Calculating for R-Value and Thermal Comfort

Hi all, I’m planning on adding exterior insulation and air sealing to my house in CZ5, and am trying to find the right balance between more r-value and the cost and complication that inevitably brings. While I’m certainly into the energy savings it’ll bring, my primary concern at this point is comfort.
For what it’s worth, I’m not talking PassivHouse levels of comfort, but more Pretty Good House levels. As a dad, I’m not afraid to tell someone to put on a sweater from time to time, so it doesn’t need to be perfect, just pretty good. However, the current wall in question is at r-9 for the assembly including windows (breakdown below), and has no air sealing to speak of. Basically, it’s cold and is uncomfortable to be near.
My initial inclination is to just make it as thick as is financially feasible, but realize that at some point there will be diminishing returns for the cost, along with the additional ‘cost’ of embodied carbon and the complications of detailing it in a retrofit situation.
I totally get that ‘comfort’ is a bit of a moving target, but is there a good way to calculate what would be necessary to ensure decent comfort?
Or maybe put another way, will I feel the difference between adding R-9 versus R-18 of exterior insulation?
The TLDR:
The overall wall is 294 square feet (263.5 sq ft wall @ r-9.7; 30.5 sq ft windows @r-3/.29 u-factor)
Currently it is TG board sheathing, with a 2×4 wall 16” OC with R-13 FG batts. I plan on using a self-adhered WRB (probably Benjamin Obdyke HydroGap SA) under the exterior insulation to air seal. I’ll be doing the retrofit one wall at a time, and resetting the existing windows, which are replacement vinyl windows, as ‘innies’. Depending on the thickness of the exterior insulation, I plan on reusing the existing aluminum siding with new trim details.
GBA Detail Library
A collection of one thousand construction details organized by climate and house part
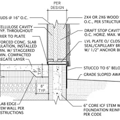
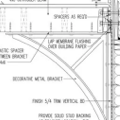
Replies
Making the walls air-tight can created a bigger difference in comfort than adding a continuous exterior R9 vs. R18.
>"Currently it is TG board sheathing, with a 2×4 wall 16” OC with R-13 FG batts."
Dense-packing cellulose over the R13s is usually worth it for ensuring air tightness & eliminating gaps in the insulation from mouse-nests etc, even when adding a self-adhered WRB. The WRB won't usually seal the seam between the bottom plates of the studwalls & sheathing, leaving potential thermal/moisture bypass paths, but dense-packing cellulose will plug up more than 90% of the potential leakage into stud bays.
Current IRC code-min for zone 5 is R13 + R5 continuous insulation, and that provides reasonably comfortable wall temperatures. Dropping back to code min or so on the sheathing insulation opens up some budget for higher performance windows, which would have a more dramatic impact on comfort than going from R5 to R9 or R18. Going with 3/4" (R5) or 1" (R6-R6.5) foil faced polyiso works well under vinyl or aluminum siding, and it is easier to make it fit if re-using the siding.
Since you're stripping the siding it's reasonable to swap out the vinyl replacement windows for a mid to high performance new-construction type window, which would also allow you to get the window flashing details right. In zone 5 U0.18-ish triple panes or U0.20-ish argon double-low-E double panes (with a hard-coat low-E on surface #4) are a significant comfort upgrade from code-min replacement windows.
As always, thanks for the insight, Dana.
I forgot to mention that I plan on using something like Fentrim or another tape/LA flashing to air seal at the sill plate/foundation transition. That said, I'm intrigued by the idea of dense-packing over the fiberglass as I'm sure it was installed pretty haphazardly. Would that change/increase the overall r-value of the existing wall in a way that I'd need to reconsider the exterior thickness ratio? Or does that process really just make it perform at r-13 because the current deficiencies underperform?
And, I suppose I had considered new windows, but I wasn't sure how much difference they'd make relative to their proportion of the wall at 10%. I'll give that another look in light of your comments, particularly since I'm already doing the labor of removing them.
The insulation value of fluffy insulation like fiberglass and cellulose comes from the air they trap, which is going to be R4 or so per inch. So a 2x4 filled with fluff is going to be R13 pretty much no matter what it is*. If there are gaps, the air is free to move, and then it doesn't act as an insulator.
(*This isn't quite true, there are higher density insulations that give higher R-values. But it's a useful approximation).
>"Would that change/increase the overall r-value of the existing wall in a way that I'd need to reconsider the exterior thickness ratio? Or does that process really just make it perform at r-13 because the current deficiencies underperform?"
Dense packing over the R13s would increase the performance of the wall, but not the R-value or exterior thickness ratio. Dense packing guarantees a complete and nearly fill with no voids (except where blocked by framing), and reduces the convection within the cavity as well as air infiltration by more than 90%.
The prescriptive R-ratio for dew point control presumes that some or all of the fiber insulation is installed perfectly.
>"I suppose I had considered new windows, but I wasn't sure how much difference they'd make relative to their proportion of the wall at 10%."
If they are clear-glass double panes (no low-E) they're essentially an R2 hole in your ~R10 (give or take, after factoring in thermal bridging and the R-values of the siding & wallboard, etc) wall. It's only 10% of the area, but it's losing as much heat as ~50% of the blank wall area. Adding R6 foam would make it an ~R16 wall, making the proportional loss of the window even higher. If adding R18 foam the window would be losing more heat than all of the blank wall area.
But the suggestion was about comfort. The much colder surface of the window reduces the mean radiation temp, and creates a cascade of cold air falling down the window pooling on the floor below. A double low-E double pane has a low-E coating facing the room, and reflects back the body heat of a warm human standing next to the window, even if there is still a (not quite as as with a clear-glass double pane) film of colder air falling down the face of the glass. A triple pane has a much warmer interior surface, but doesn't have the heat-mirror facing the room, yet is higher still in overall comfort.
Hold a candle or lighter up to the window when it's dark out and look at the reflections. There should be four reflections, one for every surface of glass (2 from the interior pane, 2 from the exterior pane). If they are all the same color, there is no low-E coating and it's DEFINITELY worth swapping them out. If one of them has a different hue it's from a low-E coating, and you'd have to think about it a bit more. A typical code-min replacement window is about R3, still pretty lossy compared to an R16 (the 1" polyiso option) or higher wall.
>"Dense packing guarantees a complete and nearly fill with no voids (except where blocked by framing), and reduces the convection within the cavity as well as air infiltration by more than 90%."
I was just reading up on interstitial convective loops this morning relative to your comment. I had never considered their role in wall performance, let alone understood that they were possible in an air-sealed environment (which, I should have). Kind of mind blowing, as I've seen how the fiberglass batts were installed in my wall during a few repairs to the drywall. Definitely not Grade 1, that's for sure.
>"Hold a candle or lighter up to the window when it's dark out and look at the reflections. There should be four reflections, one for every surface of glass."
I tried this and there's no difference in color between the reflections. Not that I'm surprised; they're vinyl replacement windows from 2004 so I wasn't holding out much hope.
While I was hoping to get a few more years out of the life of the windows—both to minimize the cost and complexity of this wall retrofit—it seems like that it is probably best for the overall performance of the wall to replace those, not to mention comfort. It turns out that there is a dealer in Boise that carries Loewen and Sierra Pacific windows, among others, and I made an appointment to go to their showroom next week.
>"Current IRC code-min for zone 5 is R13 + R5 continuous insulation, and that provides reasonably comfortable wall temperatures"
Is that based more on experience, or is that relative in some way to results from an energy-modeling program? Hopefully that makes sense. I'm just trying to figure out if 'comfort' is quantifiable in some way. For instance, I was watching The Cornerstones of Comfort: How To Choose the Right Windows and Doors for Your Climate by Enrico Bonilauri, and he mentions that people start to feel uncomfortable around surfaces that are about 63 degrees. Assuming that's a safe threshold for general comfort, it seems like that could be a benchmark for designing wall systems, and provide a reasonable way to say when something stops making financial or ecological sense in terms of adding insulation.
>" I'm just trying to figure out if 'comfort' is quantifiable in some way. "
Comfort is subjective. Joe Lstiburek of Building Science Corp. has commented multiple times something to the effect of "Five percent of all people will never be comfortable."
But regarding the surface temperatures of an R13+ R5c.i. assembly, it's a significant improvement over R13 with no continuous insulation. Without the insulating sheathing there is easy-to-find temperature striping at the framing that will be in the high 50s or very low 60sF when it's 0F outside due to the fact that the 3.5" of framing timber + siding & sheathing + wall board only add up to R5 or so. The R13 + siding & sheathing + wallboard over the middle of the stud bays adds up to about R15, and would be north of 60F (assuming no air infiltration inside the cavity)in a 70F room when it's 0F outside. Adding the R5 DOUBLES the R value of the framing fraction to R10-ish raising it's worst-case temp by several degrees, while raising the rest of it to R20-ish, with a much smaller net improvement.
But the inside surface temperature of clear-glass double-panes is about 35-40F when it's 0F outside, which is quite a huge difference from the rest. A pretty-good single low-E argon filled window's inside surface temp would run about 55F or a bit less, something that you can easily feel on your face with you eyes closed if comparing it to the wall temp. A double low-E double pane would have a surface temp in the low 50s (yes, lower than a window with a single low-E coating) since the low-E coating on th interior surface is not absorbing as much radiated heat from the room, but exposed skin next to that glass since it's reflecting the body-temp heat back at the skin that's radiating it. Any decent triple pane will have surface temps north of 60F on a 0F outdoors day.
The "mean radiation temperature" (MRT) of the room is often used as a measure of comfort, but when the temperature differences of different components are large that's less valid. Standing in shorts next to a blazing fire on a 0F night there is some distance from the fire where the MRT might be just fine, but frying you face while your butt is freezing (or conversely ) doesn't meet most peoples definition of "comfort". Raising the temp of the coldest surfaces (say, the windows) by more than 10F is easier to achieve than raising the temp the wall by 3F to achieve the same MRT, and eliminating the heat-sucking cold surfaces does more for creature comfort even if one DID raise the temperature of the wall area to hit the same MRT.
I totally get that comfort is subjective, and am reminded of that every day when I'm sweating and my wife is freezing (or, vice versa). I'm also onboard with the Joe Lstiburek idea of 5% of people will never be comfortable.
The flip side of that though is that 95% of people can be comfortable—although obviously everyone within that category will have their own definition—which it seems is what the MRT is trying to get at. That was my first time hearing that term, so thanks for bringing that up. I did a bit of digging over the weekend and came upon some articles at healthyheating.com that were really helpful in further understanding the core principles at play in that metric. The MRT gets close enough for me to start considering wall assemblies and their effect on comfort relative to their embodied carbon.
I suppose I have a final question relative to all of this: would learning an energy modeling software such as BeOPT be helpful in sorting out these sort of comparative questions such as how 2" of Gutex might compare to 4" of EPS, for instance?
First, let me point out that you've stumbled onto something important, which is that for the most part heating is all about comfort. Once you've warmed your house to the point where the pipes won't freeze and the occupants aren't at risk of hypothermia -- 40F or so -- anything after that is strictly for comfort.
A second point is that there's only a loose correlation between efficiency and comfort. I've been in plenty of houses that were inefficient but quite comfortable. If you're in the same room as a big cast iron radiator at 180F you can be quite toasty even if the house is leaky. Generally where lack of comfort comes in is when the heating is uneven -- rooms are too cold or too hot. Drafts are uncomfortable in winter. Windows or doors that lose a lot of heat are uncomfortable to sit near.
Now, a lot of things that make a house comfortable also make it efficient -- air sealing, good quality windows and doors. A well-designed heating system can make the house more comfortable, even though it may not use that much less energy, by keeping every room at a comfortable temperature.
Occasionally, I happen to stumble on something important :) Thanks for clarifying on the FG vs cellulose in a 2x4 cavity, and for reminding me of the role HVAC plays in distributing all this comfort.
I'm definitely interested in the efficiency part, and especially so where it overlaps with comfort. I also probably should have clarified that in my original post. My asking wasn't from a 'what's the minimum I can get away with?' standpoint, but rather 'when does throwing more insulation at in stop making noticeable gains?' so as not to burn more carbon by way of extra polyiso, eps, or rockwool.
I know that the answer to that obviously depends on which of those materials you use—clearly you can use waaaay more cellulose in a Larson Truss than if you were going to put XPS on your house if we're considering embodied carbon—but I figured a good starting point would be to define things in terms of comfort and that idea of a noticeable difference.
If someone had said "you need to shoot for R-40 like the Pretty Good House model suggests" then I'd probably attack things a bit differently than what Dana suggests will be reasonably comfortable at R13 + 5.
Air sealing is probably more important than insulation (within reason) for comfort. Drafts will cause people to perceive a space as uncomfortable even if you have R30 in your wall. Other things come into play too, such as a room on a corner with two exterior walls and insufficient heating in the room or a distant thermostat -- that corner room is going to be colder than other parts of the houe through no direct fault of the level of insulation (I had this problem in my own home).
Above a reasonable level of insulation like Dana mentioned, I think air sealing and HVAC design plays a more critical role. Radiant heating systems are usually thought to be the most comfortable, for example, but a tight home with forced air can be comfy too if done right. Zoning can help, and balancing airflow between registers. Note that sometimes you don't want all the registers to put out the same CFM value, either. In my corner room example, it may be beneficial for comfort to put slightly higher airflow into that room to counter the somewhat higher heat loss through the two exterior walls.
This is a simple question with a very complex answer, and it varies based on the home.
Bill
Thanks for your response, Bill. Those are all good points. I'm definitely going to handle the air sealing before I start adding insulation, particularly with that board sheathing I have.
It's funny you should mention the corner rooms and their increased need relative to comfort. I had a Manual D done, and of the three rooms that have the aforementioned wall in common have wildly differing needs: 109 CFM, 39 CFM, and 81 CFM. As you can probably guess, those two larger numbers are on the corners, and those rooms have twice as many windows as the center room.
Having a room-by-room manual J is a very good first step toward getting comfort.
I had pretty aggressive Manual J done as well as the Manual D. It was done by a mechanical engineer not affiliated with a heating and air company which was a nice chance to talk over concerns and long term plans for the house relative to the type of equipment that we selected without someone pushing an agenda.
There were some complicating factors in my setup that lead me to go with a mechanical engineer, but for fun I ran Dana's equation to calculate loads based on previous fuel use, and his method was within 1–2% of the needs the engineer came up with which I thought was both a pretty great endorsement of Dana's method as well as the work that the engineer did. I certainly trusted his other recommendations after seeing that his calculations so closely reconciled with what was currently needed.
It's pretty rare to come in with low single digits percentage difference between a Manual-J and a fuel-use calculation, since the margins of error in either calculation are more than just a couple of percent. But it happens. Fuel use load calculations typically come in 10-15% under Manual-J, almost never higher, which is more than good enough for sizing equipment.
In instances where the fuel use numbers come in higher than Manual-J it's usually a distribution loss issue, such as air-handler driven outdoor air infiltration or uninsulated ducts outside of conditioned space, etc. A fuel use load calculation simply can't separate out duct losses and other parasitic losses from the total load number.
In my case, the fuel use came in 2% higher than the actual manual j. I looked for my original fuel-use calculations just to check my math, but didn't have any luck. In my case the engineer did a pretty aggressive manual j, and it would appear gave me a bit more credit for insulation in our roof than I deserved. I think the other part of the equation is relative to the parasitic loses like you note.