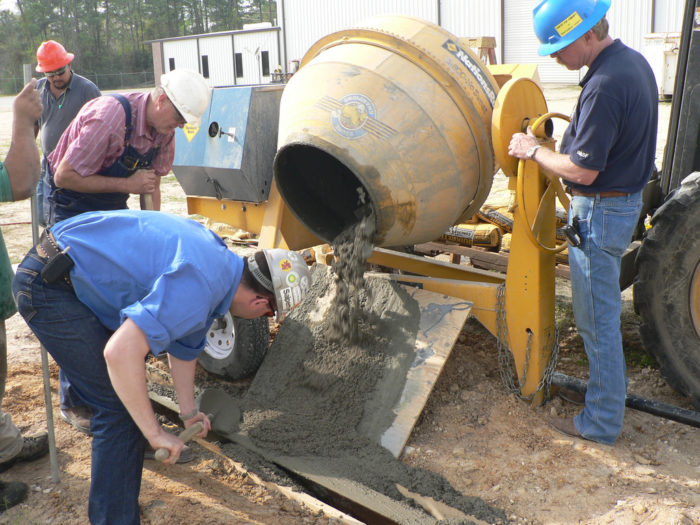
Image Credit: Rick Kimpel / CC BY-SA 2.0 / Flickr
A roomful of materials scientists, gathered at UCLA for a recent conference on “grand challenges in construction materials,” slowly passed a brick-size white block around the room. They held in their hands, briefly, part of the solution to one of those grand challenges. The white block, rock solid and surprisingly lightweight, was a new alternative to cement, the glue that holds together aggregate, or crushed rock, to make the world’s most ubiquitous building material: concrete.
Production of cement — and by extension, concrete — has a large environmental footprint, mostly due to the huge amount of energy it takes to heat limestone, cement’s key ingredient, and the subsequent chemical process it undergoes. The process of creating cement emits upwards of 80% of the cement’s weight in carbon dioxide and accounts for about 5% of human-generated CO2 emissions.
Though producing the white block still requires some CO2-emitting fuel, CO2 also is one of the ingredients used to create it. The cement-like substance, which is as yet unnamed, is about one-third CO2 by mass; it reduces its carbon footprint by sequestering CO2 inside the finished product.
Concrete, and the cement that binds it, is the most widely used material in the world, and its usage is on the rise. From 2011 through 2013, China used more than 6.5 billion metric tons (7.2 billion tons) of cement — more than the U.S. used in the entire 20th century. Between 2006 and 2050, global production of cement is expected to increase to between 3.7 billion metric tons (4.1 billion tons) and about 4.4 billion metric tons (4.9 billion tons) a year. Since concrete’s not going away, reducing the carbon intensity of its production is becoming a global imperative.
New technologies and approaches are being developed to cut down on concrete’s environmental downsides — everything from utilizing industrial by-products to reduce cement usage, to recycling existing concrete, to producing self-healing concretes that reduce the need for new concrete, to creating entirely new materials.
No perfect solution exists
That white block is not completely carbon-negative nor can it replace typical cement completely, explains Fredrik P. Glasser, a professor at the University of Aberdeen in Scotland who is part of the team that developed the cement alternative. In this case, limestone is replaced with waste CO2 and magnesium from a cement production facility and a desalination plant in Qatar, but carbon-emitting high heats are still required.
Glasser says it’s less about replacing cement than reusing the large quantities of CO2 it produces. “The emphasis has to be on taking that CO2 and making useful products from it,” he says.
The material he’s helping develop is still a few years away from market, but it’s proving in tests to be a viable replacement for some concrete and insulation in building projects. His goal isn’t to compete with cement, but to “eat away at the edges” of what it’s currently being used for, shaving down the global need for cement and the carbon emissions it produces.
Researchers and businesses all over the world are trying to find other ways to carve niches into this market — by developing novel material approaches or simply making concrete less environmentally harmful.
Simple technology from a Canadian company
The Canadian company CarbonCure Technologies has developed a process that injects waste CO2 into a typical concrete production process, effectively replacing a small amount of cement with CO2 without compromising the concrete’s strength or integrity. Once in the mix, the CO2 changes into calcium carbonate, the chemical equivalent of the limestone used in the production of conventional cement.
Four concrete producers in North America have started using CarbonCure’s technology, including Argos in Atlanta and Vulcan in Springfield, Virginia, and about a dozen more are negotiating licenses, according to Sean Monkman, the company’s vice president of technology development. One user, over the course of a single week after the technology was installed, saw its CO2 emissions drop from 124.5 metric tons (137 tons) to 119 metric tons (131 tons) by replacing some of the carbon-intensive cement in the concrete mix with waste CO2, Monkman says.
CarbonCure’s technology is a small retrofit to the concrete production process — just a computer system, a tank of waste CO2 and a tube that can pump that CO2 into the concrete mix. “It’s simple. It doesn’t require any huge change in the way things are normally operated,” Monkman says. “For a conservative industry like concrete, it’s got to be simple if people are going to want to do it.”
Change is slow, many in the industry concede, which has made it challenging for new material approaches to catch on. And though typical cement has a high carbon footprint, there’s still no cheaper option.
Recycling concrete by turning it into aggregate
Yet another way to reduce the carbon footprint of concrete is to recycle it. Researchers at the University of Notre Dame are developing a cost-effective method by which producers of precast concrete — concrete formed into a mold and brought to building sites — can effectively recycle their waste concrete into aggregate and reuse it in the production of construction beams.
Engineering professor Yahya Kurama, who’s leading this research, says the environmental toll of mining the aggregate used to make concrete — often from riverbeds and mountaintops — has been largely ignored. “You’re not only destroying the environment but you’re spending the energy to dig that material out, and then you have to transport it,” he says. By reducing the amount of virgin aggregate they mine, concrete companies can cut both environmental impacts and costs.
Another approach to reducing the need for new concrete is the advent of self-healing concrete — concrete mixes augmented with various polymers, bacteria, and healing agents that can automatically respond to cracks. Researchers in the United Kingdom are currently testing a number of experimental self-healing concretes, including one embedded with tiny capsules that open when the concrete cracks and form new solid calcium carbonate.
None of these approaches on its own will erase the environmental impact of concrete. But the more alternatives there are, the more sustainable the industry can be.
_______________________________________________________________________
Nate Berg writes about cities, science and design. This post originally appeared at Ensia, a non-profit magazine covering environmental and sustainability issues.
Weekly Newsletter
Get building science and energy efficiency advice, plus special offers, in your inbox.
7 Comments
First step here? Clarify definitions. Top concern? The term cement as used in this article isn't *cement* - it's a very particular type of cement: Portland cement. Production of natural cement is nowhere near as ecologically destructive as production of Portland cement.
What is Natural Cement?
http://www.freedomcement.com/ http://www.rosendalecement.net/
What is Natural Cement?
Natural cement is hydraulic cement made from limestone that has a high clay content (argillaceous limestone). It is different from building lime, which is made from limestone with a lower clay content, in that lime is not hydraulic (does not set under water).
Lime and Natural Cement are both produced by heating limestone to approximately 900 to 1100C, at which point carbon dioxide bound within the stone is released. In the production of lime, the burnt material is quicklime, which is then mixed with water to make building lime, also referred to as hydrated lime, or as lime putty if excess water is used. The process of hydrating quicklime is slaking, and when quicklime is slaked, it crumbles to a fine particle size. The burnt natural cement rock does not slake when mixed with water, however. Instead, it must be crushed into a powder before use. The resulting powder is natural cement, which will set when mixed with water, and hardens through a process of cement hydration.
When lime is used in masonry mortar and renders, it does not set due to being mixed with water, but rather, must react with carbon dioxide in the air in order to cure and harden. This is a slow process, often requiring weeks or months to build significant initial strength.
Portland cement is made from artificial mixtures of limestone, shale, gypsum and other additives. The mixture is heated to approximately 1400C, at which point components fuse to form a clinker. The clinker is then ground to a fine powder that sets when mixed with water.
"Natural Cement" is also weak (1100 psi @ 28 days even with a super rich 1:2 mix) and sets fast (but cures slow). Compare to portland cement: 3000 psi@1:5 mix. Net difference - you need more than 5x as much natural cement. On an equal strength basis, it's unlikely that it is more energy efficient. But feel free to post psi and mix adjusted btu data instead of unsupported claims.
Natural cement dries ultimately to 3000psi, reaching about 2200psi after a month, and sets quickly; Rosendale Cement, e.g., also offers a "quick-setting natural cement" that hits over 2000psi in 7 days: http://www.edisoncoatings.com/ROSENDALE_10C-14.pdf On an equal strength basis, it's so far ahead of Portland regarding embodied energy, energy effectiveness, mold management, and straightforward attractiveness that it simply makes too much sense on its face for anyone to use it. Of course, if you're constantly in a rush then Portland and petroleum are your "friends" if not anybody else's.
Greg,
That's interesting - as are a lot of your posts - but it gets distracting and detracts form your points when you link them to discussions of Fiat Money and Corporate Greed conspiracy theories, which have at best a tenuous connection to what is being discussed.
Context is everything in my book, Malcol. There's a reason folks turned away from non-toxic materials, and IMHO it truly has nothing to do with the science and everything to do with the massive market distortions with which we all must deal at the moment. When there's an 800lb gorilla in the room, I feel compelled to acknowledge it as much as possible. For instance, when I hear someone complaining about "climate change" and failing to reference the actual drivers of the situation Iet alone addressing said drivers I need to change the subject: Banning plastic straws and plastic bags, e.g., on the Titanic won't help it from sinking; however, discussing with others on the ship changing the course of the Titanic and then doing it? More compelling to me. Thanks for the feedback, to be sure!
Log in or create an account to post a comment.
Sign up Log in