Air & WRB options – cost vs. effectiveness?

I am a hands-on homeowner who is finishing up the design of our new house to be built in central NC (zone 4a) and I am trying to sort out the “best” way to handle the WRB and air barrier. I will be providing some support for the construction of this house in various areas so sweat equity is available, but I don’t want to spend time or money on redundancy unless there is a chance of failure that the redundancy would help to address.
I plan to use fiber cement siding, traditional framing with fiber insulation and far as I can tell, I have 4-options for the drainable WRB / sheathing / air barrier:
1) OSB + Benjamin Obdyke Hydrogap WRB (taped) + sealant / foam on the inside cavity of the OSB. Can I rely on just the interior wall cavity foam / sealant in the absence of OSB tape?
2) OSB with primed and taped seams + Benjamin Obdyke Hydrogap WRB + sealant / foam on the inside cavity of the OSB. This seems like it would be labor intensive to prime and tape the seams and since that has to happen before the WRB goes on, it could leave the OSB exposed for too long but how long is too long to have bare OSB on a wall before it gets wrapped? Is there still value in sealing the interior OSB cavity with taped OSB seams?
3) OSB + a peel and stick WRB like Benjamin Obdyke Hydrogap SA + sealant / foam on the inside cavity of the OSB. This seems like it could be efficient as the tape and WRB are combined into one step but its success seems highly dependent on 100% adhesion so that it doesn’t peel or delam which in an extreme case could introduce bulk water between it and the OSB; is this a valid concern?
4) Zip Sheathing (taped) + Benjamin Obdyke Hydrogap WRB + sealant / foam on the inside cavity of the OSB. This would likely install faster than my first two options since no primer is needed to tape zip sheathing but would the lack of primer and its associated material and labor costs offset the higher cost of this material?
In any of the situations with taped or wrapped seams is the interior sealant still adding value?
Thank you for any insight you may be able to provide!
GBA Detail Library
A collection of one thousand construction details organized by climate and house part
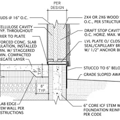
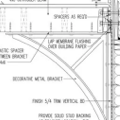
Replies
The products are important but more importantly is "red lining" the drawings the ensure the air control layer is continuous and constructable in plan and section around the entire house. Keep the details as simple as possible. Using the outside of the sheathing layer as the primary air control layer and using the interior vapour control layer as a secondary air control layer is an increasingly common option.
Make sure the materials are all compatible and are tested to maintain their air tightness for 50-100+ years. SIGA, Pro-clima and Rothoblass products have this track record. I have no experience with Benjamin Obdyke or Zip products.
I would suggest taking some Passive House training, so you can answer these and others questions yourself and be more hands-on with the build. There are lots of on line training options.
When you add Benjamin Obdyke Hydrogap WRB you immediately double or triple the cost of the details. It's a great product, don't get me wrong. However, those plastic dimples aren't made of gold, and I think you could do as well with a different, cheaper product.
I'd like to propose a 5th option based on cost, constructability, DIYness, availability, and energy optimization in your climate zone.
from inside to outside:
1. 1/2" drywall ( $.50)
2. 2x6 16" OC ( $0.15)
3. R21 fiberglass batts ($0.90)
4. 7/16" OSB with taped seams (3M 8067 or Zip tape works fine) ($0.75)
5. Tyvek commercial D drain wrap ($0.40)
That comes out to roughly $3.00 / square ft after tax. The BO SA is nearly half that by itself. Skip the foam, you can do a good job on fiberglass yourself at a fraction of the cost, and have as good of a thermal layer, if not better depending on the foam installer. Regular taped OSB is fine, and commercial D meets the drainage requirements in the fiber cement docs (95% drainage efficiency). Its easily available and is time tested.
I believe I mentioned this in a similar thread (same OP?), but this is the route I went on my in-progress house...well, other than I'm doing 5/8" drywall and the non-commercial version of DrainWrap.
It’s a very hard assembly to beat for the money! I was just about to state the 5/8 everywhere, but the whole trims wasn’t going to add much on my posts context.
Did you do any of it your self?
Well, it's still in progress (framed and roof is on, rough-ins ongoing). I wasn't intending to but did a bunch of the taping due to mistakes by the framers and the builder. In retrospect it would have been better to plan to do some of the work myself, but I expected it to go more smoothly than it has.
Regarding 5/8 drywall, I don't have competing quotes to compare, but if you're not DIY then labor cost is something to consider here -- it was made clear to me when specifying this that the labor costs would be up due to the extra weight/hassle.
I would 100% charge more for installing 5/8" drywall, ha.
Thanks! I am planning on 2x6 framing and fiberglass R21 insulation. My mention of foam was only for gap sealing not primary insulation.
Can you give me an idea on what details for the hydrogap drive up the cost vs tyvek?
Thx!
Bruno,
They’re essentially installed exactly the same way, it’s just that the hydro gap is so much more expensive. It’s a shame really, because that product could solve a lot of building science problems for many people.
I guess it’s the hydrogap SA that has special detailing to pay attention to? It seems that the regular hydrogap isn’t much more expensive than commercial D, so perhaps that’s the way to go since for the whole structure the cost difference is probably only a couple hundred dollars in materials?
Do you see any condensation risks on the interior side of the OSB with this wall configuration? Last night I read Joseph Lstiburek's book on Mixed-Humid Climates and it got me concerned about condensation within the wall cavity. thx
What specifically concerns you, Bruno?
I've not read that book, but assuming we're talking about Kyle's option 5 above the assembly should be able to dry in either direction. My understanding is a way to improve the assembly would be to add rigid insulation to the exterior of the sheathing, but the impression I've gotten from reading here is that isn't needed. From this article on exterior foam by Martin(https://www.greenbuildingadvisor.com/article/calculating-the-minimum-thickness-of-rigid-foam-sheathing):
"If you are building a house in one of the warmer climate zones — zone 1, 2, 3, or 4 (except for 4 Marine) — you don’t have to worry about the thickness of your foam. Any foam thickness will work, because your sheathing will never get cold enough for “condensation” (moisture accumulation) to be a problem."
Has the thinking on this changed since that article?
I don't know if anything has changed but in the Mixed-Humid Climate book, the example is given of an Atlanta home in the winter potentially having the interior side of the sheathing at or below the interior air dew point if it isnt clad with foam insulation. As an example, I am in central NC right now and it is 70F @ 50% humidity in the house and 43F outside...I have no idea what is going on in my wall but it could be that the interior side of the OSB is 50F or cooler which is the dewpoint.
The article makes the point that the thicker the wall, the more cavity insulation there will be and as a result, the colder the interior side of the sheathing will be which could lead to condensation. I really don't want to have to use foam sheathing but it seems like the only way to keep condensation out of the walls if the book tracks to reality in the field.
Luckily, the wall isn't all that thick, in comparison to those double stud walls. There's plenty of energy leaking through those studs to keep the sheathing a little warmer than you'd probably want.
Alternatively, as had been mentioned in the other thread you posted, you could install up to an inch of exterior insulation outward of the tyvek, and attach the hardie board directly through it, as they allow in their docs. That would essentially ensure the sheathing stayed warm and dry, and come out at about the same cost as the BO vs the Tyvek.
Frank's point about making sure the continuity of your air sealing is excellent and should be your first step. In answering your question, options 2-4 are all viable except you can omit any of the sealing and foam on the inside of the wall cavity except for penetrations through the sheathing and top and bottom plates. The outside face of your sheathing is your air barrier plane and if you use high quality acrylic tape and roll that tape (very important) on all the seams along with sealing any penetrations, you will end up with a nice and tight envelope.
Option 4 will be the fastest, but are you using the hydrogap WRB to create your rainscreen? You might want to price it out, but using wood furring strips instead of another layer of WRB could be more cost effective depending on material costs in your area. Though one of the better spec builders in my area (Pioneer Builders, frequent contributor to Fine Homebuilding and GBA) uses Zip sheathing on their builds and sometimes pair it with Hydrogap or Home Slicker for a rainscreen.
Option 2 is the cheapest, but if you use a high quality tape with an acrylic based adhesive like SIGA Wigluv or Proclima Tescon, you don't have to prime the seams of the OSB as long as they are clean, dust free, and you roll the tape. KlimaGuard Vario is a lower cost but still high performance exterior air sealing tape that can save you some money.
Here is Zip's document about the drainability of Zip sheathing by itself: https://www.huberwood.com/uploads/documents/technical/documents/Drainage-Efficiency-of-ZIP-System-Sheathing-Tech-Tip-Wall-ZIP-System_2021-01-25-220757.pdf
Unless I was using open joint cladding without a rain screen, I'm really not sure I'd bother with a drainable WRB, since they don't provide an opportunity for air circulation. Based on what you've described, I would install fiber cement directly on Zip sheathing (taped of course) and call it a day.