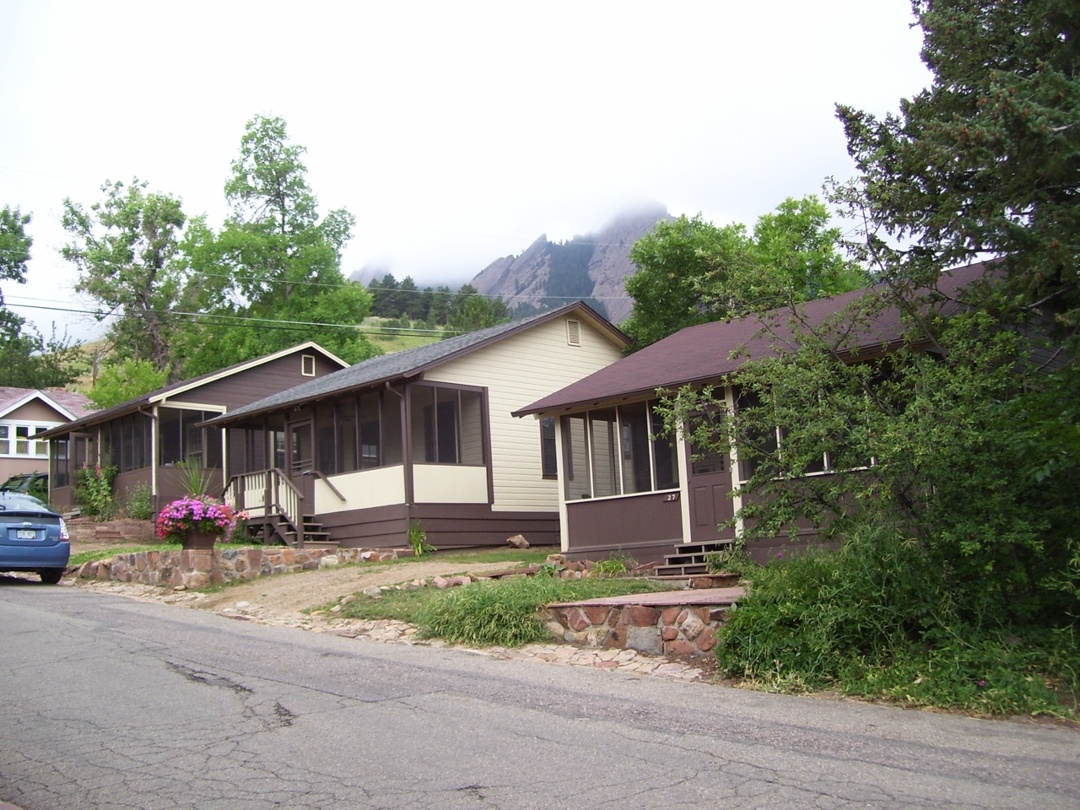
Image Credit: Jeff Medanich
Image Credit: Jeff Medanich Cottage 512, another representative residential unit that the Colorado Chautauqua rents to visitors.
Image Credit: Jeff Medanich This image is the 1st in a series of 7 showing the steps Jeff took to insulate and air seal the walls of Cottage 703 while maintaining their drying potential for long term durability. Step 1 - fur out all studs 1.5 inches for greater cavity depth for insulation.
Image Credit: Jeff Medanich Step 2 - Wedges have been driven in between the bottom courses of siding and the wall bottom plate/top of foundation to create a drainage and air space that communicates with the outside.
Image Credit: Jeff Medanich Steps 3 & 4 - Cut off the wedges flush inside and out and install insect screening.
Image Credit: Jeff Medanich Step 5 - install stops or narrow spacers against the sides of each stud. These spacers will hold the rigid insulation 1/2-inch off of the interior surface of the cladding and maintain an air space for drying potential in the wall even as it is air sealed and insulated.
Image Credit: Jeff Medanich Step 6 - RIgid insulation is pressure fit into the wall cavity up against the stops so that a 1/2-inch air space remains.
Image Credit: Jeff Medanich Step 7 - Spray closed cell foam into the remaining cavity space for a total R-value of about 26.
Image Credit: Jeff Medanich One hygrothermal approach that Jeff is taking with high performance preservation in the cottages is to use Tyvek StuccoWrap as an interior drainage plane in each open wall framing cavity.
Image Credit: Jeff Medanich Cottage 510's HERS rating score sheet prior to gut rehab: 166
Image Credit: Jeff Medanich Cottage 510's HERS rating score sheet after gut rehab: 56
Image Credit: Jeff Medanich Cottage 512's HERS rating score sheet prior to gut rehab: 165 Cottage 512's HERS rating score sheet after gut rehab: 62
Image Credit: Jeff Medanich Salvaged wood ready for final clean-up and reuse.
Image Credit: Jeff Medanich Many of the cottages had fiberglass batt insulation with no air sealing. In this image, you can see the spray foam air sealing applied after all of the batt insulation was carefully removed and salvaged for reuse.
Image Credit: Jeff Medanich This ET irrigation controller station is part of a web-enabled, on-site weather station driven system to manage irrigation according to actual conditions on the site and in the area.
Image Credit: Jeff Medanich This sign says an awful lot about the Colorado Chautauqua approach to all of its work, but particularly its work to preserve sustainably. Their motto--Escape, Engage, Elevate--is coupled with their approach to their renovation work, encouraging all to learn about all aspects of work at Chautauqua.
Image Credit: Jeff Medanich Carefully removed batt insulation salvaged for reuse.
Image Credit: Jeff Medanich Signage explaining what can be mixed recyclables and what is trash. Note the signage is in both English and Spanish.
Image Credit: Jeff Medanich True to the Chautauqua theme of learning and engaging, residents get real time feedback on electric use in the renovated cottages.
Image Credit: Jeff Medanich This cottage crawlspace, once vented and unconditioned has been insulated and air sealed and pulled into conditioned space. Note the heavy plastic ground cover over the bare soil of the crawlspace.
Image Credit: Jeff Medanich Map of the Colorado Chautauqua grounds.
Image Credit: Collorado Chautauqua This is a map of Lake Chautauqua in upstate NY. You can see how the shape of the lake lead to its name, in Iroquois, meaning "two moccasins tied together."
Jeff Medanich tells the story of preserving the Chautauqua Cottages’ historical character while retrofitting them to high performance
There really is no greater remodeling challenge than green historic preservation. After a 25-year career in East-coast remodeling and then Colorado production homebuilding, Jeff Medanich is tying together all this experience in his green retrofit work at Chautauqua.
A bit of Chautauqua history
From the late 1800s to the 1930s, the Chautauqua movement brought seasonal educational events, concerts and social activities to tens of thousands of communities across the US. During this era, Chautauqua came to mean an organized gathering introducing people from all walks of life to great ideas, new ideas, and issues of public concern.
NOTE: Chautauqua is an Iroquis term meaning either “two moccasins tied together” or “jumping fish.” The connection between these two is clear when you ground it to Chautauqua Lake in Western New York, where the earliest “Chautauqua” gatherings and events took place (see the last photo in the photo gallery, with a map of the lake).
The Colorado Chautauqua Association (CCA), located in Boulder, Colorado, began in 1898 and has been in continuous operation ever since. That’s a one-hundred-and-thirteen-year long legacy of dedication to learning, providing educational, recreational, and contact-with-nature experiences to the community. Boulder’s is the only year-round Chautauqua, and the only one whose grounds are free and open to the public.
The Colorado Chautauqua Green Goal
Given this background, it makes a lot of sense that the Colorado Chautauqua located in Boulder set out in 2008 to become the most sustainably operated and most sustainably maintained National Historic Landmark in the United States.
Much of this task is squarely in the hands of GBAdvisor and CCA Facilities and Preservation Manager Jeff Medanich. “There are four closely related themes to our green building work here at Chautauqua,” says Jeff Medanich. “Energy efficiency, water efficiency, durability, and preservation. The last for us means sustainability within an historical context.” While Jeff’s work extends well beyond the Chautaqua’s cottages to its dining hall, lodges, and community buildings, the focus here is on the 100+ year-old efficiency to 3-bedroom cottages.
The Chautauqua Cottages
The majority of the CCA buildings are sixty wood-framed cottages, most built between 1900 and 1920 and averaging approximately 500 square feet in size. These building were originally intended for summer use only, so true weatherization and building envelope improvements are a challenge (and are maybe not such low-hanging fruit after all). Jeff coined the term “High-Performance Preservation” to identify the approach to the undertaking, being sure to emphasize the dovetailing of historic preservation, stewardship to the National Landmark, energy efficiency, and sustainable building techniques.
The learning lab approach
Jeff recognized that these 60 cottages provided a situation that the building science community is always looking for: multiple examples of identical or very similar buildings that lent themselves perfectly to comparative testing. These are buildings with the same construction techniques, same building components, same size, same orientation, etc.
This lead to the creation of the Colorado Chautauqua Learning Lab. The premise is that prior to any rehabilitation work, cottages are tested for energy performance, air infiltration, energy consumption, and occupant comfort. Various energy enhancing upgrades are applied to the buildings and through the same testing protocol, changes are measured and documented. Because of the buildings similarities, various upgrade packages can be applied to one building at a time, providing the opportunity to accurately assess and compare the benefits as well as the challenges of each approach.
The learning lab approach means that Jeff and his team of Preservation Specialists, as they are known, are preserving the tradition of innovation, exploration and learning with their own buildings and their high performance renovations. At the same time, Jeff and his team at CCA use their high performance renovation work to educate visitors, both on-site and via the CCA website, as well as partner in their renovation with various local educational institutions and work programs CCA has partnered with the Boulder Green Builders Guild, City of Boulder’s Landmarks Board, and Boulder County’s Energy Smart Program to share CCA experiences and employ the CCA- owned buildings as a training facility for weatherization techniques and energy efficiency upgrades for existing buildings. Much of what CCA is learning applies to many buildings other than those designated as historic.
Start here: building assessment
Jeff is a big believer in thorough assessment prior to prioritizing work. “If we are going to make these cottages more energy efficient, we need to determine first if they are structurally sound and how they have or have not been handling moisture,” says Jeff. “Then right behind that is testing for airtightness.”
Jeff’s assessment team uses the following tools: moisture meters, blower door, infrared camera, data loggers and supporting computer software. After several years of working with outside contractors and energy raters and utilizing their test equipment, CCA, a non-profit organization, budgeted in 2011 for their own testing equipment, including a blower door and infrared camera (and professional training for both tools). These tools help Jeff evaluate his team’s air sealing and insulation techniques in real time and at multiple stages of their rehabilitation work.
The building science and construction details of high performance historical building envelopes
“The crux of our historic renovation process is the building assemblies,” said Jeff. “How do we make them more airtight and better insulated while maintaining their durability and appearance?” Jeff went looking for precedents and advice, and found precious little that applied specifically to his buildings, their construction, and preservation constraints. He ended up working through the building science principles and developing his own assemblies.
“Building science tells us that it’s okay for our buildings to take on moisture, as long as they are allowed to dry at a similar rate,” said Jeff. “We are air-sealing and insulating buildings that in many cases were never insulated and certainly not air sealed. These buildings have been getting wet for a hundred years but have had the ability to dry rapidly. Now we come along and dramatically alter the dynamics of the building assemblies. I don’t want to be known as ‘the guy that rotted Chautauqua.’”
How CCA addresses water efficiency
Right up there with energy efficiency in the Boulder area is water. Although Boulder typically gets a respectable 20 inches of precipitation annually, extended dry periods and cyclical droughts are a reality.
The Chautauqua water efficiency program is comprehensive: EPA WaterSense faucets, showerheads, and toilets inside every building. And outside, evapotranspiration irrigation controllers, drought-tolerant landscaping, and waste water irrigation collected from Coolerado space conditioning units are used throughout Chautauqua.
Weekly Newsletter
Get building science and energy efficiency advice, plus special offers, in your inbox.
Lessons Learned
Chautauqua's Learning Lab encourages both experimentation and sharing results. Here is Jeff outlining what he thinks are the key lessons he has learned from his retrofit work to date:
Using HOBOs
The data loggers we use are Hobo units made by Onset. The model I use mostly logs temperature and relative humidity, and they are set to take a snapshot of those two variables at ten-minute intervals. I have found these devices to be very useful when we are upgrading heating and cooling systems and trying to maintain occupant comfort levels in different spaces within a building. They work well on both our larger buildings and the individual cottages. In several of the cottages that we have converted to the use of wall-mounted, efficient space heaters, the data loggers provide information regarding room temperatures at various locations throughout the cottage and help achieve consistent comfort levels and provide information as to how air is (or isn't) being circulated through the building.
We have also installed two indirect/direct evaporative coolers (Coolerado) in the past two years, and the Hobo units help monitor indoor relative humidity levels as well as temperature. These devices, when used in conjunction with our energy monitors, provide an opportunity to graphically demonstrate the value of taking advantage of Boulder's climate and the value of night-cooling strategies and their effect on energy consumption.
High performance preservation wall assemblies
The nature of our cottages, the way they repeat in design, and our Learning Lab approach provides the opportunity to experiment with various wall assemblies as we conduct our rehab projects. Since we can’t alter the appearance of the cottage exteriors and must we do all our rehab work "from the inside out," we have tried more than one approach to insulate and air-seal from just the inside.
We first experimented with creating a vented air and drainage space between the siding and the insulation through the use of a layer of rigid insulation (see photos). After brainstorming with fellow building scientists at last year's Building Science Summer camp, I decided to try another approach, eliminating the rigid insulation and using Dow Tyvek DrainWrap fastened to the sides of the studs and top and bottom plates, being careful not to attach it to the back side of the siding.
Prior to installing the DrainWrap, we constructed several mock-ups of wall sections and applied various insulation materials, including closed-cell foam and cellulose, to assure that the DrainWrap retained its "wrinkles." This second approach was more cost-effective and provided a continuous drainage plane. To further increase the wall assemblies' R-value and address thermal bridging, we then applied a layer of rigid foam with all seams and edges taped and sealed to create an interior air barrier prior to installing the drywall.
Due to ease of installation, availability of materials, labor and material costs, and performance to date, the DrainWrap wall system is my favorite. We will continue to monitor and observe our retrofitted wall assemblies for any changes.
Tankless water heater performance
Especially with low-flow fixtures, it is easy to “fool” the tankless water heaters with hot water draws too low to trigger the tankless water heater. We have augmented all of our tankless water heaters with a plumbing design that includes booster tanks and sections of larger diameter pipe to promote mixing.
General Specs and Team
Location: | Boulder, CO |
---|---|
Bedrooms: | 2 |
Bathrooms: | 1 |
Living Space: | 500 |
Additional Notes: | The Colorado Chautauqua Cottages range from studios to 3-bedroom units with about 400 to 800 square feet of living space. |
Project Manager: Jeff Medanich The HPP crew: - Dave Majorowicz - Brian Hawkins - Casey Birdsall - Jeff Strohmeyer - Steve Watkins Trade Partners: - Lind's Plumbing - Meyer's Heating & Air Conditioning - Master’s Electric - EnergyLogic - ThermalCraft Insulation
Construction
Original:
- Vented, dirt-floor crawlspace
- 2 x 4 uninsulated wood walls
- Vented attic with fiberglass cavity insulation
Post-retrofit:
- Unvented, spray foamed R-12 conditioned crawlspace
- Insulated & air-sealed R-26 wood walls
- Insulated & air-sealed R-40 vented attic
Energy
- Prestige condensing boilers
- Noritz tankless water heaters
- Rinnai wall-mounted space heaters
- Energy Star Panasonic exhaust fans
- Energy Star CFL & LED lighting throughout
- Energy Star ceiling fans
- Tamarack whole-house fans
- BlueLine Energy Monitors
Water Efficiency
- HET WaterSense American Standard toilets
- Low-flow WaterSense Delta H2O Kinetics shower heads
- Low-flow WaterSense Delta faucets
- No dishwasher
- No clothes washer
- Native, drought-tolerant plantings
- ET Weathermatic irrigation controllers
Indoor Air Quality
- Exhaust-only ASHRAE 62.2-compliant mechanical ventilation
Green Materials and Resource Efficiency
- Commingled construction and demolition recycling (65% diversion rate)
- Salvaged framing and attic fiberglass batt insulation
- Green Natura and Amsan Green Solutions housekeeping products
Certification
- 5-star HERS ratings
0 Comments
Log in or create an account to post a comment.
Sign up Log in