Basement insulation

I am installing 2×4 walls in a 100 year old house in Chicago. The basement walls are made of four courses of brick and are somewhat porus. There are no leaks but moisture vaor does pass through he walls even though they are sealed with paint. Can I frame the walls, install fiverglass insulation and drywall and have the dehumidifier continue to keep the basement dry?
GBA Detail Library
A collection of one thousand construction details organized by climate and house part
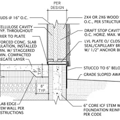
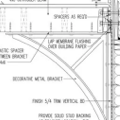
Replies
Matthew,
Q. "Can I frame the walls [in my basement], install fiberglass insulation and drywall, and have the dehumidifier continue to keep the basement dry?"
A. I don't recommend that approach. If you want to insulate the interior side of a basement wall, you need to use rigid foam or closed-cell spray foam. For more information, see this article: "How to Insulate a Basement Wall."
Hi Matthew -
I don't disagree with Martin's recommendation but you asked if you COULD install fiberglass and gypsum board in your basement.
1. So long as you keep the entire new assembly vapor open, and you ONLY have vapor by diffusion to manage, you can rely on the dehumidifier to manage your basement moisture.
2. I don't recommend that you use paper-faced gypsum board in a moisture situation such as your basement. Use a non-paper faced gypsum board such as USG Fiberock or GP Densglass, both less moisture-prone and vapor open.
3. monitor your temperature and relative humidity to be sure that you are well away from combined temperatures and relative humidity that support mold and mildew.
Peter
Longevity or mold-farming potential aside, a 2x4 wall with fiberglass or rock wool insulation would not meet the current IRC code minimum thermal performance requirements. Chicago is in US climate zone 5, where the last few versions of the IRC prescribe a minimum of R15 continuous insulation, or R19 if between studs, or U0.050 (= R20 "whole wall", including the thermal performance of the brick, wallboard, and interior side air films, and the thermal bridging of any studs.)
Installing 3/4" foil faced polyiso or 1.5" of EPS between the studwall and foundation with R13-R15 fiberglass in the stud bays would hit that performance minimum, and would have sufficient dew point control on the above grade section to allow the use of standard interior latex paint as the interior side vapor retarder. If using polyiso, stop the insulation an inch or so above the floor to limit the potential for it to wick up ground moisture from the slab.
Installing an inch or more of EPS under the bottom plate of the studwall is an adequate thermal break to keep it from taking on summertime moisture from the indoor air, as well as a capillary break against ground moisture coming up from the slab. It's fine to install the bottom plate EPS underneath the wall foam, but leave a half inch or more of clearance to the wall to allow redistribution of any minor bulk water incursions.