Best wall construction for long term efficiency & durability: Zone 6A

First off, thank you GBA for creating this fantastic resource for all to use. My wife and I built our current home 5 years ago and we were considered cutting edge for our area with the first home to use SIPs (PU 4″) and a Superior Walls Basement. Now we are looking to build a new home for our growing family and move even further north in Michigan (Zone 6A per your map) so we were hoping for even better insulation in our new home. We currently have R24 walls and R60 attic with energy heel trusses. Our initial thought was to go with PU SIPs again but their difficulty in future modifications (i.e. adding/changing windows or door openings) made me start looking at using prebuilt wall panels from our truss company and then simply spraying the cavity full of SPF. Needless to say, you guys have really gone crazy with this technology in the last 5 years (or maybe the information is now more accessible on sites like this) and my head is spinning with concerns about OSB and moisture with PU foam (inside, outside, both sides). I thought I had found the trick by using a product such as Dow SIS or ZIP R for the exterior sheathing but still it seems that I was not fulling informed. Am I correct that even the thin structural layer of the SIS if sandwiched between PSF and the 1″ of built in Dow foam will be at risk for water issues and future strength & durability concerns? Why isn’t there a simple solution for sheathing yet (i.e. steel) to do away with these concerns while allowing for great insulation in the wall cavity and a layer of foam as an thermal break on the exterior.
We are trying to build as green as possible and have a system that is very quick to install similar to the SIPs to help keep construction costs in check while also acheiving a high r-value to help keep our heating and cooling costs down. That is why I was leaning towards a wall panel approach in conjunction with SPF after the electrical is run. We are planning on using several exterior finishes including hardi-plank, cedar planks, cedar shakes, & stone veneers and to be honest I am clueless on what extra I will need to do if we do need to add 2-4″ of extra blue foam to the exterior in order to allow for all these exterior finishes to work while creating the proper insulation on the exterior to protect the sheathing.
I should also add that we liked that the 4″ SIPs of our current home did not require expensive jambs for our windows. We will have even more windows in our next home since it will be in the middle of the woods and we want to bring all the natural light and nature into the house. This raises some cost concerns for the jambs with all these super think wall structures that I am reading about (i.e. 4″ exterior foam or double walls). We plan on having large energy heels on the trusses to get the insulation in the attic up to near R70 (Foam seal & blown in cellulose) and also using a radiant barrier on the roof sheathing to help control loss of heat in winter and keep it cooler in the summer.
We hope that this will be our last home and it will stay in our family forever so we want to build it right. Durable and efficient as the title suggests. Yet we are also trying to do it as cost effectively as possible. I know I am probably going to hear 1000 different suggests but I am open to all at this point. I appreciate everyone’s input and I appologize for being such a “beginner” on this.
GBA Detail Library
A collection of one thousand construction details organized by climate and house part
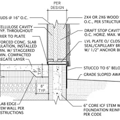
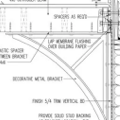
Replies
I am not a pro, but double-stud walls and dense packed cellulose is pretty green, durable, and inexpensive for the R value you can achieve (at least in my neighborhood). As for the expense of big jams, what per cent does that add to the cost of the house vs your savings in heat loss by having thicker walls? Don't you think they will be paid for soon enough? Zone 6A ain't Florida. That's my take on it.
John,
Thanks for the response. I have just started to read up on the double stud walls and the exact opposite end of the spectrum with the Advanced Framing (2x6 24"oc). Is there a good online resource showing the ideal double stud wall design from inner drywall to exterior finish?
Also in regards to the dense packed cellulose: how do you prevent settling and also is it advised to spray an layer of SPF to seal the cavity first ("1).
Paul,
1. You don't have to worry about moisture accumulation in your wall sheathing if you fill your stud bays with spray foam. I'm afraid that an earlier answer I made on another Q&A thread may have misled you on this issue; my answer in that case was based on a misreading of your question. Sorry.
2. To find out how to dense-pack double-stud walls with cellulose insulation in a way that prevents settling, see How to Install Cellulose Insulation.
Your deep window jambs needn't be a significant cost item. Install standard windows as 'outies' with 1/2" or 3/4" plywood bucks, return the interior sheetrock finish to the window at sides and top and install a wood or mdf sill board. It's a nice look and the SR returns will help reflect light into the interior. Even better if you go to a double stud wall. Deep window reveals are great.
Hi Paul,
you asked about double stud walls
I think John K, Martin and James M are giving good advice.
I think double walls, outie windows and vented attics are a good path towards Buildable & Affordable high performance and "Pretty Good" homes.
You will have a hard time finding Double Wall details at GBA except for some scattered details posted by Forum members....
hundreds of details with exterior foam...few that are Sans Foam
I have found good articles (with details) related to Double Stud walls over at JLC
http://www.jlconline.com/cgi-bin/jlconline.storefront/4f54cd880efc6e3b27170a323cb406a1/Product/View/1101hig
Articles by John Abrams, Dan Kolbert are good
I will warn you that Double Wall stratagems are not-so-popular with Building Science Corporation.
Great feedback. Maybe I should have added that our previous house was an early 1900s foursquare with beautiful woodwork thoughout. Our current home is built in the same style but we have painted trim in this house. Our next home will hopefully be our last home and we want that feel that the original foursquare had. The oak trim just had such great character and since we plan to bring nature in with a lot of windows in the next home I think we are both set on having wood returns to match the wood windows (leaning towards Jeldwen casements for our windows). The first floor will be 10' ceilings just as our current home. 2nd story will be 9' ceilings. Basement will be about 8'6" after concrete floor is poured. Still planning on using Superior Walls for our basement and it will have a walkout basement which should help bring in a bunch of natural light (I understand that the jambs in the basement walls will be deep and expensive). We plan on having 2' overhangs on the all roof trusses. A covered wraparound porch around 3 sides of the home (1st floor). I guess my point is that we are trying to build it with an "up north" cabin vibe to it be will not have a vaulted ceiling/loft in order to maximize cost per square feet. Hence the desire to have 10' 1st floor ceilings and wood trim throughout.
Martin - to keep everything on this new thread - do you mean that either SIS or ZIP or Plywood can be used as the exterior sheathing if the wall cavity is 100% SPF? If ZIP or Plywood, can you add 1" of rigid foam to creat a continuous thermal break on their exterior side - or will that create condensation concerns? The reason I am asking is trying to figure out which sheathing is best for using all of the siding materials want on the project (stone veneer, fiber cement plank, cedar plank, cedar shake) especially the cedar shake whill will need a nail base. I think the others could all work with the Advanced Framing 24 oc studs and furring strips with the SIS but the shakes will likely need furring strips with osb/plywood for a nailing base. Would I be better off skipping the SIS and simply going with ZIP or Plywood? If so, can 1" of rigid be used without concern for condensation and drying issues? Or given that there will be so many windows would the exterior foam layer simply be overkill and just use a rainscreen mesh behind the siding to allow ventilation?
Sorry for so many questions, but it is apparent you guys know your "stuff"!
Paul,
Q. "Do you mean that either SIS or ZIP or plywood can be used as the exterior sheathing if the wall cavity is 100% SPF?"
A. Yes.
Q. "If ZIP or plywood, can you add 1 inch of rigid foam to create a continuous thermal break on their exterior side - or will that create condensation concerns?"
A. I usually advise people to choose one place to put their foam insulation -- either outside the wall sheathing or inside the wall sheathing, but not on both sides. You really don't want a "foam sandwich," because it's best if the OSB or plywood sheathing can dry in one direction.
If you are concerned about thermal bridging through the studs, it's clear that rigid foam on the outside of your sheathing is preferable to spray foam on the inside.
If you insist on a foam sandwich, choose open-cell spray foam -- because it's vapor permeable.
Martin,
Sorry one last question given your answer about a foam sandwich... is there any concern about the structural layer of the SIS panel if you spray the wall cavity full of SPF? This would in essence create the foam sandwich you are speaking of and advising against? Do you know if the SIS structural layer is engineered to dispell this concern? Thanks again!
Paul,
Q. "Do you know if the SIS structural layer is engineered to dispell this concern?"
A. I don't really know, so I suppose you could direct your question to Dow. According to my research, the 1/8-in. thick interior face of a SIS panel (the structural layer) is a composite material made from recycled cardboard and additives.
You can also google Larsen Truss and Riversong Truss for more double-stud wall details. The topic of windows in, out, or in the middle is apparently somewhat debatable. The deeper into the house, the less wind-washing, etc. You'll have to read about that and make your own call. As for overhangs, mine are 3' and will be on the new house. I feel that helps keep the foundation dry.
John,
Thanks for the additional information. I agree that I want very large overhangs. I didn't know 3' was an option! The truss company offered up 12, 18 and 24" overhangs but that is probably because they are the most popular. The main roof will likely be a hip roof so the big overhangs will help keep water away from the 2nd story windows. The wraparound porch will keep it completely off the 1st story (4th wall will be a breezeway/mudroom to garage). I will definitely look into the 3' option and study up on the wall trusses.
John - also you recommend the netting with the dense packed cellulose or wet application? The wet approach scares me after reading about all the moisture concerns with walls. I think sealing the envelope and placing dry material would be the safest.... correct? Also, do you have them spray a thin layer of SPF to seal the wall cavity? That would still allow the osb/plywood to dry to the exterior and the cellulose to dry to the interior correct?
In regards to the 2x6 advanced framing method using SPF, I think I am leaning toward using ZIP + and extra layer of WRB on the top just as an added precaution instead of the SIS since the foam sandwich concerns me and I would really had to find out 20 years from now that the structural portion should not be "sandwiched" between foam! What is the best WRB to add? Felt or Tyvek? Again, I plan to use a rainscreen on top of this 2nd layer of WRB before placing the siding.
In regards to the ZIP product, are all the edges sealed on the wall sheathing? I read a previos post about some SIPs constructed with it that were cupped due to water issues and the SIP manufacturer opted to not go with the board that has all edges sealed.
Paul, one thought on the deep window wells that come with typical double-frame walls is what Marc Rosenbaum did on the "Hanover House" (http://www.buildinggreen.com/auth/article.cfm/1998/2/1/New-Hampshire-House-Pushes-the-Energy-Performance-Envelope/). There is a picture of one of the windows, with the jambs splayed out at what looks like a 45 degree angle from straight out. I liked that idea, so I used it on our new house, coming on a year old. Our windows jambs are back only about 20 degrees, which I think does the trick nicely without overdoing it. We have stained maple all around the windows, with stained pine colonial moulding trimming that out. There are a couple of windows, in bathrooms, where we left the jambs straight out for a couple of reasons. On those the "tunnel effect" of the deep wall opening is more noticeable. I went to snap a picture of one of the windows with splayed jambs for posting here, but the camera battery had run down. I'll post it later on.
As for framing of double walls, there are a great many ways to do it. Attached here are a couple of diagrams for what I did. In the case of the floor system resting directly on the sill, the rim board is insulated on the outside as part of the wall cavity (with dry, dense-packed cellulose). In the other diagram, the rim is insulated as part of the lower wall cavity.
OK, I have a shot of a window with splayed jambs. I don't know enough about photography, so I chose a window without a lot of white snow in the background affecting exposure. That's a garage wall on the outside.
Thanks for the photos. Nice option to allow in more light and prevent the tunnel effect that deep walls can have (i.e. my current basement windows). Those are deep my friend! You could probably use a stair tread for that sill.
In regards to your wall layout... did you use the Advanced Framing 2x6 24" oc method? I am leaning that way to improve the insulation and decrease lumber and thermal bridging. However, after looking at your diagrams it appears you notched the 2x6 to imbed the rim board on the outside for your deck achorage. Is this allowed? Or would it be better to extend the floor joists/rimb all the way to the outside?
Paul, the wall framing is 16" OC. Aside from exterior siding issues , I don't see why 24" OC couldn't be used. With a double stud wall, there really isn't much thermal bridging.
Originally I had the inner wall bear everything, with the outer wall supporting only itself and the windows, and also be just a 2x4. When I got to deck attachment, I had a strong preference for using the Maine Deck Brackets. Use of a ledger board bolted to the house has to be done very carefully to avoid water intrusion that has caused so many problems in other houses. In using the brackets, I didn't want the rim board to be out beyond the plane of the sheathing, as doing so would have complicated flashing and drainage plane issues. Although the brackets must be through-bolted to a sturdy rim of some sort, the attachment of the rim board itself posed a structural problem, since the vertical load of the deck wants to rip the rim off the framing. That was when the switch was made to have the outer wall be 2x6 and bear the roof load. The rim is let into outer wall studs, which would have left only 2" of stud left in a 2x4, not a lot of meat in my mind. That outer rim board is attached to the 2x6s with structural screws. The design with the rim board let into the outer wall studs and attached with structural screws was fine with the engineer and the local code officer.
Of course the floor system could be run out to the outer frame. In that case, the rim area would be spray foamed on the inside. The thermal bridging of the I-joists over the extra 8" wouldn't amount to much. Doing it the way I did really wasn't difficult for the framing crew, and I avoided a rim spray foam job.
Furthermore, as one of the diagrams shows, the outer stud wall and sill plate overhang the foundation by 2", capturing the external foam foundation insulation. This avoids the use of an ugly looking sloped Z-flashing to protect the top of the foam board. The face of the foam is protected by modified surface bonding cement.
The deck runs around a good part of the house, and the attached garage overlaps part of the uphill side. Framing in other areas of the outer wall perhaps could have been done with 2x4, to save wood, but the difference wasn't all that much and we opted for consistency in the outer framing and used 2x6 there all around.
For a house without the complication of an attached deck (eg. free standing), or where a conventional bolt-on ledger board is used, the outer wall could be just 2x4. Furthermore, the only reason to have the outer wall extend out beyond the concrete foundation is to capture the top of the foundation insulation. All the insulation just as easily could be installed on the inside, and I suspect I'd do it that way if I had to do the house over again. In a cold climate, the thermal performance of the insulated concrete basement, mostly buried, won't be much different from one insulated on both inside and outside.
Paul,
Dense pack cellulose is blown to something like 3.5 pcf which is a higher density than what gravity can achieve so there should be no settling.
Also, here is a link to my blog:
http://ourhouseuponmoosehill.blogspot.com/
I have some detail drawings there as well as photos that you might be interested in.
I try to add more stuff frequently - hoping to get some more detail drawings posted in the not-so-distant future.
The house is on a walk-out basement, 2x4 truss wall 16oc, airtight sheathing and vented attic under truss framed dutch gable (hip) roof.
The widows are outie style - planning drywall returns and h.w. sill.
My understanding of how to combat moisture problems. At least this is how I understand the theory. 1. Everything will always get wet, so everything needs to be able to dry. 2. You want to install layers in such a way that materials, especially organic and water sensitive materials, don't get wet.
A lot of moisture problems are caused because water vapor in the air migrates through vapor permeable layers in the wall to the cold side of the insulation. There the vapor turns to water and causes mold, rot, etc. Consider a standard stud wall with fiberglass in the cavities and a poly vapor barrier. If the poly isn't sealed well, moisture migrates from the inside to the sheathing and turns to water. Now you have wet OSB.
Other moisture problems happen because someone enthusiastically tries to seal out all water vapor. Spray foam inside, spray foam outside, and you get the foam sandwich that Martin cautions against. Or poly on one side and peel and stick membrane on the other. The problem is that once a little moisture gets in, it can never get out. Like a lobster trap.
As long as you know what is vapor permeable and allow a path for building materials to dry, you should be OK. And you need a good solid vapor barrier someplace on the warm side of the insulation. So SPF in stud walls is fine with almost any sheathing, as long as the sheathing can dry to the outside. The ZIP membrane, house wrap, and good old tar paper are all permeable.
I hope this help. It is my understanding anyway.
I found a lot of good information about high R-value walls over at buildingscience.com. I especially liked the section Enclosures that Work. The article "High R-Value Wall Assemblies" may be useful to you. It lists the pros and cons of 12 different wall construction methods. Of course take everything with a grain of salt, but still, I found the documents helpful.
Clement - thanks for your feedback and the link. I will give it a look later tonight. You actually summed my my new understanding perfectly. Although I think I will be leaning towards plywood after reading up some differences between osb and plywood in the last 24 hours. Either way, I think I am goint to look at advanced framing technique with 2x6 24" oc with closed cell SPF for the entire wall cavity. Then adding tar paper or tyvek to the exterior before the rain screen (regardless of plywood or ZIP for the sheathing). Huge overhangs (36" sounds perfect) and keep the basement up at least 24" above grade to keep the house "high & dry" and the garage will hopefully have 12" of footing exposed above grade for the same reason. It will have a walk out basement too so the only other concern I had was tieing in the decks but the entire deck that is attached to the house will also be covered so except in very extreme weather no water should be near the attached area - yet I think I will look at those Maine Deck Brackets just to be extra safe anyway!
What is everyone's thoughts on ZIP vs Plywood? I guess I didn't realize there were any issues with OSB since it is used so much on homes. Thinking of using Plywood instead everywhere.
Paul,
ZIP sheathing is essentially another kind of OSB that is designed so that their proprietary tape will stick to it.
Most tapes (even the high quality ones) will not stick very well to regular OSB without first being primed.
Personally, I would recommend plywood.
It is very durable and tolerates wetting and drying better than OSB - so it will probably tolerate wetting and drying better than ZIP sheathing as well.
Plywood fuctions as a "smart" vapour retarder - its permeability increases when it gets wet - I don't think this is the case with ZIP.
If you are considering an airtight sheathing approach, then there are many high quality tapes that can be used with plywood, including Siga, Proclima, and 3M.
Never having priced out ZIP, I can't comment on price vs plywood.
But every building centre that I have ever been to stocks plywood - not necessarily so with ZIP sheathing.
Pricing for ZIP ought to include the cost of their tape but plywood sheathing will have to factor in the cost of tape if you are going that route.
Remember that going with ZIP sheathing doesn't necessarily guarantee an "airtight" envelope - good details need to be drawn out especially where one assembly transitions to another.
Airsealing "the field" of the wall/ceiling is the easy part...
Paul, I like ZIP, I like quality plywood, I like pressure treated products when in doubt. OSB has to stay dry and if so is fine. Quality 4-5 ply plywood is my favorite. Never 3 ply for me anyway. Your closed cell foam should work well with ZIP or plywood. I would not use standard OSB though with your build. Hope this helps.
Thanks for the input