Vapor Retarder for Basement Walls

Hi – I am installing R-10 2 inch XPS foam boards on the interior outer walls of my walk out basement. I am then installing metal 2×4 studs which will be filled with R-15 Rockwool for a R-25 total. I am doing this on this new construction so I don’t have to insulate the basement ceiling as some here pointed out more than 50% of the basement is below grade, and my 8 foot basement is 80% below grade.
My question is before I cover with sheetrock, or cover with another product if someone could suggest one as this is an unfinished basement, do I have to put plastic over the Rockwool? I am thinking I don’t since the 2 inch foam board acts like a barrier and though Rockwool supposedly doesn’t mold, I am thinking it’s not good to have two barriers. The rim joist will be sprayed above – I want closed cell but the insulation guy says I can use open cell. I think since is trying to talk me into doing the first floor walls with open cell, he can kill two birds with one stone if the open cell people are on site.
Thanks everyone in advance.
GBA Detail Library
A collection of one thousand construction details organized by climate and house part
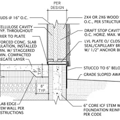
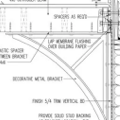
Replies
Hi James.
You do not need a vapor retarder inside the studs. Make sure that the builder air seals the rigid foam during installation. Even more important that preventing vapor drive is preventing humid air from reaching the concrete walls.
EPS is a more environmentally friendly option than XPS, by the way. And you could use the same approach that you are using in your walls (preferably EPS rigid foam + mineral wool) in your rim to avoid closed cell spray foam another material with high global warming potential.
>"I am installing R-10 2 inch XPS foam boards on the interior outer walls of my walk out basement. I am then installing metal 2×4 studs which will be filled with R-15 Rockwool for a R-25 total. "
Where to begin on just how WRONG this approach is...
The extremely high thermal conductivity of steel studs reduces the "whole-assembly R" a 16" o.c. R15 wall to less than R8, (and that's even including the R-value of the sheet rock and interior air film.)
If you're going to use steel for the studwall, use shallow steel FURRING (less than 1.5" deep, not something that fully penetrates the rock wool layer, or even half way. A standard steel 2x4 is 4.0" deep, so using standard 7/8" hat-channel furring instead of studs to trap stacked batts up against the foam will yield something over R13 for the steel + rock wool assembly using standard 2x4 steel top/bottom channels. That reduces the full penetrating steel to just the top & bottom channels. A further improvement would be to use narrower channels for the hat furring to eliminate even those thermal bridges.
[edited to add]
Take a look at the performance of assembly B.1 in Table 3.1 (p.6) this document, which is a steel 2x6/R18 studwall, the nearest assembly to your sub-assembly with steel stud 2x4/R15:
https://cfsei.memberclicks.net/assets/researchreport/RP18-1.pdf
With no credit for air films on both sides of the assembly (you only have one anyway), and gypsum on both sides, surface to surface R-value is only about R9.5, barely more than half the center-cavity R-value of the insulation. Counting just the interior side air film would bring that up to about R9.9. With a 2x4 steel stud the thermal bridge is slightly more severe, so you really can't expect more than R8 performance out of it (including air film + wallboard) for that layer of your wall.
Going with steel furring instead of studs and continuous R15 stacked batts would add a pair of air films yielding about R16- literally twice the performance using the same amount of insulation, and slightly less steel.
[end edit]
>"EPS is a more environmentally friendly option than XPS, by the way. "
This isn't even close. XPS is a three alarm environmental disaster by comparison to EPS.
In all of North America XPS is blown with a mix of HFCs (predominantly HFC134a), all of which are EXTREMELY powerful greenhouse gases, currently banned for that application under the Kigali Amendment to the Montreal Protocol. HFC134a has a CO2e footprint of about 1400x CO2 @ 100 years.
Worse still, HFC blown XPS is only warranteed to 90% of it's rated R @ 20 years. The initially higher performance that makes the labeled R legal under FTC rules is due to the HFCs, which diffuse out slowly over time. At full depletion 2" XPS will only perform to R8.4 rather than it's labeled R10.
EPS is blown with variants of pentane (about 7x CO2 @ 100 years) most of which escapes the foam at the factory where it recaptured, not vented to the atmosphere, and has no effect on the materials R-value performance. The R-value of EPS is stable over many decades.
The blowing agents make XPS by far THE LEAST GREEN insulating material in common use. It has 3x the CO2e footprint of (also pretty bad) second-worst HFC blown closed cell polyurethane at any given R-value and nearly 10x that of EPS:
https://materialspalette.org/wp-content/uploads/2018/08/CSMP-Insulation_090919-01.png
In Europe, XPS is blown with CO2 (which unremarkably has a 100 year CO2e footprint of exactly 1x CO2), and performs at a decades-stable R4.2/inch, the same as EPS of similar density.
>"My question is before I cover with sheetrock, or cover with another product if someone could suggest one as this is an unfinished basement, do I have to put plastic over the Rockwool?"
Absolutely DON'T install an interior side vapor barrier. That would trap ground moisture in the assembly, and even "exterior-grade" steel furring/studs would succumb.
With 2" of polystyrene (R8.4 @ full depletion, if XPS) and R15 batts, the foam is 36% of the total, which is sufficient dew point control at the foam/fiber boundary in US climate zone 6 or lower to be able to use a Class-III vapor retarder (=standard latex paint on wallboard) as the interior side vapor retarder, with very low risk of excessive wintertime moisture accumulation inside the fiber layer:
https://up.codes/viewer/connecticut/irc-2015/chapter/7/wall-covering#R702.7.1
>"The rim joist will be sprayed above – I want closed cell but the insulation guy says I can use open cell."
That depends a bit on your climate zone & siding assembly/type. In zones 6 or higher a 1" - 2" flash of closed cell may be necessary to protect the structural wood in winter. In zone 5 or lower open cell is usually the better bet, and VERY safe if the siding is assembled as a rainscreen (the "vented cladding" exception in R702.7.1 ).
Hi Dana. Rather than type a new question, I thought I would ask here.
Due to the rising cost of lumber, I have been considering switching to metal studs for a basement remodel project for a client (Climate Zone 4 (Cincinnati, OH)). I was planning on 2" EPS followed by 3.5" of mineral wool batts
I'm interested in your approach to use hat channel to trap the insulation bats. While the walls are not load bearing, is there any structural concern for hanging items off the wall (e.g. shelves, TV's, etc) or would the hat channels be sufficient?
Thank you Dana - I was surprised at your strong feedback me using 2x4 metal studs for wall framing as I've seen this recommended because the metal won't mold like wood. I could not find 2x4 Bluwood in Connecticut so I went with the metal which is thin and open on one side. The metal studs do not come in contact with the exterior cement walls because I have a 2 inch thick layer of XPS R-10 foam board that is sealed with 3M tape. There are a lot of videos out there on how to enclose a basement and it seems just about everyone's first layer is foam board against the cement before the framing like I did. I've seen 1 inch foam board used by many and I thought the 2 inch would be a better layer. XPS I read doesn't allow mosture through, I will say I never worked with metal studs before, and I am only doing the mechanical area of 24x24 feet this way. The rest of the 24x60 I mentioned to my wife I may switch to wood studs since the metal is a pain to work with. I do like how holes are pre-made for wiring though. After reading your feedback I looked up EPS and the only one I can find at Lowes is 1 inch thick. The PolyShield description says better R-Value but doesn't say what it is. If I put two if these 1 inch boards up, it's a range of $5 to $9 less expensive than 2 inch XPS, but I don't know if 1 inch of PolyShield is R-5 like one inch of XPS. I did a good job at airsealing the exterior seal plate against the foundation with first Liquid Zip then sealed the foundation, seal plate and sheathing with a layer of Siga Tape which is amazing. I mention this because I don't want to make mice a home with RockWool in the rim joist which is why I was going with spray foam. I think I am building tight to avoid mice but you know they get in and leave their droppings in the rim joists in the past so I am trying to be a step ahead.
>"...in Connecticut..."
-------------
>"...I looked up EPS and the only one I can find at Lowes is 1 inch thick..."
In Southern New England there are multiple vendors of USED and factory-seconds foam board at a fraction of the cost of box-store goods.
https://hartford.craigslist.org/search/sss?query=rigid+insulation
https://newlondon.craigslist.org/search/sss?query=rigid+insulation
https://newhaven.craigslist.org/search/sss?query=rigid+insulation
Used foam has an extremely low CO2e footprint, since the environmental hit has already been taken, and re-use is just piling on to the benefit side of the cost/benefit balance.
From a design point of view, with used XPS, derate to it's fully depleted R4.2/inch. With used EPS assume it's labeled performance is valid. With used polyisocyanurate it gets more complicated- some of the older HCFC blown goods is still better than R5/inch, some of the hydrocarbon blown stuff may only be good for R3/inch at temperatures that matter:
https://www.greenbuildingadvisor.com/article/polyisocyanurate-rigid-foam-and-thermal-drift
A 4" Type-VIII (1.25 lbs per cubic foot nominal density) roofing EPS would meet/beat the current IRC prescriptive R15 continuous insulation without using ANY fiber fluff between metal studs, and you could go with a 2x3 rather than 2x4. (At 4" Type-VIII EPS runs about R16.6, slightly lower than Type-II EPS' R16.8.)
Again, if using any fiber insulation use hat-channel metal furring, not studs, since the studs penetrating the fiber layer robs it of about HALF it's potential performance or more.
From a dew point control perspective using foam + fiber, all of CT is in US climate zone 5, where it takes only R5 of foam on the exterior for dew point control on R13 of fiber (about 28% of the total-R as exterior foam) to be able to use standard latex paint as the interior side vapor retarder, per R702.7.1:
https://up.codes/viewer/connecticut/irc-2015/chapter/7/wall-covering#R702.7.1
So 2" of foam (any type) is going to be sufficient dew point control for R15 batts, no interior side vapor barrier needed. But 4" of EPS (any density) and a 2x3 studwall (no fiber) would still meet code, with no vapor retarder requirement whatsoever.
In my own home in MA (also zone 5) a bit over a decade ago I installed 3" of reclaimed 2lb roofing polyiso. At the time I was presuming a derated R4.5-R5/inch, which may have been optimistic, but it still would have met code at the time (under IRC 2006.) With polyiso it's important to keep the cut bottom edge off the slab, or it can wick and retain moisture. Since my basement slab is below the local water table during some weeks of the spring thaw I stopped the foam a bit above the high-tide mark of historical flooding, just in case the power goes out rendering the sump pumps useless. With EPS this would not be necessary.
Most used foam vendors have roofing EPS in stock, though polyiso tends to be in greater supply locally. Used XPS is fine: Re-using XPS does less damage than virgin-stock EPS, since no new polymer or blowing agents are used, only a bit of transportation fuel carbon emissions.
In CT using open cell foam to insulate the rim joist is low risk, and nearly zero risk if there is a layer of exterior insulting sheathing, or back-ventilated siding (vinyl siding is the IRC paradigm for "vented cladding", though rainscreened siding is even better.)
I wish I knew about used foam when doing my foundation as I would have insulated the outside.
I wouldn't use this used stuff on the interior of my house, even if it is the basement. The plan is to have HVAC vents and registers in the basement, and even though it will be covered, no one knows the history of where this used stuff is coming from or what is on it. I'm trying to build right as you also have to remember health. When I was in Great Barrington this past summer, I told the women bagging my order that I don't think it's right to have customer subject you to their filty re-used bags. She agreed and said she tried not to think about it. I mentioned when I was a bagger in a grocery store when I was younger,, all the bags were paper and I filled a clean bag that I touched. I said I would be wearing gloves because God only knows what some of these people have been with the bags. So now with the virus, people are told not to bring their bags in the stores and this practice is being cancelled for now. So my point is there has to be a balance between health and saving the planet.
>"I wouldn't use this used stuff on the interior of my house, even if it is the basement. The plan is to have HVAC vents and registers in the basement, and even though it will be covered, no one knows the history of where this used stuff is coming from or what is on it."
That's unduly conservative.
Most used foam has only been between a substrate on roof deck and membrane roof on a flat commercial roof. You don't have to buy the stuff that looks like it's been pond-soaked or insulating a dank mushroom farm or stored in such a way as to have developed mold. Foam that's been in service for 10-20+ years has far fewer outgassing chemicals than virgin stock foam- the volatiles have already left. Most used polyiso lots that I've seen look very clean, or even new. A common tell tale sign of age is that the dimensions can a bit off due to shrinkage with age, eg: instead of 3" x 48" x 96" it might be 3-7/8" on one edge, 3-15/16 on another, and 47-7/8'" x 97-3/4", none of which really matters here.
For somewhat more money virgin stock factory-seconds foam is available at about half the price of perfect goods through distributors. The defects are usually dinged/dented corners or facers, or some un-evenness in the flatness. Both Green Insulation Group in Worcester MA and Insulation Depot/ Nationwide Foam in Framingham MA usually have factory seconds EPS and polyiso in stock, usually priced about 50% more than used goods.
I appreciate the thermal bridging Dana. Question, I too am in the process of the same design in my basement. Given the foundation wall is not exactly plumb nor straight, I was planning to set 2 1/2" metal studs 1" away from the wall. Where the studs fall, router a 1 inch channel using a hot knife tool, so there is a continuous thermal barrier of XPS to isolate the metal studs from the masonry wall. IMHO metal studs rock and no thank you to wood, treated or not. Plumb, fast, easy, do not rot. I encourage James to reconsider, and do not use the furring channel. My design is to not allow the metal studs to make contact with the wall. A top and bottom track is all you need, throw in a laser and you get perfectly straight walls. If you can anticipate items, like hanging a TV, you can provide attachments points.
Dana, would you agree this resolves the thermal penalty of metal studs? Routing XPS is easy, 8 ft level and 2 clamps. Do it outside with a fan blowing, I imaging those are some toxic fumes. All panels caulked and taped on all sides.
Another question, Does one need to have drainage at the interior base of the foundation wall for drainage? I get the dew point should obviate any water collection, but most "dry basement" applications illustrate a water drainage option. Any role for such things as hydro-lock paint applications on the wall, pre-XPS? Yes, I am looking for used XPS in my area, Zone 5. Got a full 18 wheeler load when I insulated my attic. 3 inches, came off a roof. Great shape, money well spent.
I take it back, was out there looking at the assembly, not going to router anything. Very little gain. Going to adhere the 2" XPS to the foundation wall then start the wall flush to the XPS (or nearest level point to keep wall straight) 2" metal framing, 20 gauge. Maybe rockwool in the bays, hopefully can get enough recycled XPS/EPS depending on what I find, then mold resistant sheetrock. The continuous rigid XPS, caulked and taped will be a moisture and thermal break.