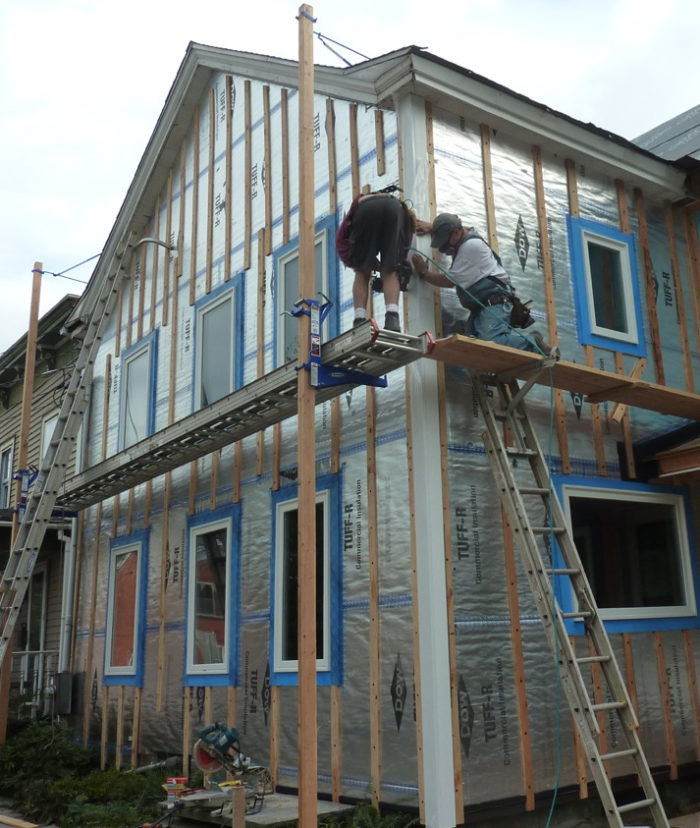
Image Credit: Image #1: Joel Schuman
UPDATED on June 24, 2018 with new product information
Twenty years ago, very few residential builders knew what a rainscreen was. These days, however, it’s no longer unusual to see siding being installed on vertical furring strips or a plastic drainage mat. As rainscreens become more common, mainstream builders are beginning to ask, “What’s a rainscreen? How do I know if I need one?”
This article will pull together information to answer the most common questions about rainscreen gaps between siding and sheathing.
What’s a rainscreen?
You can’t really point to a rainscreen, because it isn’t a thing — it’s a system. That’s why I prefer to talk about a “rainscreen installation,” a “rainscreen approach,” or a “rainscreen gap.”
For most residential builders, a rainscreen siding installation is one that includes an air gap between the siding and the water-resistive barrier (the asphalt felt or housewrap).
Some purists insist that you can’t call it a rainscreen gap unless you have ventilation gaps at the top of the wall as well as the bottom of the wall. If it only has drainage gaps at the bottom, but no openings at the top, the purists insist that the system is more accurately called a “cavity wall.”
However, the distinction between a cavity wall and a rainscreen wall isn’t particularly useful — in part because the distinction is based on a faulty understanding of “pressure equalization” principles — so I side with those who use the word “rainscreen” for either type of wall.
Every well-designed rainscreen wall needs:
Ventilation openings at the top of the wall…
Weekly Newsletter
Get building science and energy efficiency advice, plus special offers, in your inbox.
This article is only available to GBA Prime Members
Sign up for a free trial and get instant access to this article as well as GBA’s complete library of premium articles and construction details.
Start Free TrialAlready a member? Log in
103 Comments
homeslicker and nailing
I have installed cedar shingles over home slicker and foil faced-rigid foam, and I couldn't help wondering if all of those nails penetrating the foam were creating paths for water and generally ruining the foam as an air barrier.
Would like to learn about the
Would like to learn about the energy implications of a ventilated rainscreen
( lets assume stack effect one ) with a 0.5"+ gap during heating and cooling seasons.
Could the upper "vents" be only of partial total length ?
Let's say 10% opened at top...sufficient to drive air ?
Any other anti insect bottom flashing/screening devices available ?
I wonder about durability of coroplast material for fastening purposes... it becomes very brittle with age even when hiden from sun ( 10 years + period )
Brilliant article.
One typo: "However, these product has very tiny air gaps — StuccoWrap’s wrinkles are less than 20 thousands of an inch high." It happens. The article is so good that I hesitate to point out such a minor lapse. This is another keeper, going immediately to my Bookmarks.
What about open seam rainscreens?
I'm deciding between a regular rainscreen and an open seam one (for purely aesthetic reasons)
Besides the chance of bugs, wasps, birds, etc nesting behind it, is there any major issue with it?
Is there any proven housewrap or membrane for this purpose (vaproshield has one called revealshield) or plain old 15lb felt would do? (has to be black)
BTW, with open seam I mean either vertical or horizontal cladding separated at the seams, more as a louvered screen.
deeper rainscreen gap
Is there a problem with making the gap larger than 3/4"? I was thinking the in specific wall sections you could use a 3-1/2" gap (using 2x4 on end, for example) so that you could hide the downspouts behind the siding.
edit -- the image is not one of my projects, just something found online showing something similar to what I was thinking.
re: SULLKA LIMA
Sullka,
Our office has a project that used a liquid WRB that is black and (apparently) UV resistant (tremco envirodri, I believe).
It's not my project so I don't have all the details, but the contractor claimed it was pretty price comparable to vaproshield (our standard product) -- including labor.
I don't have a picture of this, but they painted the furring strips with the same black liquid for some protection but more for the aesthetic since the finished siding is gapped tiger-wood.
mat rain screen's
I have heard 2nd hand complaints from installers with matt rain screens that it get's difficult keeping the siding flat especially when installing shakes or shingles. I believe they were using a product called cedar slicker. Does anybody have any experience like this. or have your experiences all been positive?
Also Martin i was hoping you might elaborate on why vynal needs a rain-screen when put on top of more than 2'' of foam. Is because of fastener length? or some simple practical reason or is it building science based?
I'm also curious like Daniel S if using a larger rain-screen has it's downfalls? I've heard that in European construction they are leaning towards larger cavity's 1.5'' or so.
Good article!
Very timely and comprehensive blog.
Thanks Martin, the information is well detailed and timely as I am specifying these very details on the design of my house at this time. Unfortunately, my builder does not accept the need or value of rainscreens and believes that can actually make some situations worse.
@Tim Naugler: Yes, cedar slicker can be a challenge
Tim, It was years ago, but I have had first-hand experience with cedar slicker and its challenges. I installed vertical ship-lap siding over the stuff and had a bear of a time getting it to sit flat and look right. You could use some sort of shims or spacers to deal with low spots as you go, but at that point I imagine it might be just as easy to use furring strips and ditch the mesh.
the rainscreen projects i
the rainscreen projects i worked on in DE (and that we're utilizing on some of our projects) incorporated a larger airspace - basically 1x vertical battens and 1x horizontal counter battens (so 1.5" gap). the counter battens are strictly an aesthetic determination - we want the cladding to be vertically oriented.
i've seen commercial projects with deeper rainscreens to incorporate/hide downspouts, but it seems kind of ridiculous/wasted opportunity to address efficiency (e.g. add more exterior mineral wool)
Hydrogap comment
Although mentioned in a previous write-up, the Hydrogap product has small bumps on it that actually compress under lap siding if nailed too tightly, thus defeating their purpose. Alternative products, like Pactiv's Raindrop 3D, do not show that same tendency. I re-read the article and did notice that it called out the compression concerns.
Rain screens with sawn red cedar shingle siding
Would appreciate opinions about the desireability of rain screens when siding is 5" lap sawn red cedar shingles. Located in the rainy State of Washington.
Thanks!
Response to Eric Peterson (Comment #1)
Eric,
Q. "I have installed cedar shingles over Home Slicker and foil-faced rigid foam, and I couldn't help wondering if all of those nails penetrating the foam were creating paths for water and generally ruining the foam as an air barrier."
A. Most researchers have concluded that, as long as the fasteners stay in place, the fasteners do not significantly reduce the performance of an air barrier.
Nevertheless, airtightness fanatics often go to great lengths to minimize potential leaks, and your question merits consideration.
First of all, rigid foam may not be the best air barrier material. If you are concerned about airtightness, it makes more sense to establish your air barrier at the sheathing level. For more information on this approach, see Airtight Wall and Roof Sheathing.
Second, cedar shingle siding introduces more fastener holes than other types of siding. One approach to minimizing the effect of these fasteners is to install two layers of plywood or OSB wall sheathing: the first layer is fastened to the studs, and the second layer is installed on the exterior side of the rigid foam. This method is sometimes referred to as a "site-built SIP." (It's possible to install the rigid foam and second layer of sheathing all at once if you specify nailbase.) For more information on this method, see my description of the renovation of the home of Claudia King and Lindsey Tweed: More Job Site Visits in Maine.
Response to Jin Kazama (Comment #3)
Jin,
Q. "I would like to learn about the energy implications of a ventilated rainscreen (let's assume there is some stack effect) with a 0.5"+ gap during heating and cooling seasons."
A. If it is properly built, the rainscreen gap is on the exterior side of the insulation. It neither adds any significant R-value to the wall, nor detracts from the wall's R-value. However, if you use foil-faced rigid foam on the interior side of a 3/4-inch-deep air gap, the combination of the 3/4-inch gap and the foil facing will add about R-1 or R-1.5 to the R-value of the wall assembly.
Q. "Could the upper vents be only of partial total length?"
A. Yes. As I wrote in the article, "Ventilation openings at the top of the wall are optional."
Q. "Let's say 10% opened at top...sufficient to drive air?"
A. The deeper the air gap, and the greater the area of the screened openings at the top and bottom of the gap, the greater the air flow. More air flow translates into faster drying.
Q. "Any other anti insect bottom flashing/screening devices available?"
A. Of course. If you visit a building supply store, you'll find many types of insect screening or ridge vent material that can be adapted to this application.
Q. "I wonder about durability of Coroplast material for fastening purposes... it becomes very brittle with age even when hiden from sun."
A. I welcome any comments from readers with experience on this matter.
Response to Gordon Taylor (Comment #4)
Gordon,
Thanks for the feedback; I'm glad you liked the article.
Thanks also for catching the typo; I have corrected the text.
Response to Sullka Lima (Comment #5)
Sulka Lima,
Q. "I'm deciding between a regular rainscreen and an open seam one (for purely aesthetic reasons). Besides the chance of bugs, wasps, birds, etc nesting behind it, is there any major issue with it?"
A. The main disadvantage of open-joint cladding is that this approach allows UV rays to reach the water-resistive barrier (WRB). Since UV light will degrade most types of WRB, you have to be careful to specify the highest quality WRB available. Even then, there will inevitably be some questions concerning the durability of any WRB exposed to UV light.
Q. "Is there any proven housewrap or membrane for this purpose (Raproshield has one called Revealshield) or plain old 15lb felt would do? (has to be black)."
A. Using #15 asphalt felt would be very unwise, since it degrades quickly when exposed to UV. One WRB that is advertised as appropriate for open-joint cladding is Delta Fassade S from Cosella-Dörken. It's expensive -- expect to pay between $1.10 and $1.20 a square foot. More information here: New Green Building Products — September 2010.
Response to Daniel Stewart (Comment #6)
Daniel,
Q. "Is there a problem with making the gap larger than 3/4 inch?"
A. No -- at least not from a building science perspective. I hesitate to bring the matter up, because the controversy is complicated, but I should probably mention that some fire-safety experts have questioned whether deep rainscreen gaps could be unwise in areas of the country with a high risk of wildfires. The worry is that dry grass near the bottom of your wall might ignite, and that the fire could be pulled into the bottom of a rainscreen gap. The deeper the rainscreen gap, the more likely it is that the chimney effect might cause a fire risk.
Building codes are somewhat ambiguous on how fire safety requirements apply to rainscreen gaps. If this issue concerns you, talk to your local building official.
Response to Tim Naugler (Comment #8)
Tim,
Q. "I have heard second-hand complaints from installers with mat rain screens that it get's difficult keeping the siding flat especially when installing shakes or shingles. I believe they were using a product called Cedar Slicker. Does anybody have any experience like this? Or have your experiences all been positive?"
A. I have never used Cedar Slicker, but you're right -- some builders feel that the product is too squishy, and that it can be hard to get siding to look completely co-planar without a lot of fussing and care. Other builders seem to have a knack for using the product, and don't have any problems.
Q. "Also, Martin: I was hoping you might elaborate on why vinyl needs a rainscreen when put on top of more than 2 inches of foam. Is because of fastener length? Or some simple practical reason or is it building science based?"
A. Basically, it has to do with fastener length. Vinyl siding can't be fastened tight to the sheathing -- the fasteners need to be just a little bit loose, so that the siding can expand and contract lengthways to accommodate thermal expansion and contraction. This is hard enough to do when you are installing the product directly over OSB; if you are doing it over 2 inches of foam, it becomes even more challenging. Joe Lstiburek says that 2 inches is the limit before you need vertical furring strips. I might even be more conservative, and limit the thickness of the foam to 1 inch before switching to furring strips.
Q. "I'm also curious (like Daniel S) if using a larger rainscreen has its downfalls? I've heard that in European construction they are leaning towards larger cavities -- 1.5 inches or so."
A. See my answer to Daniel (above). As long as there is no fire risk, there is nothing wrong with a deeper cavity.
Response to Stephen Carlton (Comment #9)
Stephen,
You wrote, "Unfortunately, my builder does not accept the need or value of rainscreens and believes that can actually make some situations worse."
Perhaps you can urge your builder to read this article.
Response to John Schlosser (Comment #13)
John,
Q. "Would appreciate opinions about the desirability of rainscreens when siding is 5-inch lap sawn red cedar shingles. Located in the rainy State of Washington."
A. The answers to your question can be found in my article. Re-read the section under the heading, "Does every building need a rainscreen gap?" As I wrote, "Ultimately, the decision about whether to include a rainscreen gap is a judgment call."
Are your walls tall or short? Is your roof overhang wide or stingy? Is your house exposed to wind and the weather? How close are you to the ocean? How many inches of rain to you get a year? How big is your budget?
Remember, there is no downside to a rainscreen gap. It will help your wall dry faster and limit any repercussions from water entry. If you live in a rainy climate -- and you do -- I think that the cost of a rainscreen gap is money well spent.
Rain screen
Rain Screens sure are becoming a buzz thanks to you. I wish I would have know about them before I ever installed my first fiber cement job. I have actually first hand seen the effects of condensation behind cement board siding. Last fall I replaced a 3 year old job that the paint was peeling off. When we took off the siding it was completely soaked. Manufacture and paint finisher wouldn't pay a time. Never again will I install cement board in Wisconsin with out a rain screen. I would recommend looking at http://www.innovativeguttersolutions.com/siding-products/furring-master-rain-screen/product-information/ Here you will find all sorts of installation guides. Including a 3/8 furring master with intake and exhaust vents. We can install 2" foam and then use an ET&F nailer to just shoot the siding on.
Windows flashed into non-rainscreen layer?
Martin, you noted:
"Every well-designed rainscreen wall needs:
• a water-resistive barrier (WRB);
• an air gap between the WRB and the back of the siding...
Here are some more flashing principles to keep in mind:
• You can't flash properly unless you know which surface is designated as the WRB.
• All flashings should direct water to the exterior surface of the WRB..."
And from your innie vs. outie windows blog:
"The WRB (for example, housewrap) can be under the foam or over the foam. A third option is to omit the housewrap and use taped foam as the WRB. In most cases, innie windows require a WRB under the foam, while outie window require a WRB over the foam. (For more information on the question of where to locate the WRB, see Where Does the Housewrap Go?) No matter where the windows are located, flashing details need to tie the perimeter of the window into the WRB."
So based on all of that, here's an assembly:
1. Innie windows flashed into the sheathing layer WRB
2. Cont. insulation (let's assume of a type or thickness that would make it qualify as a vapor barrier) outboard of that, detailed as a second WRB w/ rainscreen
Why? So the insulation performance won't be reduced because of backventing (wish we had better ideas of the energy implications of that). Also, it can get tricky to try to flash the windows to the outside WRB in this situation, and I like to detail the sheathing as airtight layer. But, it does get redundant. I think this is a solid system w/ EPS, XPS or mineral wool, but would anyone be nervous about this setup if using polyiso (ie flashing windows behind it)
Response to Katy Hollbacher
Katy,
If I understand your question correctly, it's this: "If I use housewrap as a WRB, and if I install my WRB between the OSB sheathing and the exterior foam, is it OK to drain my rough window sills to the housewrap layer?"
A. No. If the housewrap is under your rigid foam, you should direct the water collected by the sill pan under your windows to the exterior surface of the rigid foam -- not to the housewrap.
Window flashing part II
Thanks for your response, Martin-
The sheathing WRB would actually be a liquid-applied product ("spray-on drainage plane" as I like to say). Note that if it were possible to flash to the 2nd WRB/rainscreen layer, the only purpose of the 1st (sheathing layer) WRB would be as an air barrier. That aside, I don't understand your answer in the context of your innie-outie post, as the two seem contradictory:
"The WRB (for example, housewrap) can be under the foam or over the foam. A third option is to omit the housewrap and use taped foam as the WRB. In most cases, innie windows require a WRB under the foam, while outie window require a WRB over the foam. (For more information on the question of where to locate the WRB, see Where Does the Housewrap Go?) No matter where the windows are located, flashing details need to tie the perimeter of the window into the WRB."
Based on the above, I read that it's OK to flash to the inside of the exterior insulation, but in your response in this thread you noted otherwise. Can you please clarify?
Reference from your "where does the housewrap go" post:
https://www.greenbuildingadvisor.com/sites/default/files/Housewrap%20location%20detail%20-%20GBA.jpg
Another reference, see Figure 7 on page 9:
http://www.buildingscience.com/documents/digests/bsd-105-understanding-drainage-planes/files/bsd-105_understanding_drainage_planes.pdf
Thank you again, great topic!
Response to Katy Hollbacher
Katy,
Your logic is impeccable, and you are quoting me accurately. Joe Lstiburek and others are satisfied that it's OK to direct water to a WRB behind rigid foam. In theory, it's going to work.
However, in a few rare cases, more water ends up on the sill pan than can easily evaporate. If your sill pan ever gets lots of liquid water, it's much better to direct it to the exterior of the foam than to the WRB behind the foam. That's just my opinion.
If I were flashing a rough window sill with your type of WRB, I would extend the flashing to the outside of the foam. Joe Lstiburek might disagree -- I'll try to phone him when I get a chance -- but that's the way I would do it.
Windows part III
Thank you again, Martin. I'd put my opinion somewhere in the middle of yours & BSC. For now I think I'll stick with my original instincts on this:
1) whenever possible, flash windows to the outside of the exterior insulation
2) if that's difficult because of "innie" windows or some other reason...? then:
- if flashing windows behind exterior insulation, try to use rockwool (or another vapor-open product)
- second best is EPS or XPS
- tread carefully w/ polyiso (I don't want water getting into unprotected joints on the backside of polyiso)
A very detailed discussion on
A very detailed discussion on rainscreens and its usages. Temperature fluctuations are minimized due the achievement of higher effective R-values therefore creating a much more efficient wall assembly and dramatically reducing the loads on HVAC systems.
Response to Jenny Belman
Jenny,
I disagree with your conclusions. Rainscreen gaps do not, and are not intended to, "minimize temperature fluctuations due to higher effective R-values." Rainscreen gaps have very little, if any, affect on a wall assembly's R-value. There is no way that a rainscreen gap will "dramatically reduce loads on an HVAC system."
rainscreens
Nice comprehensive article Martin. The question I never see addressed is that of fire-spread caused by the chimney effect of an open cavity. Buildings in urban-woodland interface zones cannot have roof soffit vents under some codes, since they would such burning sparks into the attic; there are some special metal screen vents on the market that limit the size of openings and have baffles to prevent spark entrance. Doesn't a rainscreen detail tend to pull sparks from grass fires into the wall?
Response to Brian Rawlinson
Brian,
In most U.S. jurisdictions, building inspectors approve of rainscreen siding installations.
In some areas of the country with high wildfire risk, questions have been raised concerning whether a rainscreen gap poses a risk during a wildfire. The code is somewhat ambiguous on this issue. When the issue was discussed on the GBA website, the controversy generated strong emotions. You can read the previous threads here:
Rainscreen performance during wildfires
Rainscreens, Wildfire Hazard and Other Unintended Consequences
The bottom line: if you are worried about this issue, talk to your local building department.
Contractors, Architects, and the Public Need this Information!
Very interesting and relevant article. It is a sustainability, HSW and energy conservation issue. I would like to recommend a no-cost, AIA approved course (open to all, not just AIA members) entitled "Rainscreen 101 Revisited,"on this very topic. Since it is an AIA approved course, there is no commercial advertising involved. The link to the course is http://bit.ly/chQaCH. A pdf on this topic is also available at http://bit.ly/Y45ZnP
New FurringMaster 2 Aluminum .032
Hello Martin , Greg Albracht here. You did an artical in Energy Update magazinel on my Furring master steel strips and Sidingmaster
I have a new Prepainted .032 aluminum
FurringMaster 2 system and new vent system.
As Scott Frey mentioned above my old steel version of FurringMaster
Is great but I just outdated it with my new FurringMaster 2
It cost less, less to ship, easier to handle and cut
and I changed the design that improves fastening capabilities by
The new Hat channel Design
It is being used on the new HONDA Smart House
A live feed of the project will show the system going up on the Honda website.
https://sites.google.com/site/gorillagutterguard/our-products/furring-master-rain-screen-system
Adding On
What a great article! I really do believe that before long most codes will include this type of system in residential building because of the effective moisture mitigation. Too long we have been focused only on vapor barriers that, when done incorrectly, trap what water does get by the enclosure on the inside of the building. I am a commercial exterior contractor that installs only rainscreen systems and I can tell you that the approaches are a little different, but this is a very effective way to button up any type of building.
One thing I did notice is that there is not much emphasis on exterior insulation in the article or comments. Without getting technical you want to keep the majority of the wall system (studs/gyp board/etc.) to the warm side of the insulation layer. The main enemies you are trying to fight with moisture is 1) Direct (rain/snow) 2) Indirect or Wicking 3) The hardest one - Condensation. Think of the typical wall makeup that has insulation on the inside of your house wrap typically between studs. Cold air from outside hits the walls and condenses the warm air from inside BEHIND your vapor barrier - exactly what you do not want. It is important that if you want to make your house healthier, and you already plan to fir out your siding, that you consider installing an exterior insulation like rigid foam or mineral fiber outside your air barrier. Keep in mind that you still want to keep the air gap to maintain the wonderful perks of a rainscreen system. All the extra work/materials as stated above will come at a cost, but you can rest easy that you have a healthy and efficient building enclosure.
Venting into roof on gable ends?
The fact that one can vent directly into the soffit will be a welcome simplification of my design, but does this include the gable ends too? I ask because my understanding (if I'm remembering things correctly anyway) is that vented soffits on the gable ends will create an issue with the "face soffit"-to-ridge air flow through a vented roof. Will venting the rainscreen into the (unvented) soffits on the gable ends cause the same issue?
Thanks!
Response to Claython Mclaw
Claython,
While the air flow through rainscreen gaps can make a significant difference in how fast the siding dries, the volume of air we're talking about is small, and the amount of moisture carried by that air is also small. I don't think that terminating rainscreen gaps at the gable-end soffits will negatively affect the ventilation flow through your unconditioned attic.
There are several reasons why I feel confident that you don't have to worry. In addition to the reasons mentioned above, the main reason is that ventilating attics is more about hocus-pocus and wishful thinking than it is about air flow. For more information on the topic, see All About Attic Venting.
Martin. Another product to add
Martin,
Looks like a new product from Canada.
Ventgrid
4x8 sheets of seemingly fairly rigid plastic grid that should reduce flex on install andreducewavy lines?
I found online that they priceabout $1/sqft (not confirmed)
Great article!
Response to Edward Cambridge
Edward,
Thanks for letting us know about Ventgrid. If GBA readers are interested in more information about this product, here is the company's contact information:
Ventgrid
P.O. Box 959
4073 Highway #3
Chester, Nova Scotia B0J 1J0
Canada
902-273-3051
E-mail: [email protected]
Correction on list
This article is a few years old but still important and often referenced. I wanted to offer a correction to your list of rainscreens:
MTI Sure Cavity and Gravity Cavity are the rainscreen products, with rigid channels mortar blocking fabric. 1/8, 3/16 and 10mm versions available.https://www.mtidry.com/products/rainscreen-drainage-planes/sure-cavity
The MTI Perforated Control Cavity is intended for the interior of Single-Wythe Walls.
Response to Tyler LeClear Vachta
Tyler,
Thanks for the updated information on the MTI products. I have edited the article to include the new link.
Using folded-over asphalt felt as furring strips
What about your comment I found on your WRB article — is this still a recommended option? It might be a good suggestion for a rainscreen on a budget for fiber-cement lap siding?
"I wrote about this approach in an article called ‘Another Rainscreen Tip.’ The article was published in the March 2007 issue of Energy Design Update. In that article, I wrote: ‘The latest tip for creating an airspace between siding and the water-resistive barrier (WRB) is simple and inexpensive: install vertical strips of folded-over asphalt felt every 16 or 24 inches on center. Depending on the choice of asphalt felt (#15 or #30) and the number of folds, a variety of thicknesses can be created; in fact, by varying the strip thickness, the strips can be used as shims to correct minor framing irregularities.’"
-- Robert Hawke
Response to Robert Hawke
Robert,
It's certainly possible to create furring strips out of folded strips of asphalt felt. There are two obvious disadvantages to this approach: (a) Asphalt felt furring strips can't hold siding fasteners, and (b) Cutting up the strips of asphalt felt and folding them over to create a thick enough layer is labor-intensive.
The disadvantages are balanced by one advantage: asphalt felt is cheap.
Why don't wood furring strips need to be pressure treated?
I appreciate all this information in one place, but I do have a question that I would like better explained. You state that "Furring strips don’t have to be pressure-treated, because a rainscreen is designed to stay dry." If the rainscreen stayed dry, wouldn't it be pointless, since its very existence is to deal with water that gets behind the cladding? I know that the materials in the rain screen will dry out more quickly than they would otherwise, but It seems like untreated 1/4" plywood could start to disintegrate over the years if it was repeatedly getting wet, whether through wall leaks or inward vapor drive through siding.
Response to Timothy Godshall
Timothy,
Most types of siding do an excellent job of stopping rain. The amount of liquid water that gets past siding is quite small. Moreover, a rainscreen is designed to encourage fast drying, so when a few drops of water get past the siding, the water evaporates quickly.
Which is all another way of saying, "Rainscreens work." They create a dry environment between the sheathing and the siding -- exactly what you want.
Using pressure-treated lumber is not only unnecessary -- it often requires the use of expensive stainless-steel fasteners.
Lots of researchers and ordinary builders have removed siding and inspected furring strips. The furring strips stay dry.
If a wall has rotting furring strips, something is seriously wrong with the wall design or installation. Rotting furring strips would usually be a sign of a serious flashing error.
re: speed of drying, top vented vs not
Is there any quantification on how much faster it might dry with top venting? I've been stewing over the decision to vent into the attic, vent below the soffit or not vent the top at all for quite a while. The local building inspector isn't of much help; he says to just build it per the design. Well, that detail is not covered in the design - the designer says to follow the local building code. So it's a circle. By far the simplest and cheapest way for me is to vent into the soffit (or rather, behind the soffit into the attic space). One factor I didn't see mentioned is what about ice damming? With snow on the roof, a sunny day in winter, the air in the rain screen is going to get pretty warm behind the south facing siding. If that's venting into the attic, will that contribute to ice damming? Or is the amount of air too small to be of significance?
Response to Trevor Lambert
Trevor,
If you vent into the attic, there is a small increase in the chance that the air flow might contribute to ice damming. I think that the effect is quite minor, however, compared to other ways that ice dams form.
You'll reduce that risk if you vent the rainscreen gap to the exterior, below the soffit, which is the standard recommendation.
If you are really worried, you can include a layer of rigid foam behind your soffit -- limiting heat flow from the sun-heated south facade -- while leaving a slot to admit ventilation air to the attic.
Reply to Trevor Lambert
Trevor,
Sorry - this is a reply to question you posted some month ago. The NBC includes requirements for fire-stops in concealed spaces. Rainscreen cavities are interpreted as being concealed spaces connecting walls to roofs. The prohibition of venting the top of the cavity into the attic is dealt with explicitly in our code here in BC (because rainscreens are required in some regions), but not in the Ontario code. You should probably run this by your inspector before deciding how to proceed.
Hi Martin,
Another excellent article. I have a question regarding the placement of the flashing. I'm adding 2" polyiso to a house that has brick halfway up the wall. I am trying to decide whether to put the flashing against the outer face of the polyiso, which will act as my WRB (option 1) or on the other side of the furring/vent assembly, immediately behind the siding (option 2). It seems that Option 1 allows more breathability in the rainscreen above the brick, but Option 2 would better vent the cavity behind the brick. The top of the wall will vent behind the frieze board. Please see pictures.
Thanks!
Steve
Steve,
The flashing must be integrated with your water-resistive barrier, so your decision hinges on which material you decide to use as your WRB. The decision often hinges on your window location -- because the WRB has to be integrated with the window flashing.
For more information on this issue, see these two articles:
"Where Does the Housewrap Go?"
"Using Rigid Foam As a Water-Resistive Barrier"
Thanks Martin,
Sorry for neglecting to mention the windows. The windows will be flashed to the outer surface of the polyiso board, which will act as the WRB, at least for the upper part of the wall.
Flashing integrated into the WRB makes sense to me. However, image #2 (of 7) for this article, shows and spells out the flashing location: "Flash to back of siding, not to housewrap". This appears to be at the bottom of the wall, which is a similar location as what I'm asking about with my brick transition. This would be closest to my option #2.
Could you elaborate?
The difference to me seems to be that in the image, the insect screen behind the 5/4 board allows the rainscreen gap to vent, whereas for my wall, option #2 would allow the upper (above the brick) wall's rainscreen gap air cavity to connect to the wall cavity in the lower wall between the brick and the Celotex, but the resulting overall wall assembly would not have much of an air "intake" at the bottom (behind the brick) as the wall shown in image #2 of this article.
Thanks again,
Steve
Hello Martin - another dead link? https://www.greenbuildingadvisor.com/detail-library/how-to-install-windows-right-details-for-leak-free-windows-and-siding
James,
Maybe. Can you tell me where the link can be found in the article on this page?
What is your opinion of rain screen mats such as Driwall Rainscreen? If it matters, the region would be southern California coast.
Jack,
Driwall Rainscreen falls into the product category called "Three-dimensional plastic mesh and plastic mat products." That's what I called these products in my article.
Look for the section of my article that begins with the heading "Three-dimensional plastic mesh and plastic mat products," and you'll find a discussion of this approach.
Does the bugscreen go under the corner trim as well? Or do you stop the bug screen at/right before the corner
Normally I’d like to use stainless nails for siding, but what about furring strips in a non-foam application?
Especially considering the rainscreen system needs less caulk, and a little bit of water is ok to go behind the siding. Would stainless be the preferred fastener for the furring strips? Or because they see so much less water than the actual siding, is it ok to just use galvanized/coated screws?
Kevin,
Post #54: The corner trim, just like trim at openings, can either go back to the sheathing or on the battens. It will last longer if placed on the battens.
Post#55: Stainless nails help avoid stains on siding, but galvanized or screws are fine for the battens.
Martin,
Thank you for this and your many other articles that I have found extremely helpful during the major renovation of my Seattle home.
I was sold on the idea of a rainscreen, even before finding your article on the topic. I was intending to use vertical 1x3 or 1x4 furring strips. Now that I am to the point of figuring out/designing the siding, it looks like we want the house to be mostly clad in vertical (likely board and batten) siding, requiring a horizontal fastening surface.
I don't like the idea of the mesh/mat options you mentioned (or that I could turn up myself). Beyond their expense, most of those products seemed to be less than ideal for a wood cladding application. Most offered a minimal gap, at best, and are prone to compression. Only VentGrid seemed to be viable (and very expensive), but it is not sold in my area.
In the section about top and bottom venting, you mention that even horizontal furring strips likely don't really require a drainage plane, and could be used to install cedar shingles, as an example. In such an example, wouldn't closing off that drainage plane with horizontal battens also eliminate the ability of that rainscreen to properly vent as well?
Given Seattle's wet climate, I would like at least a 1/2" ventilation channel for my rainscreen. I have come up with 3 ideas, each with their pros and cons, and I would love some advice. Sheathing and vapor/air barrier will be Zip R-6 (1.5"), if that is at all relevant.
1. Use the Cor-A-Vent SturdiBatten (http://www.cor-a-vent.com/sturdi-battens.cfm). This seemed to be the only potential product that I could find that might provide the ventilation channel I would like, and accommodate horizontal installation. I noticed your article doesn't mention this option, but I don't think they were available before 2015.
2. Add a second layer of horizontal furring strips on top of the vertical furring strips, prior to installing the vertical siding. While being probably the simplest and most obvious option, this would effectively double the cost of the rainscreen.
3. Use additional vertical furring strips and/or a corrugated plastic furring strip on the corner trim to provide a ventilation channel to the cavities in the rainscreen created by the horizontal furring strips. I can provide a picture of what I am referring to, if helpful (pending this doesn't sound like an obviously dumb idea). This would be the closest variation to the rainscreen I had originally been intending to use, just flipped on its side. My major concern with this idea is that the trim would not be flush with the siding, and the potential impact that would have on the aesthetics.
Sorry for such a long and elaborate question, and thanks again for all of the great articles.
Cheers!
- Steve
Steve,
If you are planning to make your board and batten cladding from cement-based panels and battens, you can still use vertically installed furring.
http://www.fp-supply.com/st-louis-board-and-batten-siding.html
Malcolm,
Thanks for the response. I didn't even think about wood alternative products for board and batten siding. I am definitely preferential to wood, especially on "the show layer", but it is good to know about. The cement panels look like they could be a very affordable alternative, and I could probably be comfortable with a ventilation channel < 1/2" if not using wood.
Steve,
If they are going to be painted, and especially if they are contrasted with real wood as another cladding or trim, it's hard to distinguish some of the composites and cement-based siding from wood.
The advantage is having a solid substrate. Compared to most other claddings, Board & Batten made from individual boards lets a lot of bulk water get through to the cavity.
Malcolm,
Thanks for the additional reply. The reason that I want to make sure that I get the rainscreen "right" is for the reason that I don't expect my cladding to be water tight. The burden of air/water tightness falling to the "building envelope" behind the cladding. The cladding needs to serve as UV Protection and aesthetics.
Assuming a viable rainscreen, I see cost/preference as the only remaining factors to be weighed for the cladding material. Wood alternative, like the cement-based, sidings definitely have their advantages, especially if painted. The cement-based panels you suggested seem to cost less at baseline, compounded if it can reduce the cost/materials of the rainscreen.
My visual preference for wood is based entirely on it being untreated/having a natural finish; though, I likely won't be the one that gets the final say on that aesthetic detail. I agree that most wood alternatives are nearly indiscernible from real wood (especially from a distance) if painted.
Beyond its visual appearance, my statement of preference was a very personal preference for working with wood. All materials have their pros/cons when it comes to working with them, and if you are paying someone else to do the work (which I likely won't be) that all factors back into the category of cost. Delving further than that is probably not worth anyone's time, as it is a very subjective preference (as long as the objective details are properly factored in).
I definitely see the merits of using a cement-based cladding, especially if it is going to be painted/installed by someone else. Thanks again for the response, and I am glad to have it as another viable option pending final design decisions from "the boss".
Steve,
I agree. If you want wood, you need to use wood. The products made to look like stained wood don't.
Steve,
I think either option 1 or 2 would be better than option 3.
You're right that horizontal battens don't allow stack-effect ventilation. But the presence of an air gap still improves the drying rate, even without the air flow.
Martin,
Thanks for the response and weighing in on the options I provided. I wanted to follow-up on your response to ask this question a bit more generically. I feel like I am still missing something or making improper assumptions.
I know this article was about rainscreens in general. My "generic" question has more to do with the use of rainscreens on buildings with air/water tight wall assemblies. My takeaway being that the major advantages of a rainscreen, on buildings with a "tight envelope", is to provide a potential drainage plane and ventilation to quickly dry any moisture that may penetrate the siding.
With a properly constructed "tight envelope", moisture penetration should only be a risk to the siding/rainscreen. Not to say that the effort should be ignored or half-assed, but flashing and sealing penetrations on the siding become less vital than in a more traditionally sheathed/sided building. The siding on a "tight envelope" building is really only necessary for UV protection and aesthetics.
My question more specifically has to do with horizontal furring strips on a "tight envelope" structure. Any moisture that makes it into one of the cavities created would only be able to exit via diffusion through the siding and/or furring strip. If the siding were painted/latex coated, diffusion through the furring strip would be the only exit path.
Without ventilation into those horizontal cavities, I'd expect even a minor moisture intrusion could quickly overwhelm the rate of diffusion. At best, this seems like this specific rainscreen application would provide no additional benefit. At worst, I am imagining those horizontal cavities becoming an ideal environment for fungus/rot.
Everything I wrote above, while potentially reading as if it is a statement of fact, is merely my current understanding/assumptions. They were provided merely to help close the gaps in my knowledge and (hopefully) aid you in providing an answer.
Steve,
I'm not sure that I understand your logic. You wrote, "With a properly constructed 'tight envelope,' moisture penetration should only be a risk to the siding/rainscreen. Not to say that the effort should be ignored or half-assed, but flashing and sealing penetrations on the siding become less vital than in a more traditionally sheathed/sided building. The siding on a 'tight envelope' building is really only necessary for UV protection and aesthetics."
Actually, installing excellent flashing, and sealing penetrations against water entry or air leakage, always matter. These details matter just as much in a house with a "tight envelope" as they do in a house that is leaky. Why wouldn't they? It can even be argued that the reverse is true -- that homes with leaky envelopes are somewhat forgiving of minor moisture entry problems, but that tight homes are less forgiving -- and therefore demand impeccable flashing.
You also wrote, "Any moisture that makes it into one of the [rainscreen] cavities created would only be able to exit via diffusion through the siding and/or furring strip. If the siding were painted/latex coated, diffusion through the furring strip would be the only exit path. Without ventilation into those horizontal cavities, I'd expect even a minor moisture intrusion could quickly overwhelm the rate of diffusion."
Actually, outward vapor diffusion allows a lot of drying -- especially in sunny weather. Moreover, the air gap provided by a rainscreen allows for moisture redistribution -- so instead of being trapped tightly between the sheathing and the siding, moisture can evaporate into the air and be more generally distributed until it dries out by outward diffusion. This redistributive function of the air space is hugely beneficial.
Martin,
Thanks for that response and your patience. It definitely fills some of the gaps in my knowledge and clarifies other assumptions.
I think something may have been lost in translation when I used the term 'tight envelope' wall construction. I am referring to wall assemblies like Lstiburek's Perfect Wall, Zip 2.0, etc. I definitely glossed over the details of these assemblies, but I fully comprehend that flashing/sealing penetrations (of 'the envelope') needs to be done more meticulously and vehemently than with traditional construction methods.
The moisture penetration I was referring to was specifically to the backside of the siding, while remaining on the outside of the the 'tight envelope'. If done properly, from my understanding, the rainscreen and cladding should be the only things on the outside of the envelope. I have attached a very crude drawing that illustrates where my quandary is coming from (though I am not sure if it is uploading properly).
With the clarification that I expect 'the envelope' to remain air/water tight, do you still think there would still be enough outward diffusion to vent the horizontal cavities through the cladding? What if the cladding was also tightly flashed/sealed and/or coated in a sealant/paint?
Again thank you for your patience with my long responses. I think you will likely be able to provide the missing insight I am requesting after this post, but if you think my responses are too long/no longer relevant, let me know and we can happily move the discussion elsewhere.
Steve,
Q. "Do you still think there would still be enough outward diffusion to vent the horizontal cavities through the cladding? What if the cladding was also tightly flashed/sealed and/or coated in a sealant/paint?"
A. Assuming that you are planning to install board-and-batten siding, relax. Yes, the board-and-batten siding is vapor-permeable enough to allow for outward diffusion drying. Obviously, you don't want to install polyethylene on the exterior side of your board-and-batten siding -- no one does that -- but ordinary stain or latex paint won't limit diffusion enough to cause problems.
You ask about what will happen if the board-and-batten siding is "tightly flashed/sealed." In most cases, flashing consists of the occasional use of 4-inch wide metal flashing or perhaps some narrow bands of peel-and-stick -- so, not a problem. Don't be tempted to cover your board-and-batten siding in Grace Ice & Water Shield. If it's wood siding, you'll be fine.
Remember, your siding is on the exterior side of your air barrier. Siding is not an air barrier. You shouldn't make any attempt to make your siding airtight. Gaps are fine -- in fact, gaps are beneficial. Don't be tempted to go crazy with a caulk gun when you install your siding. You want a caulk-free siding installation.
Martin,
Thanks for the detailed answers! I realized when you stated, "Gaps are fine -- in fact, gaps are beneficial.", that my question could have been much simpler. That was actually the perfect answer to my actual question, which could have more directly been asked as, would gaps in the siding be fine if the battens ran horizontally.
Thanks again for all the help!
Steve,
You might also want to look at products by MTI: https://www.mtidry.com/
They make corrugated plastic lath and rainscreen products that work for vertical as well as horizontal siding applications. Their lath strips would be perfect for vertical siding, but are only 1/8" wide. If you really want close to 1/2", they make a 10mm SureCavity rainscreen that would work. It comes with a fabric scrim attached that can be wrapped around the bottom to make a rainscreen. It comes in wider rolls, but you could cut it to make lath ribbons if you wanted to. The corrugations support the siding and provide 2D ventilation behind it.
Peter,
Thanks for the reply. It's good to know about yet another product alternative. For anyone else that may find the answer they need from these comments, I think the Cor-A-Vent Products I listed above would probably work better, for a vertical wood cladding application.
The MTI products all seem to be masonry focused. I would either need to wrap the entire house (which seems a waste in my scenario), or spent a lot of time cutting lath-like strips (which sounds like a real hassle/potential to ruin the product).
That said, rainscreen products/solutions have been one of the most annoying things for me to track down during my design. Even if you find one that may suit your needs, they don't seem to be ubiquitously available across North America.
So, even though I don't think the MTI products would be the most ideal fit for this application, hopefully it might help someone else and/or be a viable alternative if their other options are too costly/unavailable.
Came across these "rainscreen clips" as an interesting way to achieve the gap while simplifying siding install.
Small aluminum clips matched to a milled profile in 5/4 (ie 1 inch) hard and softwood material, either with the "flush" clips installed over furring strips or with an offset included in the clip (thus another way to achieve the gap). These seems a good alternative to tongue and groove siding, especially as it means no fasteners through the product (no splitting, no bleeding, no figuring out the difference between a framing nail gun and a siding nail gun :)
Also seems simple to do these for an open joint cladding.
Rainscreen clips:
https://www.woodhavenproducts.com/rainscreen-clip/
https://www.woodhavenproducts.com/new-products/ ("Grad clips" with a back barbed attachment)
https://www.climate-shield.com/
https://www.novausawood.com/rainscreen-siding-clips
Timbertown in Austin and Atlanta has them too. Seems that any lumber yard that can do edge milling could produce the boards. The "grad clips" from wood haven seem only to need a back profile, so conceivably could be run on a router table or even a router with an edge guide).
Perhaps also known as Ipe clips.
I have some concerns about nails and screw penetrations of the WRB behind battens and furring strips. While we know that a rain screen will by it's very nature ventilate and dry, a typical batten may have screws at 16-24" o.c, and if something like a ship-lab siding is used, it very likely could have as many as 4 or 5 nail penetrations per linear foot. For instance Nakamoto Forestry recommends the use of two 2" nails per plank. That's a lot of penetrations.
I'm aware that many of the rubberized self-adhering and "paint-on" WRB's have self-healing properties. Are there "regular" housewraps (tyvak, Solitex mento, etc.) that have self sealing properties?
Hugh,
Two things I can think of:
The mechanisms that hold the fasteners in place are inherently self-healing. Both nails and screws rely on the adhesion (and to some extent shrinking ) of the surrounding wood fibres. If the penetrations created spaces around the fasteners which would allow air-movement, the fasteners themselves would loosen or even fall out. That's something we know doesn't occur. Try pulling a box-nail out of sheathing or a stud once it has seasoned. Most times you will end up with just the head.
An increasing number of projects rely on the external sheathing as the primary air-barrier. These houses, with or without battens, yield very good blower door tests - even though they are riddled with thousands of fasteners.
My conclusion would be, that in the absence of any evidence that they pose more than a theoretical problem, they aren't worth worrying about.
Hugh,
I think Malcom is right, but in case you can't quell your concerns , they do make self healing tapes you could apply behind the batten. (475 sells some and advertises it for open cladding siding.). Is the expense worth it, would be the only question.
Thanks Tyler. Certainly the tape (Tescon Naideck, I think) solves the problem but at a price....Malcolm indicates my concern is overblown, but relates my concern primarily to air-sealing.....and I would agree with him about that. But my concerns have to do more with water penetration than air. While I don't think liquid water moving through the WRB at fastener penetrations would be significant, I would assume that even small amounts of water would find its way into the furring strips or sheathing around the penetration, and that small amount would be absorbed (or is it adsorbed?) by the surrounding wood. And over time, the wood would eventually deteriorate and loose its holding power. a self-sealing WRB would resolve this. perhaps not as effectively as a tape, but good enuf.
Hugh, I agree with Malcolm that in most cases it shouldn't be something to worry about. If you use a rain screen, good cladding details and materials that can handle a tiny amount of wetting, as long as the rate of drying exceeds the rate of wetting then the building will be fine. I'm not aware of any conventional WRBs that claim to be self-sealing at penetrations. If you are concerned, I would use Henry Blueskin VP100, Pro Clima Adhero or a fluid-applied product.
I recently worked on a project where fastener penetrations caused the total failure of the cladding system and structural failure of the wall system.
This was somewhat of a special case, of course b/c this sort of thing doesn't happen that frequently. In this case, it was a thick wall system with "innie" windows. The rough window sill stepped down towards the exterior in several steps, and a self-adhesive membrane ("self-healing") was used to cover the rough jamb and sill. So far, so good. However, the sill detail included a piece of 2x wood blocking that had to be fastened through the sill membrane to support a decorative stone sill. The blocking was fastened using 12d hot-dipped galvanized nails because of the length needed to reach the structural framing. The house is located on a river with significant rain and wind, and light salt exposure (about 2 miles from the ocean).
This system worked just fine for 5 years. In years 6-8, there were occasional leaks from the heads of first floor windows, with two leakage events large enough to damage the floors inside. In year 9, there were two leakage events in relatively quick succession, and I was called in to investigate.
We eventually found that water had been pooling in the wrinkles of the membrane on the sills and also that water had been dammed by the wood blocking despite efforts to allow drainage. Over time, the nails securing the blocking had rusted, with many of them rusting away completely. While the membrane is considered "self-healing," it was unable to "heal" the holes left by the corroded fasteners, and water had been seeping through these unprotected holes for years. The water had rotted the wood subsills and eventually entered the walls, causing structural damage to studs and headers. It was really a mess. Total rebuild of the wall system on one side of the house.
FWIW, it is also well-known that Tyvek leaks like a sieve at staple and other fastener holes. If the other cladding details cause any damming of water flowing down the WRB, it will go through the holes eventually. This is one reason why air gaps, rainscreens, and drainage are so important. The fastener penetrations behind the battens are not so important if the water can't dwell in the system long enough to cause problems. If you only tack down the WRB over the studs and use the battens to secure the WRB, you can minimize penetrations in the field of the system.
And pay attention to horizontal features!
Peter,
Ouch! I think many of the new wall systems, especially those with thick exterior foam, end up relying 0n details that are too complicated to be reliable. The wall you describe sounds like something you could have predicted would fail at some point.
In contrast, probably the most resilient wall we have come up with is one with a rain-screen over a WRB on sheathing. Because the cavity takes the heavy lifting off the WRB, It can survive a fair amount of poor installation without suffering damage.
That said, if you follow Tyvek's installation instructions and use cap-nails not staples, the WRB shouldn't leak.
Malcolm, couldn't agree more...I'm old school, plywood sheathing on studs without exterior insulation although that's heresy around these parts. If elimination of thermal bridging is absolutely required, then a double stud wall or sheathing on top of exterior insulation.
That's all well and good, but in my area, you mention cap nails and people look at you like you've got three heads. They all know it's required, but nobody does it. "It makes the siding wavy." is the typical defense. Not a very good defense, but there we go.
Peter,
I've got to confess I hardly ever use them either. But I won't complain if the Tyvek leaks.
Hugh,
If it's moisture damage through the penetrations you are worried about, the first thing I'd suggest is using pressure-treated strips as the rain-screen battens. I would say though that we have been using regular plywood strips here in the wet PNW climate for well over a decade, and the walls we open up for renovations or repair show neither damage to these battens, or the underlying sheathing behind them where they are penetrated by fasteners. If it's more than a theoretical concern, it's sure taking a long time for the problem to become apparent.
As a general proposition I'd suggest the two conditions in which it makes sense to deviate from established construction practices are when that change would either markedly improve the performance, or correct a perceived problem. I'm not sure using self-healing membranes under fasteners fits into either category.
Malcolm, I'm interested in the fact that you use plywood strips. For a variety of detailing and alignment reasons, we would like to use 1/2" furring strips, 3-1/2" wide. The simplest and most economical way to do the would be to rip plywood strips...In another tread, several responders cautioned against it. The project is on Martha's Vineyard, Climate Zone 5, with occasional heavy rain and often damp conditions. What do you think? am I ok going ahead with 1/2" plywood strips? They would be directly over plywood sheathing and WRB and covered with shiplap wood siding nailed with stainless nails. Would using PT plywood be advisable or just CDX?
Hugh,
When rain-screen walls became mandatory in coastal BC about a decade ago, lumberyards began stocking 2" plywood strips, and that's what is almost universally used here in combination with perforated metal J trim at the base. I've never heard of problems with de-lamination, which typically occurs on plywood used as subfloors and exposed to the elements for a prolonged period during construction. The advantage they have over solid stock is both price, and that they don't split when fasteners are shot through them. The downside is they are wavier if applied over exterior insulation like mineral wool.
Here the strips are available in both Pt and CDX stock. I haven't noticed any difference - and long before they would rot out your siding will have failed - but for peace of mind you may want to use Pt.
thanks Malcolm.....I'm probably overthinking things, as usual.
Hugh,
Way better to overthink than the alternative.
Perhaps I'm overthink again, but I've come up with something else that's bothering me regarding detailing of windows. We're going to be using Loewen windows for a variety of windows and would like to use them without casings due to the modern nature of the project. A Loewen rep in showing me windows boasted about how waterproof the window is when properly installed with a WRB because of it's integral nailing flanges. That's a well and good and what we want for a rain screen installation. But the window sill (see attachment) has no drip flange...probably meaning that a lot of water coming down the face of the window will go directly back to the WRB under the sill. My philosophy is that most water should be directed out and off as far out as possible. Problem? Solution?
Hugh,
I agree that all windows should (ideally) be designed and manufactured with a projecting sill. (Traditionally, this sill dripped water beyond the plane of the siding.) But these days, windows are sometimes installed as "innies" or "inbetweenies" -- making the design of the sill less critical than the design of the flashing under the window.
In no case should a designer or builder be depending on the drip line of the sill to keep rain on the exterior side of the WRB. That's the role of flashing.
Before your window is installed, the rough opening needs to be flashed. The first step in this process is to install a sill pan that directs water beyond the plane of the WRB. Without that sill pan (which needs to be sloped or needs to include an interior dam), the window opening won't be dry. Once the sill pan is installed (along with the jamb flashing and head flashing), the design of the window sill is relatively unimportant. That said, if you are installing your windows as innies or in-betweenies, you'll need durable flashing to cover the sill pan. This durable flashing would, of course, extend under the window.
Thanks Martin....I'm with you on all flashing and sill pan, but it still kind of bugs me to let water in places where it could possibly be kept out. We still think it's good practice, don't we, to have at least a bit of a roof overhang at the top of wall with a drip edge?
I am building a house in Virginia with a 3/4" ventilated rainscreen created by 1x4s installed vertically over 1" of rigid insulation. On top of the vertical furring strips I will run horizontal 2x4s as nailers for vertical white oak board and batten siding. I am planning to vent the top of the rainscreen into the soffit, which connects to a 1 1/2" ventilation channel between the rafters of a 6/12 pitch cathedral ceiling. (The ceiling will be insulated with open cell foam which I am choosing to ventilate for a bit more peace of mind.) So, there will be a continuous ventilation gap running from the bottom of the wall the whole way to the ridge vent.
I'm wondering about eliminating the soffit vent, so that all the air that exits the ridge vent would have to be drawn up behind the siding, rather than coming through the soffit vent. My thinking is that the stack effect of coupling the rainscreen with the ventilated cathedral ceiling will encourage more air to flow behind the wood siding and dry it out more quickly. This also eliminates the extra blocking and detailing necessary to install a continuous soffit vent. Are there any pitfalls I'm missing in this approach?
Timothy,
I think it is a good idea. The only places I wouldn't do it are wildfire prone areas and where it may be prohibited by code.
You need to ensure though that the two vents are sized appropriately. The ratio under most codes is 1:300 in total, and it is good practice to have at least 50% of that at the bottom so as to not to depressurize the roof cavity. I'm not sure a 3/4" cavity will supply that.
Malcolm,
Thanks for your feedback and for the reminder of that ratio. I'll have 15 vent channels 3/4" deep x 20" wide, which gives me about 225 square inches of ventilation at the bottom of the 600 square foot cathedral ceiling. The 1/300 ratio would require 144 square inches at the top and 144 square inches at the bottom, so in theory this should be okay. Even if it would be a little under what is required, I don't feel too concerned since I understand that it's debatable whether it's necessary to vent a roof with open cell foam.
Timothy,
Good luck with your build!
This is a great article with a lot of useful information that I hope to use. I am planning to replace the lap siding on my home, which is installed on .75"x2.5" vertical furring strips. Whoever installed it left no vents at the bottom or top (i.e. "closed cavity"). I also discovered there is no WRB over the sheathing, which doesn't appear to be OSB. I'm not sure what it is, but perhaps it allowed the WRB to be omitted. Regardless, I would like to convert this to a rainscreen with WRB. The new siding will have a flush profile (not lap) that is only 5/16" thick. I also plan to replace windows which are in bad shape. So with this in mind, my plan is to:
1. Fill in between the furring strips with .75" polyiso foam board to add a little R-value to the walls.
2. Remove windows and add a WRB, cutting and taping it into window rough openings.
3. Install and flash the new windows
4. Add 3/8" x 3" furring strips
5. Install new flush siding (which is installed with clips).
Most of this seems pretty straightforward, but I do have a few questions I was hoping to get some feedback on:
1. Should I just remove the old furring strips before installing the polyiso foam boards? That would save having to cut the foam to fit between the old furring strips, but then the new furring strips would be installed on top of foam board. My installer is worried about the foam getting crushed during installation. From what I've read, that doesn't appear to be problem.
2. I have one archtop window, and despite a lot of searching I have not come across any information that discusses installing an archtop window in rainscreen system. The new window will have a factory applied brickmold with a flange, so my thought is to install it the same as the old one but flashed into the WRB. Then install new furring strips on top of the flange, install the siding around the brickmold with a compressible foam strip and/or caulk in the gap to any stop water intrusion. Any thoughts on this approach?
Thanks for any feedback on this. I appreciate.
Patrick,
Remember that you need to flash the window rough opening before the window is installed -- not after. (Your description makes it sound as if you think flashing comes after window installation. It doesn't.)
Q. "Should I just remove the old furring strips before installing the polyiso foam boards?"
A. Yes. Continuous rigid foam is much better than rigid foam cut into narrow strips.
Q. "I have one archtop window, and despite a lot of searching I have not come across any information that discusses installing an archtop window in rainscreen system."
A. Several manufacturers make flashing for arch-top windows. Here is one product to consider: HeadFlash-Flex 1-3/8 in. x 60 in. Window Flashing.
Martin, thanks so much for the quick response. Yes, I was aware that the RO needs to be flashed before installing the windows. I was trying to provide some basic background while not making the post too long (which wasn't too successful ;^).
I have one question about the furring strips. Can those be nailed on (given how thin the foam is) or should I plan to use screws? Nails would be a little easier, but I don't want to compromise the holding strength.
Thanks for the link to HeadFlash-Flex. If the brickmold flange is properly taped, that should keep water from getting behind the window. But it never hurts to have extra layers of protection, so I'll probably add it if it fits (the window is 60 inches wide).
Patrick,
Q. "I have one question about the furring strips. Can those be nailed on (given how thin the foam is) or should I plan to use screws?"
A. If you are nailing the siding to the studs, then the manner of fastening the furring strips isn't very important. You can use any convenient technique you want to hold up the furring strips -- they just need to stay in place long enough to remain fixed until the siding goes up. (The siding nails will hold the furring strips in place.)
If you aren't nailing the siding to the studs -- but instead are planning to nail the siding to the furring strips -- then the attachment of the furring strips is crucial, and you can't be casual about it. For more information, see "Fastening Furring Strips to a Foam-Sheathed Wall."
I have another question related to rainscreens. According to Hardie's installation guide, you can nail HardiPlank (fibercement) directly against the WRB (i.e no air gap required). Does that mean rainscreens are only needed if you are using rot susceptible siding?
Patrick,
The aim of including a rain-screen is to make the wall perform better, not just prolong the life of the siding. Rain-screens help walls with claddings like cement, metal or composites too.
From the article:
"The gap provides a capillary break between the back of the siding and the WRB. This limits wicking.
The gap allows moisture held in the siding and sheathing to be redistributed to adjacent materials, by evaporation and diffusion, thereby limiting damage due to water that concentrates at leak points.
The gap provides a path for liquid water to drain down to the weep holes at the bottom of the wall.
If there are ventilation openings at the top of the gap, the rainscreen provides a path for moving ventilation air. This ventilation air rises due to the stack effect, which is strongest when sun shines on the wall. Research shows that this type of ventilation is a powerful drying mechanism."
Thanks Malcolm. So are people who follow the manufacturers installation guidelines and nail the siding directly to the WRB risking damage to their sheathing/framing?
My interest in this is that I've decided to change my siding to Boral Truexterior, which is a very moisture resistant siding (it can actually be used below grade). So I was wondering if the furring strips were still needed. Because I plan to add a .75" layer of rigid foam, it would simplify things (from a retrofit standpoint) if I could omit them. But maybe the better solution is to use thinner furring strips (1/4") or a mesh. Definitely a lot to think about.
Patrick,
No I don't think in most climates, with most common building assemblies, not using a rain-screen is risky. It definitely improves a wall's performance, and makes the consequences of error or changes over time much less severe, but it's not usually an essential part of most walls.
My understanding of what is necessary here in the PNW doesn't always translate into what works in other climates. Unfortunately I don't know whether your proposed wall is sufficient for where you are without some cavity behind the siding. Hopefully other posters will chime in.
I'm trying to come up with my wall details and am curious about Hardie siding over ICF. I know of a project that has been this way for 15 years with no rainscreen and no apparent damage, but that doesn't mean it was the best method. I was wondering the communities view on rainscreens with ICF were in a warm humid climate? It seems that firring out on top of the ICF would be a waste, but might be an opportunity for some of the dimpled products?
Thanks everyone for this great discussion! We are going to be building a small house on the coast of Maine (zone 6A) and are considering 3" mineral wool continuous external insulation over sheathing/WRB (maybe ZIP). I understand that the mineral wool (comfortboard 80) needs to be adhered to the siding with furring strips, typically installed vertically, creating a ventilated rainscreen for free. We are planning on having vertical siding like board and batten. I think it would be conventional to run an additional layer of furring strips horizontally to accommodate the vertical siding. I'm considering ways to avoid the use of a second layer of furring strips.
Instead of using two-layer furring I was thinking about using a single layer of furring strips run horizontally to allow installation of the vertical siding directly. My question is: Will the mineral wool provide an acceptable means of vertical air flow, and possibly water flow, from the top to the bottom of the wall to provide sufficient drying? With foam insulation I'm sure this would not be a great idea, but mineral wool is both air and water permeable. Any thoughts?
Log in or become a member to post a comment.
Sign up Log in