Closed-cell foam inside plus rigid iso outside – recipe for disaster?

We live in a family treasure 1949 Cape Cod ranch in Central Massachusetts. We don’t want to demolish it. To become more energy efficient, we want to super-insulate, rather than replace our oil furnace with solar or mini splits. (We may do the latter in the future but for now we’re not amenable). Our goals for this summer, in this order, are to: 1) replace 20+ year old shingle roof with standing seam aluminum and, in the process, bring roof to R60; 2) replace original wooden clapboards with foam-backed vinyl siding and, in the process, bring walls to R40; 3) the same day we insulate and re-side each wall, replace original single-pane windows with triple pane R5 “outies”; 4) install ERV if house is too tight after meeting goals 1, 2, and 3.
We have found an HVAC contractor to install the ERV. We also found a windows/siding contractor to install our new windows the same day he removes wooden clapboards and applies vinyl siding. We have not yet hired a roofer, but plenty are eager to strip our roof to the sheathing, then apply new underlayment, standing seam panels, and ridge vent. (The vent is needed because the very top portion of our roof is a “cool” attic—which we want to keep cool—with vents at each gable, no insulation in rafter bays, and many inches of blown cellulose on the floor).
What we desperately need help with is, what is the “best” way, without removing interior sheetrock, to bring our roof to R60 and walls to R40? By “best”, I mean, after we finish this summer’s projects, we do NOT want to touch our roof or walls again for a million years. Currently, our walls have 3 inches 1949 kraftpaper-faced fiberglass batt (3 in. x R3 per inch = R9). Our roof, on the other hand, consists of the “cool” attic at the third level (no insulation in rafter bays), followed by the second level portion, which envelopes our bedrooms and has 5 inches 1949 rockwool (5 in. x R3 per inch = R15) between the rafters.
Our initial idea to reach R60 on the roof was to leave all existing insulation in place, then add 6.5 inches rigid isocyanurate (staggered in 2 layers, top panel having 0.5 inch plyboard bonded) above the roofdeck (except over cool attic—there, we would use no insulation and woodblock or something to make it level with rest of roof surface). Our initial idea to reach R40 on the walls was to add 4 inches rigid isocyanurate (staggered in 2 layers, outside panel having 0.5 inch plyboard bonded) outside the sheathing.
Then we discovered the Massachusetts Home Market Value Performance Program (which replaces State’s Deep Energy Retrofit Program) and got all excited about the financial incentives it offers. The catch is, we MUST use a contractor from their list for at least one paid service. NOT A SINGLE CONTRACTOR ON THEIR LIST installs rigid iso above roofdeck or outside sheathing AND is willing to service our town. In fact, the only contractor willing to service this neck of the woods does nothing insulation-wise except spray foam. He told us the only “right” way to insulate our roof is to discard the tongue in groove boards from our deck (which are in perfectly good condition, as many roofers have attested!), discard the rockwool (which also appears fine), and let his company spray 5 inches (the size of our rafters) Gaco One Pass low VOC closed cell foam in our rafter bays. He claims his company “shaves as they go along”, so new roof sheathing can be applied same day. We pointed out to him that doing this would only bring us to R32; we would still need 4 inches (instead of the 6.5 inches in our original plan) of rigid iso above the deck to reach R60. He had no comment as he does not work with rigid iso.
With respect to walls, he told us the only “right” way to insulate is to discard the original barnboard sheathing (which is neither rotten nor broken), have his company spray 3.5 inches (the size of our studs) Gaco One Pass low VOC closed cell foam in our stud cavities. Again, they will “shave as they go along”, so new sheathing could be applied same day. We pointed out to him that doing this would only bring us to R23; we would still need 2 inches (instead of the 4 inches in our original plan) of rigid iso outside the sheathing to reach R40. Again, no comment, as he does not touch rigid iso.
We want to reach R60 on roof and R40 on walls in the most lasting, problem-free way possible, with NO regrets. We are not overly concerned with aesthetic issues (e.g., enormous rake boards) that stem from having super-thick rigid iso on roof and walls. We just want to do things the “right” way and fear this contractor was more intent on making a sale than doing the “right” thing for us. We are even more concerned since hearing a rumor that if one puts rigid iso outside the sheathing, they should not spray closed cell foam inside, and vice versa. Something about moisture condensing on the sheathing in cold weather…? Yuck—we do not want that! HELP!
Normal
0
21
false
false
false
ES-MX
X-NONE
AR-SA
/* Style Definitions */
table.MsoNormalTable
{mso-style-name:”Table Normal”;
mso-tstyle-rowband-size:0;
mso-tstyle-colband-size:0;
mso-style-noshow:yes;
mso-style-priority:99;
mso-style-parent:””;
mso-padding-alt:0in 5.4pt 0in 5.4pt;
mso-para-margin-top:0in;
mso-para-margin-right:0in;
mso-para-margin-bottom:8.0pt;
mso-para-margin-left:0in;
line-height:107%;
mso-pagination:widow-orphan;
font-size:11.0pt;
font-family:”Calibri”,sans-serif;
mso-ascii-font-family:Calibri;
mso-ascii-theme-font:minor-latin;
mso-hansi-font-family:Calibri;
mso-hansi-theme-font:minor-latin;
mso-bidi-font-family:Arial;
mso-bidi-theme-font:minor-bidi;
mso-fareast-language:EN-US;}
GBA Detail Library
A collection of one thousand construction details organized by climate and house part
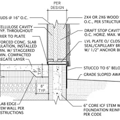
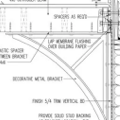
Replies
Hi Anonymous (maybe you want to tell us your name).
Are you concerned with ROI? I ask because it is difficult to recoup your investment when doing this sort of project--especially if you cannot take advantage local energy programs. Just to reality-check your plan, you may to read Martin's article on deep energy retrofits at https://www.greenbuildingadvisor.com/app/uploads/sites/default/files/Deep%20Energy%20Retrofits%20-%20FHB.pdf.
The low hanging fruit with these projects typically involves air sealing (https://www.greenbuildingadvisor.com/article/getting-the-biggest-bang-for-your-air-sealing-buck) and installing insulation in the basement (https://www.greenbuildingadvisor.com/article/how-to-insulate-a-basement-wall) and attic. With your attic, it might make more sense to add additional air permeable insulation even if you can't achieve R-60. If you are able to tighten up the house, installing a properly sized ERV (or perhaps an HRV) will help with indoor air quality. Replacing any gas appliances would be a plus as well since they are a major source of indoor air pollution.
But cape cod style homes present some unique challenges. (See https://www.greenbuildingadvisor.com/article/insulating-a-cape-cod-house and be sure to check out the sidebar links as well.)
Thank you, Steve. Maximizing ROI is not our objective. We acknowledge that what we want to do is more costly than the energy savings it will bring. Probably true of many DER projects. Nevertheless, we still want to know the “right” way to do it. We have prices for reroofing shingle to standing seam, re-siding wood to vinyl, replacing windows, and materials price only (no one has quoted labor) for different thicknesses of rigid iso. The spray foam guy quoted a dollar per board foot. No one has quoted labor for removing sheathing from roof and walls then applying new sheathing. It seems this would be costly. In any case, is it true that having closed cell foam inside and rigid iso outside causes moisture to accumulate on the sheathing?
The article you linked to Cape Cod style homes rings true on many levels. With respect to our triangular attics, the sloped roof portion of these is insulated with 5 in rockwool, as is the sloped roof above the kneewalls. Mass Save installed rigid iso in the transition zone of these attics last year.
We hope That by getting a well insulated standing seam roof, we will no longer have ice dams.
Again, our question is: how do we reach R60 on the roof and R40 on the walls? We are OK with doing this through rigid iso outside only. We are also OK with doing this through close cell foam inside plus rigid iso outside. We just want to know which will last longer and bring fewer headaches.
Thanks
Anything is possible if money is no object. If you are willing to strip off the siding and roof, you could cover everything with reclaimed rigid insulation using the persist method, for example (https://www.greenbuildingadvisor.com/article/getting-insulation-out-of-your-walls-and-ceilings).
But if you want to avoid problems (a good goal), the work should follow sound building science principles. Would you be open to hiring a general contractor who specializes in deep energy retrofits? A few GBA live in your general area and may be able to make recommendations.
My biggest question is about your plan is the R-40 walls. (See https://www.energyvanguard.com/blog/76941/The-Diminishing-Returns-of-Adding-More-Insulation.) Another option might be to do a pretty good level of retrofit and then put the rest of your budget into a solar plus battery package (assuming you have the sun exposure for it).
Adding exterior foam - 4" on the walls and 4" or 6" on the roof is the ideal solution. But find a contractor who understands the building science and knows the right way to do it. And it is never a good idea to sandwich wood (studs, sheathing) between two layers of impermeable material.
I understand that you might need to wait to trash the oil furnace due to the cost, but I've done that in my house and replaced it with a few minisplits and our home has never been anywhere near as comfortable. It's a huge upgrade to the comfort in your house. Its in the 70's here today, and very humid; we set the mini's on "drying" so the house is comfortable and dry without being "cooled" by the AC mode.
Thanks for the link to the PERSIST wall article. Seems like not the right option for us because: 1) it "wastes", rather than taking advantage of, the wall cavity to add R value and 2) if we are going to spend money to remove sheathing, we might as well take advantage by filling the cavities with something that packs a lot of "punch" in terms of R value (we are currently at R11). Re: solar, I am not sure if we have adequate sun exposure or not. We will figure out if we want to go that route sometime in the future. For now, we have no choice but to replace our roof, since it is near the end of its life (shingles starting to lift). The paint is peeled and very flaky on all our wooden clapboards. So either we paint every 10 or so years (which we don't want to) or we switch to vinyl. Reroofing and re-siding present a perfect opportunity to add some extra insulation. After this summer, we hope to never, ever touch our roof or walls again. Where we live is rural and the general contractors we found on Angie's List admitted to having very little understanding of insulation or building science. We will have to look for a contractor or architect near Boston, Worcester, or Springfield. We will gladly pay their consultation fee as long as they can give us accurate information relevant to our goals and situation.
4" of exterior polyiso + 4" of Rockwool = R38, so you're basically at R40. There is no advantage of polyiso in these walls, and sandwiching wood between two layers of impermeable material could be a disaster.
Thank you, Bob, for both your replies. I am not at all surprised by what you are saying. It makes sense and is exactly what I thought before that insulation contractor came along trying to push us down the spray foam route. By the way, his business card shows no HVAC license #. How can I check the license of a so called "HVAC specialist"?