Adding wall insulation to an older home

Hi,
I have a 1940 colonial in Connecticut. Our original cedar siding (shingles) are shot and can’t be easily repainted for various reasons, so we’re heading down the path to do full strip and reside with Hardie, and to replace our 30-year old vinyl replacement windows that have failed in various ways.
As part of the exterior reno, all existing siding, trim, windows, and a few doors, etc. will be replaced. Any rotted sheathing will be fixed, etc. Our contractor and various searches have suggested wrapping the house in VP100 Blueskin instead of a traditional housewrap. Blueskin is air and water impermeable, but allows vapor to flow out.
This gives us an opportunity to retrofit insulation into our walls from the outside. In most areas of the house, our walls are plaster over rock lath/button board, an empty cavity, and then tongue in groove sheathing covered in siding. In a few rooms, the walls are already drywall and have some kraft-faced fiberglass in the cavity. Other walls are 3/4″ tongue-in-groove wood panel instead of drywall / plaster – these walls may have kraft/fiberglass in them already… hard to tell. There is no plumbing running through the walls beyond a few hose bibs on the first floor. We have steam heat, so there are asbestos covered steam pipes in various wall cavities. All exterior walls are 2×4. (Note – the attic was airsealed and insulated to R60 a few years back, so we are OK there. But the walls are mostly empty).
I’ve read various articles about using dense-pack cellulose or fiberglass in the walls, and it’s unclear as to whether I should be concerned about moisture passing into the walls. Examples:
https://www.buildingscience.com/documents/insights/bsi-043-dont-be-dense
http://bobyapp.com/blog/2009/06/myths-about-insulating-old-house-walls
https://www.finehomebuilding.com/2009/06/29/why-i-dont-use-cellulose-or-blue-jean-insulation
All of these (to varying degrees) raise concerns about retrofitting insulation into older houses – either because of leaks / bulk water intrusion or because of condensation / moisture transfer to the wall.
How concerned should I be with this issue? How do I assess them? The VP100 and new everything should limit / eliminate bulk water, since the windows, flashing, housewrap, etc will all be tied together. But should I be concerned with humidity in the house moving into the walls? Right now, the house is quite “leaky” but I expect the windows, doors, Blueskin, and air-sealing around rim joist will address that. I don’t imagine a house this old could get too tight…
I know another options is foam paneling on the outside, but because our roofline (no overhang/eaves), this is an expensive proposition and would also be cosmetically difficult.
So the choice is either to add insulation (dense cellulose or fiberglass – injection foam is too expensive) or do nothing.
Any guidance would be helpful. I’ve tried to do my own research, but at some point, the path becomes unclear. Hopefully I’ve provided enough (too much?) info.
Thank you in advance!
GBA Detail Library
A collection of one thousand construction details organized by climate and house part
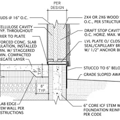
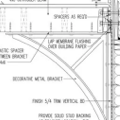
Replies
MLN,
First of all, can you tell us your name? (I'm Martin.)
Assuming that we can't convince you to install a continuous layer of exterior rigid foam, your best bet is to (a) install dense-packed cellulose insulation in the stud bays, and (b) install a vented rainscreen gap between the WRB and the siding.
For more information, see these articles:
"How to Install Cellulose Insulation"
"All About Rainscreens"
Hi Martin, My name is Marc. Thanks for the quick reply.
I actually read the rainscreen article before speaking to contractors, and asked about installing one.
We spoke to multiple Hardie preferred/elite exterior contractors and and all gave me the same line about it not being required in Hardie install specs, and that the blueskin prevents water intrusion as it is a membrane WRB.
If that is true, is there an issue with filing the walls with cellulose or fiberglass? I was (maybe incorrectly?) more concerned with interior humidity moving into walls and condensing but I can't tell if that's likely to be an issue... I've read articles on condensation points in the wall but can't tell where those are relevant to a thin 2x4 wall.
The cellulose article is excellent. The reminder that this has been done for decades in houses probably like mine in New England is helpful.
Any comments on using fiberglass? Almost every insulation company here seems to have stopped using cellulose.
Marc,
During the winter, your wall sheathing will gradually gain moisture. This moisture comes from the interior of your house, not the exterior, so your WRB (the Blueskin) won't reduce the rate of moisture accumulation.
The reason you want a raincreen gap is to allow the damp sheathing to dry quickly in April and May, once warm weather reduces the rate of moisture accumulation in your sheathing layer.
By providing a way for the back of your siding to dry quickly after a rainstorm, the rainscreen gap will also help your paint job last longer.
> "I actually read the rainscreen article before speaking to contractors, and asked about installing one.
We spoke to multiple Hardie preferred/elite exterior contractors and and all gave me the same line about it not being required in Hardie install specs, and that the blueskin prevents water intrusion as it is a membrane WRB."
Your contractors are asking you build something that would be a code violation. Who cares what Hardie says- how about what the IRC says? Chapter 7, TABLE R702.7.1:
https://codes.iccsafe.org/content/IRC2018/chapter-7-wall-covering?site_type=public
In US climate zone 5 unless there is a Class II or tighter vapor retarder on the interior the cladding must be vented, unless there is sufficient insulating sheathing (R5+) for dew point control.
The vapor openness of Blueskin is immaterial if there is no air gap to dry into. It doesn't need to be much- even 1/8" make a huge difference. The air gap is a capillary break Blueskin is not. When there is liquid water clinging to the micro-gap between the Hardie& Blueskin moisture WILL move into the wood sheathing. Hardie will tolerate that moisture just fine it doesn't need it, the way wood siding might to avoid cupping/splitting, or causing the paint to peel, but it puts the plank sheathing at risk.
Dense packed fiberglass (1.8 lbs per cubic foot density or higher, R15 @ 3.5" in a 2x4 stud bay) is fine, 1.0 lbs density fiberglass (R13 @ 3.5" in a 2x4 bay) is not. Low density goods aren't very air retardent. While Blueskin is a good air barrier (it's like 4' wide strips of tape), leakage at the bottom & top edges is harder prevent completely- the air retardency of the cavity fill still matters.
I’ll ask about the rainscreen and see what it costs and what changes it might require to various other plans. If it is possible and cost effective, it is something I will do. It seems like there are 6mm screens that are an interesting option.
Let me ask the question a different way, though I suspect you won’t like the question - if there is no rainscreen, would you recommend against the dense pack insulation (and thus laving most walls empty) for fear of condensation and wet sheathing?
Also... on the class 2 vapor retarder... at what point do 80 years of layered paint equivalent to a vapor retarder? Is this something that gets considered?
Thanks.
Marc,
Skipping the rainscreen would be false economy. If you are planning to demolish the existing siding and install new siding, now is your chance to install the siding correctly.
That said, the need for the rainscreen depends in part on the type of siding you intend to install. For example, if you are installing vinyl siding, the rainscreen gap isn't necessary -- because vinyl siding is inherently well ventilated.
>"...if there is no rainscreen, would you recommend against the dense pack insulation (and thus laving most walls empty) for fear of condensation and wet sheathing?"
Dense packing does not INCREASE the amount of moisture reaching the sheathing from interior moisture drives- it slows it down.
Using cellulose instead of fiberglass redistributes the moisture, lowering & sharing the moisture burden of the sheathing, but it's hygric buffering capacity is not infinite.
>"Also... on the class 2 vapor retarder... at what point do 80 years of layered paint equivalent to a vapor retarder? Is this something that gets considered?"
In that 80 years some of those layers are undoubtedly leaded alkyd paint, which is a Class I vapor retarder (a true vapor barrier), and yes that gets considered. It means that there is effectively zero drying toward the interior. But the interior finish wall is unlikely to be truly air tight. Has there ever been any nail holes for pictures? How about electrical outlets? Is the plaster perfectly crack-free? Iven small amounts of air leakage can move orders of magnitude more moisture than vapor diffusion through standard latex paint (a Class III vapor retarder). The air-retardency of the cavity insulation limits the amount of interior moisture delivered via convection in winter, when the sheathing to interior temperatures are the greatest, and convection drives are highest.
My house is 130 years old, and we went with the exterior insulation plus rainscreen behind wood clapboards. We created the rainscreen gap simply by fastening wood lath to to each stud through the surface of the foam. 3/8" wood lath is really (really) cheap and easy to install. There's pretty much no excuse for leaving it off, especially since Code requires it. Try to convince your contractors, or find contractors who know what they're doing. "We've always done it this way" just isn't a reasonable way to run a business.
How much should a rainscreen add to cost? Assume 35k job price for the strip/wrap/trim/siding. There a whole lot more for windows and other work but figured the siding part is relevant. Thanks.
The rainscreen mat type materials cost about $0.50 per square foot, installed. For me, the wood lath was even cheaper, at about $0.30 per square foot, as close as we could figure. I provided the lath and the siding guys installed it for free. The longer stainless steel nails for the siding were the only thing that really cost anything. They had to go through the lath and 1" of rigid foam in addition to the siding and sheathing.
HI Marc -
The free-draining and air flow forgiveness of a rainscreen cladding are a must for your climate zone (5A). If you pin water between your cladding and your WRB, water will make its way into your wall assembly (I have seen this happen with exactly your selected combination of cladding and WRB).
Also, take the interior pressure off: manage your interior wintertime humidity, maintaining it at or below 35% (at say 68F). To manage it you need to measure it; see this GBA resource: https://www.greenbuildingadvisor.com/article/measuring-and-understanding-humidity.
Peter