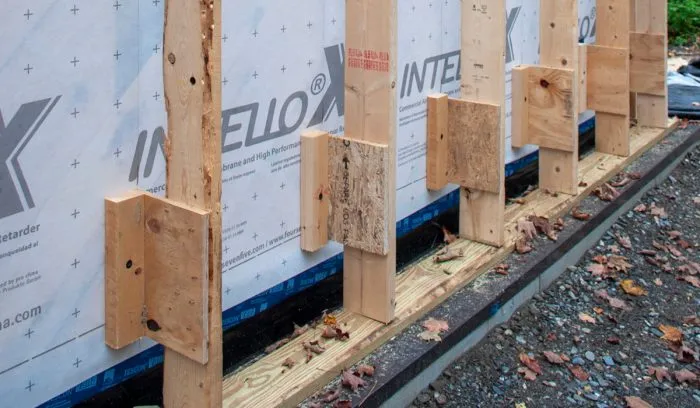
In November of 1983, Popular Science published a short article titled “Superinsulated House Trusses” that briefly described John Larsen’s alternative to double-stud walls. John, a builder in Edmonton, Alberta, developed the approach in 1981. It is still being used today and is known as the Larsen truss. The idea is to build a house with conventional 2×4 walls, install airtight polyethylene sheeting around the building, and then attach to the wall shop-made trusses of long 2x2s joined with plywood gussets. When filled with fiberglass batts inside and out, John’s walls would hit R-35 with little thermal bridging.
“I came up with this idea while framing a double-wall house,” John wrote in an email. “Normally, experienced framers do the framing much more efficiently than ordinary carpenters like myself. They are, however, not so good at vapor retarder installation, which has to happen at the same time. By using the external truss system, they can frame the structural part of the house and I or a subtrade can come in and wrap the house externally with large sheets of poly, and then install the trusses. In the ’80s there was no internet, so we spread the idea by printing ads in building publications and sold manuals with blueprints for $15. We sold hundreds.”
In a 2011 interview with Martin Holladay, John said, “I was making the trusses until the late ’80s. After that, there wasn’t a big demand anymore.”
The Larsen truss may not have taken off as a product, but variations on the idea are still widely in use today. In fact, they’re a favored superinsulated wall assembly by some cold-climate builders, and for good reasons. They don’t necessarily have to be custom-built. Common manufactured products including I-joists and floor trusses can be used. They are a fairly straightforward way to add…
Weekly Newsletter
Get building science and energy efficiency advice, plus special offers, in your inbox.
This article is only available to GBA Prime Members
Sign up for a free trial and get instant access to this article as well as GBA’s complete library of premium articles and construction details.
Start Free TrialAlready a member? Log in
7 Comments
Thanks Brian,
A really comprehensive overview, answering all the "but how would you do that" questions about detailing I had.
A small aside: Steve Baczek got away with one convincing his local authorities setbacks are measured from the face of foundations. Using that logic you could build a very small concrete core and cantilever a long way into your setbacks. I'm not sure it's a good plan (or very civic-minded) to try and reduce them on a technicality - especially as many of the restrictions concern the fire resistance of assemblies close to lot lines.
Thank you, Malcolm.
And I agree. Though I don't think it was egregious in the case of Steve's project, I've seen things like cantilevered bump outs used to subvert zoning regulations, and often, I don't love those approaches. Sometimes I don't love the zoning regulations either though.
In terms of fire separation, I believe that in the IRC, "projections" can be used as a work around for fire separation to some degree. It's described pretty well here: https://www.finehomebuilding.com/2023/10/12/fire-separation-distance?oly_enc_id=7787J8262656D9B.
Since zoning regulation and codes, in practice, often come down to decisions made between designers and builders and the officials, hopefully reasonable judgement wins!
Brian,
With setbacks in the discussion, what happened to what I remember as the Solar Access Law?
Doug
A small detail that occurred to me after the article came out is that we are cladding theses assemblies with 1x hemlock boards. So there actually is a robust exterior sheathing layer that doubles as siding.
We used Larsen Trusses on the Habitat for Humanity Passive House I designed and helped build in Corvallis, OR ( https://gazettetimes.com/albany/video-building-for-the-future/youtube_daadeb77-c11b-544f-9fdf-6a01759f4305.html ). We modified them slightly to be a 'Z' shape which allowed for a jig to be built by the volunteers and churn out stacks of the trusses that we needed for this house. We debated on doing standard rigid insulation vs a Larsen Truss and with the cost of materials and the volunteer labor, the Larsen Truss came out on top as the best option. Especially since their rigidity helped them to act as a pseudo-ladder so you could lean or stand on them if needed to reach a higher point.
Great article on showing a number of details of this system, including the often wondered about bottom covering of this thick assembly. The synthetic deck boards and insect screen is a great idea!
benwolk,
Nicely done!
No way I would rely on insect screen alone to keep pests out of walls or roofs. Use perforated flashing, or at least back the screen with 1/4" hardware cloth.
It's the only way to build or do DERs!
Log in or become a member to post a comment.
Sign up Log in