Attic/Roof Insulation vs Vents

I recently purchased a home, which was built in the mid-1950s with a CMU construction. My current roof system includes a ridge vent, gable vents, and no soffit vents. Roof has a decent pitch and is fairly straightforward in the design (not a lot of angles/crannies). No HVAC or ductwork in attic, other than duct for bathroom fan exhaust. There is some fiberglass batting on the attic floor of questionable age and depth.
I am replacing the roof later this summer with a standing seam metal (Galvalume) roof (with vapor barrier underlayment, of course). I also want to replace/update the attic insulation to R-49 (I’m in Zone 5). I do not see any reason that I need to keep the attic to be a conditioned space; I’m simply looking for the best combo of insulation and moisture control.
I understand these are my options:
Opt 1: Add spray foam to the roof deck, and eliminate my ridge vent and gable vents.
Opt 2: Add spray foam or a Flash and Bat combo to the attic floor, and keep the ridge vent. Consider adding soffit vents for more thorough air circulation. Don’t cover up these (hypothetical) soffit vents with spray foam.
Opt 3: Add rigid foam panels underneath the metal roof, in combination with one of the other approaches to meet R-49. This sounds ideal, but the cost might be unattainable.
Could someone advise me on the best approach? Or if there are other options/combos I’m not considering? I’m just not sure how I’m going to reach R-49. Of course, every roofer and insulation company I talk to gives a different opinion.
Thanks in advance!
GBA Detail Library
A collection of one thousand construction details organized by climate and house part
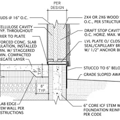
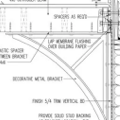
Replies
I think keeping it as a vented attic is the best approach. To do this, I'd remove the existing fiberglass, which is undoubtably filthy. Then air seal the attic floor. There is no reason to do this with a layer of spray foam, and several reasons for not using spray foam. You are looking to seal holes and seams. Once the attic floor is sealed and you've added soffit vents, just blown in cellulose insulation.
Bonus - your house will likely be noticeably quieter with R49+ of cellulose insulation on the attic floor.
Thanks for the reply, Andrew! I am also leaning toward keeping the attic vented and sealing/insulating the floor. I have an insulation contractor coming to check it out this week, but I suspect they'll push for spray foam. I'll look into alternate sealing methods and insulation types; I agree, there are some drawbacks to spray foam that concern me (particularly off gassing and removal, should we ever need/want to do that).
Any ideas on who typically installs the soffit vents? The roofers don't have any interest in doing it, and I don't imagine insulation folks do, either.
Andrew's recommendation is exactly what I would recommend too. I guess insulation contractors make more money on spray foam and so they like to push for it. You can just ignore that part of the sales pitch and tell them to leave if they won't stop talking about spray foam.
If you give a general idea about your location, people might know a contractor to suggest. I found an excellent insulation contractor by asking builders who like to use cellulose for recommendations.
The soffit work includes putting in the vents and putting in baffles to keep the cellulose out of the vents. You might find a carpenter to do the vents. The baffles could be the carpenter or the insulation contractor.
Note that putting in the baffles and air sealing the tops of the exterior walls is easier to do while the roof deck is off if they are replacing any of that, especially if your roof pitch is low, such that it's hard to get back in there from inside the attic.
Thanks for the response, Charlie. Very helpful.
I'm in Ulster County (Hudson Valley area) in New York. I found some folks who do cellulose, I think, so now I just have to convince them to answer the phone. Folks are slammed here. All recommendations are welcome!
Are you confident that (1) you never want to have habitable space up there and (2) you can never envision duct work there for HVAC (obviously depends what you currently have today)?
Never say never, but for our current purposes, we don't need the extra space. It wouldn't be a good living space, so would only be for storage. We also have a garage, a shed, storage rooms downstairs, etc.
I don't think we would ever do HVAC there. It seems that it's best avoided if possible. We have a utility room downstairs. We are considering upgrading from a furnace to geothermal, and I'm pretty sure the air handler would go downstairs.
> I don't think we would ever do HVAC there. It seems that it's best avoided if possible.
Definitely simplifies things if you can avoid it!
> We are considering upgrading from a furnace to geothermal, and I'm pretty sure the air handler would go downstairs.
Side note... geothermal probably does *not* make sense in climate zone 5, unless there are odd incentives for it. Air source heat pumps are far less expensive and have become incredibly efficient.
When you're ready, post about that and you'll get lots of info!
Thanks Patrick, I decided to create a post about the heating system. Already getting good tips!
Had the insulation contractor come by. They recommend unvented attic, closed cell spray foam on sheathing, and leaving the existing fiberglass bats on the floor to save the money of removing them. I feel like this is the opposite direction than where GBA would go. I have no reason to condition the attic (no ducts or mechanicals), so it seems like extra money in the long run to heat/cool the extra space (700 sq ft?). I also don't think it makes sense to leave insulation on the attic floor if the point is to bring the attic into the thermal envelope. Am I crazy here?
>"Opt 3: Add rigid foam panels underneath the metal roof, in combination with one of the other approaches to meet R-49. This sounds ideal, but the cost might be unattainable. "
To meet code on a U-factor basis a continuous foam panels on the roof only takes about R35, not R49. That could be as little as 6" of polyisocyanurate- it's doable, but not cheap.
If the rafters are 2x6, installing 5.5" of rock wool (R23) in the rafter bays and 4" of roofing polyiso up top (R23) also gets you there, and is enough for dew point control at the roof deck even in climate zone 6.
In zone 5 with 2x8 rafters it's fine to use as little as 3" of polyiso up top (R17), with R25-ish fiberglass or cellulose between the rafters. Even though it's less than R49 the R17 thermal break over the rafters is enough to bring it in on a U-factor basis.
Going for R49 with 7" of closed cell foam between the rafters is expensive, and somewhat underperforms the above solutions due to the thermal bridging.
Even with cheap cellulose on the attic floor there is usually a substantial amount of air sealing to be done to guarantee that it will work to spec. While it's easy to do that air sealing well when constructing a new home, it's sometimes harder to nail down adequately in retrofits.