Cathedral ceiling: R39 vs R50 vs R60

I’m in climate zone 5. Currently, I’ve got R-19 fiberglass batts with no baffle for ventilation in a cathedral ceiling with 2×8 joists. I’m talking with a local spray foam contractor to insulate with closed cell foam. He claims a 7.1 R per inch.
He was adamant that only 5.5 inches of insulation (R-39) made sense and that to fill the whole bay at 7 inches (R-50) would add only a 2% efficiency gain. To him, this was not worth it.
30ish% of my roof surface is cathedral at 350 sq ft.
R-39 cost per square foot – $9.91
R-50 cost per square foot – $12.12 (cost increase is exactly in line with R value increase)
I know code is R-49. I also know that I see R-60 recommended often on this site.
Can anyone help me justify this decision one way or the other? I have no clue of the efficiency or comfort gains from the increased 11 R value.
Also, I’m strongly considering 1 inch of foil faced poly iso (nailed to joists/above ceiling) to reduce thermal bridging and get closer to R-60. Can anyone help me justify this one way or the other as well?
I’m not a pro but I consider myself a capable DIYer with a decent understanding of building science concepts (thanks to this site). This is an expensive upgrade and looking for some second opinions before I pull the trigger.
Thanks in advance!
GBA Detail Library
A collection of one thousand construction details organized by climate and house part
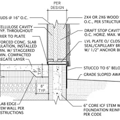
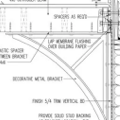
Replies
Hi Sean.
You'd have to ask someone to do some energy modeling on the roof to determine your point of diminishing returns on the spray foam, but your roofing contractor may be right, particularly when considering the financial (and environmental) cost of most closed cell foam. And as you noted is does nothing to mitigate thermal bridging.
You also may want to research local codes, if that matters to you. In your area, the current International Residential Code calls for R-49.
Another option would be a flash and fill system. You could fur down the rafters with strips of rigid foam insulation, mitigating thermal bridging and making more room for cavity insulation. Then, you could have a flash coat of spray foam installed to the roof deck and fill in with dense pack cellulose (or anything else you'd like to use). The key is to get the right ratio of spray foam-to-fill insulation.
If you haven't already, I recommend you read this article: How to Build an Insulated Cathedral Ceiling
Sean, I was recently asked a similar question by an architect friend--here's my edited response:
I've heard both claims--especially the 5" thickness, many times. I think I'd be more pro-foam if their industry did not push lie after lie... there are diminishing returns with any insulation, and depending on the price it may not be cost-effective to install closed cell foam over 5" thick, but it comes nowhere near meeting code (R-49) at that thickness. Despite sales claims, conventionally blown closed cell foam ages to about R-5.6 to R-6.0/in. So best case, at 5" you have R-30. Granted it's airtight (assuming proper installation) and blocks vapor, but it's barely half of the R-value you need by code, and half of what you spec'd. Foam installers can't fathom how to air-seal without foam, but I've done many projects under 1.0 ACH50 with essentially no foam, just with tapes, sealants and attention to detail.
The cost is heavily affected by how many passes it takes, as each pass drives up the labor. 5" is two passes of conventionally blown foam.
If you have to use foam, I highly recommend spec'ing (and ensuring they actually use) HFO-blown foam. Conventional blowing agents have a global warming potential 1030 times worse than carbon dioxide (on a 100-year scale) while HFO-blown is near parity with CO2. It's not benign by any means; half of the blowing agent is released upon installation, so the 100-year scale isn't really fair, but in any case the HFO is way better than conventional (HFC-blown). HFO-blown also maintains a higher R-value; probably R-6.5 to R-7.0 aged value, but it hasn't been around long enough to know the true long-term R-value. (Ignore industry LTTR--long term R value--it's an estimated 5-year value based on 18-month simulated aging.) HFO can also be installed in thicker lifts, up to 7" in one pass for some brands, but 4" is more typical. With two passes you can get over R-50.
Installers may balk at using HFO-blown foam, but as far as I know, every manufacturer now offers at least one HFO-blown product. The material costs a little more than HFC-blown but with the reduced labor they shouldn't be charging extra, though many do. It may require a lead time to get the HFO product if they don't normally spray it.
The HFO blowing agent was supposed to be legally required starting 1/1/20, but the ruling was reversed by judges appointed by the current Federal administration. Manufacturers were geared up and ready to make the change, from what I've heard from high in the industry, so it's really a shame that the rule was rescinded.
...........
As for adding the polyiso, your roofing is almost definitely vapor-closed; adding a vapor barrier at the interior allows no path for moisture to dissipate, and the R-value gain would be minimal at that thickness. If you still want the thermal break, I would use a more vapor-open material.
The installer uses Deimilec's HEATLOK SOY 200 foam which was named "Years best green building product" according to this article. https://www.greenbuildingadvisor.com/article/demilec-spray-foam-named-years-best-green-building-product
Seems like I'm in good shape from a blowing agent perspective.
Thanks for the response, very informative!
Heatlok Soy 200 is not HFO-blown, and nothing in that article claims it is.
It’s pretty common to add batts to fill the remaining the cavity space after the spray foam goes up. I wish I’d done that in my own vaulted ceiling but oh well. If you use batts, you don’t need to use anything fancy — cheap fiberglass batts work just fine.
You can use EPS as a thermal break that is a bit more vapor open so that there is some drying potential.
Regarding the switch to HFO foam, if the manufacturers were/are ready for switching over, they probably still will regardless of the regulations. The higher R value gives the HFO material a selling point, and the cost different will likely decrease with increased manufacturing volumes.
Bill
To put in perspective, assuming 2x8 16OC construction, assuming R7/inch for foam and taking into account the thermal bridging of the studs.
-5" SPF R28 whole roof assembly
-7" SPF R34
-2" SPF with 5.5" mineral wool batts R30
Your installer is 100% correct, the extra foam makes almost no difference.
Even the 5"SPF is waste of money. I would go with the minimum amount of foam needed for condensation control for your climate (see https://www.buildingscience.com/documents/building-science-insights/bsi-100-hybrid-assemblies) and fill the rest of the cavity with fluffy insulation.
If you want higher R value, furr out your rafters with foam strips and go with thicker batts. Just remember to increase the thickness of the SPF to match the thickness of the batts.
Going with 2" foam strips over the rafters, 3" SPF and R30 batts would get you close to an R38 roof.
Deleted
>"-2" SPF with 5.5" mineral wool batts R30"
A couple of comments-
The cavity depth is only 7.25", not 7.5". Squishing the R23 5.5" rock wool to 5.25" yields about R22, not that it changes the whole-assembly R by very much.
At just 2" (R14.2) with R22 rock wool it's a ratio of R14.2/R36.2, or 39.2%, which is just shy of the IRC Chapter 7 code-prescriptive R20 out of R49 ratio. It's not super-risky, but on the cold edge of zone 5 there is some risk unless a class-II vapor retarder is installed on the interior.
Going with 3" would have ample dew point margin, but the additional inch of foam costs more than 10x the cost a sheet of MemBrain or a bucket of half-perm "vapor barrier latex" paint.
>"Going with 2" foam strips over the rafters, 3" SPF and R30 batts would get you close to an R38 roof."
That would meet current IRC code on both an R-value and U-factor basis (= = <U0.o26, or R38.5 "whole assembly", which includes the R-values of the interior & exterior air films, the roofing, the roof deck, etc) with a hint of margin, as well as just meet the Chapter 7 prescriptive ratio (without any margin) that would allow using standard latex paint on gypsum board as the interior side vapor retarder.
Long screwing ceiling gypsum in through 2" of foam is do-able, but a PITA. It might be easier to build 1.75" Bonfiglioli strips using 1" polyios and 1x furring, screwing the furring to the rafter edges, and mounting the ceiling gypsum to the furring.
https://www.finehomebuilding.com/membership/pdf/9750/021250059.pdf
The foam quotes came in at over $1.70 per board foot even for the R50. I've recently seen HFO blown 2lb foam come in around the $1.40/board foot range for projects that size. Once you figure out just how much foam you're going to install, put it out to competitive bid.
While HFO blown foam is a lot greener than HFC blown foam, it's still one of the least green insulation materials going, with about 3x the carbon footprint of rock wool, R for R. It's not only financially expensive, it's environmentally expensive, which is a strong argument for the foam + fiber approach, using only the amount of foam needed for dew point control:
https://materialspalette.org/wp-content/uploads/2018/08/CSMP-Insulation_090919-01.png
Excuse me because I'm a novice but trying to understand. This assembly sounds like the best of every world. Can you shed some light on the function of the vapor retarder? Isn't the closed cell foam already a vapor retarder? How can an additional vapor retarder protect from inadequate insulation?
So I am looking at building a post frame house orb building with a second-floor livable space. While my plans keep changing I also wonder just exactly what I'm going to do when I start figuring my insulation because I am thinking green and warm.
so while planning this building 24 by 32 with a 22-foot wall to the eaves my plans are because the upstairs is only going to have an 8-foot wall using scissor trusses to give it the illusion of a little more openness similar to my trailer but I'm living in right now. As I'm used to living in a smaller space just me and my cat right now I really don't need huge open spaces and a ginormous house. so when I started spec out insulation I decided to go without having a uncondition attic and go with the scissor truss.
So I found that I can actually have my trust is built with longer boards or actually wider boards on the top cord or completely such as 2x6 vs 2x4 or 2x8. or just actually nail to the upper cord of the truss to extend it for deeper insulation valley. But as a post frame or pole barn design is not necessarily construed as a tight building I am looking for a very tight building by using the Huber Zip system sheathing. I was looking at zip are in the 3-inch for the walls which give me an R12 on the outside thermally breaking my post frame and giving my sheathing from my outside siding or metal whichever way I decide to go. Then because my garage is going to be a 12-foot ceiling on the bottom my plans are to use insulation under the concrete and a heavy vapor barrier under the concrete to thermally break the concrete and mitigate moisture travel. Because the garage won't be used all the time but I will be working out of it my theory is R12 would be a good starting point and down the road I can insulate the walls as I see fit. because I decided to go with bookshelf girts on my building that means the Borg go between the post not over them on the outside and I intend to seal the outside with the Huber Zip system which takes all your joints basically you have a cup upside down sitting in the air and everything inside the conditioned. My plans are to get this building down as tight as I possibly can I'm looking in a zone for building under 1.0 50 ACH.
but due to the constraints of finances I'm looking at building this building as tight as I can and spending my money to seal it as best I can, so I was looking at spray foam and the numbers I was quoted in my area was $2 per square foot per inch of spray foam. Well when you start talkin about $2 per square foot per inch when you start adding up to 6 in the game and are 36 value because I was quoted an R6 or 6.5 per inch, and my intention is to spray directly on the bottom of the decking for the roof, now I have planned a forethought of using t studs for my purlins in brackets which are thermally broke with spray foam . Keystone's are basically taking like a two-by-four splitting it down the middle and extending it out with heavy hardwood dowel rods in an x fashion or in a trust style fashion inside and then between the two sides it's spray foamed and it gets a very very good thermal break while still being usable in stud locations. While they're just coming on the scene they do have code compliance in many areas, and I kind of like the idea. but my plan was to thermally break my trusses since there's only double trusses every 8 foot for the plans I have been given so far the thermal bridging will be minimal
So my plan has been to go through and from the eaves to the peak have them butter the whole system with 1 to 1 and 1/2 in of closed cell foam paying attention to the types of chemicals used allow for proper off-gassing during construction so that I don't get into any issues down the road. Then build the rest up with rockwool Batts and my plan had been to look into using rockwool comfortboard on top of the bats and extending my chords as needed so I can panel over them but my intention was to leave part of the scissor truss exposed and simply paint it for aesthetics and cleaning.
While it may not sound perfect my plans were to do minimal interior finish I eat keep away from drywall as I've had bad luck with drywall and moisture. My plans were to use something a little different maybe even a vermiculite or even just plain painted thin plywood on top of the insulation. Honestly these people keep talking about running are 40 or 50 or 60 ceiling insulation and I know for a fact that there's no dang way my trailer has anything near that and I can heat the area I live in in my trailer with a buddy heater, and that's only 18000 BTU. So considering the fact that my intentions are much better than what I'm getting right now and the fact I'll have a couple of ceiling fans to help move air around looking at a combination of closed cell spray foam for the vapor ceiling in the thermal break between the deck sheeting of the roof and then filling it up with more conventional versions of insulation, namely rockwool due to its inherent fire resistance and less issues down the road healthwise. The reason I've been thinking this way is because with a 750 square foot roof on a 24 by 32 building if my area figures are right you're talking $1,500 for simply one inch and if I went 6 that makes my roof extremely expensive to insulate strictly with closed-cell spray foam and according to all readings that I have seen past 3 in you're only gaining about 3% per inch which means 3 in Max of spray foam Gaines you an 80% efficiency and every inch afterwards is of limiting increase to hit 100% efficiency.
these efficiency ratings I saw were on a charge straight from a spray foam manufacturer that they explained how good their insulation was and how efficient it was per inch, and at 3 in you were at 80% but at 4 in you only went to 83%, so my theory was why spend $1,500 to gain 3% efficiency when I can spend less add extra spacers on my trusses and purlins install 5 and 1/2 in rockwool Batts and get it R23 on top of my r61 in which sets me at an R 30 value then if I want anything past that my thoughts were to install rockwool comfortboard on top of that conceal it all off as best I can but leaving the majority of my trusses exposed simply for the idea that I had. but considering the fact that this is not actually going to be construed as a house I don't have to meet any code requirements even though there are no code requirements in my area and my zone is a zone 4 with a 25 snow load, so I'm not feeling too bad about what I'm looking at.
my personal opinion is that since I'm going to have a big bowl upside down sealed with no or very little air flow except possibly at the very bottom my plans show this to be a much more efficient living area as I put it together in my head.
My spray foam plans were from the eaves up to the crown of the roof, once I build my 8-foot walls using 16 in floor trusses those are the ones built with two by fours laid flat spray foam along the walls to seal the floor trusses to the side walls then when I finish out my garage ceiling downstairs my intention is on the floor 2 fill it with blown rockwool to the depth of 11 in which gives me an r49 value on the floor. my walls being a tin is thick considering the fact that I'm going to have to use a 2 by 8 4 ply column or give me the ability to install against the zip R sheathing which is an R12 which thermally breaks everything I can either go with a 3 in rockwool comfortboard which is another ar12 then throw a five and a half inch bat of Rockwall on top of that gets me another R23 which actually makes my walls fairly close to an r47 except around the post, but considering that my posts are thermally broke from the exterior cold by the zip R sheathing I don't feel all have cold spots in the walls and this also gives me better than pole barn insulation downstairs. And the garage doors I'm looking at are said to seal very well and actually be guaranteed against wind leaks when properly adjusted in the seals maintained due to the design of the tracking. using a multiple layer system also from my reading games you a small increase when switching from one form of insulation to another it just depends on how your product stack-up and how you're using your sealing products.
Just some thoughts on the way I'm planning to do my roof on my building and honestly I don't think I'm going to have any huge issues because I'm even talking about using mr. Cool DIY mini split in my upstairs in combination with a repurposed furnace from my trailer that's probably three to four years old at best before I discontinued use and it's still in good shape as it was new when I bought the trailer. And with the floor trusses I can run a centrally-located HVAC run right down the middle of my building and I'm not going to have a lot of rooms so I'm good there. And I found an error handling system that will allow me to keep that furnace but filter and check the humidity on the air going into the furnace and since it's ducted outside I won't gain any humidity from the propane using it as a backup or assist for heating in the winter. Good luck