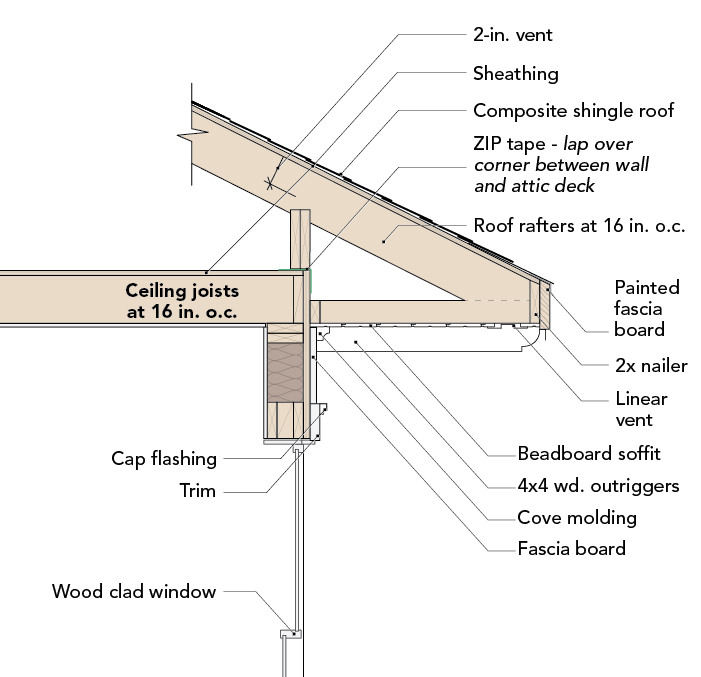
As a consultant and former contractor, I don’t have much influence on building designs and construction details. As I discussed in a previous post, Smart High-Performance Homes Start with Good Design, I am usually asked to make projects “green” after the design is mostly complete. I have plenty of ideas on how to create high-performance buildings, but do not see my clients implement them as often as I would like. In Georgia’s mixed-humid climate (Zone 3), this kind of construction is not that challenging but it is rare that I see a house or multifamily building conceived to be high performance from the start.
To create a truly high-performance house, my go-to concept is to simplify the volume. This supports a well-sealed building enclosure that keeps the interior dry and comfortable. Avoiding cantilevers, ceiling vaults and trays, dormers, and similar details makes construction easier to detail and allows a project team to get to high performance levels without breaking the bank.
About the foundation
My house is a good example of a simple volume. It’s on a slab with 1-in. XPS (R-5) under the first 2 ft. of perimeter. This is not code-mandated in my region, primarily due to the risk of termite damage but I addressed that issue by installing a vapor- and termite-barrier membrane over the entire slab.
For aesthetic reasons and to meet the local historic commission ban on slab-on-grade foundations, I installed a raised slab inside stem walls, creating a crawlspace-like look for the house. By not building an actual crawlspace, I eliminated the need for additional conditioning and dehumidification, as well as the potential for moisture intrusion from below.
Advanced framing for the walls
The walls are 2×6 at 24 in. on center, providing space for more insulation (R-22 blown fiberglass) as well as…
Weekly Newsletter
Get building science and energy efficiency advice, plus special offers, in your inbox.
This article is only available to GBA Prime Members
Sign up for a free trial and get instant access to this article as well as GBA’s complete library of premium articles and construction details.
Start Free TrialAlready a member? Log in
12 Comments
The roof detail at the very top of the article looks a little suspicious to me.
The ceiling joist aren't connected to the rafters, in a traditional sense, and those 2x boards beneath the birds mouth look like they form a double hinge joint. Is there a point or two I might be missing?
Bump.
I suppose a similar question might be asked about the poney wall on decked tjoists detail for the intriguing ceiling cavity recently shown on these pages.
I'm also very curious. I really like this method of air sealing & having a flat deck to frame off of. If it can actually be framed like this?
The sealed deck strikes me as a highly effective, buildable and very expensive approach. Would love to get a reaction to the the root comment.
another bump for this question
The rafters are tied to the header sitting on top of the decking which is tied to the structure below with metal ties and some wood blocks. It might not survive a tornado, but otherwise seems to work fine.
Is there a ridge beam? If there is a ridge beam it makes sense to me. Without a ridge beam, it seems like the outward thrust of the rafters isn't being resisted very well (normally you'd see the ceiling joists or rafter ties doing that job).
It is a hip roof and an almost square house, so there is a very small ridge on the main roof and a larger one on the back roof.
2nd that, I though the roof rafters and joist have to be connected to form the triangle that makes the roof a sturdy structure
To continue the efficiency of Advanced Framing, why not continue the 24" spacing for the rafters and ceiling joists?
User ...934,
Advanced framing usually does use 24" spacing for rafters or trusses. You can even continue that for the floor system, but it requires a very thick sub-floor or you get excessive deflection. Spacing studs and roof framing at 24" oc isn't unique to Advanced Framing. You will find it in many tract houses going back decades.
Some of the practices of Advanced Framing make more sense to me than others. Things like determining the sizing and placement of windows to conform to the location of studs isn't justified by the small savings in lumber.
Anybody in seismic zone D interested in using that top detail should really run it past a structural engineer. I see issues with it, especially relating to transferring shear in the roof sheathing to the shear walls below.
Log in or become a member to post a comment.
Sign up Log in