Anyone have experience with steel open web joist composite slab systems?

I’m in the thought stages of the next build. I’m thinking about the viability of using steel open web joists with a composite slab system, vs wood open web joists.
Last build I got some experience with composite deck slabs by doing a concrete veranda deck over a conditioned space. I used the canam P-3615 composite decking with a span of 7′ between bearing points.
This decking can allow for some very long spans between joists, 7-10′ spans depending on which deck is used.
Even some of the other composite systems like the canam hambro system where the joist is the reinforcement to the slab, their joist spacings are around 4′ (based on load design)
Those compared to the 16″ spans of wood joists. For a build of say 15’x60′ footprint, it can be a difference of 45 wood joists and 28 sheets of ply per floor vs say 8 steel joists and 5 rolls of steel decking + 6 cubic meters of concrete per floor.
Just wondering if anyone has any experience with specifying, costing or building this way? Especially now with polished concrete floors being all the rage, even on upper floors. I’ve been seeing it on some ICF specs as well.
My general perception is the steel will cost more mostly because I only see it in commercial buildings. but when costing the materials of wood open web joists those are also very expensive. Wood is a lot of material and a lot of labour. Steel I assume is expensive but much less materials and less labour.
Looking for experience in cost, time and labour.
Thanks,
Jamie
GBA Detail Library
A collection of one thousand construction details organized by climate and house part
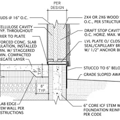
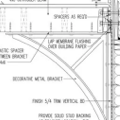
Replies
Screenshots of the composite systems to give a visual.
Jamie,
I've designed several commercial buildings that used composite systems. The skill set involved, sequence of construction and detailing are completely different and need sub-trades that usually don't work on single family dwellings. The price, including the up-charge for skilled labour, is substantial. The only houses I've seen that have used it have been high-end modernist houses designed by prominent architects.
The results can be really spectacular - and that may be a good reason to use it. Cost and efficiency unfortunately aren't. Production housing may look inefficient, but the margins are tight and there isn't a lot of fat in the process. The reason you don't see much use of alternative systems and materials is almost entirely economic. If you could build a house cheaper and quicker with steel and concrete, you wouldn't be the first considering it.
What you’re thinking about is a basic commercial floor system: steel trusses or girders strung between steel columns (usually), corrugated steel floor pan, then a concrete floor poured over the floor pan. This is solid, very much more so than typical wood joist floors, and can handle SPECTACULARLY long spans IF you use suitably large beams or trusses. You could conceivably build an entire house with no load bearing walls or columns anywhere inside.
I think Malcolm is correct about costs though. On large commercial projects, steel is cheaper since there is less of it in terms of total number of components, and it can handle MUCH larger loads so much larger buildings. On small projects, the cost savings disappears. A typical residential GC won’t be used to working with commercial building methods either, so you’ll get pushed into a lot of normally commercial contractors who probably won’t be very interested in what they will see as a very small project. Contractors that don’t want to work on a job will price it accordingly, so you'll end up paying a premium if you really need their services.
As an alternative, have you considered using some large glulams to support more typical residential flooring systems? Big glulam beams can handle pretty long spans too, but you can still work with them using regular residential construction methods for the most part.
Bill
What often drives the switch from wood to steel or concrete are building code requirements that certain occupancies or certain sized buildings be constructed from non-combustable materials.
The problem as I see it if all the steels thermal bridging forces you into an exterior only insulation requiring 3 plus inches of foam with complicated exterior finishes.
Walta
Excellent, thank you for your experience.
Malcolm, your point on getting contractors or skilled labour is what I begrudgingly suspected. No ironworking crew is going to come do a Toronto row house with the tightest access imaginable.
Bill, actually I'm very used to LVL beams and I joists. Most downtown Toronto houses are 12-20' wide. So these spans aren't much for engineered lumber. My current build I don't have any interior load bearing walls, however, I want to move away from LVL's and I joists, & Toward open web truss joists. The amount of time and money I've spend in labour with mechanicals in the ceiling, it would be worth it to shift to open web wood joists. Both from a labour and design perspective.
Interestingly though, in talking about steel... It's never really been used in residential in the past.. but it's slowly creeping in. I have seen I-beams in basements of production builds. In my current project, which is a Reno, I have 5 steel beams I've placed, just the same as the lvl beams I've placed as well. I don't see erecting steel as the biggest deal, which might be why I'm barking up this tree.
Steel has been common in the US for decades in one spot: under the ridge in the middle of basements. Joists then go from exterior wall to the steel beam in the middle, with a second joist on the “other side” from the steel beam to the opposite exterior wall. Occasionally you see steel in other places, but the midpoint of basements is by far the most common. With a single I beam places that way, you don’t really need a specialized crew.
Some of the newer houses with fancier designs need steel for other spots, notable but cantilevers or very long spans. Everyone wants “open concept” these days and steel can be very helpful when you need a long, unsupported span. I’ve used rectangular steel tube (4”x5” usually) in areas where I need to brace a floor in an exposed location since it looks cleaner than an I beam. I like working with steel due to the flexibility in design it allows, but many residential builders aren’t used to it so that’s the only real issue.
If you use a lot of steel and get into onsite welding and joining, that’s usually when you have problems with the crews. The other issue I’ve run into is that steel is much less forgiving with measurement errors than wood is. It’s easy to trim a wood beam with a saw onsite, but you REALLY don’t want to have to do any onsite fabrication with steel: you want everything pre punched so you just assemble the pieces on site. I have run into issues with having to have new steel pieces made by the steel fabricator due to problems with measurements made on site in the past. This can result in project delays and lots of finger pointing.
Bill
Jamie,
Several of my friends who design on the Canadian prairies say the trend there is having the whole structure trusses with no intermediate supports. 24" to 30" open web floor trusses and trussed roofs of various types. They say it makes coordination very easy, lots of space for services, and fairly cheap. The downside is the height the structure adds.
I've had good luck with these for areas with a lot of plumbing/hvac:
https://www.steelform.ca/portfolio/mega-joist/
They come in a number of thickness/flange widths and you can also make a built up beam out of them for larger loads. Much easier to work with as you don't need a crane to place it like with iron beams.
You need special screws to attach subfloor to them, not hard to find but not a box store item.