All exterior insulation – skip the interior drywall?

I’m designing a large workshop/storage building, single story, open rafters, approximately 1600 square feet. We plan to use rigid foam as our only insulation, both in the walls and roof, a mixture of PolyISO (to keep thickness down) and EPS (to keep the PolyISO warm). We’re in climate zone Marine 4, western Washington state. All the insulation will be outside the sheathing. It will be very close to the Persist method. The foundation will extend at least 16″ above grade (possibly 32″) and will consist of ICF blocks, which feature 2 5/8″ EPS foam on both sides of the concrete.
There are several questions we need to hash out with our local building department, as in my initial discussions with them, they don’t seem keen to approve this kind of construction at all. In fact, the official said he’d have to ask someone else if we could even use only exterior insulation. He seemed to think we ‘wouldn’t get credit for it’ – as if it wouldn’t count as part of the required wall R-value. ?!? Hopefully we’ll get together with them soon, but we’re not in a rush, and it’s a small county building department, so limited personnel and hours.
In any case, my question for now is this. Is there any reason, being that the air barrier and all insulation are outside the sheathing, that we need to install sheetrock over the entire interior wall? We plan to cover the lower 4′ of the wall with sheetrock and then tongue-and-groove cedar, both to protect the foundation wall foam, and provide a chase for all the electrical wiring, receptacles and switches. No electrical fixtures will be in the walls above this chase – all lighting will be in the ceilings.
I have seen plenty of examples of this being done, in garages, workshops, and even houses, so I know it can be done – somewhere. Just curious whether it’s a case of me not explaining it well enough to the building department, that it’s just so rare that they don’t see it as an acceptable construction method, or our state/county in particular has some specific reason to be against it. 🙂
Another issue brought up in my discussion with the county, is that we absolutely cannot use any recycled/reclaimed insulation (other than in an unheated/uninhabited structure, such a barn). Is that a common policy, or is our county/state just behind the times?
Cheers and Merry Christmas!
Aaron
GBA Detail Library
A collection of one thousand construction details organized by climate and house part
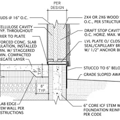
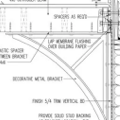
Replies
There was a similar question in Martin's Persist article:
https://www.greenbuildingadvisor.com/article/getting-insulation-out-of-your-walls-and-ceilings
Q. "We were wondering if the interior drywall and vapour barrier are needed."
A. Your exterior rigid foam is already a vapor retarder, so you don't need an additional one. It's up to your local building inspector to rule on whether you need interior drywall; in some jurisdictions, it may be required as a thermal barrier.
Aaron,
As Greg said, the only unknown is whether the sheathing will suffice as an ignition barrier. Here is a link to a project using the same method you are proposing:
https://architizer.com/projects/perfect-wall-house/
Greg,
I had seen that earlier question in the Persist article, but thanks for the reminder and quoting the relevant section so precisely. I guess I was hoping for more of an answer or justification than 'it depends', but no doubt there are various aspects of building where that's really the only logical answer. It's certainly likely that the cases where I've seen the interior drywall omitted, have less strict building codes and/or enforcement, than where I live.
If it's a fire code issue, than I am curious why an open rafter ceiling would be allowed, whereas an open stud wall would not. I can't seem to find a code reference that says interior of stud walls must be covered, but I may not be looking in the right place.
> I can't seem to find a code reference that says interior of stud walls must be covered
Look for code regarding foam thermal barriers. It may be OK with 3/4" wood sheathing.
Malcom,
Thanks for the excellent link! That's exactly the type of construction we're looking it, as you say. I'll take a look. If it's an ignition barrier question, that makes me wonder if it would suffice to put sheetrock between the studs, against the sheathing, leaving the studs exposed (and some vertical trim along the edges of the sheetrock)?
Obviously, this construction method we're proposing is a little (or a lot?) more work than just covering the studs completely with drywall, but it just seems a crime to me to waste all that potential wall space that could be used for built-in shelving, especially in a workshop.
Aaron,
I don't kn0w what qualifies as an ignition barrier under your code. The the sheathing may do, or if not it might make m0re sense than lining every stud bay with drywall, to add whatever you need on the outside of the sheathing.
Here is a video that goes into a bit more depth about the house I linked to:
https://www.youtube.com/watch?v=hTwq-qUnr9I
Hmm, well I found an article on thermal/ignition barriers right here on GBA. Love this site!:
https://www.greenbuildingadvisor.com/article/thermal-barriers-and-ignition-barriers-for-spray-foam
This would seem to be the most pertinent passage:
"The requirement calling for spray foam insulation (or, for that matter, rigid foam insulation) to be protected by a thermal barrier is found in Section R316.4 of the 2009 International Residential Code (IRC). The code refers to “foam plastic,” which is code-speak for “cured spray foam or rigid foam (including XPS, EPS, and polyiso).” In most cases where spray spray polyurethane foam is installed in a house, the foam must be separated from living spaces by a layer of 1/2-inch drywall or a material that has been approved as equivalent in fire resistance to 1/2-inch drywall."
It would seem the key is to determine what the inspectors will consider as an equivalent thermal barrier to the 1/2" drywall. We were planning 5/8" sheathing, but 3/4" would not be a major extra expense.
Malcolm,
Thanks for the video. I think I've seen it before, but hadn't looked too closely at the details. Interestingly, there isn't any sheetrock in those walls, just 1x6 pine, then 1/2" OSB sheathing. So, I would presume that the thickness of wood present in those walls, between living space the the foam, meets approval of the local AHJ as far as a thermal/ignition barrier. By the way, I'm a big fan of Matt Risinger's channel, watched many a video of his. :)
All this said, I still have a gut feeling that our building department/inspector didn't really understand our plan, even though I was as clear as I thought I could be. It seemed that he thought we were going to have exposed wiring and utilities in these open stud walls, which definitely would not be the case. Also really puzzling, his remark that we 'wouldn't get credit' for the insulation, if we used only rigid foam outside the sheathing. Is such a construction really that rare, these days? Maybe it is, in the small county where we'll be building? Anyway, we'll be sitting down with him within the next month or so, probably easier to discuss with some drawings, plans, face to face.
Answering my own question from the GBA article I linked, I see mention in the comments that 23/32" plywood is now an alternative accepted thermal barrier, now, due to a revision in 2015, sweet. Well, at least now we have the relevant code to reference.
You could potentially put drywall on the outside of the studs with the rigid foam over the drywall. This would probably be easier than cutting drywall to fit between the studs. If you use sheathing on the inside, I’d use plywood instead of OSB here. Plywood holds screws better which is a plus in a shop where you'll want to hang a lot of heavy stuff on the walls.
I don’t know why they wouldn’t like reclaimed insulation. I install used/refurbished equipment commercially all the time (there is an entire industry built around salvaged industrial equipment), and the only time I’ve ever had any arguments with the city is with some energy code stuff related to older electrical equipment — and I’ve been able to get around that stuff. My honest opinion is how would the city even know you used reclaimed insulation? If you have a few scuffs or broken corners, it was just “damaged a little during installation” right? How would they ever know otherwise? I’d fight them on this one.
Bill
Zephyr7,
I thought of putting sheetrock on the outside of the studs, but we also want sheathing on the outside - not the inside. Would a layer of drywall between the studs and the sheathing interfere with the required bracing/shear qualities of the sheathing? It would also mean 1/2" longer screws to attach the rain screen battens through the foam into the studs, which may are may not be a big deal, depending on how close we were to the limit (I think 8" screws was where we were at initially). Sometimes with those long screws, there's a huge jump in price going just 1" longer. :)
I'm in agreement with you on the reclaimed insulation, thanks for the encouragement. We're first time home builders, so there's a lot of stuff that's foreign and unknown to us, at this early stage. I had thought maybe there was an inspection during the build, where they come look at your insulation before you close up the walls, and look for some official rating/label on the insulation, but maybe not... Their initial reaction about reclaimed insulation was that it's 'all torn up', which doesn't fit what I've found, at all.
Yes, the extra fastener length through the drywall is going to affect shear load capacity of the wall. You’d need to check with an engineer to see if it would be enough to be a problem.
If your rigid insulation is over exterior wood sheathing, I don’t see that you’d need any additional fire barrier inside. Sheds are usually ok with exposed wood sheathing between studs, and the insulation on the EXTERIOR of that sheathing will not affect the properties of that wood sheathing on the INTERIOR side at all.
Bill
>"We plan to use rigid foam as our only insulation, both in the walls and roof, a mixture of PolyISO (to keep thickness down) and EPS (to keep the PolyISO warm). We’re in climate zone Marine 4, western Washington state. "
In western WA you'll get far better performance if using all-polyiso instead of EPS for the outer skin. The January mean outdoor temperatures in your area are well north of 35F, making the mean temperatures through even the exterior-inch of foam much higher- in a temperature range where it beats EPS by quite a bit. Even the world's crummiest sample of 2lb roofing polyiso referenced by DOW in their Thermax promotion still beats EPS until the mean temperature through the foam is below 35F.
https://i.imgur.com/a3SvC7H.png
Type-II EPS performs at about R4.5/inch when the mean temp through the foam is 40F and R4.7/inch at a mean temp through the foam of 25F (often specified and tested at those temps by the manufacturers). At a mean temp of 40F through the foam the crummiest polyiso is still performing at nearly R5/inch, about 10% higher than Type-II EPS. (The gray curve for mineral wool is above where Type II EPS performs.)
Making the outer layer EPS rather than polyiso would outperform polyiso of equal thickness less than 5 % of the time in your climate even in January, and would outperform EPS substantially the other 95%+ of the heating season (even January!)
https://weatherspark.com/m/991/12/Average-Weather-in-December-in-Bellingham-Washington-United-States#Sections-Temperature
^^The dotted blue line is the 90% percentile band- 90% of the time it's warmer than that in winter, and it has to be substantially cooler than that that dotted blue line for the last inch of foam to perform better as EPS than polyiso.
Hi Dana,
Thanks for the highly detailed analysis! I had been wondering, in our relatively mild climate, whether we even needed to worry about the cold weather performance of polyiso, now I know we don't. So much the better, that keeps our thickness down a bit (or R-value up for the same thickness). :)
Around here, EPS is better R per $, new or used.
You may find this Mat Risinger video interesting as he built a simulate house.
https://www.youtube.com/watch?v=4mNTHP-Y_GE&t=57s
There should be several more video from when it was constructed.
Walt
Walter,
That's an excellent video, thanks! I'll definitely check out the others in the series. It's fascinating to see how they handled things like the plumbing and electrical in this type of construction, as well as what are some of the really great benefits of the method. While our own plans aren't quite as extreme as Matt's build, given we plan to have the lower 4' of the walls covered, it's nice to see I'm not the only one realizing the benefits, and nice to have the extensive video showing the aesthetic results. I'm personally not a fan of the white-on-white-on-white, but that's me (and my wife). :)
In case you need another example, here is one from the Midwest. I worked on this house after the renovation pictured was completed (some roof and bathroom modifications), let me know if you have any questions that I may know the answer to.
https://www.architectmagazine.com/project-gallery/farmhouse-in-the-city