Basement insulation

Hi! I appreciate all the forum advice I get from your organization. I am seeking to take over my Dad’s residential construction business and I am designing my own house which we will build in a few years. I am in college to do so and am learning an awful lot. For basement insulation, I narrowed down some ideas that I would like to go with. To let you know some of our practices, we dampproof our basements and run drains around the perimeter just in case. As for the insulation, upon much research, I have found that it is best to use sub-slab insulation. We live on the southern edge of Zone 5. As for the walls, I’m considering using a thin layer of EPS for moisture control on the interior (to avoid having to mess with termites), then finish the rest with Polyisocyanurate. I don’t want to finish the walls right away, but just insulate them, so I heard polyiso is acceptable in case of fire. EPS and Polyiso are much better for the environment from what I’ve read, so that’s what I want to stick with. Any thoughts? I would appreciate your advice.
GBA Detail Library
A collection of one thousand construction details organized by climate and house part
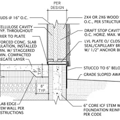
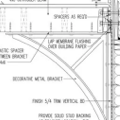
Replies
I'm not clear on how EPS is supposed to manage termite? Termites and other wood boring insects tunnel through EPS fairly readily.
Polyiso works just fine on it's own as long as it has suitable facers to prevent wicking of moisture from the concrete, and the concrete is reasonably dry.
I also thought if moisture came through the block wall it could cause the Polyiso to have less R value. With the damproofing it may not be much of a concern, I don't know.
.
No. Sorry. I'm avoiding insulating on the exterior of the wall to avoid dealing with termites. Thus, I'm putting it on the interior of the block wall. Another reason I don't want to insulate the outside of the wall is that if I use EPS I would need an incredible thickness to achieve my R Value, and thus I would have to extend our sill plate on the first floor above out farther to cover the insulation while using a wider 2x as a sill plate, which would get costly. You're saying that I don't need the EPS? I saw a few websites saying the polyiso shouldn't be run down to the base of the wall because of moisture. That was my concern. If I can just use Polyiso, that would be great!
Golf,
The practices you mention -- installing dampproofing and a footing drain -- aren't "just in case." They are code requirements. Omitting them would be illegal.
For information on insulating basement walls, see this article: How to Insulate a Basement Wall.
Resting the cut bottom edge of polyiso on a slab has some risk of moisture wicking, but the facers (even asphalted paper facers) are sufficient protection from any moisture in the foundation wall. As little as 1/4" of air between the cut bottom edge is a sufficient capillary break, as is filling in the bottom inch or so with EPS instead of polyiso.
Slab insulation of 2" EPS (R8-ish) is rational on a lifecycle basis in zone 5 even for unfinished basements, as it stubbing up with 2" of EPS for the entire slab perimeter, thermally breaking the connection to the walls. In high termite-zones there may be some rationale to covering over the perimeter foam with a termite blocking material such as strip of copper flashing or copper tape, even at the cost of the thermal bridge that would create. (Copper is a preferred material, since it kills the gut flora that termites need to digest wood.)
Ha ha Martin. Sorry. I don't know what the IRC says as I am not yet running the business, I just know what we do. I should have known it though. Yes. Dana. Thank you! So, what I can do is apply the sub slab EPS, then run the perimeter EPS from the sub slab insulation to an inch or so above the slab. Cover EPS with copper on exterior side if need be? (I'm from southcentral Pennsylvania, but I have seen termite damage.) Then run polyiso on top the EPS on the rest of the wall? I'm glad I asked you all. It sounds reasonable, but how do I protect the EPS at the base from fire? Parge it with a layer of cement?
Trim the EPS flush with the slab, copper tape the top so none of it shows. Cover the cut bottom edge of the wall foam with flashing tape and let it rest on your EPS/concrete. The edge tape is a good enough capillary break, and the copper is a good enough termite barrier.
With 2" slab-perimeter EPS and 2.5" (the amount necessary to hit an IRC code-min R15 in zone 5) the EPS will be completely covered by the polyiso. If it's fire-rated polyiso it will serve as the ignition barrier for the EPS it is covering. Make sure your local code officials are on-board with this, since not all will accept fire-rated polyiso in an unfinished basement.
So I think what you are saying is ,"Place the sub slab EPS, then place perimeter EPS a bit higher than where the top edge of the slab will be. After slab is poured, trim perimeter EPS flush to top edge of slab. Cover cut edge of EPS with copper tape, then polyiso is 2.5 inches to code so it will cover the EPS and tape. I will have to see if our code official is okay with the polyiso. He's an engineer, but I hope he allows it. Thank you very much. Let me know if what I said is correct.
I'd also extend sub-slab plastic sheet up a bit such that if water ever runs down the wall, it is directed underneath the slab (vs out on the floor).
Golf,
I would step back from the design phase and focus instead on learning as much as possible about what goes into building a pretty good house. This site contains a lot of relevant information on that topic.
When specifying polyisocyanurate that will be left exposed, Dana reminds you to use a "fire-rated" product (that is, if your code official is on the ball.) The polyiso in stock at the big box is most likely the down-market version that is NOT fire-rated. After all, they're all about the lowest price. You'll find that polyiso with an approved facer is available, but at a much higher price point by special order. For example, the big boxes typically stock TUFF-R by DOW, but you'll actually need their more expensive Thermax. If you're buying from a recycler, you're way ahead on price but many times those boards are completely unidentifiable.
One possible way around this problem is to build up your insulation thickness in multiple layers (better for airsealing anyway), then pay for premium ignition barrier only on a thin inside visible layer.
Golf,
As a first step to every decision you will make building houses and running a construction company, you need to know what the building code requires. That comes before branching out into what you think is desirable or a better way to do things.
As Martin intimated, You need to know what the IRC says about basements before you design one. You also need to know you don't include perimeter drains "just in case", but because you are required to. Knowing the parameters of any problem makes solving it a lot simpler.
Good luck with you career!
IRC section 405.1, ..."Exception: A drainage system is not required where the foundation is installed on well-drained ground or sand-gravel mixture soils according to the Unified Soil Classification System, Group I soils, as detailed in Table R405.1."
I believe this is in your state code.
Im going to guess you were talking about laying perforated drain tile? A "porous" layer (stone) and sump is all that is required in soils other than Group 1 per R405.2.3, if your state is still based on 2009 IRC. I think 2015 IRC has the exact same provisions. It will vary state to state.
There may be provisions for municipalities or code agencies to require otherwise.
You should have a copy of your code, if you dont you need to get one and know it and never trust internet code advice including what I am telling you right now, check for yourself cause it's your butt on the line when it matters.
Well. ha ha. You all are getting a bit more technical than I originally was thinking. I just saw Martin in a post state that the drains may not be required, but I'm sure my Dad has thoroughly checked that out for our area. Also, I've been told by my Dad and the log home company that I'm going to work with that I need a walk out basement by code. What do I do there? Make the block opening 8" wider and place the polyiso on either side, then frame the opening out with a stud wall for the doorway? How do I insulate that? If I'm including multiple layers of Polyiso, I will need to cover the top of the foam at the sill plate with a layer of thermax to cover the back layer(s) as well for fire protection (just trying to be as thorough as possible). JON R. Yes! Instead of placing the vapor barrier under the stone like we do with crawlspaces, I saw that it needs to be on top of the EPS, but is the water supposed to go down the wall and behind the plastic sheet or vapor barrier? You all are very helpful. I'm taking this in like a sponge. This will greatly help my Dad and I out.
Golf,
Q. "I've been told by my Dad and the log home company that I'm going to work with that I need a walk-out basement by code."
A. I've never heard of any building code that requires a walk-out basement. Perhaps there is a bedroom in the basement, and the code requirement is for emergency egress.
Q. "What do I do there? Make the block opening 8 inches wider and place the polyiso on either side, then frame the opening out with a stud wall for the doorway?"
A. A walk-out basement usually has a framed wall that is significantly wider than 8 inches wider than the door. For example, if the house is 24 feet by 24 feet, then the walkout side would have a framed wall that is 24 feet wide.
Q. "How do I insulate that?"
A. The framed wall is insulated like any other above-grade wall.
Q. "I'm taking this in like a sponge."
A. Good. Study before you build.
Golf,
Q. "I would have to just frame my walls with 2x8's to cover the 8-inch block we're using and maybe a plastic sheet vapor barrier on either side of the wall. How does that sound?"
A. That sounds like a bad idea. I don't know whether your 2x8 wall is an above-grade wall or a below-grade wall -- your description is unclear -- but in either case, you don't want to have a "plastic sheet vapor barrier on either side of the wall."
If it's an above-grade wall, an exterior vapor barrier is a wrong-side vapor barrier that can destroy your wall.
If it's a below-grade wall, you don't want any polyethylene anywhere in the wall.
For more information, read these articles carefully:
Do I Need a Vapor Retarder?
How to Insulate a Basement Wall
Okay. I know the door is an egress door, and thus it is to code. We are planning on sloping the ground on either side from the main level grade down just enough to let an egress exit door out the back of the house from the basement. To avoid any hassle, I would not have to add perimeter EPS and keep the subslab EPS back from the edge so I wouldn't have to protect that. This would cause a minor thermal break, and just frame my walls with 2x8's to cover the 8" block we're using and maybe a plastic sheet vapor barrier to protect the wood on either side of the stud opening. Then I guess I wouldn't have to make the opening any wider than we normally do and just frame the door in. How does that sound?
Golf,
Q. "I think I know what I'm doing! "
A. Glad to hear it.
So I don't need a vapor barrier, just stud the door in with 2x8's, then use spray foam around the door for insulation like normal. One guy noted to run the polyethelene from atop the subslab insulation above the slab a little to keep moisture coming down the walls and onto the floor. Is that correct? Otherwise, I think I know what I'm doing! Thank you!