Baffle depth

Zone 6 Mpls
Have a traditional 2 story with an unconditioned attic built in the 40’s. This past summer when we had siding/roof replaced we popped the facia behind the gutters and cut holes between each rafter. As you can see this was not a perfect science in terms of the symmetry of the cuts as we had tounge and groove 1×4’s over the rafter ends. However we were able to get some decent sized openings cut in.
As with most retrofits situations access from the inside the attic is ok, though not ideal. You can see in my attached picture I can get at the toplate and I have removed the blocking over the rafters to allow me decent access into the soffit area. I also have blown celluose between my rafters of the attic floor Questions are ( I have read as much as I could of Martins’ Site Built baffle article, rest is behind paywall)
What is the min depth should the site-built baffles I make be relative to the roof sheathing? Some say 1″ other suggesting 2″ ?
I can either place a piece of 1″ XPS vertically on the backedge of the toplate (prevent wind washing) and then run my XPS built baffle to it, using sprayfoam where they intersect and on the sides of my baffle similar to the attached pic that Fine Home Building uses in their article.
OR
Friction fit a piece of 2″ over the toplate and use a piece of vertical XPS as described above. My rational for going this route is the I am not sure how much cellulose I can stuff bewteen the toplate and the baffle and figure if I cut piece of XPS and place it over the toplate it may give me a bit more R value then just straight cellulose. (though is more work and want to make sure its worth it)
Assume 1″ XPS will work for making the baffles. I have some left over from another project.
GBA Detail Library
A collection of one thousand construction details organized by climate and house part
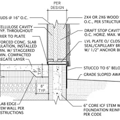
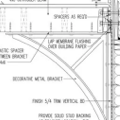
Replies
Minimum baffle size for air flow is 1 inch, 2+ inches is best.
You want as much insulation over the top plate as the thickness of the wall, minimum. 2x4 wall, 3 1/2 inches is best, if it can be achieved. The more the better.
MS,
The first thing you need to do is calculate the amount of eaves ventilation your attic requires. That will inform how deep the baffle needs to be
Malcolm
I am guessing that calculation is beyond my pay grade. I will shoot for 2" deep channels.
MS,
2" will be fine. The technique you suggest will also be fine.
I am mostly intrested in whether the technique I described is the right track
When the plan is for loose-blown cellulose, you needn't build your own rigid baffles. There are plenty of inexpensive vent baffles off the shelf at the box stores that will save plenty of time and effort made to fit 16" and 24" rafter spacing, and if you seal the perimeter they control wind-washing just fine.
Make sure to seal the top plates well inside and out--a whole lot of air leakage happens there coming from the interior space below. Stopping air leaks at that top plate matters WAY more than the R value or the size of the air gap above it.
@jason S Do you have any rec's on brands of baffles. Hard to explain, but over the top of the floor joists I have wood planking. To attach the planking in the soffit area they placed 1x6's on the side of the floor joists so my rafter spacing is not really 16" or 24". I will have to modify either way. Might be easier to go the XPS route
I think what I used was Durovent with canned foam at the bottom and sides. Nothing special about them. They're pretty flimsy but do the job fine if & when they fit well. Pull a tape and trust your own judgment on that. You may well be better off with the scrap foam you have on hand if they would require too much trimming.