Azek trim question for carpenters
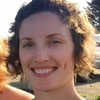
I have a question for carpenters experienced in using Azek pvc trim. I am building my own house and learning as I go. I have 2×6 subfascia and am about to put up 5/4 x 8 Azek for fascia boards and 5/4 x 4 Azek for shadow boards/build-outs on top of the fascia. I have been reading about what the best way is to fasten it to account for the expansion/contraction of the material on long runs (I’m in coastal Maine Zone 6), and I have found some old thread comments on FHB from Mike Smith of RI who suggests leaving unglued shiplap style joints in long runs and butt joints for corners. I am using SS trim screws for fasteners and am planning to glue the fascia board to the subfascia with construction adhesive and will fill the screw holes and paint it all. My question is for the shadow board – do I glue/weld it to the fascia with either construction adhesive or Azek glue and treat them as one unit, making the joints in the same places as the fascia board? Or do I not glue it to the fascia/or just construction glue it and treat it as its own unit and stagger the joints away from the fascia joints? Do the smaller boards expand differently than the larger boards? I had planned on a 3 row fastening schedule with the bottom screw only going through the fascia board and the top two screws going into the shadow board and through the fascia board (is that a bad idea?). That leads me to think I should weld or const. glue them together and make the joints in the same places but I don’t want to screw it up! Thanks for any advice!
Generic picture included of shadow board on fascia for reference
GBA Detail Library
A collection of one thousand construction details organized by climate and house part
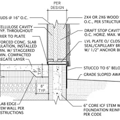
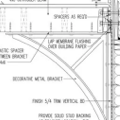
Replies
K, I'll bite. Would love to hear others' opinions on this too.
"...planning to glue the fascia board to the subfascia with construction adhesive"
I was typing out that I would probably not bother with this - screws will hold it fine, and I'm not sure construction-adhesiv-ing the fascia to the sub fascia gets you much.
And then I Googled it, and Azek actually does recommend gluing to a substrate (page 3):
https://azekexteriors.com/docs/installation/azek_trim_moulding_installguide.pdf
"Do I glue/weld it [shadow board] to the fascia with either construction adhesive or Azek glue and treat them as one unit, making the joints in the same places as the fascia board?"
If you did this all on the ground, the glue up should be easy enough, but it will be heavier to lift into place to install. Not sure gluing gets you much, though, and you'd want to clamp it till it sets up. Joints between runs might be trickier this way.
"Or do I not glue it to the fascia/or just construction glue it and treat it as its own unit and stagger the joints away from the fascia joints?"
I'd install fascia then shadow board separately, staggered joints.
I probably wouldn't glue the two together, but (see above) I might be wrong on that.
Definitely glue the joint when you're joining runs together.
Fine Homebuilding's Instagram just had a good video about PVC trim joints, basically a shiplap joint + PVC glue. Azek shows a scarf joint in most of their documentation, but the FHB solutions seems slicker (and probably easier to get right).
"I had planned on a 3 row fastening schedule with the bottom screw only going through the fascia board and the top two screws going into the shadow board and through the fascia board"
This sounds fine to me, just use long enough screws that you're getting 1 1/2" penetration into framing / substrate when screwing through the shadow board - so, 3 1/2" screws or something.
I prefer solvent welding, but I'm not going to comment on the "how much it moves" type questions since I haven't worked with large enough pieces to be certain how to answer that. If you do a good job with a solvent weld connection, it should all behave as one big piece. Solvent welding usually has less risk of discoloring the material too.
BTW, the process of how the solvent weld works on the molecular level is interesting. Years ago I read something about it, and what happens is the solvent frees the ends of the polymer chains in the materials, which then intermingle (I always imagine this as seagrass or fine algae strands swaying around gently in the waves). When the solvent evaporates, the polymer chains become locked together in what is basically a massive tangle of molecules.
Bill
Thank you Paul and Bill for your answers. The JLC thread that got me worried about welding or gluing the joints was here: https://forums.jlconline.com/forums/forum/jlc-online-expert-forums/exterior-details/40550-repairing-azek-joints?t=45547. The Azek glued joints on the guy's house broke the material apart in jagged cracks when it got really cold suddenly. But it's an old thread and Azek does recommend gluing the joints but seems to also suggest leaving expansion space at the ends of the run.
The local lumberyard today recommended not gluing the shadow board to the fascia because it would make it slippery and hard to put up. If I were to weld them together then I feel like the joints need to be in the same places so they can move as one unit. Azek says to glue the board to the substrate but they don't mention what to do if the substrate is Azek. I think I am leaning toward not gluing the top board down and staggering the joints. Thanks for your help!
Hi jwalker-
I'm curious what you ended up doing. Coincidently, I'm in Maine and also getting ready to install fascia with a shadow board. I had reached out to Azek to clarify their recommendations for this type of installation. Their response:
"The minimum recommendation would be to mechanically fasten the AZEK. It could be beneficial to use adhesive. When bonding AZEK to AZEK you will need to use a cellular PVC cement. When bonding AZEK to a substructure you will need to use a non-silicone based construction grade adhesive."
Regarding adhering PVC to the wood substrate: I'm a bit of a skeptic regarding the long-term effectiveness/benefit of gluing thick PVC to a dissimilar substrate (with high differential of thermal coefficients of expansion). My concern is more gut-feel than fact based. I've done a fair bit of furniture making and metalworking - movement almost always wins.
If I end up using PVC for the fascia I'll likely not adhere the PVC fascia to the wood sub-fascia, I'll also not adhere the PVC shadow-board to the PVC fascia. I'll just solvent weld the joints.
Currently, I'm actually leaning toward using wood for the fascia ;-). Anyone else have any feedback/ experiences regarding using PVC for fascia? -I'm interested in longer-term performance/results after many seasonal thermal cycles.
Sorry I did not see this until today! I ended up using a combination of techniques. The Azek fascia is 5/4 x 8 with a 5/4 x 4 Azek shadow board. I'm planning to paint the trim so every piece was sanded to remove the shiny coating. I used stainless trim screws throughout every 12" and filled the holes. I put construction adhesive on the wood subfascia, then hung the fascia board with two rows of screws. I decided to go with lap joints in the field, which I routered and glued with construction adhesive, and added plenty of fasteners around them. I figured I wanted them to be firm but be able to move if needed so I didn't use Azek glue there. I will fill with caulk before painting. For the corners, I started out (on the back of the house!) with butt joints but didn't like them so I mitered the rest. I followed the advice in this article https://www.finehomebuilding.com/project-guides/siding-exterior-trim/pvc-roof-trim and cut my miters at 46 degrees a little long, and used Azek glue, with trim nails to hold while the glue set. Where the rake boards hung lower than the eave boards, I drew a level line across it even with the bottom of the eave board and cut it afterward with a circular saw and sanded it smooth. A lot easier than trying to cut them perfect ahead of time for a beginner! I then hung the shadow boards on top of the fascia boards without glue, with 2 rows of longer screws long enough to penetrate through both boards into the wood. I staggered the lap joints. I'm putting gutters on all the eaves so I didn't have any mitered corners for the shadow board. I Azek glued the angles and just did butt joints there. I think it came out pretty good for someone who's never done it before, besides a few small mistakes!
I used PVC trim for one project where the longest run was maybe 12'. The installation was in the summer, peak heat. When winter came around, with a max temperature differential of about 70F, I had gaps that you could fit multiple quarters in, even those where I had left an appropriate space and filled with caulk. When summer comes back around, they close up. It was terribly aggravating, but since it was a personal project I just let it be.
I spent a lot of time thinking about how to mitigate it, and I think if I had to do it over, I'd make solvent welds on all junctions, and make lapped cuts maybe 2 ft on each side, un-caulked, with a style cut that I'm going to try to draw out in text.
(solvent)
-----------------------------------------| | ------------------|---------------------| | -----------------------------
-----------------------| |-------------------------------------|----------------------------------------| | ----------
That would have kept the corners and joints tight, and allowed a lapped joint that was free to open and close as the temperature changed, but minimized the cut look elsewhere.
I built two large houses on the beach in Saco 15-20 years ago with 100% PVC trim and to the best of my knowledge only one or two joints opened up, and those did not get the treatment we used on all of the other joints: 2-3 rows of stainless steel screws on each side of the joint, tightly-fit, 45° scarf joints with PVC cement, long boards snapped into place if it was hot out but just the right length if it was cold during installation.
It's a lot of steps to get it right, which along with the many environmental downsides has led me to avoid PVC trim ever since then.
Here's an article about some of the details on one of those homes: https://www.finehomebuilding.com/2008/01/17/a-balcony-deck-built-to-last.