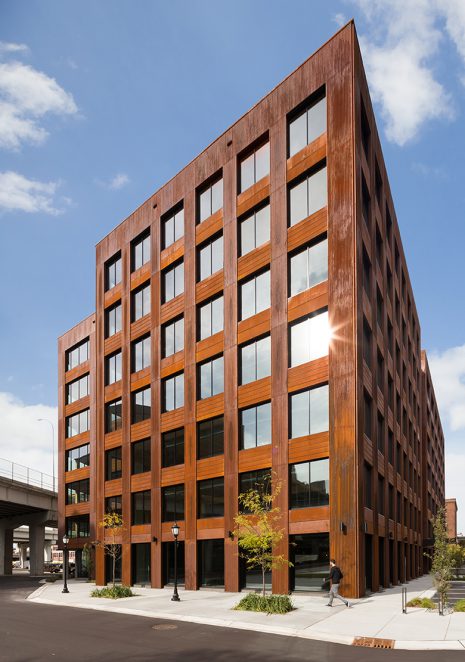
Image Credit: Ema Peter, except where otherwise noted
Image Credit: Ema Peter, except where otherwise noted T3 is clad with corrugated steel.
Image Credit: Ema Peter On the inside, structural wood panels, beams, and posts all have been left exposed to view. The finish floor is concrete placed over the nail-laminated timber floor panel. Panels up to 40 feet long and weighing as much as 8,000 lb. were fabricated off site and trucked to the construction site. (Photo: StructureCraft Builders) StructureCraft made the nail-laminated panels at a temporary shop in Winnipeg and trucked them to Minneapolis for assembly. They consist of 2x8s capped with a layer of OSB. Once placed, the panels got acoustic insulation and a 3-inch topping layer of concrete. (Photo: StructureCraft Builders) Each panel was labeled so crews knew exactly where it should be located. The glulam columns are two stories tall, with NLT panels notched to fit around them. (Photo: StructureCraft Builders)
A seven-story office building constructed largely of heavy timber components has opened in Minneapolis. It’s the first major timber building in the U.S. in more than a century, according to the architect who designed it, and currently the largest in North American.
The building, called T3, was constructed of glulam beams and columns and nail-laminated timber (NLT) panels. Although T3 uses some steel and concrete — the foundation, first floor, and central elevator core are concrete — most of the structure is wood. T3 is one of a number of large timber structures completed or designed in recent years as more designers warm up to the idea of using wood rather than concrete and steel for big commercial projects.
The developer is Hines, an international real estate company headquartered in Houston. T3, which stands for timber, transit, and technology, has 224,000 square feet of floor space, with 12,000 square feet of ground floor retail space and another 10,000 square feet of “tenant amenity” space that includes a fitness center and 100 parking stalls for bicycles.
Michael Green Architecture , which designed the building in conjunction with the DLR Group, said the building was intended to complement historic buildings in the North Loop warehouse district where it was constructed.
It uses some 3,600 cubic meters of wood — its 1,100 NLT panels range in size from 10 feet to 40 feet long and incorporate 1.4 million linear feet of 2×8 softwood. Most of the wood used in construction, according to the architect, came from trees killed by the mountain pine beetle.
NLT panels were a less expensive choice
The wood panels were fabricated and assembled by StructureCraft, which said that NLT construction had a couple of advantages over two possible alternatives, cross-laminated timber (CLT) and glue-laminated timber (GLT). Factors included high strength, lower cost, and shorter procurement times.
StructureCraft is based in Delta, British Columbia, but the panels were made in a temporary shop it set up in Winnipeg and then trucked several hours south to Minneapolis. The glulam columns and beams were shipped to Winnipeg by a European supplier, already milled and ready for steel connectors, according to a project description at the company’s website.
The building went up quickly. StructureCraft said its crews put up the glulam frame and 180,000 square feet of NLT panels in 9 1/2 weeks. The building is clad with corrugated steel.
Wood components have some attractive advantages over more conventional materials. One is weight. StructureCraft says that T3 is 30% lighter than its equivalent in steel would have been, and 60% lighter than post-tensioned concrete. That translates into a smaller foundation and lower seismic loads. Unlike steel, wood components did not need any extra fireproofing because of the protective layer of charring that occurs.
The wood in the building will sequester some 3,200 tons of carbon, StructureCraft says. Conversely, cement, the glue that holds concrete together, is a significant contributor to global greenhouse gas emissions (about 4% of total CO2 emissions, according to one estimate).
The use of wood also reduced costs in another way, according to an article posted at Architecture Magazine. Most conventional commercial buildings use gypsum wallboard and acoustic tile in the ceilings to camouflage a steel and concrete structure many people don’t find very attractive. But inside T3, the entire timber structure is on display, eliminating the cost of interior finishes.
“The final product has been very successful,” Michael Green Architecture associate Candice Nichol told Architecture. “The texture of exposed NLT is quite beautiful. The small imperfections in the lumber and slight variation in color of the mountain pine beetle wood only add to the warmth and character of the new space.”
NLT technology isn’t new
Justin Brown, a structural engineer at StructureCraft who worked on T3, said the use of NLT panels is well established, showing up in buildings in the early 1900s. To make a panel, carpenters arrange 2xs on edge and nail them together, more or less like a carpenter would make a built-up beam from 2x stock for a carrying beam. In this case, workers used ring-shank nails ranging from 3 to 3 1/2 inches long and from 0.120 to 0.142 inches in diameter.
Panels can be as long as the design requires, but nail size and spacing, and the placement of splices between boards must be calculated carefully. The panels in T3 are up to 40 feet long, 10 feet wide, and weigh as much as 8,000 lb. They are capped with a layer of 15/32-inch-thick OSB, which acts as a diaphragm and prevents the 2x8s from “folding over like a deck of cards,” Brown said.
A 3-inch layer of concrete on top of the OSB, reinforced with wire mesh, gives the building added mass and, in conjunction with a layer of acoustic insulation, helps deaden sound.
“Timber buildings are light, which reduces the foundation and the seismic load on the building because the inertia is less,” Brown said. “But something you have to be aware of with timber buildings are the acoustics and vibration. Giving the building some mass, such as a concrete topping slab, is a solution that’s often proposed. It helps a lot with acoustics and the vibration you’d get of someone jumping on the floor.”
Brown said fabricating the hundreds of panels off-site took time, but once on site the components could be assembled rapidly with very few people. “It could be six to eight people who were throwing the whole building together, and that was all that was necessary,” he said.
Every panel, column, and beam was carefully labeled and catalogued so assemblers knew exactly where each of them went. (StructureCraft has placed a number of videos of the project at its website, and Brown wrote a blog about the project.)
Other mass timber buildings are on the way
T3 may be the biggest mass timber project now, but Architect reported earlier this year that work will start on two taller buildings in the U.S. next year.
One is a 12-story mixed-use tower in Portland, Oregon, and the other a 10-story residential building in New York City. In Vancouver, an 18-story CLT student residence at the University of British Columbia is under construction, with completion expected next summer.
The U.S., however, is behind other parts of the world in its adoption of mass-timber construction, the article says, with Europe already claiming a half-dozen buildings over six stories, and Norway holding the current record with a tower 160 feet high.
Building codes have been slow to recognize heavy timber construction, and regulators worry about the potential for fire — unfairly, according to a regional manager of the American Wood Council.
“There is a lot of combustible material in mass timber,” Paul Coats, the Southeast regional manager at the American Wood Council, told Architecture. “But there are a lot of advantages to it. … What mass timber brings is a high fire resistance. It’s a solid wood slab.”
T3 may be a breakthrough for the building industry, but its owner is in no hurry to talk about it. GBA requested more information about the project from Hines but was told by Mark Clegg of its corporate communications department that Hines didn’t want to talk about the building. It wasn’t clear why.
Wood building also can be tight
Timber buildings also can be used in much smaller, residential structures — and when detailed correctly will perform to Passive House standards.
In Ontario, David Murakami Wood is building a house from cross-laminated timber panels. This week he reported the results of recent blower-door tests. In a preliminary test by Malcolm Isaacs of the Canadian Passive House Institute, airtightness was measured at 0.4 air changes per hour at 50 pascals (ach50) — despite a malfunctioning entry door that wouldn’t close properly.
In a second round of testing, Wood reported at his blog, results were much better: 0.185 ach50. That’s less than one-third the miserly amount of air leakage permitted by the German Passivhaus standard.
Wood quoted the email he got from Isaacs: “I’ve just finished recalculating the blower door test results from my visit yesterday. We did not do too badly, with an overall n50 airtightness of 0.185 ACH @ 50 Pa for both overpressure and underpressure. To the best of my knowledge this house is the most airtight building in Ontario. … This result shows the high quality and performance of all components used in the house, as well as the significant extra efforts of each of us who worked on the air-sealing. The impact on overall energy demand in PHPP [the Passive House Planning Package software used for calculating energy performance] is very significant: it drops overall specific energy use from 14.6 kWh/m2y (assuming 0.6 ACH) to 12.5 kWh/m2y.
“Speaking as an engineer,” Isaacs continued, “we have a special technical term for this results: KICKASS.”
(You can follow Wood’s progress at GBA with his blog series Wolfe Island Passive House.)
Weekly Newsletter
Get building science and energy efficiency advice, plus special offers, in your inbox.
0 Comments
Log in or create an account to post a comment.
Sign up Log in