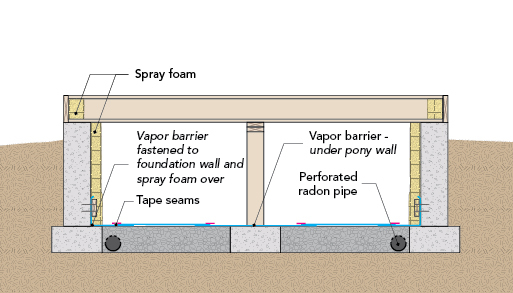
Crawlspace detailing is important in every home. When you’re building in Teton Valley Idaho, like I do, it is even more critical to get the details right. Our valley floor is at the foot on the Teton, Big Hole, and Palisades Mountain Ranges. The homes on the valley floor are in Climate Zone 6, while the hillside homes in the mountains are in Climate Zone 7. Besides harsh elements, and temperatures that drop below -30°F, we also have some of the highest radon levels in Idaho; and Idaho has some of the highest levels in the U.S. The average national indoor radon level is 1.3pCi/L. The average in Teton County is 10.5 pCi/L, which is over double the EPA’s recommended limit of 4.0 pCi/L.
Radon gas is produced as granite rock decomposes below the surface. A properly detailed passive radon mitigation system will create a barrier that will not allow these gases into the house and provides a path for gas to escape in a vent pipe exiting the roof of the house.
We begin this process before pouring footings. At interior footing locations, we must hand-dig for a 6-in. sleeve to be placed under the footing, near the exterior foundation wall. This will allow our 6-in. perforated radon gas collection pipe to be run around the entire perimeter of the crawlspace, after the foundation walls are poured. Then we cover the pipe with clean gravel or pea stone.
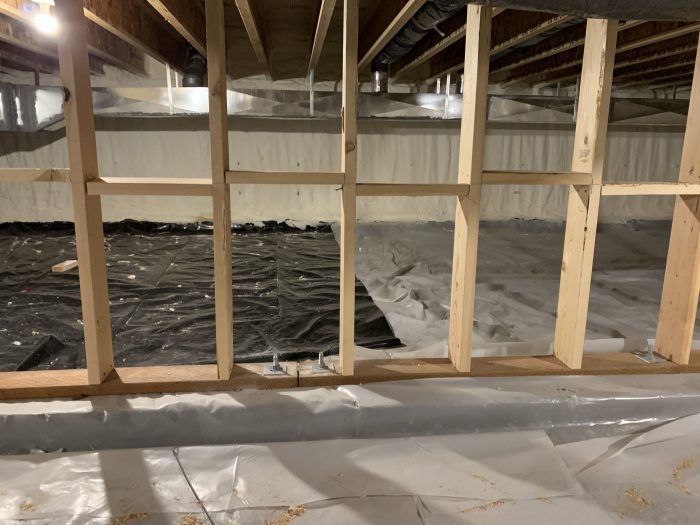
The next step is to install a vapor barrier to completely seal the crawlspace from the layer below, which is where the radon gases will accumulate. We run 2-ft. strips of 10-mil. polyethylene over the interior footings before framing the pony walls on top. This way, the vapor barrier…
Weekly Newsletter
Get building science and energy efficiency advice, plus special offers, in your inbox.
This article is only available to GBA Prime Members
Sign up for a free trial and get instant access to this article as well as GBA’s complete library of premium articles and construction details.
Start Free TrialAlready a member? Log in
4 Comments
An anecdote about radon and encapsulated crawlspaces:
My home had a 0.6 pCi/L when we bought it, with a vented crawlspace.
We converted the crawlspace to an unvented crawlspace (conditioned with a dehumidifier), and installed a perimeter drain in case it was needed, but did not install the vertical radon pipe at that time. It didn't occur to me to retest the radon at the time.
My coworker mentioned that he had had a radon tester tell him that sometimes sealing a crawlspace increased the radon levels in the house.
I retested and measured above 4.0 pCi/L!
I had a radon mitigation company connect an active exhaust system to the perimeter drain pipe and that brought the levels down to near zero.
The fact that radon levels can vary dramatically over time means it's hard to draw any causal conclusions from my anecdote, but I thought it was interesting. And the moral of the story is that testing your radon levels is important and radon mitigation works really well!
A question:
If the performed radon pipe is at the same height as the perimeter drains (and below them where it is dropped at interior strip footings), what keeps this pipe from filling with water? Shouldn't more interior fill be used, which would also bury the vulnerable joint between the footings and stem wall?
The illustration is a bit confusing as it omits sill-plates, and how the insulation at the wall and rim joists are made continuous.
Malcolm, in the high desert where the author and I are, there is rarely any water in a crawl space or basement. Unless of course you build too low in the flood plane.
Seeking best practices for radon sealing where my slab intersects with the foundation? I have a radiant heated slab with XPS foam board separating the slab from the stem wall. The XPS/polysheeting creates perimeter seams around the entire slab. I have applied SIGA Fentrim tape across that seam but uncertain if that will seal out radon? Underneath the slab is your classic 4" perf pipe sitting in drain rock and plumbed for a possible radon exhaust fan. Perhaps just depressurizing the slab with the Fentrim seal is sufficient? Would Sika polyurethane sealant be another option? It's important to get this right as that perimeter seam gets buried with the bottom plate.
Log in or become a member to post a comment.
Sign up Log in