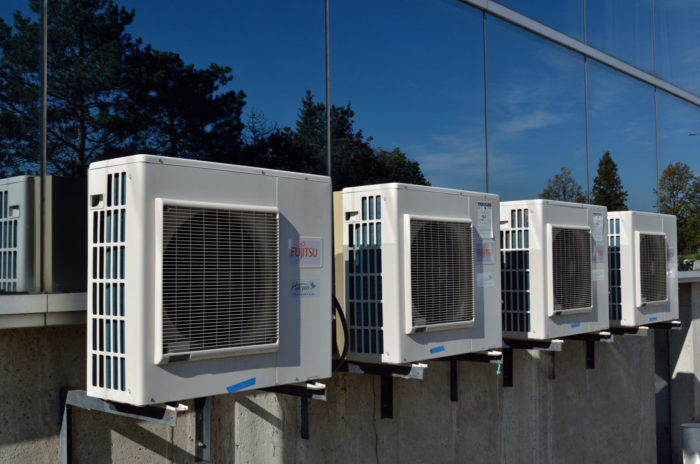
Image Credit: Open Grid Scheduler / Flickr
The agreement earlier this month among 170 countries to phase in strict limits on the use of a common type of refrigerant will mean changes to many products used by residential builders, including foam insulation and heating and cooling equipment, but consumers probably won’t be seeing wholesale changes for a number of years.
The accord reached in Kigali, Rwanda, commits the countries to a gradual phase-down of the production and consumption of hydrofluorocarbons (HFCs), a class of chemical used as refrigerants and as blowing agents in foam insulation, beginning in 2019.
A conversion to environmentally friendlier chemicals has been anticipated for years in the foam insulation industry, and in some cases already is underway, but makers of extruded polystyrene (XPS) insulation don’t expect to be weaned off HFCs until 2021. On the heating and cooling side, one major manufacturer doesn’t expect a switch to newer refrigerants for residential equipment such as ductless minisplits for a number of years.
The pact is an amendment to the 1987 Montreal Protocol and will be put into place gradually. The U.S. and the European Union are on a faster timetable than other nations, according to an article posted at The Guardian. In 2019, the U.S. pledges to cut its HFC use to no more than 90% of its baseline (an average from the years 2011 through 2013). By 2024 that drops to 60%, and then to 15% of the baseline by 2036.
Unlike the refrigerants they replaced, HFCs don’t damage the ozone layer in our planet’s atmosphere. But they are powerful greenhouse gases with 1,000 times or more the potential of carbon dioxide to trap heat. As the demand for refrigeration and air conditioning has shot up, so has the use of HFCs.
In addition to their use as refrigerants, HFCs also are used as blowing agents for extruded polystyrene insulation, a rigid foam common to many high-performance buildings, and in some types of spray polyurethane foam. Their high global warming potential (GWP) has steered some builders away from these products even though they excel as thermal insulation.
Insulation changes are already underway
A conversion to other chemicals for making insulation is already in the works in both the U.S. and Europe. The most likely replacement looks like hydrofluoroolefins (HFOs). They have a global warming potential of less than 1 and could be used in both spray polyurethane and XPS. Manufacturers still need to solve a few technical issues related to the conversion.
Prodded by the EPA’s Significant New Alternatives Policy (SNAP), U.S. manufacturers already are facing a phase-out of HFCs in the years ahead. Most formulators of spray polyurethane insulation are planning a conversion to HFOs in anticipation of tougher EPA rules, according to one industry insider. Lapolla Industries Inc. already has such a product on the market.
“Those that I’ve talked to in the foam industry seem to have this well in hand,” Alexander Hillbrand, a technical analyst with the Natural Resources Defense Council, said in a telephone interview. “I think we see much more environmentally friendly alternatives on the market. They have better thermal performance by and large. They blow pretty well.
“I have not heard any particular response [to the amendment] from the foam side,” he continued. “I haven’t heard of any particular holdups there.”
Timing remains a question. The EPA has mandated a transition away from HFCs in XPS insulation by 2021, and Hillbrand said it’s still not completely clear how the Kigali agreement will be implemented.
“We are waiting for the State Department’s guidance on how the U.S. can formally become party to the treaty, including this amendment,” Hillbrand said. “Perhaps additional steps need to be taken. We certainly have ratified or at least become a part of all the previous amendments. We have existing Clean Air Act authority to carry out all the control measures that we’ve agreed to under the HFC amendment. But in terms of the formal process we’re still waiting for some guidance on exactly how that will happen.”
XPS industry hasn’t made the switch
Dow, Owens Corning, and Kingspan are the major manufacturers of XPS available in the U.S. and none has announced a switch from HFC to HFO blowing agents.
When asked about a change, Kingspan sent GBA a two-sentence statement: “Kingspan is fully supportive of the plans to reduce HFC use agreed in the Rwanda Accord. International political agreements like this are crucial if we are to address successfully the threats posed by climate change.” The Extruded Polystyrene Foam Association (XPSA) issued a similar statement.
Owens Corning said by email it would comply with regulations in the U.S. and Canada, meaning an end to HFC blowing agents in 2021, but presumably not before, adding, “The Kigali amendment does not affect the timing of the North American regulations or our compliance plans.” The company said it “fully supports” the intent of the Kigali agreement.
EPA had originally sought a 2017 phase-out of HFCs in insulation, but the industry said the effective date was unrealistic. In its final rule, the EPA delayed the transition until 2021. Until then, HFCs will remain “acceptable” for use in XPS.
In August, XPSA said it supported the phase-down of HFCs, calling it “an important accomplishment for the industry’s stewardship and sustainability objective and a natural step in the ongoing search for better technologies to serve our customers.”
But, the association added, blowing agents are “not interchangeable” and that it took the industry 10 years to successfully complete each of the last two conversions from one blowing agent to another.
The association says that the refrigeration industry is much bigger player in the debate than insulation. The use of HFCs in foam accounts for only 16% of total HFC production in North America, it said; just 7% of the HFC-134a produced here goes into foam insulation. A “significant” amount of the blowing agent remains in the foam at the end of its service life, with typical in-use emission rates between 0.5% and 1% per year, the association said.
Plus, the trade group adds, energy savings resulting from the use of XPS are significant. “For every 1 lb. of C02 equivalent created to make an XPS foam board, 233 lb. of C02 equivalent are saved because of the energy spared throughout the life of the building,” the association said.
Refrigerants may be a tougher problem
The phase-down is a bigger deal for makers of air conditioners and heat pumps because components such as valves and compressors often must be altered or even completely redesigned when manufacturers switch from one kind of refrigerant to another.
“There definitely will be an impact on refrigeration and air conditioning based on the amendment that was agreed on in Kigali,” Hillbrand said. “When that will happen is less clear.”
The EPA, he said, has yet to approve an alternative to the R410a refrigerant used in central air conditioners, ductless minisplits, rooftop AC units, and high-pressure chillers. Alternatives are coming to market, but they’re not here yet.
“We are definitely seeing a lot of movement of industry toward a couple of alternatives, but the products that use these refrigerants are still under design, and the safety standards and codes are still in the process of being updated,” Hillbrand said.
In the past, the industry has approached conversions by looking for alternatives that are as compatible as possible with current equipment.
“That is to say, chemical producers have worked closely with manufacturers of equipment to minimize the equipment redesign that will be required when transitioning to the new refrigerants,” Hillbrand said.
“All of the major manufacturers have been supportive of the amendment to the Montreal Protocol,” he continued. “Most manufacturers do need to make some changes, of course, and there is real engineering that has to be done and changes to production and design. But the manufacturers have found time and time again they are left with better products that are more energy efficient and so they have supported these transitions and have continued to do so.”
Mitsubishi sees changes years out
Mitsubishi Electric Cooling & Heating, maker of a popular and efficient line of ductless minisplits used for both heating and cooling, said that the industry is hard at work on an alternative to R410a. Exactly when the industry will phase out its use of HFC refrigerants, however, ultimately depends on the EPA.
“It’s probably going to be 2023 or 2024 for a changeover, but that’s not even definite,” said Paul Doppel, the senior director of industry and government affairs at Mitsubishi. “Everything is pretty much dependent on the EPA’s SNAP program.”
EPA hasn’t hinted it will delist R410a for use in home heating and cooling systems anytime soon, and the agency may target other industries first to meet terms of the Rwanda accord, he said.
The global warming potential of R410a is about 2,000, and Mitsubishi expects an interim step will be to develop refrigerant blends of HFCs and possibly some HFOs that get the GWP to no more than 750 before further development takes that value into the single digits. But an outright switch to an HFO refrigerant isn’t in the cards.
“Development cycles are long,” Doppel said. “It’s going to take a while. It’s around the corner, but not right around the corner.”
When the industry does move away from HFCs, he added, Mitsubishi doesn’t expect the efficiency of its heating and cooling equipment would suffer, and doubts there would be much of an impact on consumer pricing. In fact, an earlier conversion from R22 to R410a helped Mitsubishi introduce its inverter-driven compressors, a technical innovation that improved performance.
Deal has broad support
A statement issued on October 19 by David Doniger, director of clean air programs at the Natural Resources Defense Council, and Stephen Yurek, CEO and president of the Air-Conditioning, Heating and Refrigeration Institute, praised the new pact on HFCs.
Because of the growing worldwide demand for air conditioning and refrigeration, they said, HFCs are “the fastest growing of the gases damaging our climate.”
“Unlikely as it may seem, this global HFC phase-down has the backing both of leading environmental groups and the industry that makes and uses these chemicals,” they said. “With their support, the Obama administration pushed hard for the Kigali deal to reduce and replace HFCs. Coming after last December’s Paris climate agreement, an HFC pact is the biggest step we can take this year to significantly reduce human impact on the environment.
“The HFCs avoided over the next 35 years will amount to the heat-trapping equivalent of 70 billion tons of carbon dioxide,” the statement continued. “That is equal to stopping the entire world’s fossil-fuel carbon dioxide emissions for more than two years.”
They said the agreement also will lead to better technology.
“Cooperation on HFCs shows that we can still govern — locally and globally — and can solve the challenges of climate change,” they said. “ We all can and must do more to beat the heat and the HFC success story is a victory for common sense and the environment.”
Weekly Newsletter
Get building science and energy efficiency advice, plus special offers, in your inbox.
2 Comments
And the meaning of "life" is... ? :-)
Without properly defining the term, there's a huge squish factor in the XPSA spokesperson's claims:
"A "significant" amount of the blowing agent remains in the foam at the end of its service life, with typical in-use emission rates between 0.5% and 1% per year, the association said.
Plus, the trade group adds, energy savings resulting from the use of XPS are significant. "For every 1 lb. of C02 equivalent created to make an XPS foam board, 233 lb. of C02 equivalent are saved because of the energy spared throughout the life of the building," the association said."
Really?
What's missing here is the definition of anticipated lifecycle, which could be anywhere from 20 years to 200 years, or even something else.
The 233lb. per lb. of CO2 equivalent is a curiously precise number (sure it's not 237 lbs?), but completely devoid of content. To have any relevance at all, in addition to the lifecycle, we'd need to know:
What is the paradigm energy source that's emitting all that CO2-equivalent?
What is the seasonal heating/cooling energy use where that number becomes true?
What is the description of the building assembly with the XPS behind that number?
Clearly if you wrap 10" of foam around a house heated/cooled with a mini-split in the mountains of Costa Rica (where the grid is 99.9% renewables, and the loads are low) a 233lb. savings of CO2 equivalent over a lifecycle simply can't be true, even if you assumed a 1000 year lifecycle.
But putting 1" on a house heated with an oil burner in Churchill Manitoba the 233lb. number is probably an extreme under estimate.
In short, that number appears to be complete fiction, a made up piece of marketing fluff with no bearing on reality. If there is a context & data behind that number, it's well past time to show the supporting evidence. Without context it is meaningless drivel.
@Dana
"Clearly if you wrap 10" of foam around a house heated/cooled with a mini-split in the mountains of Costa Rica (where the grid is 99.9% renewables, and the loads are low) a 233lb. savings of CO2 equivalent over a lifecycle simply can't be true, even if you assumed a 1000 year lifecycle.
But putting 1" on a house heated with an oil burner in Churchill Manitoba the 233lb. number is probably an extreme under estimate.
In short, that number appears to be complete fiction, a made up piece of marketing fluff with no bearing on reality. If there is a context & data behind that number, it's well past time to show the supporting evidence. Without context it is meaningless drivel."
That is a very good point, also with diminishing returns the 1st inch of foam will save much more then the 15th inch.
Log in or create an account to post a comment.
Sign up Log in