Addressing the ping pong issue

Zone 4A. Hip roof necessitates unventilated attic, therefore spray foam insulation against the bottom of the roof deck.
Joe Lstiburek is saying that the source of humidity in this kind of assembly is from the interior, and he describes a “ping pong effect” that results in moisture accumulating at the ridge. His solution is to use closed cell foam or condition the attic (below Climate Zone 5).
Would it not work to spray a layer of cc foam against the sheathing, followed by open cell foam to make up the required insulation value?
If yes, what thickness would suffice? Since the purpose would not be to keep the sheathing warm, but to simply create a vapor barrier, would 1 1/2” not be enough?
Thanks very much.
GBA Detail Library
A collection of one thousand construction details organized by climate and house part
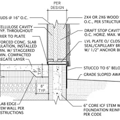
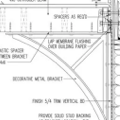
Replies
The roof deck is protected by as little as 1" of ccSPF, but that alone doesn't stop; the ping-pong effect, since moisture can still accumulate at the cool edge of the ocSPF
If using a combination of ccSPF + ocSPF, in zone 4A making the ccSPF 30% or more of the total R keeps moisture from accumulating at the oc/cc foam boundary, since it's temperature average will be higher than the indoor air's dew point.
David,
As a guideline, I suggest that you use the percentage recommendations in the second table found in this article: Combining Exterior Rigid Foam With Fluffy Insulation.
While the ratios in that article were developed for assemblies that include exterior rigid foam and interior air-permeable insulation, the same ratios apply when considering a combination of closed-cell spray foam and open-cell spray foam.
David,
Here is a link to an article with more information on these problems: High Humidity in Unvented Conditioned Attics.
Martin, "High Humidity in Unvented Conditioned Attics" is one of your best articles, and an example of why I subscribe.
This article supports my suggestion that a thin layer of ccSF would suffice; see for example your response in no. 16: "If the roof sheathing is protected on the interior by a layer of vapor-impermeable cut-and-cobble foam, then the moisture in the attic air is decoupled from the roof sheathing. The rigid foam prevents the migration of moisture from the attic air to the cold roof sheathing.
That's why (according to Lstiburek and Ueno) this phenomenon isn't observed in attics insulated with closed-cell spray foam or the cut-and-cobble approach."
A layer of ccSF takes the place of the cut and cobble in my case.
Dana, the sheathing is described as the culprit that absorbs and holds onto moisture, thereby allowing it to accumulate over time. As I understand the literature, it is this accumulation that creates the problem. Otherwise, the cut and cobble approach would not be so effective.
David,
My recommendation is more conservative than yours. You may well be right that 1.5 inch of closed-cell spray foam will result in an attic without humidity problems.
You may also be wrong.
As my article made clear (I hope), building scientists don't yet agree on the mechanisms responsible for these humid attics.
The danger of using closed-cell spray foam that is thinner than the recommendations in "Combining Exterior Rigid Foam With Fluffy Insulation" is that moisture will accumulate in the open-cell spray foam (because the interior side of the closed-cell spray foam is cold enough in winter to become a condensing surface).
Assuming your Mechanicals will be in this attic space wouldn't it be cheaper to just use ocSPF and add a small return/supply duct?
"Dana, the sheathing is described as the culprit that absorbs and holds onto moisture, thereby allowing it to accumulate over time. As I understand the literature, it is this accumulation that creates the problem. Otherwise, the cut and cobble approach would not be so effective."
A few concepts to clear up:
The sheathing only accumulates moisture if it's cold enough long enough, relative to the dew point of the attic air. But anything that's cold enough long enough will accumulate moisture given a sufficiently high permeance path. The vapor permeance of even fairly high moisture content OSB is still 5 perms, which is permeable to contribute some to the rapid daily swings, but only when it has a very high moisture content. Being fairly vapor permeable, open cell foam can also accumulate moisture when it's cold enough. It takes about a foot of foam to hit 5 perms, and 5 perms isn't sufficiently vapor tight to limit wintertime moisture accumulations in the foam itself. The cooler exterior couple of inches can store quite a bit more moisture than" OSB, and through less than a foot of open cell foam it can both take on & purge that moisture far faster than OSB. The daily ping pong problem is moisture cycling into and out of the colder (at night) side of the open cell foam layer, once it has taken up a seasonal load over the winter. The smaller amount of moisture entering & leaving the roof deck itself is secondary relative to this phenomenon.
High moisture content of the OSB is still a concern with or without the humidity ping pong, since it's structural and can develop rot if it's damp enough long enough. High moisture content of the foam isn't a problem- it's function is only compromised when wet, it doesn't rot, and it dries more rapidly than OSB (if given a chance.)
The cut'n'cobble method is effective at what? In practice cut'n'cobbled rigid foam doesn't work very well at all on roof decks. Even if the air seal is perfect on the day it's installed, it won't stay air tight forever, and ends up creating a moisture trap between the rigid foam and the low-permeance roofing materials above. Closed cell foam sprayed directly on the roof deck has much better long term air sealing integrity.
If sealed perfectly it can protect the roof deck from excessive moisture accumulation, but if used in conjunction with a higher permeance insulation on the interior moisture will accumulate on the cool side of the fiber insulation. That is, unless the foam-R is high enough that it's interior surface temperature averages above the attic air's dew point. It takes the same R-ratio independent of which side of the roof deck the foam resides. When the rigid foam on the interior side (and sealed perfectly) it's lower vapor permeance can protect the roof deck, but not the higher permeance insulation from retaining moisture. The ratio is still important.
There's another BSI-088 paper that discusses vapor diffusion vents. Figure 7 therein shows an example of a vapor diffusion vent for a hip roof. That paper may give you additional food for thought.
Wouldn't the relative humidity be higher at the ridge than it would be in any walls? That would mean a higher dew point, and thus imply a different permeable to impermeable insulation ratio.
I don't know what the numbers would be, but my paranoia says be a LOT more conservative than with the walls. Either that, or use open cell with a vapor diffusion vent just for the ridge. Sounds wrong, but that's the limits of my current understanding. So my questions are:
- Are the guidelines for the ratio in the walls really anywhere close to being sufficient for the ridge?
- Does it make any sense to just have the ridge be vapor permeable with a ridge diffusion vent?
I've spent a lot of time digging into roofs, and I'm still confused.
I will point out that looking back at BS-016, as referenced above, it does say that:
"The key to this is the storage capability of the wood based roof sheathing."
That would imply that my concerns are just paranoia. On the other hand, other materials have some moisture storage capability and from BA01409, it mentions:
"The ccSPF roof assemblies worked well under most conditions; the cases that were at risk of failure were high interior RH (50%) in colder climates. Note these risks are seen for worst-case orientation; at a south orientation, these assemblies have no risk."
Considering things like thermal bridging through rafters, etc., it seems that, while better than others, it's not necessarily bulletproof. Additional steps like air-exchanges in the attic or perhaps a vapor diffusion vent at the ridge seem like they would be necessary to address any remaining risk.
I've never found anyone even mention the idea of combining a vapor diffusion vent at the ridge with any mix of closed-cell for the rest of the roof. That does lead me to believe that perhaps the idea is utterly ridiculous. :-)
Christopher,
While a fair amount of certainty has been expressed in many comments on this thread, I'd like to remind readers that many building scientists still express uncertainty about the mechanisms causing high indoor humidity in attics insulated with open-cell spray foam.
Q. "Are the guidelines for the ratio in the walls really anywhere close to being sufficient for the ridge?"
A. No, which is why GBA (and most building scientists) advise builders to use different ratios of vapor-impermeable foam to vapor-permeable insulation for roofs than for walls. All of the GBA articles on this topic emphasize that you need a higher percentage of your R-value in the form of vapor-impermeable foam for a roof than for a wall.
The ping pong humidity problem is different from the roof deck failure risk issue. A skinny inch of closed cell foam can substantially mitigate risk to the roof deck, but doesn't necessarily fix high attic humidity if an adjacent open cell layer is substantially more than would be allowed under IRC chapter 7 prescriptive ratios.
The average wintertime temperature of roofs (particularly north facing pitches) is substantially cooler than walls, due to nighttime radiation cooling toward the sky into clear dry air. Wall surface temps hew pretty close to the outdoor air temperatures at night, whereas on clear nights roof surface temps can drop to the outdoor air's dew point temperature. It's that cooler average roof temperature than demands a heftier R to keep the roof deck (or first condensing surface) temp above the indoor dew point temperature enough hours to keep it from taking on excessive moisture.
Q1: Please help me understand the distinction between vapor and moisture. In the posts above, several seem to be suggesting that permeability equates to being a sponge, i.e. a wet surface that continually contributes moisture back into the attic. What is the % moisture content possible?
Q2: Can the moisture vapor held within ocSF really condense? By definition that means becomes liquid water, which SF cannot hold. In my ignorance, this seems a contradiction. And if it condenses, does it then drip?
David,
Q. "Please help me understand the distinction between vapor and moisture."
A. Moisture is the more general term. Moisture is not a scientific term, but in common usage it can refer to liquid water (usually droplets or a thin puddle) or water vapor.
Vapor is specific. It refers to an element or compound in the gaseous state. In this case, we are talking about water vapor.
Q. "Several commenters seem to be suggesting that permeability equates to being a sponge."
A. Permeability (water vapor permeability) is defined as the rate of water vapor diffusion through a sheet of any thickness of material. Water vapor permeability is a property of a material and is independent of thickness. It is measured in units of ng/Pa•s•m. If a material is has a high vapor permeability, it can be defined as sponge-like. Materials can also have a low permeability.
Q. "...a wet surface that continually contributes moisture back into the attic. What is the % moisture content possible?"
A. Wood moisture contents below 20% are fairly common. When wood moisture content exceeds 30%, rot is likely (if temperatures are warm enough). Moisture contents for wood between 20% and 30% are cause for concern, especially if they last for a while.
Q. "Can the moisture vapor held within ocSF really condense? By definition that means becomes liquid water, which SF cannot hold. In my ignorance, this seems a contradiction. And if it condenses, does it then drip?"
A. Yes, it can condense. And if it condenses, it can drip.
> Hip roof necessitates unventilated attic
I'd re-examine this assumption. Ventilation allows less heat loss/gain for less $.
Jon,
A hip roof can be ventilated, if, at the time of new construction, the builder is willing to install two layers of 2x4 purlins (cross-hatched 2x4s, installed at 90 degrees to each other) between the tops of the rafters and the sheathing.
There seems to be lots of successful exceptions to that, including the one above me. Using hip vents, shingle vents, static vents, etc.
As Lstiburek writes: "Where the air leaves isn’t as important — whether it’s a ridge vent, or mushroom caps, or gables".
But if vented hip roof failures occur with well sealed/insulated attic floors and code compliant venting, I'd like to read more about it.