Soffit venting antique timber frame house

Good afternoon. I am residing my 225 year old timber frame center chimney colonial in New Hampshire. I am using hardi 4 inch reveal clapboards and I am building a drain screen with 1×3 furring strips to hold the siding off of the exterior weather barrier. My question comes from building an adequate soffit vent that will flow air. The building currently has no soffit venting. The soffit board is a 2×6 that spans the 10 feet between each timber frame bent. The original builder left a 2 1/2 inch gap between the building and the start of the soffit board which was then covered with a piece of crown molding. So given this 2 1/2 inch gap and my drain screen I will have a continuous air gap all the way from the bottom of the building and into the attic space. I will be using ridge vent 20 made by airvent at the top and bottom of the drain screen to keep bugs from making there way up the way behind the siding so this will slow down at movement. Does anyone have an opinion if this will allow adequate air flow to act as a soffit vent or will I need to drill holes up through the soffit beyond the crown molding through the 2×6 to give adequate soffit venting. The home has no ridge vent unfortunately because of the 8×8 used as a connection between each vent where the ridge board
would traditionally be. The building only has gable end vents at the peak.
GBA Detail Library
A collection of one thousand construction details organized by climate and house part
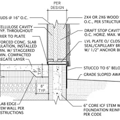
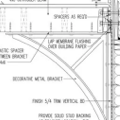
Replies
Hi Jonathan.
The short answer is that it is generally okay to vent your rainscreen into a vented attic. However, your building inspector may or may not accept this as your attic venting intake and if you want to follow what the IRC has to say about attic venting, you'll need to do some math to determine if the rainscreen is providing enough intake.
I suggest you read these two articles: All About Rainscreens and Venting a Tricky Old Roof. The first discusses venting the rainscreen into the attic. The second will walk you through the math. It also offers some alternative options to soffit intakes.
Thank you for the reply and helpful articles. My concern about venting into the attic space( I would prefer to vent into the attic for ease of detailing) comes from the fact that it is an old home and even the best attempts at air sealing and insulating will still allow this area between the siding and the wrb to get moisture I am sure because of air leakage from the warm inside air during the winter which will then head up into the attic where even after the best attempts at air sealing and insulating allow moisture to condense on the cold wood surfaces if I don’t run my gable end fan about 6 hours per day in the winter.
If it is your belief that the amount of moisture will be very minimal that is added to the attic through the rain screen venting into the soffit than I will just not worry about the additional small amount of moisture. Adding up the 3/4 “ over the 40 feet nets me 2.5 sqft out of the 4 square I am suppose to have for 1200 sqft. With the addition of the front of the house that will give me 5 sqft so that would be an adequate amount of soffit ventilation. The gable end vents only provide about 1 sqft each but I have the option to turn the gable vent fan on and or open the 4 windows in the gable ends to increase air flow.
In conclusion if you think that the venting of the rain screen won’t added significant amounts of extra moisture into this space then I will just do that and forgo the venting the rain screen to the exterior or not top venting it at all. I was also for go doing a traditional soffit vent. Thanks.
The important benefit of rain screens is provide a capliarry break between the siding and the WRB. Rain screens are about as effective with only the bottom vented and top sealed up. This is a very common detail.
I would cap the siding a bit bellow the soffit and cover the gap with a piece of bend perforated flashing as your eaves vent. You want to make sure that critters can't make it into your attic through the gap.
If your gable vents are the correct size, you might not need soffit vents either. I would check this before going crazy on this detail.
If you do want to vent your siding to the attic, I would check your local code first. Code might not allow it as it could be a fire hazard.
Thank you for the reply. I am not overly concerned bulk water making it around the hardi clapboards but more of a drying space for interior moist air that has made its way out of the home. I don’t want to add moisture levels to my attic space in large quantities though since top ventilation is lacking without a ridge vent and only 1 sqft gable end vents. I do have a gable end vents fan though which I plan to put a humidistat controller on so that it only kicks on when moisture levels rise rather than a timer.
Jonathan,
As far as I know only BC precludes connecting a rain-screen with the attic. The argument in favour of doing so is to increase the air-movement in the wall cavity, but especially with two storey walls like your house has, the amount of air being supplied will be well below that necessary to vent the roof space.
Given that you are ideally trying to situate at least 50% (or better still 60%) of the required roof ventilation at the eaves rather than the ridge, I don't see any good way around supplying some form of soffit vent.
In new, well air-sealed houses roof ventilation can be a lot less important, but in older homes, especially those where insulation is being increased, it adds layer of necessary protection.
To get back to your primary concern: My own hunch is that the benefit of increased air-flow in joined wall cavities and attics is outweighed by the potential added moisture - but it is just a hunch.
Edit: The problem with using an exhaust fan in the attic is the same one as supplying less ventilation area at the soffits than at the ridge: The attic becomes depressurized and pulls more moist air from the house below.
Thank you for your reply. Some of it confuses me though. Are you saying that a two story house wall cavity will decrease total air flow through the rain screen? The math works out to be 2.5 sqft on each side for a total of 5 sqft where 4 sqft is recommended. What is the reason that you feel that will be an inadequate amount of make up air from the low point in the roof assembly?
I guess that you are thinking that with only two square feet up high that at the gable end vents is creating some sort of imbalance but I’m unsure of how more soffit vent located just inches away from the rain screen venting into this space will fix it? I suppose I am just confused.
I am unsure of the comment about the wall cavity rain screen being tied to the attic. Are you saying that it will be beneficial to have the rain screen connected or that the potential for added moisture to the attic from the two being connected will be an issue?
Jonathan,
Sorry if my reply wasn't clear.
The reason Joe Lstiburek cites for connected rain-screens not being a problem for flame-spread is that the friction losses in such a small cavity mean there is very little air-movement- and that friction increases with the length of the wall cavity - especially as many are not going to be continuous from foundation to roof because of windows and lower roofs. I don't think you can rely on the total open area of the wall cavities supplying the same amount of air as you would get with vents the same size at the soffits.
Like you, I'm not sure the benefits of increasing the air-movement in the wall cavities outweighs the potential downside of introducing more moist air into the attic - although as I said I have nothing to back that up.
Connecting the two may work, but rather than chance it I would do as Akos suggested and block the top of the cavity close to the soffit, allowing the ventilation air for the attic to be introduced from behind a frieze board instead.
Malcom, thanks for the clarification, I understand what you were saying now. So as far as “introducing air into the soffit behind a frieze board” I now am not sure of what your thoughts are there as far as a soffit vent. Behind the freeze board means to me the building sheathing. Or did you mean further out of the soffit toward the drip edge?
Jonathan,
Again the fault is mine - I should have said a "new" frieze board at the top of the wall. If you stop the siding (and cavity) a few inches below the soffit, placed vertical blocking at 16" oc, and covered it with a frieze board, it could overlap the siding slightly , but still leave a ventilation gap. The gap could be protected by cor-a-vent or perforated flashing.
Thank you for the reply. I decided to pull down the old 2x6 solid soffit board. I then ran a level line with the bottom of the existing facia boards on the house itself, attached a ledger on that established line out of a 2x4( provides the hard stop for any air flowing up the rain screen) and then attached 2x4 blocking from the ledger to the outer facia. This allows me to know install 2 inch wide louvered soffit vent for the whole length of the house which will get me more than enough of required soffit vent and terminate my rain screen into a vent below the frieze board.
For my frieze board i plan to use the same “air vent” ridge vent material( black hair type) that I am using as a strip st the bottom between nailers to prevent insects and rodents from climbing up. I used coravent on the gable end at the top because the siding that was landing on the pitch of the roof up top needed a solid nailer to land on. I will use a 5/4 board for the frieze board and dado the bottom to provide a gap for it to drop over the top of the siding and allow a vent I believe. I would just stand it fully proud of the siding with blocking but the issue is that I am putting crown molding up top between frieze board and soffit and my soffit is only 8 inches deep, I need to reduce how far my crown extends onto the soffit as much as possible.
Hi Jonathan: I, too, live in NH and have been distressed to see the value of these homes decrease because they are uncomfortable and hard to heat. I urge you to look into adding exterior foam to the walls and roof; it's only doable when you are redoing siding (and roofing) so you have the perfect chance to make a huge difference in the comfort of your home right now.
To your question: Does your roof have full length rafters rather than rafters and horizontal purlins? The latter are more common in the older colonials and impossible to vent on the inside of the roof. Assuming it's a continuous rafter roof, I'd suggest a separate soffit vent for the roof, which could be brought in through a screened gap between two of soffit boards which will be less visible. Provide a 1-1/2"- 2" interior space for the vent, and air seal the attic side of the channel. If you have a rafter and purlin roof, the only good way to vent it is to add a vent channel above the roof (again air sealed to the inside), at which point it makes sense to add exterior foam under the vent channel. (and close off the existing vent space). Both wall and roof foam can be pretty well "hidden" so they aren't very noticeable from the exterior, especially if you can adjust the roof trim at the same time. Good luck with your project!
Thanks for the reply bob. I have a gap between the roof deck sheathing and what might be considered the “top plate” on traditional framing but is the connection between the timber frame bents. This allows me to have a soffit vented into the attic space. I would love to add exterior foam, money isn’t really an issue but a couple issues have made me decide against it even though it is the time to do it. I resided the north side of the house last year and a couple issues that I had to deal with was that the roof sheathing ends just proud of the wall sheathing, no overhang. So without doing a roof tear off this was a non starter for foam. The other issues that I dealt with is the fact that the sheathing boards are 225 years old, some needed replacement which I did about a 1/4 of them and the others I wouldn’t trust trying to screw vertical nailers into that sheathing and then hang hardi siding off of that( lots of sheer strength needed because of the fact that the siding would be so far away from the sheathing. Lastly the issue was that I wouldn’t want the windows to be inset from the siding creating a recessed look. I thought this wouldn’t look right at all especially on an old house. Like I said, I would have really liked to add foam but just didn’t see a way to overcome all those issues.
I would 2nd Bob's suggestion. Rigid insulation would significantly reduce your heat loss.
Even if exterior insulation is out of the budget, covering the board sheathing with a layer of peel and stick can significantly reduce the air leakage. This is probably the best return for your dollars in terms of energy efficiency and comfort. I've done this with a 100 year old garage when converting it to a studio and the difference was night and day.
Thank you for the reply. See my above statement about foam.
As far as a sticky wrb like blue skin, I hadn’t given that much thought. I already covered it with tyvek and taped the seams. I know this wouldn’t be as good as a sticky wrb but I think it will add considerable “air tightness” to the building.
Any opinion on the air tightness of a peel and stick vs. tyvek? I can definitely
Consider blue skin for the other two sides that I will be siding this year.
Although it is possible to detail house wrap as air tight, I just don't think it is robust enough.
Because of board sheathing, you have big gaps and can have a lot of 3d air flow paths. Once you have a hole in your house wrap, air from everywhere in the wall will find that. This can't happen with peel and stick.
House wrap is not great at resisting positive pressure which you would see near the top of the walls. Over time, any small stress from nails/staples would become larger tears and leaks.
Another issue with housewrap is you can have a small gap on the cold side of your insulation. The board sheathing allows pretty good air from from your insulated wall cavity and you can potentially set up convective loops through your insulation reducing its effective R value.
This is why I would recommend peel and stick. Make sure the product you choose is permeable.
P.S.
If you are dense packing your walls, the air sealing from your WRB is less of a concern as the insulation does a good job of limiting air flow.
Good info, ill have to use a sticky wrb with an appropriate perm rating for the other two sides since at this point the tyvek and rain screen are already installed.
One pointer for peel and stick, most can be installed as vertical strips without any special detailing or additional overlap. It is a way easier install on walls.
Thanks Akos. Hanging it vertically would be A good option. Any suggestions on brand and product of sticky wrb?
Would Henry blue skin wp200 be an appropriate wrb for this application?
The WP200 is for foundations and impermeable.
You want VP100/VP160 or Sopraseal Stick VP or one of the fancier ones from https://foursevenfive.com.
Awesome. Thank you.
Recycled polyiso foam is readily available for half the cost of new.
Tyvek is only as air tight as you can make the top, bottom, sides, openings and seams, all of which need to be carefully taped, while the peel and stick, when properly adhered is tight wherever it is.
My experience with several houses is that recessed windows are hardly noticeable as different from non-recessed windows. The overhangs are a larger issue - if you are adding foam to the roof you can easily replicate the original trim details slightly higher on the building, so it disappears. If you are not doing the roof, you would need to extend the overhang slightly which would bring the eaves down slightly on the wall.
That makes sense about the tyvek that air will work its way out around the sides. I’ll tape the bottom and the top to the sheathing with zip tape. I’ll use a peel and stick for the other two sides.
As far as the in set windows, you are probably right that it wouldn’t look bad. Another concern I had was about the wall system staying dry since I have a 1/2 inch of foil faced eps with seams taped on the interior over the studs as a thermal break and vapor barrier. So with that system the moisture that makes it’s way around really needs to dry to the exterior is how I understand it. So placing another layer of foam over the exterior and taping the seams would probably be an issue? If I was to do things again and money / time was no object, I would remove the roof assembly and reframe the roof with rafters to make a strong and flat roof assembly along with 2 inches of XPs to bring it into the building envelope. I would build overhangs on the gable ends as well which would have allowed me to do 2 inches of xps on the exterior all the way around.
with interior polyiso you definitely do not want exterior polyiso! Double vapor barriers like that can prevent the wall from ever drying out. But 2" of white EPS (coffee cup foam) would work fine. I've done a few new houses with strapping over exterior foam - using GRK screws for fastening the strapping, and have used cement board with no issues. But the manufacturer frowns on that and wants at least 1-1/4" or more of wood for the nails.
I'd also suggest (unless you've already started siding) that you look at LP Smart Side siding - it's an Advantech type board, very water resistant and does not have the delamination and moisture sensitivity issues of cement board. Also much lighter, easier to use and as with cement board is nailed at the top edge.
Yes, I was concerned about the two layers of eps, I didn’t know that polyiso could be used though so that is great knowledge to allow the moisture to dry to the polyiso side.
As far as the nailers through the foam using grk, I wouldn’t be concerned about that if you screwed into framing with the grk but given this is 1 inch boards for sheathing, they are 225 years old and the vertical studs are
About 30 inches oc, I just don’t have the confidence in the strength of the boards. Maybe I am overthinking it but I only used half inch thick strips for nailers on the north side last year and screwed them at 12 inches oc and every 1 foot up the wall.
On the side that I am doing now, I don’t have to deal with the lack of an overhang so I went with 1x3 strapping as my nailers instead.
As far as hardi goes, I have found it to hold up excellent in the past. It Holds paint excellent. If the gaps against any trim are kept at 3/16 and chaulked with a high quality chaulk I have seen no trouble with delamination.
I know that the LP is a little newer to the market and may be a superior product but I also knew that there was similar press board products in the past that didn’t hold up. Maybe If I had been doing this in 5-10 years and the lp was holding up good still out in the field then I would have done that. Just kind of using what I know works well for longevity. The hardi is awful to work with though! Dusty and a pain to make detail cuts around stuff.