Cathedral Roof Issue

Hi, Long time reader here. I can’t sleep at night because I am unsure how to proceed with my roof assembly.
I am building a house addition, Zone 6. I intended to have unvented cathedral ceilings. The contractor was supposed to put R25 XPS above the osb roof deck, but talked me into R10 XPS above the deck, with R38 Roxul between rafters. I wasn’t thinking and agreed to it… now I regret that because it is unvented and I know I will have issues.
So, at the moment I am mid-construction. He has installed OSB deck, 2″ XPS, and OSB on top of that for a roofing base. Rafters are 2×10, and already blocked in between so no soffit vent is possible (have no ridge vent anyway so what’s the point I guess).
As a solution, all I can come up with is to spray 2.5″ closed cell foam against the inside surface between rafters. Then fill rest of rafter cavity with batts.
Is there anything else I can do at this point?
GBA Detail Library
A collection of one thousand construction details organized by climate and house part
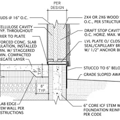
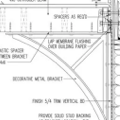
Replies
Depending on your jurisdiction, your contractor's recommended construction might not meet local code. If that's the case, you should make him tear off the top layer of OSB and install the R25 that was specified. Just because he convinced you to do the wrong thing does not make it legal, or make it your problem. If he pushes back, you can invite the local code inspector to take a look and make the call. It is well within your rights as the building owner to call for your own inspections. You only get once chance to get this sort of detail right, and you provided good specifications for a durable assembly. Try your best to get it the way you wanted it. Spraying 2" of SPF inside might protect you from condensation, but it might not get you to the code-required R-value for the assembly and it will end up costing more than doing it the way you specified in the first place, with poorer performance and worse global warming potential.
Thank you!
I will ultimately get code minimum R-value. It comes down to cost now- between either spray or re-doing it.
Can I just use a regular big box store ceiling paint on the gyp board, or do I need something especially breathable?
There's going to be a good chunk of thermal bridging through those 2x10's (and blocking and in to the OSB). R-10 XPS will help (and I wish I had that on mine) but R-25 would be much better.
There are two issues here: code compliance, and long-term building durability in the face of potential moisture accumulation.
To pass code, you can call the 2" of XPS R-10, 2.5" of closed cell spray foam R-18 and the remainder of the space would be batts or blown insulation totalling about R-24, for a total of R-52 and more than 50% of the R-value in the impermeable foam layers, safe from moisture accumulation.
For building durability, it's better to think of the aged values of the foam layers. 2" of XPS will age to about R-8.5 and 2.5" of closed-cell foam will eventually be about R-14.5, a total of R-23. The fluffy layer will remain about R-24, for a total of R-47 (nominal). Slightly less than 50% of the total R-value will be in the foam layer, which in climate zone 6 puts it into the risky category. I'd add a bit more spray foam (HFO-blown for both environmental and performance reasons) and/or add a variable permeance membrane at the interior.