Addressing Top Plates for Deep Energy Retrofit
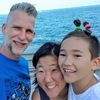
Is there a way to address the thermal bridge around the top plates – roof truss connection on a deep energy retrofit without having to insulate over the top of the roof with layers of rigid foam (trying to avoid the cost and complexity)?
I know this is a topic that’s been addressed a few times here on GBA. I’m assuming it’s still pretty common for those trying to retrofit existing homes.
https://www.greenbuildingadvisor.com/question/insulating-top-plate
https://www.greenbuildingadvisor.com/article/insulating-tight-spaces-eaves#0
https://www.greenbuildingadvisor.com/article/one-mans-quest-for-energy-independence-part-4
In a PH Accelerator episode (17 minutes):
https://youtu.be/jlCQ15_NyN4?t=1031
Just wondering if anyone’s come up with a solid alternative solution?
Since the existing roof needs to be replaced, I was wondering about the following as an option (see attached diagram):
Repair existing roof sheathing as necessary.
Add roof underlayment.
Add 2×4’s through sheathing and into existing roof trusses. This extends out the existing overhangs, which are shallow (8-9”), and serves as a nailing base for a second ½” layer of roof sheathing.
Add second layer of roof sheathing.
Apply roof underlayment.
Put down shingles.
The point of all this would be to take advantage of the full height between the top plates and the existing roof sheathing. We think there’s about 4”, give or take, in this space. Not having to maintain an air gap in this space to ventilate the roof will give us an additional 1.5” of insulation.
We will maintain an air gap for ventilation by adding the 2×4’s and then a second layer of sheathing. With new soffits (continuous vents), ample air flow from new soffits up the roof to the ridge vent between the 2×4’s.
With spray foam over the top plates, this should be about R-20 to R-25 (?).
The rest of the attic would be blown-in cellulose (R-60 to R-80).
In this article:
https://www.greenbuildingadvisor.com/article/lstibureks-rules-for-venting-roofs#0
Joe suggests matching the R-value over the top plates with the R-value of the existing wall. Is this still the correct goal to shoot for?
Paul and Jesper seem happy with their solutions. Any chance the potential risk for moisture/mold/rot in this area around the top plates is overstated as long as the air sealing in this area is perfect?
Welcome any feedback.
Thanks!
GBA Detail Library
A collection of one thousand construction details organized by climate and house part
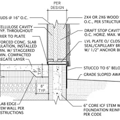
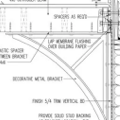
Replies
If you're using some type of loose fill insulation here (which is usually the best option for attic floors), just put in some vent baffles and then bury the entire connection between top plate and truss. You'll end up with at least R12-16 or so, which is enough to address any thermal bridging, and it's much less work than anything else that could be done!
On the exterior, if you do a reside, put on some exterior rigid foam and extend it up past the top plate all the way to the bottom of the vent channel. This makes a thermally insulating insulation dam for your loose fill insulation (which means you really want to do the exterior insulation before the attic insulation), and the end result is your top plate will be completely insulated on all exterior faces.
Bill
Bill,
Yes, once the top plates were spray foamed, the remainder of the attic would be blown-in cellulose.
"...much less work than anything else" is what has us exploring this option.
"put on some exterior rigid foam and extend it up past the top plate all the way to the bottom of the vent channel. This makes a thermally insulating insulation dam for your loose fill insulation (which means you really want to do the exterior insulation before the attic insulation)"... this is how I was picturing things proceeding as well. Thank you.
Based on everything I've read so far, Passive House folks argue this area around the top plates will fail with this proposed set-up (using WUFI or THERM anaylsis), leading to moisture problems, or even significant rot.
Comments from Martin and Bill Rose in the linked articles also suggest it may be a problem.
The links to Paul's project, along with Jesper's, had me hopeful that a solution is possible that could avoid layers of rigid foam on the roof (with the complexity and cost associated with it).
My thinking was: close off the existing ventilation channel under the roof sheathing to gain another 1.5" of R-value in this vulnerable spot, and then add a new ventilation channel above the existing roof sheathing with 2x4's and a second layer of roof sheathing.
The 2x4's/2nd layer of sheathing doesn't seem onerous mainly because the overhangs need to be extended anyway. Even better if they could help us avoid layers of rigid foam on the roof.
Eric,
I don't know what the house looks like so this might not work architecturally, but have you thought of converting the existing gable roof to a dual-pitched (or Bonnet) roof?
Creating a lower shallower sloped roof on say the bottom six feet would allow you to extend the overhangs, increase the space over the exterior walls, and limit the amount of over-framing you would need to do.
Having seen what happened when you applied yourself to new construction, I'm interested to see what you come up with on a reno.
Most of the house is a basic gable roof structure. I hadn't thought of altering the roof structure with something like the Bonnet-style roof. I can see how that could work. Unfortunately, I don't think the homeowners in this case will appreciate the aesthetics of it.
It looks like we either get comfortable enough with burying the top plates-truss connection in spray foam to pursue it (and hope for the best), or else just go with layers of rigid foam on the roof.
If someone could establish the long-term durability of burying the top plates-roof truss connection in foam (combined with an airtight ceiling of course), it seems like it would make deep energy retrofits both more straightforward and cost-effective.
Thanks, Malcolm!
Eric,
I will admit to never running a wufi analysis on anything, so this is just sticking my thumb in the air. But, if you've got 4" of rigid insulation on the exterior that runs up to the underside of your existing sheathing baffles, and 4" or so of cellulose on top of the plates, then the plates are completely inside the thermal envelope. Even the outer edge of the plates is inside 3/4 of the insulation. I can't imagine that there would be any risk of condensation on the plates. No spray foam necessary, as the exterior rigid would act as a dam for the fluffy. I would check that space again. You might find that it's far taller than 4" and then your risk goes down even further. I think I'd skip SPF in that corner if you can achieve good air sealing from the interior. Stuff in attics dries out fast in warmer weather if it can, and the air flow over top of cellulose is going to wick away a lot of moisture if there's any there in the first place.
Thanks for the comment, Peter.
It's funny that you mention using cellulose over the top plates instead of SPF.
One thought I had was filling the area over the top plates with cellulose as you suggest. Prior to adding the cellulose, I was thinking of applying a liquid membrane (e.g., Prosoco, Visconn) to the top plates and the first couple of inches of the roof trusses with an airless sprayer in order to prevent damage from seasonal moisture accumulation.
Since we're doing quite a bit of work out at the eaves anyway, maybe it's worth the effort, even if we have to remove the first row of roof sheathing to get enough access for spraying properly (?). We're talking about roughly 80-100 linear feet on the north and south sides of the house.
Still easier than covering the roof with multiple layers of foam and detailing it properly, I'm thinking.
If moisture were to accumulate in this area, it can't damage the top plates/roof trusses, and hopefully the cellulose can absorb and then slowly release it (as long as the moisture doesn't linger), as you suggest. Presumably it could safely do this year after year.
The logic would be similar to a masonry retrofit where they apply a liquid membrane to the interior side of brick/masonry and then can safely use fluffy insulation in the wood framed wall cavity.
Maybe, like the logic with double stud wall cavities, the liquid membrane is overkill and the cellulose is capable of handling the excess moisture all on its own?
https://youtu.be/WM9fywMTrl0
>"The logic would be similar to a masonry retrofit where they apply a liquid membrane to the interior side of brick/masonry and then can safely use fluffy insulation in the wood framed wall cavity."
That's not actually true -- a liquid sealant applied to masonry does not prevent condensation when using fluffy insulation. Condensation will occur whenever the surface of the masonry wall is below the dew point of the interior air, any waterproofing layer applied to the block, liquid or otherwise, won't change anything here. You'd still need rigid foam against the block since the rigid foam doesn't allow the transport of moisture (or at least it allows very much less than batts).
I don't see a liquid barrier applied to a top plate helping much either. If you have enough water accumulating there to be an issue, it will just run off of the sealed top plate and go somewhere else. As long as you have a vented attic, you shouldn't have moisture issues at the top plate since the ventilation will carry it away before there is a problem. If you're really worried here, and this is new construction, consider using a treated top plate the way you'd normally used a treated sill on top of a masonry wall.
Bill