Basement Wall – Insulation with Interior Drain Tile & Steel Bracing

Background: I am in the early stages for a basement finish and want it to be as comfortable as possible – plans are drawn but I want to get out in front of the builder on some of the things I know they’ll take shortcuts on if I don’t do it myself, like sticking batt insulation in the wall cavities. Our house is a 1956 ranch in NE Kansas (zone 4) where our soil is more akin to clay and is very expansive. To add insult to injury, the houses in this area were built very low to the ground with terrible grading and minimal opportunity to create positive slope. Suffice it to say we and the previous owners have invested tens of thousands of dollars into stabilizing and getting this basement dry – I believe we have achieved that goal so now it’s all systems go. Worth noting is there are no efficiency standards adopted by Kansas, so insulating the walls is not code, but as I mentioned I want to make it as comfortable as possible and follow best practice in the meantime.
I plan to use EPS (sadly 1.5″ seems to be all I can find nearby) on the walls and in the rim joists and seal off properly with expanding foam, caulk, and tape.
1. We have an interior drain tile system that leads to two sumps – would it be best to put a dimple mat on the wall to be sure if any water does penetrate, it finds its way to the sump wells? If I do this is there a way to seal off the bottom of it, to make sure the water drains into the crack between the wall and the floor? Would flashing tape between the floor and rolled up the dimple mat work for this?
2. We have perimeter bracing that consists of w-steel columns (4″ flanges) poured into the concrete floor and stabilized using the overhead (main floor) system around the entire basement spaced mainly at 4′ intervals. This presents multiple issues to finishing the space, not the least of which is having to pull framing out from the perimeter walls between 4″ (best case) and 7.5″ (worst case) depending on how it lays out. I would like to get the backside of the finished space sheetrock as close as possible to the face of these columns – but I don’t want them to be contacting it directly – so what if I wrapped them in 1/2″ or even 1/4″ rigid foam? Would that be enough of a thermal break?
3. Based on #2, it isn’t hard to imagine some of our walls have bulged and are nowhere close to being on a flat plane and plumb, making it hard to affix a rigid foam panel without having various gaps behind it – is this a significant issue? (FWIW we’ve had a structural engineer inspect the foundation, so overall integrity is not at issue)
4. Would it be better to hold rigid foam panels off the floor with a gap large enough that I could fill this entire lower cavity with expanding foam once the bottom wall plate is fastened?
5. If we finish the ceilings and walls with sheetrock, does that eliminate the need to cover any spray or rigid foam applied in the rim joist bays with a thermal break?
6. I could easily use 4″ rigid foam insulation if I wanted to based on the wall bracing, but cost and availability seems to be an issue at that width. I’d like to use at least 2″ minimum (2.5″ preferably) if I can find it. Big box stores only seem to carry up to 1.5″ EPS but can find 2″ XPS more or less anywhere. I’ve looked online briefly but haven’t been able to locate any reclaimed stuff nearby. Is there a reliable website that lists where this might be found?
Thank you for these articles and all the expertise – very helpful to the weekend warriors out there like myself. I skipped doing any actual work today to chase rabbit holes here all day instead…
Michael
GBA Detail Library
A collection of one thousand construction details organized by climate and house part
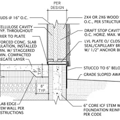
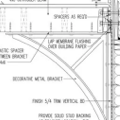
Replies
Those wide flange columns will be a pretty big thermal bridge. The good thing is that you are in milder climate, so you can get away with less insulation. I would wrap the beams with at least 1" of rigid. Bring this rigid back all the way and tape it to the foam on your walls. For condensation control, the 1.5" you can easily get is more than enough in your climate with insulated 2x4 stud wall.
Drywall is fine protection of the foam, you do need a much wider top plate so that it completely covers that 4" to 7" variable gap. On the bottom it is fine to run the EPS all the way down to the ground and have the bottom plate in front of it. Rigid is not so rigid and can easaly take up a fair bit of bow in the wall. Quickest is to attach the foam to the foundation with those hilti IDP anchors (not cheap) but you can also go with insulation washers and hammer drive pins.
You don't want a gap between the rigid on the walls and the fluffy in the studs. You'll have to push the batts in until they touch the rigid. It is fine to have a gap behind the drywall. Mineral wool might better as it is stiffer and will stay in place even if not fully between studs. You can also skip the fluffy and go rigid only.
I'm not a fan of dimple mat on walls, there is something wrong with water running down inside foundation walls for me. Water should be fixed on the outside. If you have water making it in through your foundation, you need to fix the grading, sucks when the house is low. There is no simple fix for that.
I agree that dimple mat on the interior is not ideal if you are trying to solve an active water issue, I like it more as insurance against an intermittent issue that the owner may not be aware of. I typically have it in projects where a client is buying a home they are unfamiliar with and immediately building out/renovating a below grade level. In this situation the client really doesn't know how the lower level behaves with regards to water infiltration, so we pitch dimple board as a bit of insurance.
In Michael's case, since he's spent years in the home, I agree that skipping the dimple board is fine and it will just come down to their personal risk tolerance.
Akos,
Thanks so much for the reply - you are very active on here and your posts are extremely informative.
Water penetrating the walls has not been an issue for over 5 years now, so I am confident we are good there. I read one of the other articles and considering we have no exterior drain tile (or at least a non-functioning clay one), it noted to use dimple mat on the inside. I assume the intent of this is to be certain any water that does find it's way through also finds the weep system for our internal sump. If that is overkill then all the easier for me to save some time and money in just putting up the foam board.
"Drywall is fine protection of the foam, you do need a much wider top plate so that it completely covers that 4" to 7" variable gap"...I did a poor job of describing why the walls would be anywhere from 4" to 7" off the foundation wall - that will really be up the framer as far as where this ends up (fully in front of the bracing or framing around the bracing, so to speak). I think at this point I'd like for the interior side of my wall framing to be 5.25" off the wall. That gives me room to wrap the columns in 1" rigid and still have a slight gap between those columns and the sheetrock. Am I right to believe it best these two items not be in contact, even if the columns are wrapped? The framer is going to hate me to have to cut around all this bracing, but it is what it is - I'm sure he'll charge accordingly...
You're correct though, there will be a gap at the top of the framed wall between the top plate and the top of the foundation / sill plate. Can that gap be fireblocked with 1/2" plywood? That was the intent and then the floor joists are going to be insulated from below to lessen sound transmission. It's hard to describe but between all the bracing, fasteners, and steel plates tying it all together I'm about to abandon the entire project.
Speaking of, ceiling height is already a giant concern and issue and we're likely going to have to fir the entire ceiling down 3/4" to get around a number of obstructions (i.e., the aforementioned steel plates lagged into the bottom of my joists that protrude 3/4" around likely half the room). Knowing this, there are no options for properly addressing the floor by building it up - the plan for now was to use Mapei Planiseal MSP, then a self-leveler, then LVT flooring on top of that. Am I going to regret this?
Planiseal MSP is a two-coat, high-solids, polymer-based adhesive isolator, sealer, moisture-control membrane and self-leveling primer. Planiseal MSP protects flooring installations against subfloor moisture and pH in concrete slabs with moisture vapor emission rates (MVERs) up to 15 lbs. (6,80 kg) per ASTM F1896, relative humidity (RH) up to 99% per ASTM F2170 and alkalinity protection up to pH of 12.
Thanks!
What is considered sufficient fire blocking depends on local code, our is 1/2" plywood or 2x lumber. This needs to go from your inside drywall surface all the way to the foundation, rigid insulation should start bellow this.
Having bump outs around your steel columns will definitely make the framers and drywallers day more difficult. If you have the room, I would come out so that the wall is completely flush (interior side of framing at column+1"rigid depth). There is nothing wrong with the drywall directly over the foam on the steel columns, you don't need a gap.
I have installed LVT directly over concrete slab. You don't need a self lever if the floor is decently finished, just grind of any obvious high spots/bumps. You can get thicker LVT with a foam backing that also helps a bit.
If you don't have a sub slab vapor barrier, sealing the floor also works.
Around me, about 80% of the basements are finished and they add a lot of value to a house. Generally, it is worth while if the space is usable (7' height or so).