled with cellulose and 6 in. of exterior polyisocyanurate foam. Similarly, the roof’s 16-inch-deep I-joist rafters will be filled with cellulose, and 8 inches of EPS will cover the roof sheathing, bringing the R-value of the roof assembly to 92.
Weekly Newsletter
Get building science and energy efficiency advice, plus special offers, in your inbox.
One Comment
Congrats on the project
Nice to see you guys were able to get around some of the code and certification issues and get this bad boy rolling. I can't wait to see the progress, and your solutions to these issues as they come up.
Log in or create an account to post a comment.
Sign up Log in