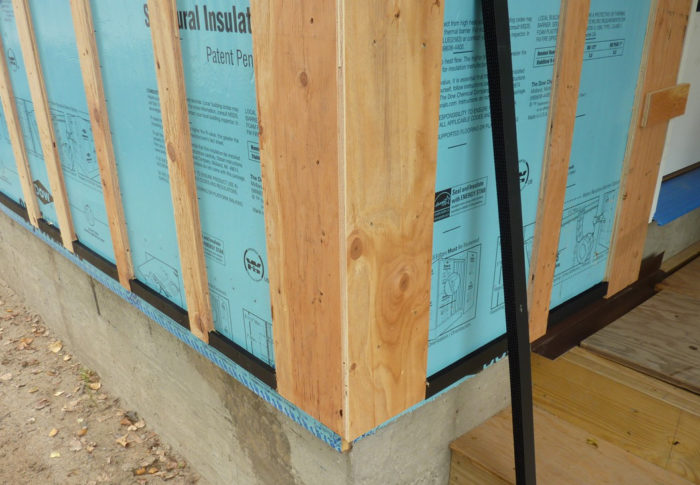
A vented rainscreen is an increasingly common exterior detail on exterior walls. Instead of attaching siding directly to the sheathing, builders add an air space behind the siding, which helps carry away moisture and prolongs the life of the siding.
Builders typically use vertical furring strips to create the gap, but there also are commercial products like Home Slicker, a plastic mesh, that are designed to do the same thing.
A rainscreen certainly is an extra step in construction, but many builders think it’s well worth the effort. So, Eric Mikkelsen asks, are vented rainscreens equally valuable on a roof?
“I’ve seen lots of info about rainscreen walls,” he writes in a Q&A post. “What about roofs? I’m planning on using a standing seam metal roof, 10/12 pitch. Should I be considering rainscreen details for this?”
Although Mikkelsen’s original post dates from 2012, the question is still sparking interest among GBA readers.
Is the attic ventilated?
James Morgan’s first question is whether the attic is ventilated, which would leave the underside of the roof sheathing open for inspection. If the attic is ventilated, Morgan says a rainscreen detail on the roof is unnecessary.
The roof, Mikkelsen says, is insulated with spray polyurethane foam applied on the underside of the sheathing, meaning the roof is not ventilated.
GBA editor Martin Holladay notes that a common approach for builders worried about ice dams — admittedly a concern that rarely plagues homes with metal roofing — is to apply 2x4s on the flat on top of the roof sheathing, with one 2×4 over each rafter or truss. Then a second layer of roof sheathing goes on, followed by roofing underlayment and the roofing. The 2x4s will create a 1 1/2-inch air gap between the two layers of sheathing.…
Weekly Newsletter
Get building science and energy efficiency advice, plus special offers, in your inbox.
This article is only available to GBA Prime Members
Sign up for a free trial and get instant access to this article as well as GBA’s complete library of premium articles and construction details.
Start Free TrialAlready a member? Log in
16 Comments
My concern with battens or crosshatched batten to batten is getting a good connection for the metal roof. In high wind areas attention to detail is important. I have seen winds take the shingles off in a valley where not enough fasteners were used, all roofs need to withstand strong winds.
I think there are two factors driving the depth of ventilation gaps on both roofs and walls.
One is the minimum size necessary to allow air to move without excessive friction, and provide sufficient volume to dilute moisture.
The second is the likelihood of the cavity becoming blocked by either the WRB or insulation. In walls this mainly occurs with building paper, which can bridge the cavity, impeding air-flow and short-circuiting the capillary-break. And unlike those diligent souls who follow GBAs advice to provide vent-channels, most builders of cathedral ceilings still leave the batt insulation open at the top, where it can impede the vent-channel. Our code acknowledges this possibility and requires a 3" gap.
One important factor not discussed is how to finish off the eaves and ridges of the roof. After all, these are the places where the air enters and exits the rain screen assembly. Another detail not mentioned is how to connect a roof rain screen from a lower roof to an upper floor sidewall.
One company, Coravent, makes a series of products for roof and wall rain screens.
http://www.cor-a-vent.com/
They also make a specific product for the roof to wall connection.
http://www.roof-2-wall.com/
One of the chief advantages to their products is that they are perforated across the entire section to allow airflow and water drainage (unlike a wooden batten).
A third area not discussed is fire safety. Eave and ridge vents should be designed so that wildfire embers can't blow in under the secondary roof decking. Brandguard makes some very good products for that purpose.
https://www.brandguardvents.com/products.php
Also, just because you have a metal roof installed doesn't mean that your roof is fire resistant. The heat from a wildfire can transmit through your metal roof and set your sheathing on fire. A product like GAF Versashield will help prevent that.
https://www.gaf.com/en-us/roofing-products/residential-roofing-products/roof-deck-protection/fire-resistant/versashield
Finally, makes sure that all your fascia, trim pieces and the underside of your eaves are covered in fire resistant or fire proof materials, such as Hardiepanel cement board or metal. Fire can race up the side of your house and get trapped under the eave, then through the eave vents and into the roof assembly.
"The heat from a wildfire can transmit through your metal roof and set your sheathing on fire. "
Wouldn't there need to be an air space between the sheathing and metal roof for that to happen?
HI,
What is recommended for between a NB polyiso insulated panel on the rood and asphalt shingles? I plan to use GAF asphalt shingles and Deckarmour. (I have Henry Blueskin between the panel and the roof deck). In a perfect world with endless supplies of $$, I would add a rainscreen atop the deck armor but the world isn't perfect. Will I be ok? Should I consider taping the seams of the insulated NB panels? Zone 5. closed cell spray foam under deck. Not perfect... but pretty good. Thought on the area between NB deck and asphalt shingles please. thanks
Andy
Andy,
By "NB polyiso panel," I assume you are talking about a brand of nailbase made by Hunter -- in other words, polyiso bonded to OSB.
Between the Hunter nailbase panel and the asphalt shingles, you need roofing underlayment. GAF DeckArmor is one brand of roofing underlayment, and it should work fine.
Hi Martin,
Yep - Hunter H Shield NB is the panel. I specified plywood. Do you think I should tape the seams of the NB panels or am I going overboard? Also been reading studies that have added CDR VentTM by Keene Building Products over the DeckArmor and under the asphalt shingle. Overkill?
Thanks
Andy
Andy,
Q. "Do you think I should tape the seams of the NB panels or am I going overboard?"
A. Attention to airtightness is always a good idea. Sure, tape the seams of your nailbase.
Hi Martin,
My roofer is advising a waterproof membrane on my Hunter NB panels as opposed to a water resistant membrane like DeckArmor. I think since the asphalt shingles prohibit any outward drying that waterproof membrane could be fine. Thoughts?
Thanks
A
Andy,
I'm not sure what type of membrane your roofer is recommending, but all roofing underlayments need to be waterproof. (Some roofing underlayments are vapor-permeable, and some are vapor-impermeable -- but all of them are waterproof.)
You aren't getting any outward drying through your asphalt shingles, so the vapor permeance of your roofing underlayment is irrelevant. Either vapor-permeable or vapor-impermeable roofing underlayment will work.
Figure 20 below shows that permeable underlayment under asphalt shingles does dry better. The text also suggests that fully adhered might still have an advantage in some cases.
http://rdh.com/wp-content/uploads/2015/03/The-Problem-with-Ventilated-Attics-RCI-March-2015-Nov-5-2014-For-Printing.pdf
Thanks Jon. I would use peel & stick water proof membrane over the whole roof in a heartbeat if I could be sure that I was not sealing existing moisture into the plywood. On the other hand, using vapor open membrane may cause a pathway for later moisture into the plywood. Thus, my dilemma.
Andy,
Whatever type of roofing underlayment you choose, it's essential that the nailbase be dry on the day you install the underlayment and shingles. Wait for a sunny day -- and start work at 10:00 a.m. or later, after the dew has evaporated.
Jon,
Interesting study. But the test roof configurations were entirely open at the bottom, to simulate roof sheathing over an attic. Andy is talking about nailbase, which can't dry inward. I'm not sure that the research results you shared apply to Andy's case.
I've been trying to figure out how to do this for my mother's house, it's a huge converted barn that has a tin roof that's about 50 years past it's freshness date! I want to lay down foil faced polyiso w/ taped seams, then diagonal wood batons (or plastic spacer pucks) and then the cheapest metal roof I can find. no builder ants to do that though! It's down to a DIY project at this point.
Sasquatch,
Here are links to two relevant articles:
"How to Install Rigid Foam On Top of Roof Sheathing"
"I Can’t Find a Contractor to Do That"
Log in or become a member to post a comment.
Sign up Log in