Attic insulation and venting in an old timber-framed house

Sometime in the ’40’s or ’50’s (my guess) someone put about 2″ of fiberglass between the ceiling joists in the attic of my 1890 timber framed Greek Revival here in Mystic CT.
One issue in adding insulation is that eave venting is really hard to add due to the way the house is built. There are huge, heavy timbers used to frame the eaves. The depth of the eaves is quite shallow. The top plate of the wall is nearly 8″ square, and there is a timber which is attached to the rafter tails and presumably to the plate as well, to form the soffit, and this timber is pegged in a way that suggests it is rather thick and heavy. The best I could do would be to use a long drill extension and poke some holes, but this would mean the area directly above the top of my upstairs walls would get little to no insulation after I add baffles, due to the classically low pitch of the roof. I think it might be more important to insulate that area than to vent it…
There is some “eave venting” because I can see daylight through a few gaps between the roof deck and the top of the cornice molding. I’m thinking if I simply stuff fiberglass into the eave cavity there might be enough air movement through these gaps…
I added a large screened louver at one gable to supply venting (this used to be a window). There is already a ridge vent. The other gable has a traditional fan window. This window is held in place with a few clips and so might also qualify as “venting”, since as you would expect there is some daylight around the perimeter. (Weirdly, there is no evidence of moisture damage or moisture entering there. I repaired the window and put it back the way it was.)
My approach to insulating this attic is currently to do some thorough air-sealing of the ceiling, and then add lots of fluffy insulation. I happened to find a great deal on Craigslist and got a whole bunch of R-49 fiberglass batts, nearly enough for the whole thing. After air sealing, my plan is to throw these in between the joists and then go back over the whole thing with blown-in cellulose, maybe go about 10″ higher than the thickness of the batts.
Is this going to be problematic, or is my approach ok?
Another issue related to the first, is what to do around the chimney which pokes through the center of house. Intumescent caulk and metal flashing for air sealing, sure. Then I guess it’s ok to put mineral wool up against this?
Also, there are some heavy timbers in the ceiling (of both floors) that are right up against the brick. These have obviously been there since the house was built but are clearly not “up to code”. Should I never use my fireplace? Moving these is out of the question since a couple of these are heavy beams and are part of the basic structure of the house…
My plan is to add a pop-up damper at the top of the chimney. I’d like to insulate around the chimney on the lower floors as well, since the masonry itself could be viewed as a giant thermal conductor. The top-mounted damper will prevent the column of air from traveling but presumably air is a thermal conductor as well, which would take the heat from the center of the house and bring it right up through the roof. Given the extremely tight clearance between the existing (Chestnut!) wall framing and the masonry, I was thinking that rigid mineral wool board might be a good choice, although I also happen to have some KoolTherm phenolic board that is supposed to be non-flammable. It’s rated at R-10 at 1.18″ thick, or thereabouts.
GBA Detail Library
A collection of one thousand construction details organized by climate and house part
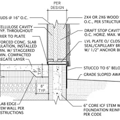
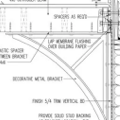
Replies
I had a circa 1812 house that experienced huge icicles and ice dams. Like yours no way to eave vent. I found that with rigorous air sealing, 20" of insulation, and a few small gable vents, the house was 100% free of ice and snow problems. I did keep the insulation away from the roof deck at the eaves by adding a 1/4" osb baffle under the rafters.
Thanks for that information! Makes me feel optimistic.
What's the logic behind keeping the insulation out of the eaves, if there's no vent there?
What kind of insulation did you use?
I'm assuming you used Great Stuff or similar for your air sealing?
How long were you in the house post-insulation? Ever check the attic in the winter for condensation?
I thought having the attic air exposed to all of the deck would help keep temperature even across the deck and prevent ice dams. I'm not sure there's building science to back that up. I actually put a poly vapor barrier under the joists, back when that was the recommended approach. I had gutted the whole second floor, including walls, so it was easy. Another house I did, I used great stuff, caulk, and pieces of sheetmetal, whatever would work. That house was more traditional, however I found out after I was done, that the vented soffit had a solid backup behind it. That house, too, lost its icicles and ice dams after I was done. I did notice in the old house a little black mold in the attic after a couple of years. I assume the roof was occasionally getting cold enough to get below dew point. I don't live in either house anymore so am unable to check current status.
MKCF,
You approach will work, although it's hard to evaluate the risk of fire associated with the timbers in contact with the chimney.
Don't worry about venting the attic -- just proceed with your air sealing plan. If there are no signs of moisture problems in your attic right now, there aren't any reasons to believe that you'll have moisture problems in the future.
Old chimneys were usually thicker than new chimneys -- with perhaps 8 inches or more of brickwork or stone between the flue and the exterior of the chimney (as opposed to 4 inches with modern chimneys). That improves fire safety.
That said, it's possible to imagine a dangerous situation. Over many decades, wood framing near a chimney can undergo pyrolysis -- that is, chemical changes due to exposure to heat. The pyrolytic process makes the wood more flammable. Eventually, if the chimney gets unusually hot, the wood can catch fire. This typically occurs when you have a chimney fire (that is, when accumulated creosote ignites), so it's essential to keep your flue clean.
Thanks guys! Makes me feel more confident. This is my first old house and I plan to stay here until I'm too old to take care of it.
Pyrolysis sounds totally possible as the wood gets drier and drier. There's some blackish discoloration that I assumed was due to water leaking around the flashing, but it could be worse. Maybe I can carve it away to create an air gap. I doubt my fires will get super hot though. I converted the firebox to a Rumford so hopefully it will heat the room very well with only a small fire... I haven't tested my firebox yet so there's also the possibility that the fireplace will be entirely decorative, if I screwed it up.