2021 IECC Insulation Requirements

The 2021 IECC increases ceiling insulation requirements for Zones 2 and 3 from R-38 to R-49. Based on the math below, this increase seems to make a meager difference in performance, even at a large Delta T. I can’t imagine it would save much energy. What reasons for this increase might I be overlooking? Or, more generally, what other considerations go into setting code insulation levels?
Math: 100F outside temp (so, average roof at ~160F), AC set at 78. Delta-T = 82. The air film on the ceiling (R-0.92) is radiating heat down on you, so you want insulation…
Under the 2018 IECC, R-38 of *continuous exterior foam* (no thermal bridging) yields a ceiling temp of ~79.94F. (Math: 160 – [38/38.92 x 82]).
Under the 2021 IECC, upping that to R-49 yields a ceiling temp of ~79.51F. (Math: 160 – [49/49.92 x 82]).
Any indoor air stratification would raise the ceiling’s base temperature, reduce Delta-T, and thus lead to *less* difference between R-38 and R-49. Am I missing something here, or putting too much emphasis on the difference between ceiling temps?
Bonus question: Any reason to think about this differently with an unvented cathedral ceiling, vs. a traditional vented attic approach?
GBA Detail Library
A collection of one thousand construction details organized by climate and house part
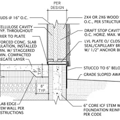
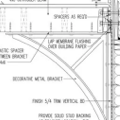
Replies
I think it's more about energy use than comfort, and the good news is that that's a simpler calculation. ΔT = 82, say 1000 sq. ft of roof. That 2158 BTU/h with R38, 1673 with R49. So you are saving about 500 BTU/h. Not a lot, but on the other hand, the cost to add that insulation isn't a lot either, if you use inexpensive insulation like blown cellulose in a vented attic.
Well, assuming it is about energy use, not comfort... I agree that one might as well add more insulation where it's not all that expensive. But in some cases, pushing to that R-49 might force someone to fur down all their rafters to fit thicker batts, change to spray foam, use a much taller fascia to hide a bunch of exterior foam, etc... I can think of lots of cases where the payback period of the additional insulation isn't that bad, but all the carpentry details it adds double the cost.
And, to give a specific example, but with a high SRI white roof, you could be looking at a ΔT more like 50. And there are only a few months in Zone 2 where such temps happen. In that case, it's 1315 BTU/h with R38, 1020 with R49... saving only 295 BTU/hr, for a pretty small number of hours per year. And wintertime ΔT's hover around 25 if you wear a sweater. But even if that ΔT was 50 for 6 months straight (4320 hrs), assuming a COP of 3 (not great for a minisplit) and electricity at $0.14/kWH (common in the sunny, deregulated, our-grid-is-collapsing South), the additional savings of going to R49 is $17.42/year... drop the average ΔT to, say, 38, and it's ~$13.29. Use the CDD formula (which grossly overestimates, in my opinion, using a design temp of 65) for a sample area like Austin, and savings are ~$18. "May as well" if it's just blowing in more cellulose, maybe not if it's forcing you to do much more, or use more high-embodied-energy materials (like foam).
Code does not require people to build fancy roof systems. If the cost is an issue, build simple and blow in cellulose.
It's not always that simple. Let's say a person is in San Antonio, where pretty flat roofs are common. Under baseline construction practices, they don't have that much room to blow in cellulose as you're probably imagining. So, to achieve R-38, they might need raised heel trusses (which often don't cut it under 3.5:12), a spray foamed roof deck, exterior rigid foam, etc... or they could build a house with a gable roof, which would give them plenty of room to blow in cellulose, and which would cost much more.
Does your code distinguish between roofs insulated between their rafters and those with attics? Ours allows much lower values when you don't have the depth in your structural members.
>"It's not always that simple. Let's say a person is in San Antonio, where pretty flat roofs are common. Under baseline construction practices, they don't have that much room to blow in cellulose as you're probably imagining. So, to achieve R-38, they might need raised heel trusses (which often don't cut it under 3.5:12),"
A vented flat roof or even a 2:12 roof is a disaster is a lousy idea in that climate to begin with.
VENTED gabled roofs bring more summertime moisture into an air conditioned house in a place like San Antonio than keeping it unvented. Venting also introduces higher risk of losing the roof in a hurricane or nearby passing tornado/derecho.
R49 spec performance (= < U0.026 ) is still pretty cheap & easy in an unvented assembly using blown fiber insulation and a minimal amount of exterior sheet foam. eg:
Filling a simple 2x12 rafter with 2.5- 3lbs density cellulose (11.25" x R3.5-3.7/inch= R39- R42) with an additional 1.5" of 2lbs roofing polyiso (R8.5) , or 2" EPS (R8.4) above the roof deck would get it there, and do much better job of protecting the roof deck than a vented solution in that climate. It would still meet IRC code minimums on a U-factor basis, even if it comes up an R or two short of making it on center-cavity R alone.
Alternatively a 10" deep (or deeper) I-rafter or open web truss rafter packed with 2.5-3lbs cellulose (R35-R37) would usually make it too, with an 1.5" of exterior roofing polyiso (R8.5) or 2" EPS (R8.4) to meet the code prescriptives for dew point control at the roof deck in that climate. If deeper than 10" the foam can be backed off to 1" polyiso, 1.5" EPS.
Either of those will work at any roof pitch in zones 1A-3A.
What doesn't work so well is a vented attic in those climates, (and a vented flat roof doesn't work well in any climate.) Even if it takes R70 of 3lbs cellulose to fill truss that needs to be 20" for structural reasons, a mere R5 foam under the membrane roofing is still sufficiently protective from interior side moisture drives.
Thin sheet foam + plus bulk fiber is pretty cheap stuff compared to 7-8" of sprayed closed cell foam or any all-sheet-foam solution. Even with the extra labor & high scrap rate of roof lines cut up with hips and valleys thin foam isn't crazy-expensive.
Note, it was a bit over a decade ago that Building Science Corp was suggesting R50 being cost effective for a vented attic climate zones 2 & 3, R40-R45 for "compact roofs". See Table 2 page 10:
https://www.buildingscience.com/sites/default/files/migrate/pdf/BA-1005_High%20R-Value_Walls_Case_Study.pdf
Energy efficiency standards have a tendency to get way off into the area of diminishing returns, similar to a lot of emissions control standards. Similar things can be said about the code change from R10 basement wall insulation to R15. If the energy savings gained by the additional insulation over the life of the home doesn't at least cancel out the cost of that additional insulation, then the money would have been better spent elsewhere. Oftentimes this means you'd actually have a greater energy use reduction doing something else with that money.
Loose fill insulation on an attic floor is the cheapest insulation to install though, which is one of the reasons for higher R values being required in that space. If they start requiring R49 walls, then you're getting off into crazyland.
BTW, one other thing to always remember about code changes: they aren't always all about safety and efficiency the way they'd like you to believe. There are politics involved too. I don't mean politics like political parties and government bodies, I mean politics of manufacturers and code writers. If a manufacturer can, for example, convince the code writers to require that manufacturer's product in the code, that is a huge win for the manufacturer, but it doesn't necassarily help the end user any. Arc fault circuit interrupters are often said to be something like this, and there are others.
While you do have to build to code in most areas, don't always assume there is a sound engineering reason behind any particular code requirement -- sometimes the "reason" is not what you'd think.
Bill
Thanks Bill. Where I live, and often work on others' houses, there are no building codes. This is terrible... and yet, it's also given me cause to examine a ton of code provisions that I otherwise would've just had to accept (like AFCI's, which I decided to always install, to the point of refusing jobs when the client wouldn't pay for them, only after tons of research and reflection).
R-49 walls would be nutty, except in the Arctic. I live in a place where, in decades to come, 120F days may be common. So I agree that if someone is blowing their attic full of cellulose, what the heck, just keep piling it up as long as the drywall can take it! But if (as is increasingly often the case) their attic is in the conditioned space, or they have a cathedral ceiling, it's more complicated. There could be lots of additional expenses and losses, as I mentioned to Charlie above...
And that's why, in this case, I find myself scratching my head. I do wonder what a well-intentioned member of the IECC committee would say. I feel like it'd be "JB, you're overlooking considerations other than temperature gradient." But what? Aside from things like how the requirements may be overkill as a way to compensate for framing factors, installer error, material degradation, etc...
My guess is the reason is just "more R will be more efficient", and there was probably no cost/benefit study done. It's probably not a huge cost increase for most builds, I just doubt that it's really justifiable.
BTW, regarding AFCIs, the only case either myself or any of my contractors has ever seen the case that would trip one actually occur is on a 277v lightning circuit, where AFCIs aren't required. No one has seen it happen in a residential setting. The AFCIs introduce lots of new nuisance issues (vacuum cleaners, thunderstorms) th0ugh, and costs. I've been told that there IS one issue where the arcing condition DID cause problems, and it was in sub-sub-sub-sub-subletted high density cheap housing developments, with daisy chained plug strips smashed behind furniture. I've also been told that future code revisions will be changing the AFCI requirement to only be required in residential developments of more than a certain number of units. That might be something to think about and watch out for in the future.
That all said, I've heard a few stories about rodent chewed cabling and over driven cable staples possibly being issues (such things have been known to trip AFCIs, but not necassarily to have actually started any fires). I often recommend the use of the plastic cable staples with two captive nails instead of the traditional formed metal staples since it's much more difficult to damage the cable jacket with the plastic cable staples.
I think the code should ban the use of push-in backwired switches and receptacles. Those things DO cause problems, and are kinda scary.
Bill
AFCI's suck in the real world. They got pushed into by manufactures and lobbyists looking to make more$$. Most pop for no reason anytime you plug a motor in. Vacuum is a common cause, but almost every corded tool I own will pop them.
I am sorry, but I see there are in fact governing building codes in your city. If Bastrop is in your city as you list on your forum member info, then why would you make such a statement?
Comfort might not be the reason behind the code insulation increase. Homes bleed the most energy thru the roof (as compared to walls). Consider that residential homes attribute a significant % of total energy consumption in the usa. Autos and industry, and commercial buildings make up the balances. [https://www.eia.gov/totalenergy/data/browser/?tbl=T02.01#/?f=M]
Increasing insulation requirements helps to mitigate (reduce) that % over time, as buildings aim towards less overall energy use. So, while 500 BTU per differential hour may seem negligible, or minuscule, I encourage you to do the 'bigger picture' math, 500btu x 24hrs per day, x a month, (you can crunch out annual heating/cooling loads), then x's this amount of savings of energy use to new construction, and remodels, etc. Adding an insulation increase to codes is a small price to pay to help offset out of control energy consumption of homes as they've been built in past decades.
I live in an unincorporated part of Bastrop *County*. There are no governing building codes. Nonetheless, everything I've designed and built is far above the codes that apply in Bastrop *City*. For example, the 7" of polyiso on the assembly I posted about here is well above even the updated IECC for my climate zone.
My understanding is that the R value parts of code are mostly determined by some ROI calculations. Evidently assuming that ceiling insulation is cheap and wall insulation is expensive. But the opposite could be true.
Right, I think that wall insulation is typically more expensive, but all those calculations vary by building beyond a certain point. Someone might have a structure with only 2x6 rafters and a shallow slope roof and have quite a bit of trouble getting beyond R-whatever, and thus might have good reason to ask why code requires them to do so. There are tens of millions of Americans living in places where codes don't apply... probably a larger number than those living in places where insulation codes are strictly enforced.
Malcolm: "Does your code distinguish between roofs insulated between their rafters and those with attics? Ours allows much lower values when you don't have the depth in your structural members."
No, mine doesn't. I don't see that IECC does either. But I'm a little surprised that you're saying your code allows *less* insulation when it's just piled on an attic floor, as opposed to in the rafter bays. I'd expect the opposite since it's much easier to air-seal the bays (to get full/consistent R-value), and also much easier to just pile up fluff on the attic floor.
Thanks for chiming in. I always appreciate how you bring a thoughtful builder's perspective to the table.
Sorry James, I must have worded that poorly. The insulation requirement for rafters is geared to the largest dimensional lumber size (2"x12") with space for ventilation. If you have unlimited depth, the way you do on an attic floor, you are required to provide much more insulation.
I'm sure the outgoing requirement was based on that -- batt insulation manufacturers make R-38 batts that are ~11 1/4" D. Incidentally, this alone reflects how much these standards are based on materials limitations (fiberglass can only give you about R-38 in a 2x12 cavity) and thus manufacturer preference (even if said preference were totally benign).
If the concern were actual performance, then why would code officials say: "well, you have more space on your attic floor, so you're required to insulate it to a higher R-value than the guy with the 2x12-framed cathedral ceiling," as opposed to "both of you need to insulate to the appropriate R-value -- and if that's harder for you, Mr. Cathedral Ceiling, then so be it."
Interestingly, Austin, generally considered forward-thinking on such matters, requires R-38 for ceilings... unless you use spray foam, in which R-25 is acceptable! That's a pretty massive difference considering that R-25 doesn't pass muster anywhere. They don't explain why, of course (kinda the theme here), but it obviously has to do with them assuming that spray foam is more likely to provide its full R value due to installation practices, and they probably also assume that it's CCSPF (~always is here) and thus will serve as an air seal. We are, I'm sorry to say, extremely far away from when more than 1% of guys with a hammer will know what a blower door test or Pascal is -- and until they do, code inspections are a bandaid. Anyone who criticizes that bleak claim... hey, come to Austin, net-zero city of the future, and work on 10 job sites with me. Then tell me what you think. So yeah, part of me thinks these requirements are just born from this fact of our present: if you think people need R-20, better tell them to go for R-40, because they're gonna screw it up.
There is a lot of anti-cathedral-ceiling material on GBA (as in, material that argues for great caution, largely on the assumption that almost no one will be careful enough to satisfy the requirements in Martin's excellent article) -- and I agree with almost all of it in principle. However, it's very easy to posit situations in which a cathedral ceiling is far more green. I know many people who build much smaller houses, much tighter, because their relatively small houses feel quite spacious thanks to things like cathedral ceilings and skylights. Such people use less energy and fewer building materials overall (again partly thanks to making some choices that are energy-wasteful in and of themselves). The problem is, and this comes up here a lot, it'll be a cold (or rather, very hot) day in hell before Americans are willing to consider going back to homes that had about 400 SF per person. My own build has about 250 SF/person, thanks to, I think, creative use of space that includes cathedral ceilings. That's what got me interested in this IECC change, though I think the question is valid generally.
The "R25 is OK if you use spray foam" argument is something that originated with the spray foam manufacturers. The idea was the better air sealing afforded by the spray foam made it perform better than R value alone would indicate. There may be some truth to that in regards to the air sealing, but you still have to hit code minimum R values regardless. The spray foam people would be better off saying that code minimum installs of their product may perform better than expected instead of trying to pitch below-code installs.
I don't think anyone has ever tried to claim cathedral ceilings are somehow "less green", just that they need more attention to some details to be able to perform well. A properly detailed and insulated cathedral ceiling isn't going to lose any more energy than an equivalent area of a "regular" ceiling.
I'd also argue that there are other things to be concerned with aside from only energy efficiency, and energy efficiency alone should not be the sole determining factor in any particular aspect of construction.
Bill
> less green ... equivalent area
It depends on which "area". If it's floor area, then yes, a cathedral ceiling uses more energy and is less green. And then there is the typical use of foam, which is less green than cellulose.
Well put (took me back to the 2009 Martin vs. Icynene Zealots battle :)). And, RE: "I'd also argue that... energy efficiency alone should not be the sole determining factor in any particular aspect of construction."... Totally. I think that when it comes to insulation, all of the non-energy-related things fall under the umbrella of "thermal comfort," which is a more nebulous concept. I'd love to see more studies on what percentage of people (there's some stuff on healthyheating.com) can notice a 1-degree temperature differential on a ceiling or wall, which is often all that the final panel of foam or lift of cellulose is gonna get you. The specific numbers have to do more with material properties of popular types of insulation... obviously, Owens-Corning prefers R-38 to R-39 since they sell R-38 batts for 2x12 cathedral ceilings.
James: air sealing and insulating are a win-win for both efficiency AND comfort, a definate plus. I would doubt there are many people who could notice a 1 degree difference, and I'm sure essentially no one could notice a small change if it was done very slowly over time. What people do tend to notice are rapid changes, such as walking from a comfy room into a drafty one.
Jon: I meant per unit surface area, in which case losses are losses regardless of the type of structure. If you mean per unit floor area, then yes, a cathedral ceiling has more surface area compared to what would be the case for a simple flat ceiling. I disagree that you have to use foam though -- while foam is common in retrofits, a new build can be designed to use dense-pack cellulose or other things -- you just need to plan for that in the design.
Retrofit cathedral ceilings are one of two niche places I actually think spray foam makes sense (the other is irregular foundation walls, such as cut stone). I usually recommend against it for nearly everything else, since it offers little benefit for the cost, or the lack of greeness, when compared to other types of insulation.
Bill
RE: Dana (#18) -- "A vented flat roof or even a 2:12 roof is a disaster is a lousy idea in that climate to begin with." Agreed -- but I've seen it plenty. I'm not usually dealing with insulation for clients, but I definitely get to see the terrible designs from the inside out... that said, I didn't intend my hypothetical example to be a vented roof. Was just trying to say that the "eh, why not just blow in a few more inches of cellulose?" adage, while usually all well and good, doesn't apply in all cases. And sure, that's at times due to sub-optimal design choices.
And I appreciate BSC's recommendations, but remember this exchange?
Martin: "I called up Joseph Lstiburek and asked, “How did you determine the R-values in the published table?”"
Joe L.: "We guessed, and I think we guessed reasonably well." (https://www.greenbuildingadvisor.com/article/r-value-advice-from-building-science-corporation)
Dana,
You mentioned that, "A vented flat roof or even a 2:12 roof is a disaster is a lousy idea in that climate to begin with." Is that 2:12 roof applicable in Zone 4B climates also? I See many 2:12 roofs in that climate zone and don't see any long-term problems or failures.