Air-to-Water Heat Pump vs. Electric Boiler

Hello everyone,
I’ve been doing lots of reading on this site and others. I have read a few articles on having a highly insulated house with radiant in-floor heat. I am trying to decide if it is worth the cost of installing an Air-to-water heat pump, or to go with an electric boiler. After 1 year, I would have a good understanding of my energy consumption and build a solar array accordingly.
Our house will be 2000sq, 25′ wide and 42′ long, with the front facing south with a good amount of glazing. Exterior walls with be R47 which includes 4” of exterior mineral wool. Attic is R88 of blown in cellulose and the slab on grade with have R20 underneath. Our window package is quad pane, with a U value of .15 or a R value of R6.66.
As you can see it should be a well insulated home and we will put our attention into proper air sealing of the envelope. I am wondering if people think it is worth spending the money on a ATWHP, which I have been pricing out the Arctic HP and buffer tank/DHW.. just north of 20,000, which would include everything. Or if a in-floor heating system with a electric boiler would be the better choice, and in a years time it would be supplemented with a PV array.
We are located in the Yukon, which I believe is climate zone 7A.
Thank you for your feedback.
GBA Detail Library
A collection of one thousand construction details organized by climate and house part
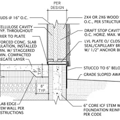
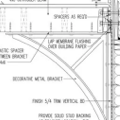
Replies
There's no advantage to an electric boiler over just embedding electric wires in the slab, the energy efficiency is the same and the embedded wires will be a lot simpler to install and control.
I do agree that it would be easier to install and control, I am a licensed electrician so it would be an easy install.
I haven’t really heard of people using electric cables for in slab whole house heating, mainly small areas of a house. I believe water is able to deliver more heat at a lower operating cost.
I also have watched many concrete pours, and typically the contractors I’ve watched are not overly light on their feet, and I believe that the cable could be easily damaged rendering the entire cable useless.
I like the idea of pex, as a variety of delivery systems can be incorporated into the design to deliver the hot fluid.
"I believe water is able to deliver more heat at a lower operating cost."
It all depends on how the water is heated. If heating the water is done more cheaply than running electricity through a resistance element -- by burning fossil fuels on site, or by using a heat pump -- that's true. If the water is heated using a resistance element the cost per btu is the same as using wires in the floor.
Underfloor wire systems aren't typically installed in the concrete pour, they're installed before the finished flooring but after the slab.
Right now there isn't a good all-electric solution. Air to water heat pumps are a niche solution, on the verge of experimental. They also suffer from performance drop-off at cold temperatures, which is going to be an issue in Yukon. They're also really, really expensive. You can buy a basic minisplit for less than $500, you'd be pressed to get started with air-to-water for 20 times that.
You can ballpark annual costs some: take your heat load, say it’s 5kw. Next, divide by the heating degree days for design day: for example, a base temp of 20C and low of -40 gets you a HDD of 60. Then multiply by annual average HDD then multiply by 24. So if HDD average 6000 annually, you’d need about 24 x 5/60 x 6000, or 12000kwh. That’d be your usage if you only had an electric boiler. A heat pump might save you 6,000 to 8000kwh per year, roughly. If you go with the ATW, may as well install the electric boiler too.
So I don't know what part of the Yukon the question-asker is from, but I just looked up Dawson City and the average high temperature for January is -2F. Average low is -22F. I'm not sure in those conditions you're going to get COP greater than one.
Definitely not in Jan, but in September!
I am located in Whitehorse, the main city here in the Yukon, it is about 6hrs south of Dawson. Dawson is definitely colder than Whitehorse, usually by around 5-10 degrees Celsius in the winter, and typically warmer in the summer.
OK, your January average low is -1F, high of 13F. That may be within heat pump range.
Have you done a Manual J or similar heat loss calculation? Do you know what your 99th percentile heating temperature is?
I should have the manual J calculation back hopefully in the next week or two. I sent all of the needed information to Arctic Heat pumps to have them calculate it for the house.
According to this site your 99% heating temperature is -37C/-35F. That's pretty cold!
Radiant floors in low load houses are problematic. The high mass in the floor means that the responsiveness of your heat emitter is way out of sync with the responsiveness of the house. When you factor in solar heat gain you are likely to have major comfort issues with temps overshooting the thermostat set point. Think of the floor as an enormous thermal flywheel.
More from Martin Holladay:
https://www.greenbuildingadvisor.com/article/all-about-radiant-floors
Low mass emitters pair well with low load houses for this reason. I’d do a heat load calc and then choose an appropriate cold climate mini split ashp—Mitsubishi for ex. Install electric baseboard for backup.
Agree, and in general concrete is a poor choice for a radiant floor. (Unless you're parking cars it's a poor choice for any floor.)
I'm old enough to remember when radiant heat first got big about 35 years ago. Most houses back then were so leaky that the challenge was getting the floor to produce enough heat. If the floor is hotter than about 90F it becomes uncomfortable to stand on, and at 90F with an air temperature of 70F the floor produces about 40 BTU/square foot. In those old houses that may not have been enough.
The key to maximizing output is to get a consistent surface temperature, if there are cold spots you're losing heating capacity. The reason concrete worked well in those installations is that it has good heat conductivity, so the surface temperature is relatively constant. Somehow this became interpreted as a semi-magical property of a mythical "thermal mass."
As you point out, you want to minimize heat capacity in a radiant floor (or any radiator). If you look at modern underfloor systems like WarmBoard they have two properties: high conductivity and low heat capacity. WarmBoard is basically MDF with a thin layer of aluminum. That's what you want in your floor.
With such a well insulated home you understand your floor temp is likely to be lower than your body temp so your floors are likely to feel cool under foot and not warm the way heated floors do in poorly insulated home of the past did.
Understand the COP of all heat pump fall as the temperature differential between input and output gets larger when it is -20 and you are trying to make 160° water may go negative meaning resistance would cost less to operate.
I general am not a fan of ground source heat pumps but if your fuel is going to be electricity and you’re in the Yukon if the budget allows it maybe the best option.
Walta
The year-round average temperature in Dawson City is under 25F. Which means the ground is going to be permafrost below the surface. Frozen ground has poor heat conduction and doesn't work well for ground source heat pumps.
A vertical well might work but it would have to be deep. This would be true geothermal in that you'd only be extracting the earth's heat.
Just as a for-instance, you can see performance stats for the Arctic heat pumps here:
https://www.arcticheatpumps.com/specifications.html
(I don't have any experience with them, but their claim is good cold weather performance.)
Let's look at the middle one, which is rated for a nominal 14kW (48kBTU/hr) at 7c.
At 7c: 14kW, COP= 3.2
At -7c: 11.5kW, COP = 3.1
At -20c: 8.3kW, COP=1.8
So as it gets colder, the heat output gets reduced -- 40% drop from 7c to -20c -- and the efficiency also drops. This is typical of all heat pumps. What you'd need to figure out is how big a pump you'll need for the coldest times. Another thing to think about is backing it up with either resistive heat or some sort of fossil burner for the really, really cold times.
If I were to go with a ATW heat pump, it would have a buffer tank, and the buffer tank would have heating coils, which I believe Arctic Heat pumps default is 12kw.
Yesterday I was talking with a fellow who lives down the road, they have just finished one full winter living in their new slab on grade, in floor heating, well insulated, southern exposure house. He said they don’t have any overheating issues. They use the heat pump during the winter, but said after -21C (-5.8f) it switches over to electric resistance in the buffer tank, which I feel he was hoping it would operate to a lower temp on the heat pump. I don’t know what brand or model they are using.
It will be interesting to see where the manual J calc lands, that will help steer the decision I’m hoping.
This is the way to go- the decision is more ATWHP + electric boiler or just electric boiler. Nordic is another Canadian brand that makes them. Ideally yes, it’d always run and the elements would just supplement, not replace.
Did you notice the only way to get the COP up they are only running 45°c or 113°f and they do not make the calculation below -4°f. No one gets warm toes with 113°f water leaving the boiler and and my guess is the Yukon get much colder than -4°f.
I run my water at 95F and my floors are 78F or so, depends on the outdoor temperature because I have outdoor reset. That's a temperature where you just notice that they're warm, definitely not chilly. That's good for 16 BTU/sf. My house works out to 8 BTU/SF at design temperature (21F) but I only have heated floors in the bathrooms which allows me to run them warmer without overheating the house.
The biggest design decision is going to be what the cutoff temperature is where you switch from heat pump to resistance heat. From the weather stats you can estimate for any temperature how many of the degree-days in a year fall below that point which tells you how much of the total heating load for the year gets handled by each method. The lower you set that point the less electricity you use (until you get to the point where the cop hits 1.0) but the more expensive your equipment will be. So the question will be whether the lifetime electricity savings justify the additional initial cost.
To put those costs in perspective, let's say your house needs 14kW of heating to stay at 23C when it's at your design temperature outside, -37C. Just taking the numbers from post #13 for the sake of example, at 7C you'd need 3.7kW; at -7C you'd need 7kW; and at -20C you'd need 10kW.
If you set the cutoff to 7C, you'd need 3.7kW. At 7C you get 100% of rated capacity so you'd need 3.7kW of rated capacity.
If you set the cutoff to -7C, you'd need 7kW of actual capacity. At -7C you get 97% of rated capacity so you'd need 7.2kW of rated capacity.
If you set the cutoff to -20C, you'd need 10kW of actual capacity. At -20C you get 56% of rated capacity so you'd need 17.9kW of rated capacity.
We'd have to run the numbers, but I could see a scenario where even at -20C (which is where your neighbor is set) the heat pump doesn't provide a significant fraction of the total heat for the year, because most of the heat is needed on the coldest days. At the same time the cost of the heat pump doesn't really justify the savings on milder days. If that's the case, you look at other ways of providing heat -- conventional boilers, or just electric resistance, no heat pump.
If you go with electric resistance, there's really no point in having a hydronic system, it's easier to put the heating elements under the finished floor.
The important thing is to figure this all out before you start construction. It's never easier later.
I took a close look at the Whitehorse Heating degree days (This is in Fahrenheit, forgive me).
Over the last 3 years, Whitehorse averages about 12000 heating degree days with a base temp of 65F. About 85% of all HDDs are within heat pump range (for the Nordic brand). If your heat loss comes in at 10kw at -40F, you'd use about 27000kwh annually if you're using an electric boiler. Using a heat pump + electric boiler, you'd use about 13000kwh a year assuming the heat pump handles temps -5F and higher. Savings seem substantial and higher than I expected.
That sounds good, better in fact than I would have thought. Since this is such a crucial calculation I want to dig into the numbers. If 85% of HDD are in heat pump range, that means 23kWh in heat pump range and 4kWh outside. If the total usage is 13kWh, 4kWh would be for the resistive heat and 9kWh for heat pump. So the heat pump is producing 23kWh of heat using 9kWh of electricity, which gives a weighted COP of 2.55.
I'd want to make sure that's accurate. It's toward the top end of the range, the COP maxes out at at 3.2 at 7C. As the temperature drops, the COP drops and the amount of heat needed increases; both factors tend to drive the weighted average down. So a weighted average of 2.55 is higher than I would expect.
Now it is true that the year-round average temperature is 32F and there are probably a lot of hours in a year where heating is required but the outside temperature is in the range where COP is highest. But I'd want to dig into the numbers more.
I was looking at the Nordic heat pumps because those were more readily available to me. But looking at the Arctic ratings, seems even better! The largest is rated at a COP of 3.1 at -7C and 45C output water temp and the design supply water temp should be closer to 35C and even more efficient then. Since the Arctic supposedly works down to -30C, there will be additional savings vs. the Nordic which stops at -5C. Either way, these are just rough estimates.
Even if you don't go with a heat pump to start with, I think at this level of energy usage, the added benefit that having a hydronic system allows for some flexibility in the future is worth considering. No doubt, more expensive, but it's not easy to go back and add the tubes. I'd bet that heat pump technology continues to improve over the years. But even without changing heat pump tech, if the bills become too high for resistance heat, you could always had a gas/propane burner if necessary to a hydronic system.
In terms of year’s operating costs, our electricity rate is .187cents/kw, would I take the 27,000kwh/year multiplied by .187 for my annual operating costs?
Electric boiler would cost 5,050/year
ATWHP would cost 2,431/year.
The ATWHP unit itself costs approximately 7500.00 where as the electric boiler is more in the 2500.00 range.
Am I correct to think that the ATWHP has just under a 2 year payback period when compared directly to the electric boiler?
Roughly! But depends on the actual heat loss. This was assuming you could meet 100% of heating needs down to 0F, so that’s probably the largest model.
That's basically correct. Keep in mind that the 27,000 wH/year is based on a hypothetical heating load of 10kW, you have to do your own heating load calculations. In theory the COP is independent of the size.
But, but, but ... You really have to focus on the details. If you look at my post #25, you really have to focus on sizing the heat pump. Because the capacity falls off at lower temperatures, in order to get the full ability of a heat pump it has to be generously sized. That can be problematic because they come in a limited number of fixed sizes, you can't just order as many kW as you need, you have to buy what's available. And maybe you'll have to have two to get the capacity you need. Or maybe you'll end up at a point where you're slightly undersized with one unit, but to go from a COP of say 1.7 to 1.9 costs you another $5k and you have to decide if that's worth it.
OK, I nerded out on this, because I find it an interesting question. I tried to model AWHP heat pump performance over a full year. My results are in a spreadsheet that is here:
https://docs.google.com/spreadsheets/d/1sIpGCu2Rkb-SqlzY0vw-DUIAQGv8KMxMXG3p1QjuAaQ/edit?usp=sharing
Please take a look.
My provisional result is that the COP you will experience depends on the size of the heat pump relative to the heating load. In the Whitehorse climate, a heat pump with a nominal capacity about twice the 99% heating load will give a year-round COP of 1.9. Smaller heat pumps give lower COP's; at 1x load you get a COP of 1.7.
Here's what I did:
First, I looked up climate stats at: http://cms.ashrae.biz/weatherdata/STATIONS/719640_s.pdf
For every degree between the break-even temperature (18.5C) and the 99% heating temperature (-37C) I estimated the heating load, the capacity of the heat pump, the COP of the heat pump, and how many hours a year we should expect at that temperature. If the heating load was greater than the heat pump capacity I assumed backup heat would make up the difference; if the COP was less than 1.0 I assumed backup heat would be used alone.
For heat pump performance, I used the figures that Chiltrix has here: https://www.chiltrix.com/CX34-air-to-water-heat-pump/
because they were the most complete I could find. If you look at the charts, you see that COP goes down as temperature goes down, and the capacity of the heat pump goes down as well. Looking at the graphs it looks very much like a straight-line relationship, so I just took the two endpoints and treated it like a straight line to estimate points in between. My calculation was that COP went below 1.0 at -33C.
To model heat load at each temperature I just made up a 99% heat load, and used a straight line between that and the break-even temperature.
To estimate the number of hours at each temperature each year, I assumed that temperatures are normally distributed. The weather stats gave me the average annual temperature and the 99.6% temperature. If they are normally distributed 99.6% would be 2.7 standard deviations from average, which allowed me to calculate the standard deviation of the distribution. Knowing the average and standard deviation I could calculate the percentages for every point in the distribution.
Chiltrix doesn't show any performance numbers below -20C. It might be that for some reason it can't go below that, so I tried turning off the heat pump for temperatures below -20. That only reduced the annual COP from 1.9 to 1.8.
Let me know what you think.
Awesome! The cooling degrees.net data will give you the distribution too, of days not hours. There are more warm days than very cold days
Degree-days were created for conventional heating systems that work the same pretty much regardless of the outdoor temperature, so you can use average temperatures. Since heat pumps' performance changes so dramatically with temperature you care much more about the extremes than the averages. That's why I tried to model hour-by-hour.
The big assumption I used is that temperatures are normally distributed. I don't know if that is in fact true. If I add up all of my degree-hours and divide by 24 I get 7100 for the year as opposed to 6600 from degrees.net. Which kind of makes sense, there will be days where on an hourly basis heating is needed but not an average basis. If I change my assumption for average or break-even temperature by a degree I can eliminate the difference and it doesn't change the big picture at all.
But the big finding is that when you look at hours rather than days there are a lot of hours when the heat pump doesn't run, or runs a lot less efficiently. The overall COP is quite a bit lower.
Hi DC,
I guess it depends what data base you have. If you have only daily averages, if you have this for the last 10 years (or not) - it depends.
I did that once for my house here and year to year differences are so big that the difference between worst year and average year is at least as big compared to degree-days and -hours.
Then you have the "thermal mass" of the house etc. (you know what i mean) and things like the black box called "HP control" . Is the HP also doing hot water? How?
You can get more than a gut-feeling but have to accept some limitations - i can still sleep well - at least the big mistakes can be prevented.
At the end I did HDD with the worst of the the last 10 years and called it a day.
regards
I think the hourly makes sense if you have the data. I think the issue is that these definitely don't appear to be normally distributed, so you'll be overly pessimistic on the seasonal COP. Here's what 36 months of HDD65F look like for Whitehorse, it is definitely not normally distributed.
Awesome work! This spreadsheet is a nice breakdown. I don't know if all the A2W heat pumps blend resistance vs heat pump power well or not. Chiltrix it sounds like is able to modulate their inline heater.
I am truly impressed with the level of knowledge being passed around by the group!
We're all still learning too.
I'm more of a fan of the air source heat pump but if you do end up going with electric resistance heating imbedded in the slab, I have seen a design where conduits are placed in the slab prior to the pour and then afterwards the heat tracing cables are pulled through the conduits similar to regular wiring. This design allows for replacing of the cables if/when they burn out. That's one advantage over installing piping in a slab. You just have to make sure to size the conduit large enough and the bends with a large enough radius to allow for pulling the cables. Good luck.
Interesting..you are only allowed a maximum of 360 degree (example (4) 90 degree bends) in electrical conduit, according to electrical code, and you are only able to have wire in conduit for 100ft before you need a junction box. That would mean you would either need a lot of junction boxes, or many home runs to make this happen. Unless there is a different way that I am not thinking of...
Electric resistance heating is not normally installed in the slab, it goes on top under the finish flooring.
The historic hourly data is useful for more than equipment sizing. I used it to calculate the humidity transfer from ventilation (via HRV) to understand how we might manage indoor humidity during our long shoulder seasons. As it turns out, in Vancouver BC it's worth upsizing an HRV to handle moisture removal during certain times - that is if you have the controls to monitor outside humidity but that's another topic.
Another thing to note: heat loss isn't exactly linear with respect to temperature differential vs design temperature (mainly due to the foundation), but when I summed up the hourly heat loss over the years the value was within 5% of the value predicted by HOT2000. So, more than good enough.
I, too, am looking at Arctic heat Pumps. One piece of advice they give in one of their articles is not to design the system based on the coldest temperature of the year - use an average over the course of the coldest month.
As to in floor electric heating or water filled tubes, I'm hesitant about burying a system in concrete. When it fails (eventually) it's unreplaceable. I'd rather do low temperature radiators. For back-up on the really cold days, I would use a direct vent propane heater set on a thermostat to come on only when needed (or if you're away in the winter and there's a danger the pipes could freeze.
Finally, in the Yukon, what effect would a warm slab have on ground containing perma-frost? I though most builders up in the far north recommend getting buildings up on piers?
There are certainly areas in the Yukon that do have permafrost, but that is about 6hrs north of where we live. The most common practice here is a crawl space with a pressure treated foundation.
I have attached my heat load calculation for our home design. I must say, y'all were very close with your 10KWh estimate!
Please let me know your thoughts. They adjusted the air changes per hour down to 0.3...which obviously is quite low. They said beyond that, backup heat would be required for the colder days, which I'm guessing is their electric resistance heating in the buffer tank?
I will attach two reports. One shows their heating load based on the -22F temperature limitations of their heat pump. The other shows the true heating based upon my location, and a design temperature of -41.8F
It's amazing that at 0.3 ACH50 infiltration still accounts for over a third of your heat loss. That's some cold!
I assume that -22F is where the COP becomes less that 1.0? That's within a couple degrees of where I figure the Chiltrix went below 1.0 in post #25.
Its truly amazing! I thought .6 ACH50 was good, but who knew.
I think your right, at -22F the COP becomes less than 1 and the unit shuts itself off.
The ACH values in the report are not ACH50 -- they are ACH natural. ACH50 is about 20 times larger and so 0,3 is about 6.0 ACH50
Well jeez! That is very helpful.
Thank you for clearing that up.
Ok, so I just got off the phone with the company. They are going to send me a updated version, with .75 ACH. I feel like .3ACH is just way too low. As much as I want to achieve a very airtight house, it dramatically changes the KW/h from one to another.
I believe he said that at the -40F design temperature, anything above .3ACH would require hotter water than the system can provide.
Thoughts? Still a little confused
With floor heat, the heat output is determined by the temperature difference between the floor and the air in the room. The floor temperature is in turn determined by the water temperature. The higher the heating load per square foot, the hotter the floor needs to be, and the hotter the incoming water needs to be.
Traditionally the limit was how hot you could stand the floors, which is about 90F. With a heat pump you also have to worry about how hot the water coming off the heat pump is. The rule of thumb is that a floor puts out 2 BTU/SF for every degree above room temperature. Looking at the calculations, you seem to work out to about 17 BTU/SF, which would mean a floor temperature 8.5 F above room temperature. I get that with 95 F water and 70F room temperature. However, there are two big caveats: first, the 17 BTU/SF is for the whole house, there are lots of places in the house like under cabinets or plumbing fixtures, stairwells, closets, etc., where you can't put floor heat. If you can only put heating under half the house then you need a lot hotter floors and water. The other factor is that's an average temperature, the water cools as it travels through the floor, to have an average temperature of 95F you might need water entering at 105F and returning at 85F.
Since infiltration is such a big part of your heating load, increasing the assumption around infiltration makes a big difference in the total load and may push you past the point where you can do the whole thing with floor heat.
Back when houses were a lot leakier this was a common problem, the solution is to supplement the floor heat with either radiators or fan coil units.
Here is the updated report with .75ACH50..
A comparison;
0.3ACH50 requires 34,373 BTU/H (10.07 Kw/h) with air infiltration accounting for 13,114BTU/h (3.84Kw/h)
.0.74ACH50 requires 54,114 BTU/H ( 15.85Kw/h) with air infiltration accounting for 32,798BTU/H ( 9.6Kw/h)
Would you agree that one can plan for a heating system, but until i did a final blower door test, or possible a pre drywall blower door test..it may be hard to size the final equipment accordingly?
When I built my house I had a friend who's a mechanical engineer advise me on the heating system. He wanted to oversize the heating. I explained that I was using a high level of insulation and air sealing. He responded, "Yeah, but what are going to do in ten years when it's not so tight any more?"
That kind of points up a problem with high-performance houses: it only takes small deviations from your assumptions to make big changes in the outcome. So the same effect is in play for the r-value of your walls or the u-value of your doors and windows -- if they don't end up performing the way you assumed they would your model is going to be way off. At least with air-tightness you can test the as-built assembly.
The assumption is that if the errors are random they will cancel each other out. But I would think in a very cold climate with a high-performance house it's unlikely that errors will compound in your favor. This is one of the reasons that heating systems are typically oversized.
In your case I think you have to prepare for a wide range of contingencies. There's a certain "it is what it is" aspect to construction, once this house is built you're not going to tear it down if the blower door comes in at 0.76 instead of 0.75. You probably won't know for sure how much it takes to heat it at -40 until the first night it hits -40. But you should be prepared for the contingency that it's much more -- or much less -- than you planned for.
Those are not ACH50 values -- they are natural ACH. The corresponding ACH50 would be around 20x larger which is quite leaky even at 0.3.
yes! for a proper tight house it is more important how many air changes YOU want to create a certain air quality. (by telling the ERV/HRV what it is supposed to deliver) Mind that in the winter the ambient air is quite dry and you want to limit the air exchange so that the humidity is not too low - and the 0.3 ach is typical. Unless you have a party with 10 guests and need to ramp up the ach..
If the btu's from the active floor is getting low (because of the sf or because the heat pump cannot deliver the hot water) - you can always incorporate a fancoil behind the ERV - then the lower water temp. can be ok. Also that will improve comfort due to pre-heating the air.
Regarding "an in slab system is too slow". Yes - if you are picky this is correct and a responsive system will create a more stable actual room temp. On the other hand, a proper hydronic system with low system temperatures (so low delta to the air temp.) will automatically have a lower output if the room temp. goes up due to external or internal gains. With less output the return water temp. is higher and the hp will switch off faster so it is not that bad. Yes, you have a bit of a temp. swing to the cozy side but who cares? That swing "up" is still stored in the house for a later time. If you use mainly outdoor reset and a balanced water volume per "zone/room", the house will be comfortable.
Note also that an in-slab system (because of its inertia) does not need the buffer tank for the hp if you go with outdoor reset only (and/or treat the whole house as one zone). To get the bath room warmer you can tighten up the pattern in the floor and put an extra loop into one wall so to match radiator area to heat load.
Do you need cozy feet or an efficient heating system??
regards
The problem is when your heat load goes up quickly and you have a swing to the non-cozy side.
For instance, if you have good solar gain. Check out this thread: https://www.greenbuildingadvisor.com/question/hows-this-for-solar-gain
where I talk about how last December I had a day when outside it was at my design temperature -- 21F -- and my heat didn't run at all from 10AM until sundown. My design heating load is about 30K BTU/hr, so when the sun went down my heating load went from zero to 30K almost instantly.
The footprint of my house is 2000 square feet. If I had a heated slab, to put out 30K BTU/hr that slab would have to be 15F over room temperature. A 2000 square foot slab 4" thick weighs about 75,000 pounds. Increasing the temperature of that slab by 15F takes about half a million BTU. At the maximum output of my heat pump that would take over twelve hours.
For best comfort you want your heat emitters to be as low capacity as possible.
I use mostly low heat-capacity emitters -- aluminum plates -- along with some fan coil units. Even so, on that day it took about an hour for the heating system to catch up when the sun went down and the inside temperature dropped.
There is a persistent misconception that concrete is the best material for heated floors. It's not even a particularly good material. You get much better comfort from something like WarmBoard which is engineered to have low heat capacity. Concrete also makes for a lousy residential floor. And it's terrible for the environment.
I am more than happy to look further into warm board. The slab on grade comes from the fact that the previous owner of the property has already completed the ground work for a slab, so I thought I would continue with that type of foundation.
Definitely look at WarmBoard, the only downside is that it's kind of expensive. The upside is that it's a replacement for subfloor and the framers should be able to install it. There are a couple of competing systems that are lower cost. What you want to look for is something that advertises itself as "highly responsive" or something similar.
I think if I were building on a slab in your climate I would put down 2x12 rim joists and frame the floor with 2x10 floor joists. Before putting in the floor joists I'd put down 1-3/4" of foam board insulation and then fill between the joists with R-38. Then WarmBoard or similar as subflooring.
In your climate I imagine you want your first floor up off the ground so you can open your doors when it snows. A foot may not be enough! Also it's handy to have that space to run wiring and plumbing.
When using an air-to-water heat pump with radiant floors you have to have a buffer tank. The thermostat has to control zone valves and not the heat pump directly. You have to have some way of keeping the heat pump from short-cycling when all of the zone valves are closed.
If you zone the house then I am with you. If you can treat the whole house as one zone - only then - then not. If your potential gains dominate the heat load then you are in a limbo - like in your house.
For milder overcast climates it is easier to simplify the system. Then, obviously, a house with less heat load and more emitter area has an advantage - but will be more costly to build.
Heat pumps are different from boilers.
With a boiler you can have a thermostat turn the boiler and circulator on and off. If you only have one zone you don't need a zone valve. With heat pumps you can't do that, you have to guard against short cycling. Even with only one zone you have to have a zone valve which is what controls the flow of hot water to the radiant floor. You have to have a buffer tank so that if the zone valve shuts off while the heat pump is running the heat pump can keep running. The temperature in the buffer tank is what triggers the heat pump to turn off.
If you have fan coil units you don't need a buffer tank, you have the thermostat turn the fan on and off while the water continues to circulate.
one zone/loop in a concrete slab is its own buffer. Beside that it is a control issue. Let the circulator run all the time, whenever the return temp. is low (against an outdoor reset value) then run the hp. A minimum run time for the hp after each start is very doable. When the hp is "off", the circulator can run at a slower speed to save energy. For a defrost cycle, the hp can rely on the slab.
And yes - if internal or external gains happen, the house will overheat a bit - but will not drop into a hole when these gains disappear.
(responding to #65)
I have a Chiltrix air-to-water heat pump. It has outdoor reset. The heat pump itself operates off of the return water temperature as you describe.
What you describe is not a sufficient control mechanism. In order to keep the internal air temperature constant, you have to have something measuring the internal air temperature and reacting to it. You need a thermostat. That thermostat has to control something. In the manual for the heat pump it says you can't use a thermostat to turn the heat pump on and off. You have to instead turn off the demand for heat, which means switching of a zone valve so that the water no longer circulates and is no longer being cooled. Instead that water goes into a buffer tank. I'm not making this up, it's right there in the manufacturer's instructions.
I'm old enough to remember when radiant floors got big in the 1990's, I installed my first radiant floor over 25 years ago. There was a lot of "wisdom" circulated back then that turned out to be utter nonsense. One of the nonsensical ideas that was promoted was that radiant floors were somehow self-regulating. No, not if you care about comfort.
Your statement that "if internal or external gains happen, the house will overheat a bit" is exactly the kind of hand-waving that went along with that magical thinking. I installed my system following the manufacturer's instructions and it keeps my house within half a degree of the thermostat setpoint all winter long.
A heat pump can work without a buffer tank in an in floor setup if the zones are sufficiently large.
Paul --
It's really a misnomer to call it a "buffer" tank. It's a bypass tank. It's required because there's no way to circulate hot water in a heated floor and not have it give off heat. The only way to turn off the heat is to turn off the water flow. You need to have some place for the water to go when you've turned the floor off and the heat pump is still running.
The size of the floor is irrelevant, because the purpose of the "buffer" tank isn't to reach some minimum capacity, it's to allow the heat pump to run while you're no longer calling for heat. As I noted above, if you're using fan coil units you don't need a buffer tank because you can continue to let the water circulate and turn off the fan when you want to turn off the heat output.
Dear DC,
I am not familiar with the Ciltrix. I know (mostly modulating and some fixed speed hp) installations here in Germany. It is standard here to go into the slab without buffer tank. (a buffer tank would only be used on some systems for the defrost cycle, some use the slab to provide the energy for that) You have outdoor reset, some systems use a room thermostat to modify this reset. Code requires a zoning with local thermostats and zone valves but you can get a waiver for superinsulated houses. If the lower modulation limit is still too much heat, the hp will rather stop. Modulation and outdoor reset have to control this behavior to have sufficient run time.
It is not an ideal world - you sacrifice the best temperature stability a low mass emitter can deliver - no problem with your statement. But it still works.
Are you suggesting a floor assembly similar to this?
For what do you need the 2x6 joists? The concrete provides the stability ?!?
Look around here, a lot of examples. Like
concrete + 1-2" low compression EPS (+ sleepers or floating) subfloor + radiant heat system + hard floor. A 6 mil poly either above or below the eps if the concrete had no time to dry..
Something like that needs less height, is better in R value (continuous insulation) and also very doable
(Responding to #72)
As I noted in #56, in a low-load house a concrete slab is essentially unregulatable. The slab holds so much heat relative to the heating loads that even if you had a thermostat it wouldn't matter because the slab would take many hours to respond to changes in the thermostat. So I read what you're saying as simply acknowledgement that a thermostat is pointless in that situation so it is not required.
I agree, code minimum here in the Yukon is 1.5ACH/50
Post #50 raises a really good point, the ACH numbers used are ACH natural. In post #43 I marveled at how high the infiltration losses were; I assumed that was due to the extreme cold -- infiltration losses go up with the square of the temperature delta -- it didn't occur to me that they could just have been miscalculated.
The standard assumption is that infiltration is driven by temperature difference and is linear to temperature delta. I don't know where the numbers come from, but in my climate -- 20F heating temp, 92F cooling temp -- we use 0.041 times the ACH50 as the ACH natural for heating and 0.014 times the ACH50 as the ACH natural for cooling.
Extrapolating out to -42F I get a multiplier of 0.097 ACH50 for ACH natural. Basically one tenth. So take the numbers given and divide by 10.
Reading the report I now see it says "Air tightness: Average (1946-1960)." Sheesh.
Yes, there was some confusion. In the email, he wrote 0.3Aacah/50.. but that was clearly a mistake.
Yukon has a code minimum of 1.5ACH/50, with a mandatory blower door for any new buildings.
The report also seems to assume constant mechanical ventilation of 100 CFM, which is a loss of 4800 BTU/hr. I would assume that in a -40F climate you'd have a heat recovery ventilator. I would also look into having it triggered by CO2, VOC and humidity sensors rather than running continuously.
OK, they are assuming an HRV effectiveness of 60%.
At the design temperature I get infiltration around 20 CFM, which would be a reason to reduce ventilation and have it run on a sensor.
Yes we will have a ERV in the house.
I am fully on board with having the ERV controlled by CO2, VOC and humidity sensors. The Broan Overture sensors look like a great option.
#70 reply. You can circulate a tiny bit of water once the thermostat turns off the heat pump with little overheating - it’s just not much heat. For example: say 1200 ft of 1/2” tubing, that’s only 11 gallons. With a 20 F delta T, that’s 1800 btu. Yes, it’ll heat the room more than the thermostat told it to, but it probably won’t even change the thermostat reading.
There’s not much short cycling concern if you have a large, infloor zone.
The thing is the thermostat doesn't turn off the heat pump. In the Chiltrix manual they tell you explicitly not to wire it up that way. The reason is twofold: first to avoid short-cycling, but second so that the output of the heat pump can be modulated to meet the load.
What turns off the heat pump is the water returning reaching the temperature where the heat pump controller decides it can't modulate that low and must turn off. In order for that to happen you have to have some way of turning off the floor, because it's going to continue to lose heat otherwise and the return water temperature is never going to get high enough. So what has to happen is the thermostat turns off the zone valve. The heat pump continues to circulate water through the "buffer" tank. The buffer tank heats up, and then the heat pump turns off when the water coming from the buffer tank is hot enough to trigger it to shut down.
There's a method in the madness. The way the heat pump "wants" to run is where it modulates its output to exactly match the heating load, it runs continuously at constant output. This is the most efficient way of running. The way it modulates is to look at the temperature of the returning water and try to adjust its output to keep the returning water at a constant temperature. So long as the heating load is higher than the minimum modulation level for the most part the heat pump will run continuously.
The buffer tank only comes into play when the heating load is less than the minimum modulation level, and the heat pump has to cycle on and off rather than modulating. Again, "buffer" is a misnomer, the purpose of the tank isn't to buffer as it's commonly understood, increase the water capacity of the system. It's to give the heat a place to go when there is no demand for heat, and allow it to accumulate so that it can trigger the heat pump to turn off.
DC,
I think I see the difference.
For you the outdoor reset is put slightly above of what is needed for the heatload, so the hp HAS to shut down because zone valves WILL close. In order to do that in the way you describe (return above a certain limet - outdoor reset - typical difference "supply-retun" + hysteresis) you need that bypass tank as indication - you want to generate that switch-off with zone valves closed.
That way you have a robust system, all zones (can) have thermostats and for a user the thermostat is what you have to look at and control. Small mistakes in outdoor reset stay hidden.. Disadvantage is that extra hardware (tank + some zone valves) and the slight hit in efficiency due to the higher outdoor reset.
I meant a system with some zones without dedicated zone valves. Lets say a house, areas which will tend to "overheat" etc. with zone valves/thermostats but like 50% of the load NO zone valves - maybe a thermostat (a meter to the control). "My" outdoor reset is set at the steady state "no extra gains" temperature to satisfy the load and not above. When the buildings becomes too warm, the return will also eventually go above a certain level. If the control is set up properly then you have also your shutdwon signal - but without the extra tank. You can shift the outdoor reset curved if the actual temp. is always slightly off - that is a slow extra control "on top" the outdoor reset. (or change outdoor reset manually) Maybe the hysteresis here is lower than what some controls used - ok.
I understand that such a system needs some babysitting during commisioning and first use and that this is something only "experts/nerds/home builder" might tackle - so a niche market.
From a pure BS perspective this is still very doable and the more effcient system - all I am saying. Whether it is worthwhile is up to the energy costs etc..
A warm welcome from my side.
Thanks wastl --
So here's the thing about that control system. Imagine a house with a 30,000 BTU/hr heating load. The design is for the load to be met with water supplied at 100F, returned at 90F. Average water temperature is 95F, floor temperature is 10F less, room temperature is 70F. The shutdown signal is set for returning water temperature of 95F or above.
Then imagine that the heating load drops by 10,000 BTU/hr. This could be because of sunshine, or a lot of other factors -- that's only about 3,000 Watts, so it could be using the oven or the dryer or even two hair dryers. Or you have a gathering with 15 people.
So now you've got a heating load of 20,000 BTU. Same 100F supply temperature, but 95F return temperature, so average water temperature is 97.5F which gives a floor temperature of 87.5. If you were getting 30,000 BTU/hr with the room at 70F and the floor at 85F -- a 15F delta -- to get 20,000 BTU/hr you'd need a 10F delta. With the floor at 87.5 that gives a room temperature of 77.5F.
That's a pretty big swing. In this country hydronics is a premium system and commands a premium price, I don't think people would consider that premium performance.
I'm going to amend my answer a bit. As the interior temperature increases the heat loss increases too, so I need to account for that too. Taking that into consideration I land on an inside temperature of 75.8F and a heating load of 23.5k BTU/hr.
That represents an increase in heating cost of 17%.
Dear DC,
I hear you. If you wait till 95F then this will happen but why do you have to?
If you need that hysteresis, if you control is that coarse. Shut down at 92F (as an example).
In a way - with the zone valves closed you hide that excess hp power from the house and translate it into a temp. swing your control system can react to.
Lets say we assume a 2000 sf house, 4" slab, even distribution and average slab temp etc. then with the 10000 btu/h excess heat you have like 7F rise of the slap temp per hour (we disregard any different energy loss from the slab to the house) The house is heated by the extra gains, so the slab will loose less heat than before and heat up even faster (same with the return temp.) As you wrote we have no perfect conductivity in the floor so the room will see that later and as a reduced raise (and the return will go up again) so in beginning the swing in the room is small(er). And then the effect you mention because of the higher heat loss from the building.
What I want to say is that the return will see a raise in temp above the 90 before anyone will be annoyed. If your control can react that precise then all is fine.
The hp had at least 20 min run time (most probably some more because it did not start exactly when the sun came through) and you are safe. With a modulating heating pump reacting to the higher return immediately even more.
For a fixed speed pump I have no problems with your configuration, for a modulating one it is different.
For sure, here such a (modulating) system is standard and people do not expect a premium - they would take any performance as given.
edit: ok - we use here normally a concrete screed to cover the hydronic loops which is maybe 2" thick so the reaction is faster - but still slow against a low mass emitter.
(Reply to #82)
That actually sounds like how the Chiltrix works. At any given exterior temperature it has a target for delivered water temperature and return water temperature. It has a variable speed circulator so it modulates the water flow rate to try and hit the targets, if the return water starts coming back too hot it slows the circulator down. It also modulates the compressor to match the heat load of the water flow rate. If it gets to the point where it is modulating as much as it can and still the return temperature is higher than the target it cycles on and off, and keeps the circulator going, cycling on when the return water dips below the target and cycling off when it goes above.
I agree that such a setup would work without a buffer tank. Somewhat. It's entirely possible that the Chiltrix was actually developed to be used in this way.
But think about what is happening: if the heat pump is successful, it is keeping the supply and return water temperatures constant. The temperature of the floor is determined entirely by the water temperatures, so the temperature of the floor is kept constant. The amount of heat flowing out of the floor is determined entirely by the temperature difference between the room and the floor. If the heating load is varying, and the floor is at constant temperature, it is the temperature of the room that is modulating to adjust for variations in the heating load.
I think most people would find it preferable instead that the temperature of the room be kept constant and the temperature of the floor be modulated to compensate for variations in the load. To do that you need some sort of temperature sensor in the room. A very simple way it to have an on/off thermostat attached to a zone valve. But if you do that you have to have a buffer tank for when the zone valve is closed-- or all the valves are closed, in a multizone system -- so that the heat pump doesn't get deadheaded.
The buffer tank is essentially an ultra-low-load zone so there's always at least one zone open.
(Replying to #74)
Here is my best try at a sketch:
Black is vapor barrier, gray is concrete, blue is foam, yellow is batt insulation. I drew the subfloor and floor as a single piece for simplicity.
Against the stud wall is a 2x12 that is sitting on the concrete. Attached to it are 2x10 floor joists. My thought is to have them hung from the 2x12 like regular joists so that the flatness of your finished floor doesn't depend upon the flatness of the concrete and that there's space below them for continuous insulation. A 2x10 is exactly 2" less than a 2x12, but I went with 1-3/4" of foam insulation (blue) so that if the concrete isn't perfect it doesn't make hanging the joists a pain. You could go with smaller lumber, but since the joists are hung I thought you'd want to have a decent span. There's no reason the joists have to span the whole structure, you could have them supported by partition walls. I think you will also appreciate the height when it's time to run plumbing and electrical.
You could frame and dry-in the whole house before putting in this floor, which would allow you to have the concrete dry for several months. You could also do most of your rough plumbing and electrical before the floor goes down.
This is more insulation than is required but I think you will appreciate it.
Here is an updated report showing a more realistic ACH.
As you can see air infiltration has dramatically been reduced.
That looks better. I'd argue your ventilation number is still high, if you need 0.28 ACH and you're getting 0.18 from natural infiltration then the ventilation only needs to supply 0.10, about a third of what's listed. If you have sensor-driven ventilation it should automatically adjust.
But that's quibbling. Under 30K BTU/hr for that far north is impressive.
After getting frustrated at designing the system I'm due to install in about a month, I found this post and I have to say, you all have made me nervous about installing in-slab radiant in Central NY. I'm two zones warmer than Yukon but some of these responses about the temperature swings are a bit yikes on those coldest nights. I'll probably still bury the pex anyway because warmboard is prohibitively expensive and pex is cheap, so even if it doesn't get used down the road its not a big deal, but I'm now thinking I should get a backup electric furnace since I'll have forced air ductwork anyway. I just hate that I'm already looking at twenty grand just for the components, before duct work.
If you have the ductwork the easy thing to do is put in a heating/cooling heat pump rather than just air conditioning. That shouldn't add much to your cost, and it allows you to downsize the hydronic a bit if you want. In the winter set the thermostat on the heat pump a little lower so it only kicks on when the hydronic isn't keeping up.
The big thing to increase the responsiveness of your hydronic is to reduce its heat capacity. Generally that means thinner concrete if you can get away with it.
Note that in upstate NY if your ductwork is sized for cooling it's almost certainly too small for heating. That's OK if it's supplemented by the hydronic.