Can a conditioned attic space be too big to work well?

I’m a builder and would like to spec my homes with a foamed conditioned attic. I’ve done one home already that was about 3,000 s.f. (single story, 9/12 pitch roof) and it seems to be performing well. I’d like to do this on all of my homes, but have concerns about the larger homes performing well.
The concern is that the sheer volume of the attic is so large, I wonder if the HVAC systems can’t be downsized much or even worse, may have to be larger. What are your thoughts on how well a conditioned attic works on a 4,000 s.f. to 5,000 + s.f. single story home with a 9/12 (average) roof?
The homes are being built in Oklahoma City area which is a mixed-humid climate. The walls will be 2×6 net and blow fiberglass with a frame seal and Energy Star qualified windows will be installed. I plan to meet all mechanical and fresh air ventilation requirements. I appreciate any comments.
GBA Detail Library
A collection of one thousand construction details organized by climate and house part
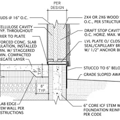
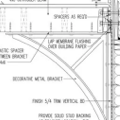
Replies
James,
If you design homes with HVAC equipment and ductwork located in the attic, then you have to consider two facts:
1. Locating HVAC equipment and ductwork outside of the conditioned envelope incurs an energy penalty.
2. Insulating between the rafters to create a conditioned attic enlarges the home's thermal envelope and increases its volume, incurring an energy penalty.
Here's what you need to remember: Energy Penalty #1 is always much bigger than Energy Penalty #2, so there is always a net gain (lower operating costs) when you create a conditioned attic (assuming, of course, that we're talking about houses with ductwork in the attic).
That said, there are always lots of ways to skin a cat. Creating a conditioned attic is expensive, so you might consider other ways of bringing the ducts inside -- perhaps by using soffits. Or you could create a small conditioned mechanical room in part of the attic instead of bringing the entire attic into the thermal envelope.
Finally, get ready to receive some flak for building 4,000 to 5,000 square foot homes. If you and your clients are serious about energy savings, you might start building smaller homes.
This is an interesting question as traditionally this would never be done and a "cathedral" ceiling or other type that was either not an attic or had high ceilings, was considered energy inefficient. While I hope to see some more results from those who have done this, I see several negatives. First is that a 9/12 roof will have 25% greater surface area than the flat ceiling so that even with the same R-value and performance of insulating, there is a theoretical 25% greater heat loss or gain. This doesn't include gable end walls that will add additional area. This is also an increased area to insulate with an increase in initial costs but no gain in performance. Second is that heat rises and unless the ceiling is a barrier, which is not likely although possible, heat will rise into the attic instead of being in the living area conditioned space. This may be desireable for cooling but not for heating. Third is a personal concern about sealing wood in foam. Unfortunately roofs leak for many reasons. Wood also has varying degrees of moisture at the time of construction so it is hard to say what the condition will be when the foam is applied. The product is still relatively new so who knows what will happen 10, 20 or 50 years from now with these installations. Finally is that foam is still a lot more expensive than fiberglass or cellulose although it has a lot of benefits. I used it in my house because I wanted to see how it worked. So far I'm happy. I know this is not the definitive answer and I hope others respond with some greater experience in this application.
I also like Martin's answer although I question his conclusion that there will be "a net gain (lower operating costs) when you create a conditioned attic." Where I am in Michigan we almost never put ductwork in the attic, although there is generally a basement which raises a whole different set of issues. Therefore Martin's point number 2 will generally control for us. On the other hand, his comment on the size of the house is the best solution to your problem. Build a smaller, better, well detailed house that has more amenities and lower operating costs for those that live there. Maybe use the attic space as livable area if you are going to insulate it anyway. It will saves land leaving it for natural space and use less material. A well done small house can still be worth as much as a larger one so you could have the same profit margin with a much better product. Sort of a quality over quantity approach.
Corain,
Lest there be any confusion: I don't advocate that ducts be installed in attics. In fact, I've been actively advising against the practice for years. If there's no equipment or ductwork in the attic, it obviously makes sense to put the insulation on the attic floor, not between the rafters.
Concerning the net benefits and losses associated with the two energy penalties I described, Energy Penalty #1 and Energy Penalty #2: most builders underestimate the energy penalty associated with putting air handlers and ductwork in unconditioned attics. The penalty is severe.
Martin, I agree with you that a well built small home can be more energy-efficient than a comparably specified larger home. The average size of new homes is on a downward trend for many reasons, but energy efficiency is probably not one of the main reasons. Most do want an energy efficient home, however, provided they don't have to sacrifice much. There's a large segment of the population that still want large homes and I'm trying to build the most energy effecient, durable and affordable home I can for these folks. If I don't build them, someone else will, so I'll take the money and build a better product. I know some will disagree and that's OK; I feel good about what I do and sleep good at night.
I don't completely understand conditioned attics. For instance, there's not near as much insulation that goes on the rafters as you would put on the ceiling, yet the attic is comfortable summer and winter. The one house that I've done foam on (rafters and walls) seems to be performing well; big roof and all. I had the HVAC system designed by an engineer and we're running about 1000 s.f. per ton of AC. The design called for a huge extending-reducing plenum for reduced duct runs. I was pretty nervous and skeptical about the performance, but so far, so good.
One of the big benefits I found of using the foam is airtightness. All my homes are subjected to blower door tests and this one had about 1/2 the air leakage as my other homes (all Energy Star Qualified) and the only difference was the foam. I agree that foam is almost prohibitably expensive, but it does seem to work well and comes with a high perceived value from the prospective home buyers.
I could put the air handlers in a conditioned room in the attic. I wonder how much of the "energy penalty" that absorbs while leaving the ducts in the unconditioned attic still? Martin? I don't think running chases in the conditioned space will fly in my homes. I think that would mess up our ceilings too much and be unattractive. I would assume on a large sprawling home that it would also add unecessary length and 90's to the ducts because you'd follow the edges of rooms and hallways as opposed to a straight run in the attic? I don't know since I haven't done it before.
If anyone has experience with conditioned attics on large single story homes, I'd like to hear about your experience and how well it performed. Thanks for the comments so far, by the way.
CCSF IMHO = Confusing Collection of Symbols For Impressing Many Home Owners ?
James,
If a builder's idea of a conditioned attic is to move the insulation to the rafters -- but to install less -- then the homeowner is getting cheated.
You wrote, "There's not near as much insulation that goes on the rafters as you would put on the ceiling, yet the attic is comfortable summer and winter." This is unfortunate, and is a sign of two trends:
1. Spray-foam contractors are cutting corners because the price of their product scares away customers unless they cut corners.
2. Code enforcement officials are looking the other way or getting bamboozled by fast-talking spray-foam contractors instead of doing their job.
As a result, homeowners are left with homes that have below-code levels of insulation. That's wrong.
For more information on this problem, see It’s OK to Skimp On Insulation, Icynene Says.
James,
I agree with Martin.
I live in North Texas....my home has a "conditioned attic" and it performs very well.
I paid a $premium$ to install beyond code minimum R-value(open cell foam).
A little over 2 years ago I realized that "conditioned attics" are really NOT the best strategy.
I will go a step further and call the trend towards "conditioned attics" a Folly.
Especially for homes with not-so-low-pitch Roofs.
I urge you to consider other methods to create an airtight "lid" above your living space and keep all HVAC under the "lid".
Once you have an "airtight lid" you can install inexpensive Cellulose to levels EXCEEDING minimum code R-value.
You all here at GBA have a solution to this attic situation. A tall enough second floor so that a dropped ceiling encloses hvac system. Then above this attic floor sealed tight and install as many feet of cellulose as you desire. R 60 or more even. The key is using either some passive house sealing tapes or a thin layer of spray foam.
John,
Can you elaborate on your thought process? You have a conditioned attic and say that it "performs very well" but you have concluded that it is not the best strategy. Is this strictly cost based or are there other factors?
Please note that I don't disagree with your conclusion, I'm just interested in your reasoning. As spray foam contractors in Zone 5, (NE Ohio), we always recommend at least code minimum r-values, regardless of what system we are installing. When possible we insulate on the flat with a combination of foam for air sealing and cellulose to R-60.
Remember, 5 inches of closed-cell spray foam might work for North Texas (Climate Zone 3), but it isn't enough for Climate Zone 4 (which requires at least 6 inches of closed-cell spray foam) or Climate Zone 6 (which requires 7.5 inches of closed-cell spray foam).
Martin...OKC is in CZ3. Although this past winter they were CZ10!!!
James,
The homes I design in North Texas, DFW, all have conditioned attics so far and all have high-pitched roofs (it’s the thing here). The one thing to do is include some of your livable space in the attic, create an office, workout room, bedrooms, entertainment room, etc in it, then you “gain” that space and you can install all your hvac equipment in the “conditioned space”. One of my clients just finished a 6,000sf house, including the attic, with 6tn of heating and cooling and less than $200/mo energy bills. It performs very well, but it was designed, installed and balanced the right way.
The new codes required for “livable” attics to have fire escape, structural floors and all the other electrical and safety codes, just the same as the regular space.
If you are going to install foam under the roof decking, make sure you have a full 10” OCF, 5” CCF or a combination of 5.5” OCF and 1” rigid insulation on top of the decking to prevent thermal bridging and condensation.
As I mentioned on one of your questions before, make sure your hvac system is design properly, with the right ventilation and humidity control.
One thing I've learned in my journey to building high performance homes is there's frequently not one solution or answer and many tradeoffs need to be considered. I appreciate all the different perspectives and opinions.
If Martin is correct, then perhaps I've been bamboozled by the insulation contractor who installed 5 1/2" of closed cell on the underside of the rafters. I questioned him because it was only around R-19 and he confidently explained to me that it would work. I also asked about whether or not condensate would form on the underside of the decking and he explained that the temperature would not reach the dew point there with what he installed. It's really hard to cipher through what is factual and what is not. Without a whole lot of actual empirical testing and data, you almost have to try something and see if it works. That's a scary proposition for me.
I will say that the house was comfortable through the winter as a model home, but it wasn't completed until late September last year and hasn't seen the hottest weather yet. Time will tell.
Armando. We haven't talked in a while. I misplaced your phone number. Give me a call or drop me a line sometime. Thanks.
James,
If you have 5.5 inches of spray-foam insulation with a total R-value of R-19, then you have open-cell spray foam, not closed-cell.
In Oklahoma City, open-cell spray foam does not require an interior vapor retarder, because your winters aren't as cold as winters in Boston (Climate Zone 5).
Of course R-19 insulation can "work." It just doesn't work as well as R-30 or R-38 insulation.
You are correct that it is open cell; I misspoke. I'll be interested to see the bids when I ask for 10" of foam.
I picked open cell over closed primarily because of price.
James,
The reason you and many people (including me, long a go) into buying on the 5.5” OCF is because the code allows it under the performance side of it and the insulating contractors in order to give you a “competitive bid”, they’ll tell you that it’s enough. The fact is as Martin said, Rvalue is Rvalue, and we need to start installing the minimum Rvalue by prescriptive code or else we run the risk of condensation, performance and durability problems.
You can contact me anytime at acobo100 at hotmail dot com or Nine Seven Two – Seven Eight One – Eight Seven Two Four
James,
I believe we(folks that visit GBA) should start building better than minimum code
And we should consider things other than cost.
but if only assuming dollars and minimum code.....
If your prices are similar to a recent Dallas price quote....
R-30 Open Cell at the roof deck = $2.80/sf
(includes required Intumescent coating)
R-30 Cellulose at the attic floor = $0.50/sf
Your example One Story house of 4,000 sf...
Cellulose attic floor = 4,000 sf X $0.50/sf =$2,000
Sprayfoam (9/12 pitch) roof deck = 5,000 sf X $2.80/sf = $14,000
(does not include any gable walls)
approx a $12,000 "incentive" to airseal the attic floor and get HVAC below the "attic floor".
If the house has gables...the incentive would be even greater.
If you wanted to do something really crazy like double the R-value to R-60
Cellulose upgrade would cost about $2,000 and....
it could even be postponed to a future date
The price to upgrade Spray Foam (if even possible) would be $$,$$$
Torsten,
I am concerned about things other than cost....
Health & Safety(workers & homeowners), Durability (of compact unvented roofs) and GWP
I am curious about the price of your hybrid suggestion
How much would your method (foam airseal with cellulose topping) cost?
R-30 for a 4,000 sf attic floor ?
R-60?
I've seen the sprayfoam airseal at the attic floor mentioned in other threads as well.
Is part of the motive to avoid ADA airseal at the gypsum ceiling? Or do I misunderstand the application?
Joe
Joe W,
Avoiding Airtight Drywall Details is the reason that I assume people would consider the foam/cellulose combo approach.
I will be curious to hear Torsten's price quote.
I think gaskets or sealant at the top plates would cost less and be Not-So-Foamy
There is also the option of Airtight Sheathing as the Attic Floor Deck
The advantage of a sheathing air barrier is that it could be blower door tested before drywall.
I have done the ventilated roofs, unventilated roofs, boxing ducts in attics, furr-down hallways and rooms to keep ducts bellow ceiling, you name it… and after all that, in most cases I’ll do the conditioned attic.
You can also look at the cost of conditioning attics in new construction by reducing overall cost IF: 1. You design rooms in the attic, therefore reduces the house footprint (less foundation, less cladding, less roofing, etc). 2. Install all equipment in the conditioned space and not having to deal with furr-down construction, air seal and corner seal. 3. Smaller duct runs 4. Shorter plumbing runs 5. Easier job on airtight construction. 6. Reduce labor considerably in all trades.7. I can use open web floor trusses with dedicated chases to minimize my air supply runs and make it easier for the HVAC contractor to install his ducts (saves money)… I can go on and on about all the “savings” I think about when doing a full condition attic… can you?
Armando,
I realize that I am biased to a Not-So-Foamy approach.
I like to use the One story Example because it makes my approach easier to justify.
;--)
After All this thread is about One Story Homes.
I also think that for small affordable homes
3 bedrooms 2 baths and Not-So-Big
... A One Story just makes more sense....
Easy to build, economical, easier to maintain and Aging in Place Friendly
For Two Story and Three Story Homes the Cost Savings for a vented attic are harder justify.
I still think it (vented attic) is worthy of consideration for other reasons.
Closed Cell Spray Foam, IMHO, is a great product in some conditions. The major drawbacks being health hazards and cost. IMHO, I would look very hard at using a very tall energy heel truss, using Knauf ecoSeal or Owens Corning's similar product, and blowing a boatload of cellulose on top. Eliminate ceiling penetrations, keep all the ducts in the conditioned space. Pretty dang good bang for the buck
John, you say "one story makes more sense", but of the 500,000 (more in most years) new homes built annually I would bet 80% or more are 2 story. I like foam in my homes and climate but I am stil trying to limit ducts and HVAC equipment in the attic and do vented attics where I can. I like Armando's advice of using open web floor trusses and dedicated chases (which we do) to keep ducts out of the attic. The challenge I have is in very large homes where the architect does very little upfront planning in providing supply chases and mechanical closets. For decades they have just stuck everything in the attic.
Allan
Allan,
My comment about One story homes "making more sense" was for small affordable homes.
I agree that a very high percentage of new homes are 2 story.
Lot sizes are getting smaller and land is more expensive.
The trend near Dallas has been to build near the maximum available footprint in order to get higher appraisals and maximize builder's profits.
I think you are wise to move back toward vented attics.
Have you tried asking your Architect to include mechanical closets as part of the program?
In addition to the coffee bar ... and the cigar room... how about a mechanical closet?
John
With spec houses I do give some thought on the design stage regarding HVAC needs, and discuss with my architects. Most of the houses I build are designed by clients without my involvement. Many times I am not even in the discussion until the bid stage, and I have no opportunity to discuss mechanical.
Regarding the Dallas market as you see it, I think builders are probably building what the market is demanding. You mentioned builder profits, I vaguely remember what profits are, can you help me jog my memory :)
Finally, regarding design, remember that just like all things in our society, sex sells. This also applies to houses. Boring stuff does not sell.
Allan
I like the idea of floor trusses as a ceiling in a one-story house. Surely, that would work, raised heel trusses on top ... and save a load of time on framing, sealing, covering HVAC/electrical soffits throughout even a house <2000 s.f. of course my bids will show me if i'm wrong, or anyone local would be willing to do it.
I like your #21 drawing, John, with the sheathing continuous from the walls and then sealed (over the floor/ceiling trusses).
Now I'm wondering if the sheathing needs to be plywood (for permeance) or if it can be OSB. With cellulose on top of it and interior air below it ... but I've been wrong before haven't I?
Thhe approach seems simpler, buildable, and more cost of OSB is about the same as sheetrock. It could be sealed from the attic instead of having to deal with the cranky sheetrock guys down below.
Ready for this to be a 'bad idea'
Joe
For you builders out there building 5,000+ sq foot homes...
Since this a green building forum, I think I should say a couple of things.
You certainly have the right to build these ridiculously large monstrosities. You certainly have the right to install spray foams and foam sheathings, and place HVAC and ductwork in the attic.
I just hope you aren't promoting these excessive dwellings as "green" homes, because they are CERTAINLY not green.
Brett Moyer (#28)
In my homes HVAC equipment and ductwork are in the conditioned envelope. I do use spray foam in most of my homes, I believe it is the best insulation for my clients. I do not promote myself or my homes as being “green”. I do not believe that label is beneficial or smart marketing for the slice of the market I try to build for. In fact I think it would be detrimental. I do consider myself an exceptionally high quality builder and do try to use the best methods and practices in every aspect of home building, those being structural soundness, architecture and design, energy efficiency, styling, finishes, warranty, customer service, technology, etc.
Allan Edwards
See if your truss manufacturer can make you trusses out of I- joists. On the bottom of the top cord put 1" of XPS and seal it in. Then mesh the bottom and blow in the BIBS. Get the truss as deep as you need for the desired R-value. This is the cheapest high R-value roof assembly we have found and it is also vented.
James, may I suggest using SIPS?
The SIPS package places the insulation above the rafters, large sandwiches of OSB or plywood and polystyrene. The point with this system is that the panels can be made and cut to measure in a factory, they are joined together using smaller sandwich inserts, finished with spray in foam, the result can be an airtight box.
Keep in mind that it is easier to produce a cube or rectangle when it comes to wanting a completely air tight perfectly insulated box, but you want the attic to be of high standard, this is the best you can get. The best fixing is glue, but mechanical fixing may be used provided it does not bridge the whole unit.
Hi
I just completed a house (Zone 5) with the attic being within the thermal envelope of the house. The house is in a flood plain, so it worked out best to put the mechanicals in the attic rather than trying to shoehorn them into a closet somewhere.
The house is just under 2,000 sq. ft. and the attic is size of the footprint. The roof is unvented and insulated w/ dense packed cellulose and 2" of rigid foam. The foam is on the interior side of the rafters. Seams were taped and all penetrations caulked and or foamed. There are some interesting threads concerning cellulose in an unvented roof assembly on this site. But it has been done in this area for years without issue.
Mechanicals in the attic is commonplace throughout the southeast. The problem is that usually it is done w/ a vented roof and fiberglass in the rafter bays, which ends up acting like a giant chimney for the house.
It seems that if the house is well air-sealed and the roof insulated to appropriate levels for an unvented assemebly that it works well to include the attic in the thermal envelope. We have found it much easier to appropriately air seal a roof than the at the ceiling plane.
Martin
If you are building a 2 story house in hot humid area, and you are able to keep all HVAC equipment and ducts below the attic area, in the conditioned space, is there any benefit in doing a non-vented attic.
Allan
Allan,
No. Deep cellulose on the attic floor would definitely be the way to go.
Martin
Is cellulose as good an air barrier as open or closed cell foam.
Allan,
Q. "Is cellulose as good an air barrier as open or closed cell foam?"
A. No. So seal your ceiling before you insulate!
Brett,
I really don't want to change the direction of this thread. I'd rather get opinions and suggestions regarding the subject of whether or not a conditioned attic (using spray foam on the rafters) is feasible on a large single story home. I will take a chance and comment on your post #28.
Keep in mind, that "Green" is different things to different people. I'm not a tree-hugging hippie proclaiming doom (although they definetly have a place) and I'm not the guy saying there's nothing bad happening to our planet. I'm somewhere in the middle. My whole take on building green is this: Build a home that is highly energy efficient with built-in durability that is healthy and comfortable to live in that people find appealing and want to and can afford to buy. Along the way use as many local resources as possible and fewer resources than a comparable code-built home. That's "green" to me and I'm very comfortable to market that. It's a big first step in my marketplace and it's been well received by my clients and prospects. A smaller home uses fewer resources though, no doubt.
I didn't create the market for bigger homes. The market exists in spite of myself and other builders. If and as the market changes to smaller homes (which it is, but maybe not small enough for some of you) builders will adapt as well because we're not doing this for kicks and grins, we're doing this with the hopes of making a profit. As long as we're a capitalist economy (God help us if it's not), this dynamic will never change and I hope it doesn't.
I made a decision to build a better home that uses far fewer resources over it's life cycle than the same home built to code. I call that being "green". That decision has added a whole new level of complexity to my building process which increased both my hard and soft costs which I probably won't ever completely recover in my market. I'm OK with that because I'm still making enough money to keep me engaged in this business and I feel better about the improved product that I offer.
I know my point could be debated and I really do understand and respect Brett's and other's point of view. I hope I haven't changed the direction of this thread by posting this. I still would love to hear more about conditioned attics on large single story homes. Thanks.
James,
My understanding is that you are still talking about a ONE story House and a 9/12 roof pitch?
Can you get some per square foot quotes from your spray foam company and compare them to the numbers that I posted?
Assuming that your prices are similar to the ones I posted.....
Did you understand my point (post 19) about the $12,000 incentive to consider other methods?
James,
what was the R-value for the Bid you quoted?
John,
I just got a foam quote on a 4700 s.f. home I just started framing and I estimate that the cost over the blown fiberglass to be about $6,500 more. There was also an additional cost of over $7,000 to apply a fireproof coating "if the code official requires it". I haven't checked to see if that's required yet. I assume that if the fireproof coating is required that I could install several other energy efficient materials and procedures for the extra $13,500 and have a better performing system than the foamed conditioned attic. Or I could install a comparable performing system for less money. It's kind of hard
If the fireproof coating is not required (or needed) then it might be a more difficult tradeoff. I haven't done all the numbers yet and I'm expecting more quotes to come in still. When I get a chance to put together the numbers, I'll let you know and hopefully get some good feedback.
John,
Five inches of closed cell, which is a little shy of the standard 5 1/2". I understand there's a lot of controversy over the thickness of foam applied after reading the painfully long thread (300 posts) that Martin started regarding Icynene claims. I couldn't tell you exactly the R-value because they didn't specify which product it was (which I'll find out). I understand there's a slight difference in R-value per inch between the different products.
For $13,000, I could obviously do a lot of things like:
1. More insulation, but after reading the aforementioned thread, I'm more confused than ever about the diminishing returns concept of more insulation. I'm also considering using cellulose in the attic instead of fiberglass to reduce convective losses in colder weather.
2. Seal up the house more tightly (although, they are fairly tight already)
3. Install a better HVAC system. Higher efficiency units, variable speed blowers, engineered and tested duct layouts, dehumidifier, etc. I realize it's better to have this in conditioned space, but it's probably not going to happen unless I foam the attic. With better design, down to the type of registers, I can increase the HVAC performance dramatically.
4. Solar board on roof decking.
5. 1" rigid foam on outside of house.
6. Passive solar design considerations
7. Better windows.
8. Geothermal? Could be done for the same or less as the foamed attic in our market. Our local utility is paying for the wells and leasing back to the homeowner for $35/month.
Other ideas? I have to do a cost-benefit analysis on everything to determine what makes sense. I still have to be able to sell these homes and cost has to be considered.
I have a similar situation to the original post (OK city area, ~ 3k sqft, flexduct (returns only) in attic, blown fiberglass between ceiling joists with batts on walls of dropped/raised ceiling transitions, hipped roof, rotating roof ventilators with occasional soffit vents ... Existing construction [~1995]).
Trying to learn from this thread about what might work to improve performance cost effectively; some comments/questions, tried to organize by +/- on 'Conditioned attic, foamed?' (orig. question), though shifted to my situation:
In favor (of foam: air seal and insulate together under deck):
1. Covers Air Sealing: OK is windy; and roof vent turbines (my case; or ridge vent more common these days) isn't 'demand-controlled'; we don't really know how much it's venting. Blown fiberglass looses R-value via convection in top layers. If soffit vents are inadequate, passive venting might de-pressurize the attic, increasing exfiltration from the conditioned space. The alternative to foam at roof deck means removing existing ceiling blown fiber and air sealing first. Given the complexity of the ceiling (#2)...closing vents + foam at roof deck could be simpler.
2. Minimal Surface Area Penalty: These houses have lots of different ceiling levels, trays, etc., short walls (w/fiberglass batts), so the difference in area between roof and attic floor is somewhat less than the theoretical difference raised in @Corian's approach in #2. Hipped roof helps reduce surface area too (vs. gable).
3. Lots of Recessed Lights: not AT / IC rated; save cost of replacement / sealing / insulating.
4. Save cost of sealing ductwork (beyond glaring problems, which you'd take care of anyway)
Opposed (with questions/comments):
1. Prep-work: Attic ceiling includes covered porch areas that are currently uninsulated, so would need to add more there [but adding knee walls is pretty easy].
2. Moisture problems: Open cell could let moisture reach roof deck and condense, but also lets it out when roof gets hot; so in mixed / sunny / windy climate it seems pretty safe. But where does it go? Asphalt shingle roofs are not very permeable...For this reason also, adding closed cell below seems like a bad idea...roof leaks, etc...so you might want to ventilate between foam and deck, which means adding continuous ridge and soffit vents (or soffit vents + ridge plenum to existing ventilation)...not inexpensive, and complicated / impossible with hips and valleys.
3. Foam ain't 'green': lots of issues here, after reading the horror stories elsewhere from GBA readers...
4. Cost of professional foam spray (and hope they get it right!?) vs. [advanced] DIY...and high peak means reach issues for installer.
Which pushes me toward singing a 'Riversong', if I understand correctly: air seal ceiling and deep cellulose above, and tighten/insulate return ducts very well.
But what about ventilation, then? Are periodic soffit vents with lengths of vent channel ok, or does insulation need to be held back from the roof deck in all places? At which point you could add continuous soffit vents...but is it necessary?
More broadly, is _any_ ventilation even necessary? With ice-damming unlikely to be a problem in OK (sealed ceiling + windy, dry, sunny), passive ventilation for moisture removal means a winter penalty. Some summer benefit (reports say minimal with 6.5" insulation; would be even less at R-30 to R-60), but the wind might not blow when you want it to. Like with un-conditioned crawlspaces, if venting is for moisture removal, why not just seal it? (and dehumidify if necessary; here I'm worried about a hipped shingle roof not being permeable enough). If we vent for heat removal reasons, shouldn't it be controlled (balanced pressure unless perfect air barrier at ceiling, and closed in winter)? And that should make a dehumidifier unnecessary.
Proposal: Why not air-seal + insulate the ceiling, seal the (passive) vents, and control the ventilation: high/low vents closed when windy/cold, open when windy/hot, fan assisted if necessary / beneficial when still/hot?
Probably the answers are on GBA already...or somewhere else...will keep looking...
Thanks,
David/OK
[edited...hopefully clearer / shorter this time...]
Hello all,
I apologize for resurrecting an old post, but this post is exactly what I’m considering for a new build. My concern is the same. Curious to see if thoughts/opinions have changed since this was posted 9+ years ago. Maybe more data? I’m in south TX, climate 2.
We are about to build a 4460 sqft one-story house. Although the architect did a good job with the layout and elevations, she was upfront about not being an HVAC expert and recommended that we speak to a HVAC designer/contractor.
After speaking to a few contractors and doing some of my own reading, I’m leaning towards a sealed attic design. This house will have some complicated ceiling designs, with varying heights, and many can lights. Roof pitch is 6/12.
Although all one attic, there are a few sections:
1. Attic space above back porch area
2. Attic space above all conditioned rooms
3. Attic space above the attached garages.
The thought is to section-off the attic above the conditioned rooms from the back porch and attached garage spaces. attic walls will be built to separate them.
The attic space above the conditioned rooms (additional 4460 sqft) will be a sealed/unvented attic. The attic space above the back porch and garages will be vented.
The HVAC design suggests we only need 5 tons.
In summary, adding 4460 sqft of attic space to the thermal envelope makes me “question things” ... even though the HVAC designer says we will be OK.
I thought this was an interesting discussion and learned a lot from it. Thank you. I’m interested in hearing your latest thoughts/opinions, or guidance, if anything has changed.
Thanks,
Ron
Yes I know every house in Texas has its ductwork and HVAC equipment in the attic and I think it is lazy and stupid.
If this were a remodel you are stuck with some bad choices. In new construction I see no reason to accept poor planning just because that is how we do things in Texas.
It is your money be strong and say no to stupid.
Consider mini splits or 2 or 3 small ducted system in closets serving a joining rooms.
Walta
Thanks for responding, Walta.
I forgot to mention that I do need/have climate controlled storage and I’m wondering if the sealed attic may be able to be used as this. I’m OK with spending extra money to insulate the attic with open cell foam if the house can perform well and the attic gives me “semi climate controlled storage” (without a significant operating cost). I’m just used to hot attics, so adding what appears to be a significant amount of attic space to the thermal envelope just automatically sounds bad. That’s my biggest concern. I’m also *very* ignorant on unvented/sealed attics and don’t know how well they work.
It is hard advise without a picture of the layout. That is a LOT of attic to make fully conditioned, but it is likely it doesn't all need to be conditioned. Plenum trusses may be useful for sections that contain mechanicals.
https://www.greenbuildingadvisor.com/article/use-plenum-trusses-to-keep-ducts-out-of-your-attic
Ducted minisplits are often the ideal solution for use with a plenum truss.
What are your goals as far as efficiency? It sounds like the plans could use a thorough review for things like continuity of the air barrier and thermal barrier. Complicated ceilings and roof lines mean there can be a lot of issues without prior planning.
With a little planning, you should be able to get the AC system down below 3 tons unless there is a ton of badly placed glass. But you need to define the thermal envelope and then have an engineering firm design the HVAC. Installer will put it in per specification.
Deleted