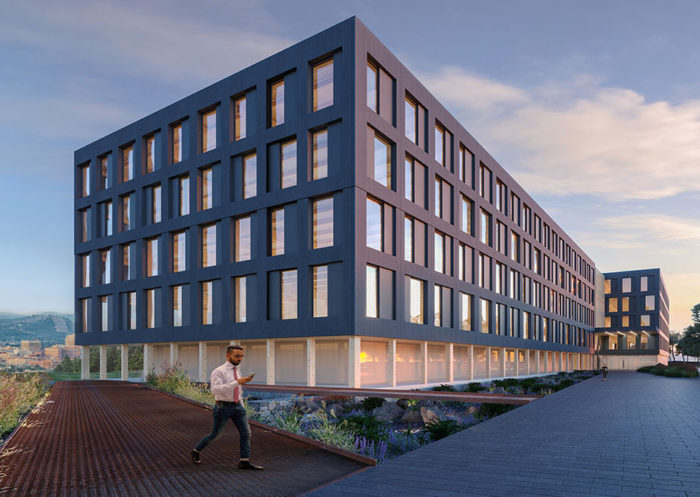
Image Credit: Katerra
A three-year-old technology company named Katerra is looking to upend the construction industry. Katerra has acquired Michael Green Architecture, a well-known firm specializing in mass timber designs, and is now building a 250,000-square-foot factory in Spokane that will produce cross-laminated timber building components.
Based in Menlo Park, California, Katerra believes the last several decades of electronics manufacturing can be a template for the slow-to-change world of construction. By controlling every step in the design and construction process — and leaning heavily on prefabricated building components — Katerra sees a bright future for construction that is “better, faster, cheaper.”
Katerra has grown rapidly, picking up $865 million in its latest round of financing, according to Building Design + Construction, and winning $1.3 billion in contracts last year. Its approach includes an aggressive schedule for building new factories, including the Spokane facility that’s expected to be fully up to speed by early next year.
Vancouver-based Michael Green Architecture has been responsible for a number of mass-timber designs, including the T3 Tower in Minneapolis, that showcase the use of timber components over more conventional steel-and-concrete. Green and others argue that cross-laminated and nail-laminated timber buildings have a better environmental record and can be built faster and more economically than buildings with steel or concrete frames.
According to an article in Architectural Record, Green was at first part of a “design consortium” assembled by Katerra design director Craig Curtis. Then Katerra brought Green and his 25-member firm directly into the Katerra fold.
“It couldn’t be a better scenario,” Green said of the merger. “We get all of Katerra’s cool innovation capacity and R&D.” Katerra sees the deal as a way of advancing systems that will modernize the construction industry.
The construction of Katerra’s Spokane factory will certainly give mass-timber building a shot in the arm. Already planned elsewhere in the city is the Catalyst Building, a 150,000-square-foot office building designed by Green and made with cross-laminated timber components. It will house several programs of Eastern Washington University.
Not your average modular builder
Mass timber construction is only part of Katerra’s game plan. It currently has a single factory, in Phoenix, Arizona, where it produces a variety of building components — everything from roof trusses and kitchen counters to cabinets and prefabricated wall components. By next spring, Katerra expects to have another half-dozen manufacturing plants up and running, according to Building Design + Construction.
It’s far from the first company to promote prefabricated building components that are made in highly automated factories and shipped flat to construction sites. But it may be the most successful to date, and the company created a real buzz among attendees at this year’s International Builders’ Show, said Susanna Ross, an industry analyst with the marketing research firm Principia.
Why is Katerra such a big deal?
“Because they were able to figure out at scale and get out there and promote in a very socially savvy way that offsite construction is cool, and it’s the way to go,” Ross said in a telephone call. “They came out of the gates boldly because they had so much money behind them, so much of a disrupter model, and an attitude and confidence behind them.”
Prefabrication is still a minor player in the U.S., representing only about 3 to 3 1/2% of the overall market, Ross said. The Modular Building Institute (MBI) hopes to get that to 7% by next year, but even then the U.S. industry would be far behind Canada, where 12% of all new buildings are made that way, and Europe and Australia, where half or more of new buildings are prefabs.
“It’s pretty much standard practice in Europe and Australia and New Zealand and very popular up in Canada,” Ross said, “and what we’ve seen over the last three or four years the United States is beginning to adopt prefabrication, off-site construction, as a potential. It’s been negatively colored by the fact that most people think of prefab and off-site construction as modular man camps or mobile home sites, and that’s now what we’re talking about.”
Weekly Newsletter
Get building science and energy efficiency advice, plus special offers, in your inbox.
One Comment
Interesting...
This is in my backyard. I went to EWU years ago. My current institution I work for may actually have some space inside the Catalyst building, so I may get a chance to walk through it.
Log in or create an account to post a comment.
Sign up Log in